I thank my students and colleagues for their constructive comments to make the book more useful. Lastly, I always believe in 'kaizen'—the continuous process of improvement in everything I do, and that goes with this book.
Introduction
Related Issues of Operations Management
- Production Function
- Productivity
- Difference between Production and Productivity
- Effectiveness
- Efficiency
Production in an industry can be increased by hiring more labor, installing more machines, and putting in more materials, regardless of production costs. The ratio of output to one of these input factors is usually known as the productivity of the considered factor.
Operations Function in Organizations
Manufacturing Operations Vs Service Operations
Taylor implemented Smith's theories and fought for scientific management in the productive sectors of his time. The most obvious of these, reflected in the new name - operations management - was the shift in the service and manufacturing sectors of the economy.

Types of Production System
Flow Manufacturing: In this type, the factory, equipment and layout are mainly designed to produce a certain type of product. Because this kind of production is on a large scale, it cannot meet individual taste.
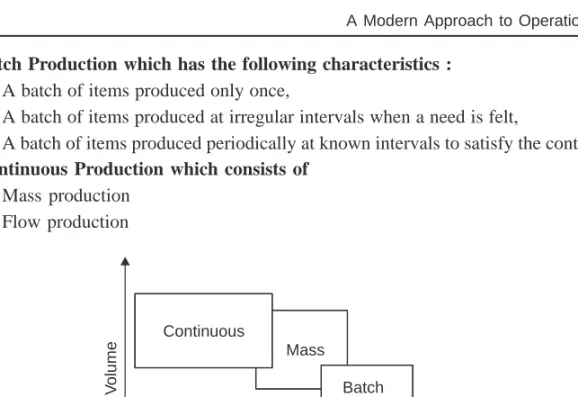
Role of Models in Operations Management
Types of Models in Production Operations Management (POM)
Because all machines are dedicated and purpose-built, the system does not change-. The diagrams are also schematic; they are very useful for showing relationships between variables, as long as all legends, symbols, and scales are explained.
Mathematical Models in Production and Operations Management
Architectural models of new buildings and highway engineering replicas of a proposed overpass system are iconic models.
Modeling Benefits
Classifying Problems
Uncertainty of Outcomes
A monthly average of rejection rates. the number of initially rejected items in the schedule)/(the total number of items in that schedule). Suppose a news agent has a complete overview of the demand (= actual sales + demand that he cannot meet) for a particular newspaper, as shown in Table 6.5; the frequency of the question can be plotted as in Figure 6.14.
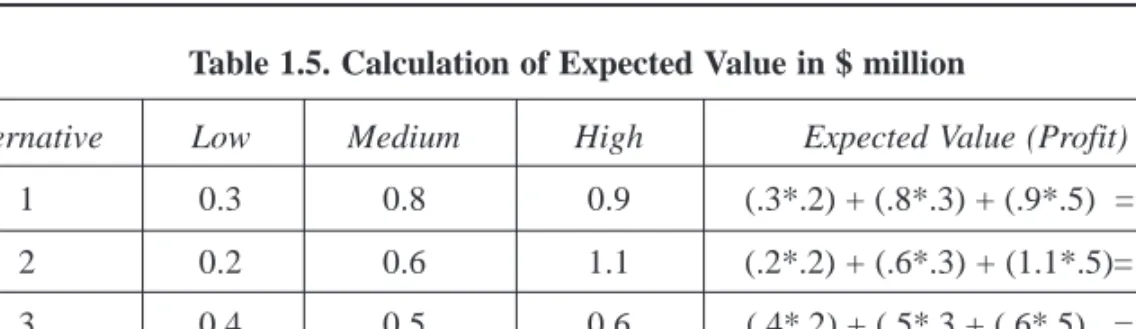
Maximum Rule
Interdependence Among Decisions
Some examples of multilevel problems are encountered by operations managers in project management, capacity planning, and aggregate planning. Production Systems and Operations Management 15 1.2 The bottling plant manager came to work early on Friday, having been out of town all week.
Reasons for Location Changes
Since the operations managers determine many costs with the location decision, both the effectiveness and efficiency of the conversion process depend on the location. We will also discuss the facility location procedure and related issues in the following sections.
