PENDAHULUAN
Latar Belakang
Selama ini perusahaan belum pernah melakukan pemetaan sistem untuk melihat kondisi sebenarnya dalam proses produksi. Dengan menggunakan pendekatan lean management dengan metodologi VSM diharapkan dapat mengurangi waste yang terjadi pada proses mulai dari gudang bahan baku, proses produksi hingga gudang bahan jadi.
Diagram Keterkaitan Masalah
Permasalahan utama yang menjadi fokus penelitian ini adalah perlunya memetakan kondisi proses aktual yang saat ini terjadi pada proses produksi di produksi. Kartu pengambilan Kanban yang digunakan menunjukkan jumlah bagian atau barang yang dapat dikeluarkan dari supermarket untuk diproses lebih lanjut. Sedangkan value stream maping merupakan alat yang digunakan untuk mengidentifikasi pemborosan dalam proses manufaktur (McWilliams dan Tetteh, 1069).
Mesin yang digunakan pada proses ranjang rumah sakit dalam proses produksinya tidak menggunakan mesin khusus, sehingga mesin yang digunakan juga dapat digunakan untuk produk lainnya. Penyeimbangan lini pada proses produksi tempat tidur rumah sakit berlangsung dengan menggabungkan proses-proses yang berdekatan satu sama lain dengan mengikuti alur proses komponen yang harus diikuti. Mesin yang digunakan pada proses produksi pembelahan sel berjumlah 16 mesin ditambah mesin pada proses finishing dengan gerinda tangan yang jumlahnya disesuaikan dengan jumlah operator.
SKN dalam proses produksi tempat tidur rumah sakit, perusahaan perlu menerapkan strategi perbaikan seperti penyeimbangan lini, mendesain ulang aliran proses pada mesin yang digunakan, mengubah tata letak proses menjadi tata letak seluler untuk proses tertentu, dan memperkenalkan sistem traksi dimana perbaikan ini dilakukan secara bersamaan.

Rumusan Masalah
Tujuan Penelitian
Tujuan dari penelitian ini adalah untuk memperoleh pemetaan proses pemetaan yang sedang berjalan pada proses produksi di bidang manufaktur untuk digunakan sebagai dasar pembuatan usulan pemetaan dengan menerapkan sistem manajemen lean yang mampu meningkatkan nilai tambah bagi pelanggan. Lean tools yang digunakan oleh Toyota Production System (TPS) yang dapat digunakan di perusahaan mana pun adalah sebagai berikut. Pemetaan Gambaran Besar adalah alat yang digunakan untuk menggambarkan keseluruhan sistem dan aliran nilai di dalamnya.
Definisi lain dari pemetaan aliran nilai adalah metode pemetaan pasar ramping yang digunakan untuk menggambarkan semua aktivitas yang diperlukan dalam proses produksi suatu produk atau layanan (www.greensupplies.gov). Waktu yang bernilai tambah adalah waktu yang dihabiskan oleh pekerja yang mempunyai nilai tambah yang nyata. Mesin-mesin yang digunakan dalam proses produksi pada umumnya adalah mesin bengkel, mulai dari yang konvensional hingga yang otomatis.
Pada pemetaan saat ini pada Gambar 4.6, aliran pergerakan material terjadi secara acak pada mesin-mesin yang digunakan pada masing-masing departemen, sehingga satu jenis mesin digunakan untuk memproses beberapa produk selain produk tempat tidur rumah sakit, hal ini menyebabkan timbulnya antrian akibat perubahan waktu lembur.
Ruang Lingkup Masalah
Metodologi Penelitian
Tahap ini terdiri dari mengidentifikasi masalah, merumuskan masalah, menetapkan tujuan penelitian dan membatasi ruang lingkup masalah agar masalah yang akan dibahas jelas dan terarah. Studi pustaka berbagai literatur yang berkaitan dengan permasalahan yang diangkat yang diambil dari skripsi dan tesis sebelumnya, buku, jurnal dan benda tertulis lain yang relevan.
Lean Thinking
Lean Tools
Just in time merupakan filosofi manajemen yang berupaya menghilangkan pemborosan dan biaya yang merupakan aktivitas yang boros dengan menghasilkan produk yang tepat di tempat yang tepat pada waktu yang tepat serta dalam kuantitas dan kualitas yang tepat. Alat ini merupakan batu pertama bagi aliran yang berkesinambungan untuk menghasilkan atau mengamankan suatu bagian pada waktunya untuk operasi selanjutnya. Kanban ini bersifat just-in-time yaitu suatu sistem yang memungkinkan produk ditarik dari satu proses ke proses lainnya dengan menggunakan sebuah kartu dimana kartu tersebut menunjukkan kuantitas yang dibutuhkan untuk diproduksi secara batch seperti pada gambar 2.1 diatas, ada 3 jenis Kanban, (Penyadapan, 2002).
Kanban produksi adalah kartu yang menunjukkan jumlah produk atau suku cadang yang akan diproduksi oleh suatu stasiun kerja, yaitu kanban produksi.

