The first phase of the research work presents the successful fabrication of microchannels on transparent PC using the LIPAA technique. The channel dimensions, i.e. the width and depth of the channel, were calculated from the numerical study.
Contents
- Chapter 3 Microchannel fabrication using LIPAA and study on the influence of metal target properties
- Chapter 4 Parametric and statistical investigation into microchannel fabrication on PC and fabrication of thermally bonded
- Chapter 5 2D thermo-physical modelling and simulation on LIPAA of moving heat source for microchannel fabrication on
- 3D thermo-physical modelling and simulation on LIPAA for microchannel fabrication on polycarbonate with aluminium
7.1.3 2D thermo-physical modeling and simulation on LIPAA for microchannel fabrication on PC with aluminum metal targets. 7.1.4 3D thermo-physical modeling and simulation on LIPAA for microchannel fabrication on PC with aluminum metal targets.
64 4.1 Approach for the parametric and statistical analysis 69 4.2 Effect of pulse power density, pulse duration and pulse repetition. 107 5.6 Temperature vs Distance plot along the scanning direction 108 5.7 Temperature distribution along (a) X-axis and (b) Z-axis varying.
List of tables
List of abbreviations
Nomenclature
List of publications
- Introduction
- Microchannel Fabrication Technologies
- Laser-based micromachining
- The motivation of the present work
- Laser-Induced Plasma Assisted Ablation (LIPAA)
- Scope of the present research work
- Organization of the thesis
- Chapter 2 presents an extensive literature survey on the fundamentals of laser- based processing of transparent materials. The current status on related aspects such as
- Chapter 4 presents the comprehensive full factorial experimental investigation on microchannel fabrication on polycarbonate using LIPAA and aluminium metal target. The
- Chapter 5 presents the development of a two-dimensional thermo-physical model of Laser-Induced Plasma Assisted Ablation (LIPAA) using the finite element method
The laser beam passes through the material and is focused on the top surface of the metal target sheet. Studies on the ablation of the metal target are not within the scope of current research work.

Literature review on laser machining of transparent materials
Scope
Transparent materials in scientific and industrial applications
It is also used in the development of urethane (Polycarbonate Urethane, PCU) that acts as a supporting material in orthopedic prostheses, knee prostheses (Kanca et al., 2018), etc. Dudala et al., (2020) and Prakash and Kumar (2015a) also fabricated microchannels in PMMA substrate using CO2 laser for microfluidic applications.
Overview of various microchannel fabrication technologies
- Micro-wire molding
- Lithography based technology
- Embossing or imprinting technology
It's a simple and cost-effective process that takes versatility into account. It is one of the simplest methods, in which the template comes into contact with a plastic or polymer base.
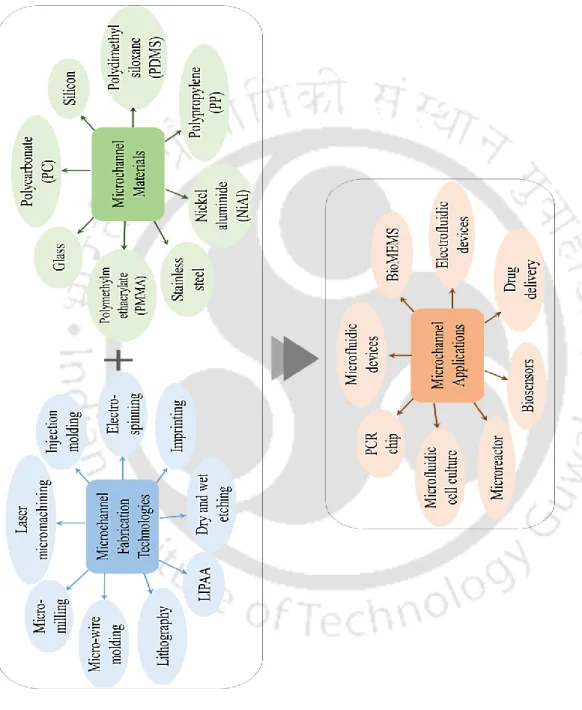
Laser based fabrication technologies
Multi-pass translational method was used and the technique was observed to be able to produce clean bottom microchannels. 2014) presented the technique of laser micromilling for fabricating microchannels with different geometry and dimensions on copper.
Laser-Induced Plasma Assisted Ablation (LIPAA)
- Experimental investigation on LIPAA
- Numerical investigation on LIPAA
Again, Linsen and Guoquan (2012) built a laser drilling thermodynamic model based on the characteristics of the laser drilling and processing environment. It was observed that the thermal stress can be reduced by the dual-laser-beam method.

Process parameters
- Laser parameters
- Workpiece material properties
The thermal and optical properties of the workpiece materials have a great influence on the laser ablation process. In relation to thermal properties, it is noticeable that several literatures report on the influence of thermal conductivity and specific heat capacity on laser metal processing.
Optimum process condition for laser-micromachining of transparent materials The optimum selection of process parameters has played an important role for increasing
However, limited research has been conducted investigating the effect of the thermal properties of the metal target on the transparent material during the LIPAA process. A study of the effect of the thermal properties of metal targets on the transparent material during the LIPAA process may therefore be useful.
Observations and conclusions
However, little work has been reported on the systematic and detailed analysis of the effect of laser parameters on channel size and quality during the laser-induced plasma ablation (LIPAA) process. However, very few studies have been reported on the systematic and detailed analysis of the effect of laser parameters on channel dimensions and quality during the laser-induced plasma ablation (LIPAA) process.
Research objectives
The width and depth of the microchannels were observed under the same conditions of laser parameters for three metal targets and based on the data, the effect of material properties such as thermal conductivity and specific heat capacity on the channel width and depth was presented. The effect of laser parameters on channel geometry and roughness has been extensively investigated. A statistical analysis was performed to analyze the importance of the factors on the responses and to develop mathematical relationships between the input laser parameters and the process responses.