General Factors Influencing Location
Rural and Urban Sites Compared
A comparison between rural and urban areas with respect to various factors can be made as shown in Table 2.1. A compromise solution will be to go for a suburban area which has good points from both rural and urban areas.
General Procedures for Facility Location
Preliminary Screening
Selection of Exact Site
Estimates should also be made of all costs associated with operating the plant at each of the sites. These costs include: initial costs, raw material costs, production costs and distribution costs.
Some Other Facility Location Models
- Simple Median Model
- Center of Gravity (GRID) Model
- Linear Programming (LP)
- Simulation
- Break Even Analysis
This method assumes that distribution costs are a function of the quantities shipped and straight-line distances (ie, X and Y coordinates). Distances in each of the X and Y coordinates are averaged, using volumes as weights.

Introduction
Effects of a Plant Layout
Bottlenecks and bottlenecks are eliminated (by line balancing) so that raw material and semi-finished goods move faster from one job site to another.
Factors Affecting Layout
- Types of Industries
- Types of Production System
- Type of Product
- Volume of Production
This is characterized by custom-made, low-volume, labor-intensive products; from a large product mix; with general purpose equipment; from interrupted product flow; and from frequent schedule changes. In the next section, one such method called Systematic Layout Planning is briefly discussed.
Systematic Layout Planning (SLP)
These charts are discussed in detail under 'Work Study' in any Industrial Engineering book. In any case, space requirements and space availability must be balanced before proceeding to step 6.
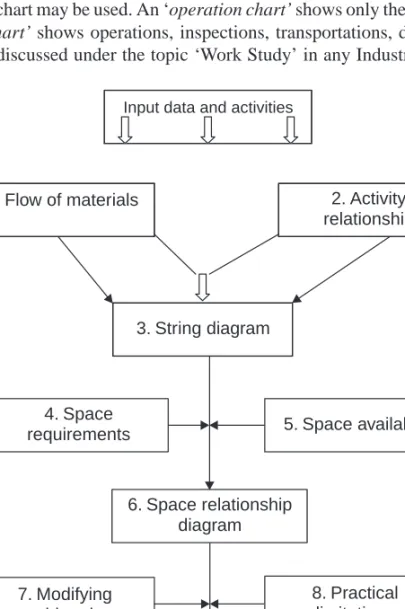
Other Approaches to Plant Layout
Principles of Plant Layout
Types of Flow Patterns
Types of Layout
- Fixed Position Layout
- Process-Oriented or Functional Layout
- Repetitive and Product-Oriented Layout
- Office Layout
- Retail Layout
- Warehousing and Storage Layouts
- Combination Layout
Management must also know the priority relationship between the activities (ie the order in which different tasks must be performed). Although the main objective of retail layout is to maximize profit, there are other aspects of service that managers must consider.

Material Handling
- Principles of Material Handling
- Simplified Version of Principles of Material Handling
- Material Handling Equipment
- Relationship Between Material Handling and Factory Building
Planning Principle: Establish a plan that will include basic requirements, desired options, and consideration of contingencies for all material handling and storage activities. The principle of ecology: use equipment and material handling procedures that minimize adverse effects on the environment.
Functions of Material Management
Most manufacturing organizations spend more than 60% of their money on materials, which means that materials eat up a significant portion of the capital invested in an industrial concern. Materials management can be thought of as the integrated operation of various parts of the company dealing with the supply of materials and other related activities to achieve maximum possible coordination and optimum expenditure on materials etc. used in the industrial concern.
Objectives of Materials Management
To trace new sources of supply and develop cordial relations with them to ensure. Conduct studies in areas such as quality, consumption and cost of materials to minimize them.
Purchasing or Procurement Function
Objectives of Purchasing Department
To reduce investments tied up in inventories for use in other productive purposes and to.
Activities, Duties and Functions of Purchasing Department
Acting as a liaison between the suppliers and various departments of the company, such as pro-. To prepare and update the list of materials required by various departments of the organization.
Centralized and Decentralized Purchasing Organizations
To ensure that prompt payments are made to the sellers for the sake of good public relations. Where branch facilities require heavy and bulky items such as oil products, fuels, paint etc.