Definisi Non Value Added
Konsep 7 Waste
Pemborosan jenis ini biasanya terjadi pada aktivitas ketenagakerjaan di pabrik, terjadi akibat kondisi kerja dan peralatan yang tidak ergonomis, sehingga dapat menyebabkan rendahnya produktivitas pekerja dan mengakibatkan terganggunya waktu pembelajaran produksi dan arus informasi.
Big Picture Mapping
Metode Value Stream Mapping
- Pendahuluan
- Pengertian Value Stream Mapping
- Product Family
- Current Mapping
- Proposed Mapping
Peta saat ini atau kondisi saat ini menggambarkan bagaimana perusahaan saat ini menjalankan bisnisnya dan juga menjadi dasar perencanaan peta masa depan dan memulai manajemen value stream. Tujuan dari pengukuran aliran nilai ini adalah untuk membantu memvisualisasikan proses dan mengidentifikasi masalah proses. Pilih beberapa yang berhubungan dengan proses yang ingin Anda uraikan, namun Anda harus selalu menggunakan waktu proses dan waktu eksekusi.
Setelah melakukan pencarian sebenarnya dari keseluruhan proses, hasil value stream kemudian dapat dilihat dengan menjumlahkannya. Pemetaan yang diusulkan adalah gambaran tentang bagaimana proses value stream harus dilanjutkan setelah perbaikan dengan menghilangkan pemborosan.
Value Stream Mapping Tools
Proses penyeimbangan hanya dilakukan mulai dari proses pemotongan hingga proses finishing, hal ini dilakukan karena pada proses selanjutnya komponen-komponen yang ada pada mesin dialirkan berupa batch container pada proses pembersihan dan conveyor pada proses powder coating. Untuk memanfaatkan sistem informasi yang ada maka Kartu Pekerjaan (KK) yang berbentuk sistem push akan digunakan sebagai sinyal kanban yang akan diteruskan oleh operator pada proses bawah kepada operator pada proses atas. berupa tampilan yang ditampilkan pada layar monitor pada setiap bagian produksi. Sehingga KK yang diberikan dalam bentuk software oleh manajer produksi tetap dapat dimanfaatkan dengan mengubahnya sebagai sinyal yang pada akhirnya membentuk sistem traksi dalam proses yang berjalan.
Setelah dilakukan perbaikan pada peta yang ada saat ini, diharapkan waste yaitu inventory dan WIP yang terjadi pada produksi dapat berkurang dari total durasi 22,5 hari menjadi 4 hari dengan operator yang terlibat langsung dalam proses produksi tempat tidur rumah sakit dapat dikurangi sebesar 26 orang. hingga 18 orang. Perlunya perubahan sistem informasi yang berhubungan langsung dengan operator bagi perusahaan yaitu Kartu Karya (KK) yang menganut sistem push menjadi sistem tarik dengan menggunakan kartu kanban agar operator mengikuti prioritas kerja dalam proses produksi. komponen dan mengurangi biaya.

