Standards Australia would like to acknowledge the participation of the experts who contributed to the development of this standard through their representation on the committee and through the public comment period. Detailed information on Australian Standards, drafts, amendments and new projects can be found at www.standards.org.au. Standards Australia welcomes suggestions for improvement and encourages readers to notify us immediately of any apparent inaccuracies or ambiguities.
This standard was prepared by the Australian members of Joint Standards Australia/Standards New Zealand MT-001, Iron and Steel, to replace AS Wrought alloy steel Standard, hardenability (H) series and hardened and tempered to the specified mechanical properties. After consulting with stakeholders in both countries, Standards Australia and Standards New Zealand decided to develop this standard as an Australian rather than an Australian/New Zealand standard. The purpose of this standard is to specify requirements for forged alloy steels for general engineering purposes supplied in the form of hot-rolled or cold-worked bars for machining, forging and bars, blooms, billets and plates for forging.
The alloy designations used in this standard correspond to those used in US specifications that have been accepted worldwide for many years. The terms 'normative' and 'informative' are used in this standard to define the application of the appendix to which they apply.
SCOPE
1050 Methods for the analysis of iron and steel (all Methods) 1050.1 Part 1: Sampling of iron and steel for chemical analysis AS/NZS ISO.
DEFINITIONS
Finished steel of the same size, made from the same casting and which has been subjected to the same heat treatment. A semi-finished forged, rolled or continuously cast product intended for processing into finished products by further forging or rolling. The cross-section is usually square or rectangular, with dimensions not larger than 165 mm × 165 mm (or equivalent cross-sectional area), and the ratio of width to thickness is less than 4:1.
The cross-section is square or rectangular with dimensions greater than 165 mm × 165 mm (or equivalent cross-sectional area) and the ratio of width to thickness is less than 4:1. The largest difference between the three dimensions measured at the same cross-section across opposite faces of the hexagon. The difference between the maximum and minimum diameter of the rod, measured at the same cross-section.
The difference between the two dimensions in the same section across opposite faces of the square. The cross-section is rectangular, with a thickness greater than 100 mm and a width/thickness ratio equal to or greater than 4:1.
DESIGNATION
A part or single item taken from the sample for the purpose of applying a particular test. Modification symbols may be added to the serial designation as follows:. a) The letter 'X' placed before the series designation to indicate a major deviation in the chemical composition of any grade from the corresponding AISI-SAE grade. NOTE: Information on AISI-SAE grades is provided in the appropriate steel product manual from The Iron and Steel Society of AIME, 410 Commonwealth Drive, Warrendale, PA 15086, USA.
For boron-treated steels, the letter "B" is placed between the second and third characters of the four-digit series designation. NOTE: Equivalent Brinell hardness ranges and advice on the selection of suitable steel grades capable of meeting these properties for sections up to 250mm are given in Appendix C. NOTE: The absence of these suffix letters means that the steel can be coarse or fine grained as desired supplier.
CONDITION OF STEEL ON DELIVERY
MATERIALS
If necessary, tensile testing should be carried out in accordance with AS 1391 (see also clause 4 of this standard). If necessary, the hardenability test shall be carried out in accordance with AS 1770 (see also section 3 of this standard).
FREEDOM FROM DEFECTS
SURFACE DRESSING
Not more than 1.5 mm for every 25 mm of measurement, up to a maximum depth of 20 mm, provided that the sum of the depths on two parallel sides in opposite places does not exceed 1.5 times the maximum allowable depth for one side. Not more than 2.5 mm for every 25 mm of thickness, up to a maximum depth of 20 mm, provided that the sum of the depths of two parallel faces does not exceed 1.5 times the maximum allowable face.
ROUNDING OF TEST RESULT VALUES
MARKING
STEELS SUPPLIED TO CHEMICAL COMPOSITION ONLY
CHEMICAL COMPOSITION
STEELS SUPPLIED TO CHEMICAL COMPOSITION AND
CHEMICAL COMPOSITION
HARDENABILITY TEST
HARDENABILITY REQUIREMENTS
STEELS SUPPLIED TO CHEMICAL COMPOSITION AND MECHANICAL
- CHEMICAL COMPOSITION
- HEAT TREATMENT
- MECHANICAL PROPERTIES
- METHODS FOR MECHANICAL TESTING
- SAMPLING
For forgings with a flat section equivalent diameter greater than 30 mm, either integral test specimens (test specimens forming an extension on the forgings) or separate test specimens shall be provided. Test specimens are forged or machined into the main body of forgings or parts and heat treated with the finished product they represent. Test specimens shall be cut from heat-treated bars and shall not be subjected to further heat or mechanical treatment.
When testing is to be performed on heat-treated test pieces, the heat treatment shall be performed either on the test specimen or on the test piece, unless the minimum tensile strength of the steel is 1300 MPa or more. In this case, the necessary heat treatment of the test specimen is carried out after it has been machined to the dimensions of the test piece, plus a grinding allowance if necessary. A test specimen showing defective machining or defects shall be rejected and another test specimen submitted.
Test pieces for tensile testing and impact testing shall be prepared with their principal axis in the longitudinal direction of the product. For adjustment sections of the test specimen up to and including 30 mm, the test pieces shall be machined coaxially from the test specimen. For adjustment sections of the test specimen over 30 mm, the test axis shall be 12.5 mm from the surface of the test specimen.
For test specimen sections up to and including 30 mm, the test piece shall be machined coaxially from the test specimen. For test specimen having sections over 30 mm, the axis of the test piece shall be 12.5 mm from the surface of the test specimen. Elongation results should be reported at a gauge length of Lo = 5.65√So, where So is the cross-sectional area of the test piece before testing.