Modes of Purchasing Materials
Spot Quotations
Floating the Limited Inquiry
Tender
Steps in One Complete Purchasing Cycle
Some Questions Related to Purchase
Purchasing systems and vendor rating 67 Periodic indicative notice: This is published by utilities, as opposed to public sector organisations. Security Deposit: Once a vendor is selected based on his quotation, he is asked to make a security deposit so that if he fails to provide the items on time or of inferior quality, the security deposit may be forfeited.
Tender Procedure
Exact details of the delivery schedule will be agreed between the supplier and the relevant department(s) of Osaka Gas. Delivered equipment, device(s) or material must pass inspections by the relevant department(s) of Osaka Gas.
Vendor Rating
Technical Specifications: When purchasing the material, detailed specifications of the items are given separately along with the tender documents. However, in some cases it is necessary that some items (400 KV equipment) be shipped directly to substations/power plants.
What is Expected of a Better Buyer
Some Working Definitions
- Quality Index (QI)
- Delivery Reliability Index (DRI)
- Flexibility Index (FI)
- Price Performance Index (PPI)
- Frequency of Rating
- Use of the Indices
It should be evaluated against what the company's internal customers expect from the relationship. Once price performance is quantified and the index calculated for a specific period (monthly, quarterly), it must be evaluated against what the company's internal buyers expect from the relationship.
Stores and Material Control
Requirements of a Material Control System
Stores Management
- Functions of Stores Department and the Duties of the Storekeeper
- Location and Layout of Stores
- Advantages of Centralization of Stores
- Advantages of Decentralization of Stores
To coordinate and cooperate fully with the purchasing, production, inspection and production planning and control departments. All departments should have easy access to stores and especially those requiring heavy and heavy materials should have stores located nearby.
Benefits of Better Operations Planning and Control
Main Functions of OPC
Some Specific Activities of OPC
Directs and coordinates the company's resources for the achievement of desired goals in the most efficient manner.
Detailed Functions of OPC
- Planning Phases
- Routing or Sequencing
- Loading or Assignment
- Scheduling
- Sequencing and Dispatching Phase
- Controlling or Follow-up Phase
For each job, we have knowledge of the sequence of machines required by the job and the processing time on each of those machines. Some of the rules that work orders use are: first come, first served (FCFS), earliest due date (EDD), longest processing time (LPT), and preferred customer order (PCO).
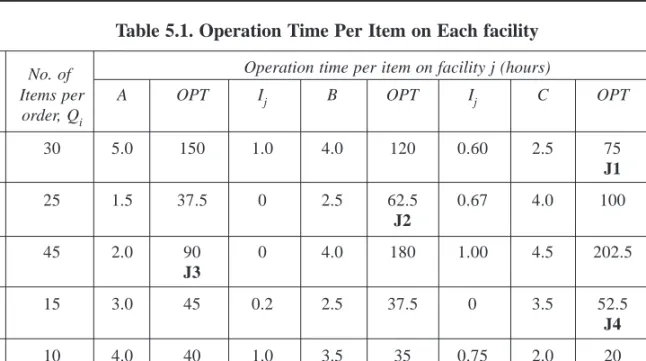
Purpose of Inventories
A typical business has different types of inventory such as: raw materials and purchased parts; partially completed goods called work in progress (WIP); finished products or merchandise in retail stores; spare parts, tools and supplies; and goods in transit to warehouses or customers (called pipeline inventory). In this chapter, we will discuss the purpose of inventory, the basic requirements of inventory management, the various models of inventory control, and other related issues.
Objective of Inventory Management
- Requirements for Effective Inventory Management
- Inventory Counting Systems
- A Perpetual Inventory System
- Ordering Cycle System
- Demand Forecasts and Lead-Time Information
- Inventory Cost Information
Then it's time to reorder using the order card located at the bottom of the first bin. Items are divided into groups, and each group has its own sorting cycle, independent of other groups.

Types of Inventory Control Techniques
Qualitative Techniques
For example, 1000 items of a steel plant can be classified based on the VED classification. The three broad techniques discussed above can be extended to the following classifications as shown in Tables 6.2a and 6.2b.