Tata Letak Mesin
Line Balancing
Operator yang terlibat dalam produksi pemetaan saat ini adalah mereka yang terlibat dalam proses pemesinan dalam produksi tempat tidur rumah sakit. Work in process (WIP) terdapat pada hampir semua proses, namun WIP tidak terdapat pada proses pembersihan (machining, rinsing, Surface Treatment, Phosphating) karena aliran material pada proses ini dilakukan secara kontinyu menggunakan bak berisi air yang berisi air khusus. zat-zat yang diperlukan. untuk membersihkan komponen dari zat-zat yang tidak diinginkan dan juga untuk menghaluskan permukaan logam sebelum proses powder coating. Pada proses powder coating digunakan conveyor belt untuk pengangkutan yang menghubungkan proses pengecatan dengan oven pengeringan. Komponen yang akan diproses diantri dengan cara digantung pada gantungan yang diberi jarak sesuai standar jarak pada jalur perakitan. Proses ini mempunyai waktu pengerjaan yang mengikuti kecepatan belt conveyor yang kecepatannya dapat diatur oleh operator.
Gambar 4.2 menunjukkan bahwa waktu yang terjadi pada setiap proses jauh lebih rendah dibandingkan taktima, dan juga terdapat perbedaan waktu proses pada masing-masing proses. Seperti terlihat pada Gambar 4.5, waktu proses pada masing-masing workstation masih dibawah waktu clock, sehingga dapat dilakukan penyeimbangan garis.
PENGUMPULAN DAN PENGOLAHAN DATA
PENGUMPULAN DATA
- Visi dan Misi Perusahaan
- Data Penjualan Produk
- Data Jumlah Tenaga Kerja
- Jumlah dan Tata Letak Mesin
- Aliran Informasi
- Aliran Material
- Jam Kerja
Data di atas merupakan jumlah pekerja sebenarnya dan komposisi jabatan produksi sesuai kewenangan Manajer Pabrik per Juni 2010 yang berjumlah 66 pekerja produksi. Panah putus-putus menggambarkan aliran material dari gudang bahan mentah ke gudang barang jadi. Apabila masih memenuhi kapasitas, sales menerbitkan Surat Perintah Produksi (SPP) yang diberikan kepada PPIC.
Bagian administrasi produksi akan membagi pekerjaan operator dalam bentuk kartu kerja (KK), yang kemudian KK tersebut dapat diakses oleh operator di setiap bagian produksi dengan bantuan komputer yang terhubung dengan jaringan. Secara umum aliran material produk memiliki 14 langkah proses mulai dari penerimaan material di gudang bahan baku hingga proses pengiriman dari gudang barang jadi ke pelanggan.

PENGOLAHAN DATA
- Pareto Chart
- Pembuatan Current Mapping
- Transportasi
Permintaan pelanggan terhadap tempat tidur rumah sakit sebanyak 349 unit pada periode Januari 2010 sampai September 2010, dimana jumlah hari kerja efektif yang digunakan adalah 23 hari kerja, sehingga rata-rata permintaan per tempat tidur rumah sakit adalah 349 unit. hari itu. Sangat penting untuk mengetahui apakah produk tempat tidur rumah sakit yang dihasilkan dapat memenuhi permintaan konsumen, maka dilakukan analisis kapasitas produksi pada setiap proses dengan menggunakan rumus sebagai berikut. Sehingga dapat digambarkan dalam grafik perbandingan antara takt time dan waktu proses pada pemetaan saat ini.
Oleh karena itu diperlukan langkah-langkah untuk mengubah alur proses dari layout proses menjadi mobile layout dengan mendedikasikan beberapa mesin yang dialokasikan hanya untuk produksi produk tempat tidur rumah sakit tanpa mengubah layout mesin seperti pada Gambar 4.7. Dari hasil penelitian dan pengukuran peta saat ini dan peta usulan, dilakukan beberapa perbandingan sebagai berikut.