If necessary, the conversion of results from a non-proportional gauge length shall be in accordance with ISO 2566-1. Where the size of the section makes a determination of Brinell hardness impracticable, the Vickers hardness shall be determined in accordance with AS 1817.1. The Izod or Charpy notch test is carried out at ambient temperature in accordance with AS 1544.1 or AS 1544.2 respectively and the average value of the results for three notches is determined.
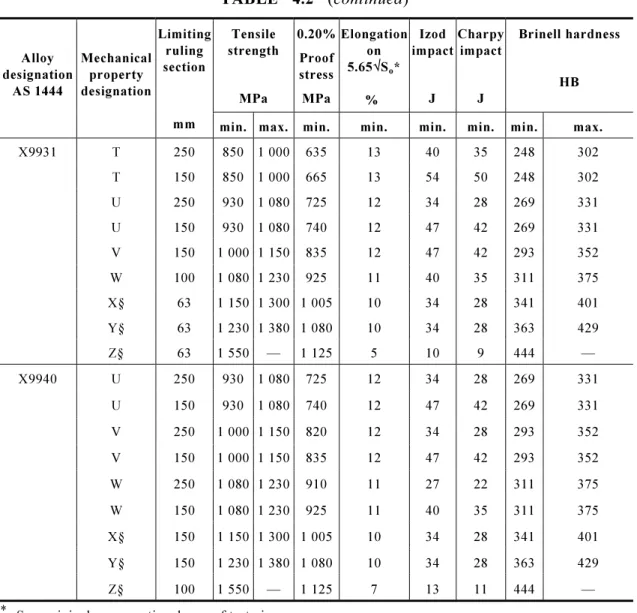
MANUFACTURING TOLERANCES
DIMENSIONAL TOLERANCES FOR HOT-ROLLED BARS
DIMENSIONAL TOLERANCES FOR COLD-FINISHED BARS
1 Out-of-round, out-of-hex, out-of-square in bars have tolerances equal to half the tolerance band. 2 Cross-sectional dimensions are measured at a distance of at least 150 mm from the end of the product. For the length of the mill, bars having a total weight of up to 10% of the supplied quantity may be shorter, but not less than 3.0 m.
This Appendix contains advice and recommendations on the information to be provided by the buyer at the time of the inquiry or order. NOTE: Where further processing requires a maximum hardness to be specified, the value to be used shall be subject to agreement between the purchaser and the supplier. If it is the purchaser's intention to inspect the steel at the manufacturer's works.
To make statistical sampling meaningful to the customer, the manufacturer or supplier must demonstrate how the above conditions are met. The purpose of product certification is to provide independent assurance of the manufacturer's claim that products meet the stated standard. The certification scheme serves to indicate that the products consistently meet the requirements of the Standard.
Where the manufacturer or supplier can demonstrate an audited and registered quality management system that meets the requirements of the relevant or prescribed Australian or international standard for a supplier's quality management system or systems, this can provide the necessary confidence that the specified requirements will be met. Regardless of acceptable quality levels (AQLs) or test frequencies, the responsibility remains with the manufacturer or supplier to provide products that meet the full requirements of the standard. In selecting a steel grade, one of the most important considerations is that its composition must allow the desired mechanical properties to be developed throughout its cross-section by heat treatment.
The requirement for maximum imperfection depth in squares and hexagons of a nominal size is the same as for rounds of the same nominal diameter (eg a square section with faces 24 mm × 24 mm corresponds to a 24 mm dia. round section) . For cold finished bars, the recommended minimum machining allowance is also determined using Table E1; the rolled size is that of the original hot-rolled bar. Through a Memorandum of Understanding with the Commonwealth Government, Standards Australia is recognized as Australia's peak non-governmental national standards body.
Requirements or recommendations contained in published standards are a consensus of views of representative interests and also take into account comments received from other sources. Standards Australia represents Australia on both the International Organization for Standardization (ISO) and the International Electrotechnical Commission (IEC).
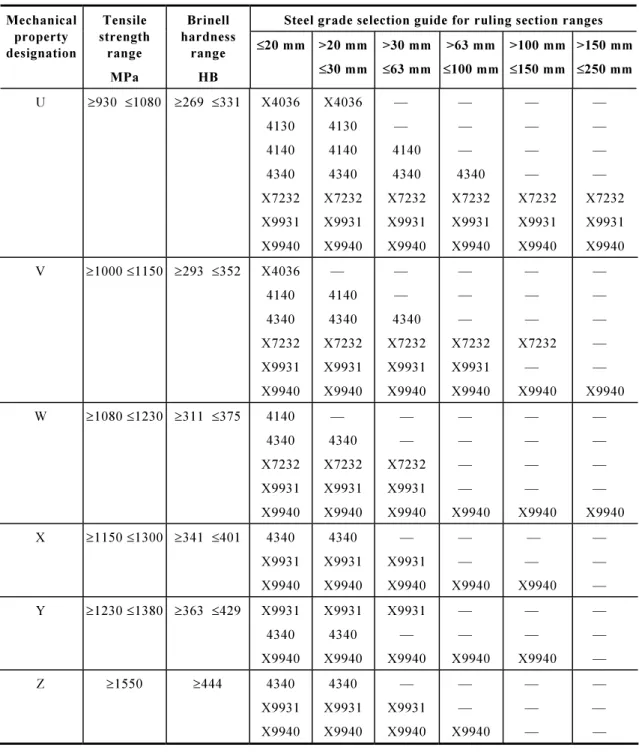