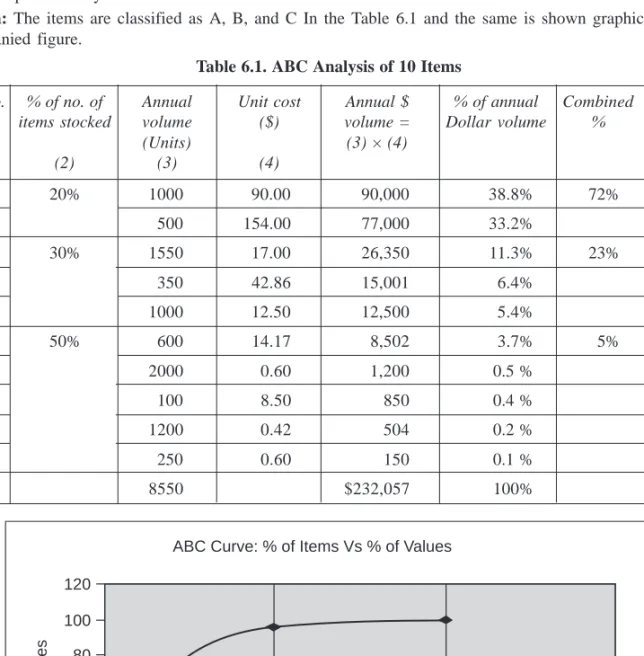
Quantitative Techniques or Models
This is an important point—the EOQ calculation gives us a quantity to order, but often people are better off ordering on a time basis, e.g. This can be seen from the shape of the total annual cost curve in Figure 6.6.

Stocking of Perishables
Solution: Suppose he decided to take the average demand (ie, 80 letters per day) as his order quantity. The example shows how the newsagent can affect the total profit by adjusting the level of his order quantity.
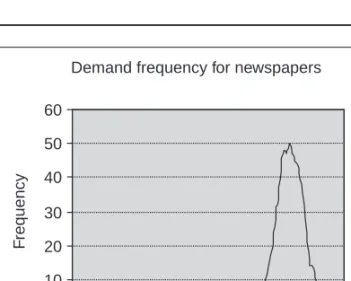
Introduction
Need for Materials Planning
Terms Used in MRP
The expected amount of inventory that will be on hand at the beginning of each period. On hand = Scheduled receipt + Available from previous period – GR Net requirement: The actual amount required in each period.
Basic MRP Concepts
- Independent Demand
- Dependent Demand
- Lumpy Demand
- Lead Time of Item
- Common Use Items
- Time Phasing
An order lead time for an item is the time required from the initiation of the purchase requisition to receipt of the item from the vendor. It is clear from the other branch of the tree that the end item E is also needed to produce N, S and T.

Factor Affecting the Computation of MRP
Production Structure
Lot Sizing
This is because the gross demand for a component is derived directly from the (planned) order quantity of its parent. 136 A Modern Approach to Operations Management in the planned order, be calculated before the gross demand at the component level can be accurately determined.
Recurrence of Requirements within Planning Horizon
Lead time values (or a process for determining these values based on order quantity) must be passed to the MRP system, which stores them for use in establishing the correct reconciliation of requirements and planned order data during a demand burst.
Objectives of MRP System
Prerequisites and Assumptions of MRP
Prerequisites
Assumptions
Inputs to MRP
Master Production Schedule (MPS)
However, the 140 A Modern Approach to Operations Management master production plan used by management and the marketing organization is often developed and specified in months or quarters. The MPS must then be broken down and reformulated in terms of weeks and specific final product numbers.
Bill of Material (BOM)
Material Requirements Planning 141 levels above the items at each next higher level are called the parents of the items at the level immediately below it. In the product structure, the quantity (number) of each item required for the parent item is specified.
Inventory Record File
For example, subassembly S2 contains two of components C4 and C5 and one of components C6. The other information in the Bill of Materials file is the part number, child parent numbers, and the date each child takes or becomes effective. removed from use on the invoice (effective date control for technical schedule changes), scrap and yield rates, destination for shop floor delivery, and level of engineering review. In general, the three segments in the inventory record file consist of the item master data segment.
MRP Outputs
Primary Outputs
Secondary Outputs
MRP Logic in Brief
A Sample of Management Information (Output) from MRP
The sample report shows that 400 units of this item (GR) are needed in week 4 and an additional 500 in week 8. No previous outstanding orders have been placed, so no units of this item are scheduled for receipt at this time.