ANALISA
Process Activity Mapping
Kemudian waktu aktivitas pada tabel di atas dalam satuan menit diubah menjadi jam, yang kemudian ditampilkan pada grafik di bawah ini.
Kapasitas Produksi
Melihat tabel di atas, perusahaan perlu melakukan beberapa perbaikan strategis seperti penyeimbangan lini, mendesain ulang alur proses pada mesin yang digunakan, dan menerapkan sistem kanban dalam pembuatan pemetaan usulan. Berdasarkan kondisi aktual tata letak mesin eksisting, maka stasiun kerja direncanakan menjadi 3 stasiun kerja sesuai urutan proses pada Gambar 4.4. Beberapa mesin khusus dalam tata letak seluler ditentukan berdasarkan kedekatan lokasi, dan spesifikasinya ditunjukkan pada Tabel 4.6.
Dalam tata letak seluler, komponen-komponen yang berbagi proses yang sama disusun untuk bekerja pada mesin tertentu. Kedepannya, disarankan agar penelitian ini dikembangkan dengan memperoleh data yang lebih komprehensif yang dapat menghubungkan kegiatan dengan biaya dan hasil aktual pelaksanaan pemetaan yang diusulkan.

Improvement Strategi
Line Balancing
Untuk memastikan produk memenuhi permintaan pelanggan maka waktu setiap proses produksi tidak boleh melebihi takt time, berikut perhitungannya. P/T (menit) Takt Time Dengan melakukan penyeimbangan lini diharapkan jumlah operator yang terlibat dalam produksi berkurang dari 26 operator menjadi 18 operator, hanya saja kapasitas produksi setiap proses tidak melebihi jumlah permintaan per proses. . hari.

Aliran Material Proses Proposed Mapping
Pembuatan Proposed Mapping
Setelah dilakukan perbaikan diharapkan waste yaitu WIP awal 22,5 hari dapat dikurangi menjadi 4 hari berada di lantai produksi. Diperlukan komitmen yang kuat dalam penerapan sistem kanban di lantai produksi mulai dari manajer pabrik hingga operator, serta perbaikan berkelanjutan oleh seluruh departemen dan bagian terkait. Belajar Melihat: Pemetaan Arus Nilai untuk Menambah Nilai dan Menghilangkan Muda 1, (Edisi ke-2nd) The Lean Enterprise Institute, Inc., Brookline, MA.
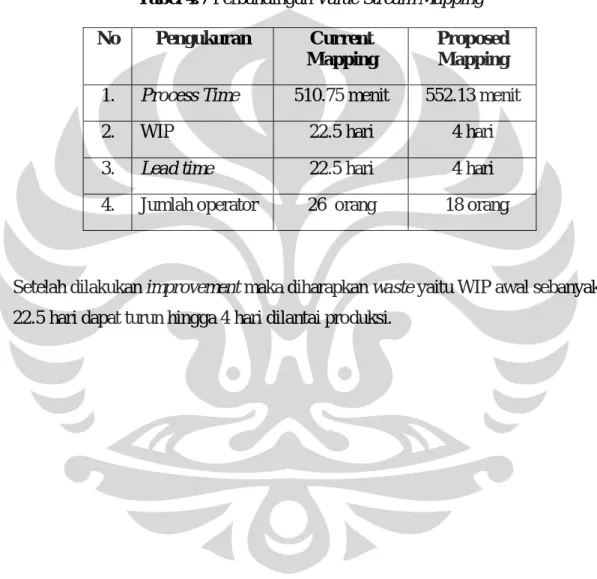
KESIMPULAN DAN SARAN
Kesimpulan
Saran