Limitations and Advantages of MRP
Manufacturing Resource Planning (MRP II)
154 A Modern Approach to Process-Centered Operations Management as illustrated in Figure 7.10. In fact, this is an ongoing process, with the master schedule updated and revised as needed to achieve corporate goals.
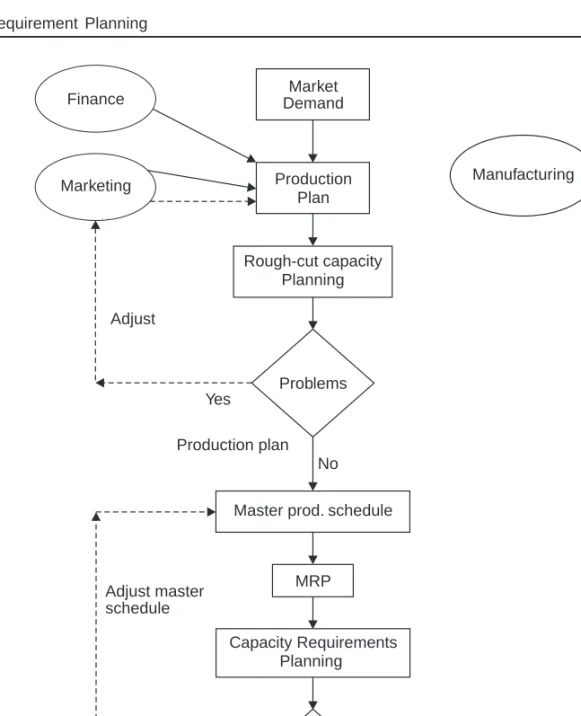
MRP Implementation
An Inventory Control System
The process starts with an aggregation of demand from all sources (e.g. firm orders, forecasts, required safety stocks). Production, marketing, and finance personnel work to develop a master schedule. Subsequently, a more detailed capacity requirement planning (CRP) must be performed to determine whether this more specific capacity requirement can be met.
A Production and Inventory Control System
Although production people will have a large input in determining this schedule and a large responsibility for making it work, marketing and finance also have an important input and responsibility.
A Manufacturing Resource Planning System
An MRP system requires accurate data when decisions are made based on information provided by the computer. A company that does not install an MRP system will need to create an accurate bill of materials as a first step.
How Can Industry Benefit From MRP?
The beginnings of this production system are rooted in the historical situation that Toyota faced. To reduce costs, Toyota has introduced production levelling, which eliminates irregularities in the flow of goods.
History of Relations Between Management and Workers
- Adaptation to New Production Environment
- The Kanban Control
- JIT Today
- JIT Application Profile
It spread throughout Japan in the 1970s as a logical way to manage a large flow of materials. A JIT company adds value with every activity where JIT has been introduced; there have been dramatic increases in the proportion of actual value-added time to total cycle time, often more than 70%.
Keys to Successful JIT Implementation
The Kanban System
Just-In-Time Approach 167 card sent directly to the point of supply (i.e., the manufacturer or inventory lists). Transport kanban (C-kanban): This indicates the need to deliver more parts to the next work center (also called a "move kanban" or a "withdrawal kanban").

Japanese Vs American Management
- Downsides of Japanese Management
- JIT Manufacturing System Overview
- The Seven Wastes in JIT
- Value-Added Manufacturing
The requirement of JIT is that equipment, resources and labor are made available only in the quantity required and in the time required to perform the work. Any step in the production process that does not add value to the product for the customer is wasteful.
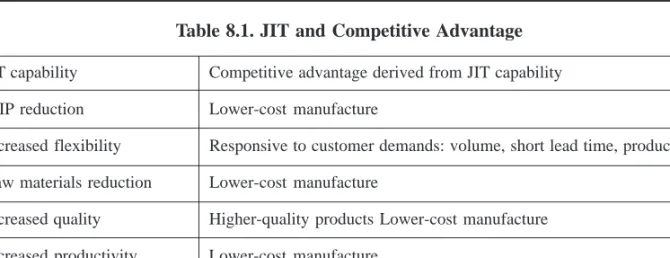
How Japanese Manufacturing Ideally Works?
Stockless Production
Comparison of MRP and JIT
Push Vs Pull System
Control over moving the work rests with the following action; each workstation pulls the output from the previous station when needed. Thus, in the pull system, work is moved in response to demand from the next stage of the process.
Requirements for Successful Implementation of JIT
Goals of JIT Manufacturing System
Important Aspects in JIT Manufacturing
Empowering Workers: A company that empowers its workers gives its workers the authority to solve problems on their own. Problems with communication include ambiguity in the interpretation of the requirement and failure to specify the requirement.
Advantages and Disadvantages of JIT
There are often a number of obstacles that must also be overcome to reach the ultimate goal. Manufacturers can afford fewer errors in supplier component delivery; if a part is not there, the assembly line stops and this can result in wasted manpower and money.
Theory of Constraints (TOC)
- Systems Thinking
- Five Focusing Steps of TOC
- The Five Layers of Resistance
- Quantifying the Improvement
But even if we add a second machine in Step 3 that effectively doubles its output, the system can only produce 15 units per day. Adjust the rest of the system (some steps up, some steps down) to enable the restriction to operate at its maximum efficiency.
TOC Tools
- Current Reality Tree (CRT)
- Conflict Resolution Diagram (CRD) or Evaporating Cloud
- Future Reality Tree (FRT)
- Prerequisite Tree (PRT)
- Transition Tree (TT)
Flow, on the other hand, has much greater growth potential as it is only limited by how much can be sold on the market. Guests don't say when they're moving Being on the Intel Neighbors mailing list doesn't matter.

Some Terms Related to Network Planning
CPM and PERT Model
Time Estimates in PERT
Algorithm Used in Calculating Critical Path
Variability of Activity Times
Probability of Completing a Project by a Given Date
Project Crashing and Time-Cost Trade-off
Resource Leveling
Heuristic Methods
Resource Leveling of Project Schedules
Project Delay
Introduction
Inspection
Types of Inspection
Purpose of Inspections
Some Quality Related Terms
Statistical Quality Control (SQC)
Acceptance Sampling
Where do we use Sampling ?
Advantages and Disadvantages of Acceptance Sampling
Representative Sample
Sampling Plans
Single Sampling Plan (SSP)
Double Sampling Plan (DSP)
Sequential or Multiple Sampling Plan
Process Variability and Control
Control Charts
The p-Chart
The c-Chart
Steps in Constructing S-Chart
Steps in Constructing the X Chart
Use of Computers in Quality Control
TQM Need Commitment
Various Approaches to TQM
Deming’s Approach to TQM
Juran’s Approach to TQM
Crosby’s Approach to TQM
Feigenbaum’s Approach to TQM
Ishikawa’s Approach to TQM
Some Quality and TQM Related Terms
Relationship Between ISO 9000 and Quality
Relationship Between ISO 9000 and TQM
Principles of ISO 9000
Benefits of ISO 9000
The LP Formulation and Underlying Assumptions
The General LP Formulation
Graphical Solution of 2-Variables LP
A 2-Var LP with a Unique Optimal Solution
Different Forms of Linear Programs
The Assignment Problem
Transportation Problem
Transportation Algorithm (Modi Method)
Objective of Work Study
Tools and Techniques of Work Study
Method Study
Work Measurement (Time Study)
Standardization
What is a Standard?
Examples of Standards
What is Conformity Assessment?
Standards Development, Acceptance/Implementation
Benefits of Standards to Industry
Benefits of Standards to Government
Benefits of Standards to Consumers
Cardinal Principles of International Standardization
Assembly Line
History of the Assembly Line
History of Moving Assembly Line
Pre Industrial Revolution
Industrial Robot
Postal Mechanization/Early Automation
The Age of Automation
Automation
Social Issues of Automation
The Automated Workplace
Productivity Improvement Stories
Story of US Agriculture
Automation Improves Productivity in a Tire Company
Automation Sends Productivity Soaring
Story of Increased Productivity in Photographic Industry
Automation Systems Today
Introduction
Some Basic Concepts
Definition of Value
Reasons Behind Poor Value
Types of Values
Types of Functions
Value Tests
Steps in Value Analysis
Examples of Value Engineering
Some Simple Case Studies of VE
Value Engineering and Simplification Analysis
The Primary Questions
The Secondary Questions
Checklist
Benefits of Value Engineering