Microchannel fabrication using LIPAA and study on the influence of metal target properties
Scope
Motivation
Theoretical background of LIPAA
I z I e (3.1) where I (z) is the laser intensity at depth z, Io is the incident laser intensity and µ is the absorption coefficient of the substrate material. The plasma generation threshold is considered to be reached when the electron number density (Ne) reaches a value of around 1018/cm3 (Dahotre and Harimkar, 2008). This shock wave expels a large percentage of the molten material from the irradiation site through the micron gap between the transparent and metallic target plates.
Development of experimental setup
When the transparent plate is ablated, a few percent of the molten material is redeposited in the ablated area itself and a larger percent of the molten material is acted upon by the plasma-induced shock wave (Campanella et al., 2019). Thus, a homogenized laser beam with a wavelength of 1.06 μm passes through the PC plate and focuses on the top surface of the metal target sheet, leading to plasma generation, thereby removing both the PC and the metal target plate. Considering this property, aluminum was chosen as the metal target for the well-defined ablation, which was supposed to take place on the back side of the transparent material.

Laser based machining using LIPAA principle
- Field Emission Scanning Electron Microscope (FESEM)
- Energy Dispersive X-ray (EDX) spectroscopy
- Non-contact high precision surface profilometer
- Effect of the thermal conductivity of the metal targets on the channel dimensions
- Effect of the specific heat capacity of the metal targets on the channel dimensions
The FESEM images of the width and depth of fabricated microchannels are shown in Figure 3.13. A schematic representation of the effect of high thermal conductivity of the metal target on the fabrication of microchannels on transparent material during LIPAA is shown in Figure 3.14. A schematic representation of the effect of a higher specific heat capacity of the metal surface on the fabrication of microchannels on transparent material during the LIPAA process is shown in Figure 3.16.

Summary
High aspect ratio microchannels also result in a high rate of heat and mass transfer, making them an excellent microdevice for heat exchangers. Higher aspect ratio microchannels are fabricated with aluminum metal target compared to those fabricated with copper and stainless steel as metal target. As such, further investigation of our research was carried out considering aluminum as the metal target.
Parametric and statistical investigation into microchannel fabrication on PC and fabrication of thermally bonded micro-channels
Scope
The need
Further, the need was identified to form a closed channel and test its ability to be used as a microfluidic device, thus verifying the viability of the LIPAA process. In addition, the effect of microchannel profiles on the resistance of the fluid flow passing through them has been identified. Thus, the need to fabricate microchannels of different profiles to achieve better performance of microfluidics or microchannel-based heaters was also identified.
The present approach for parametric and statistical analysis of LIPAA The key objective of the present experimental study was to investigate the impact of the
The need to conduct experiments was thus identified, to study the effect of process parameters on the responses and to determine the appropriate parameters for the fabrication of microchannels as desired by various applications.
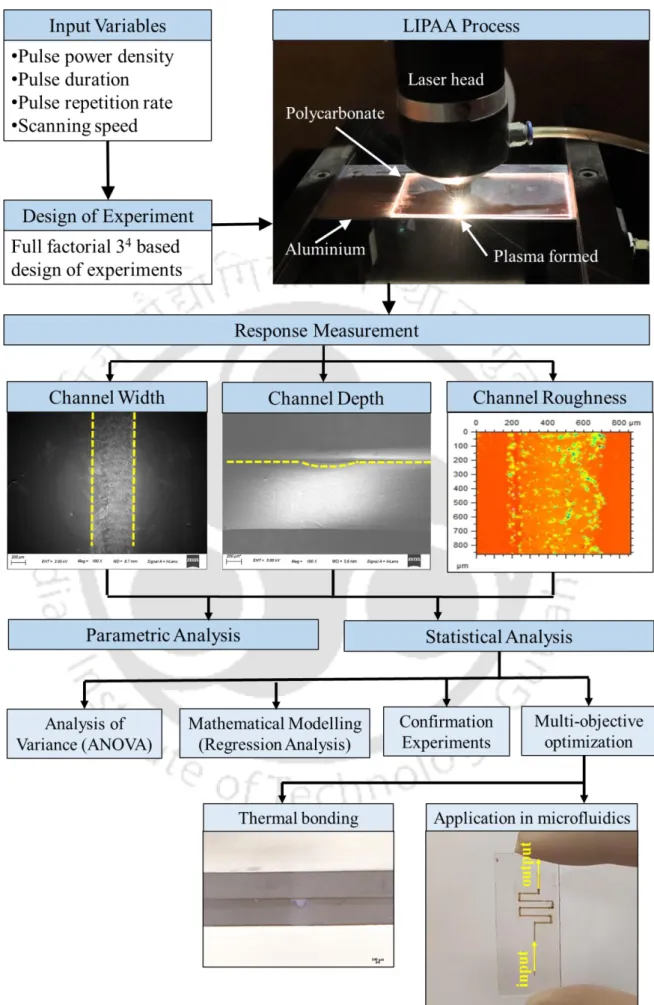
Results and discussion
- Parametric study
- Statistical analysis
The graphs show the effect of pulse power density, pulse duration, pulse repetition rate, and scan rate on channel width. The surface roughness (R) of the channel is also affected by process parameters such as repetition rate, pulse duration, scan rate and pulse power density. The analysis shows that linear process parameters such as pulse power density (IP), pulse repetition rate (f) and pulse duration (ton) have a significant effect on channel roughness.
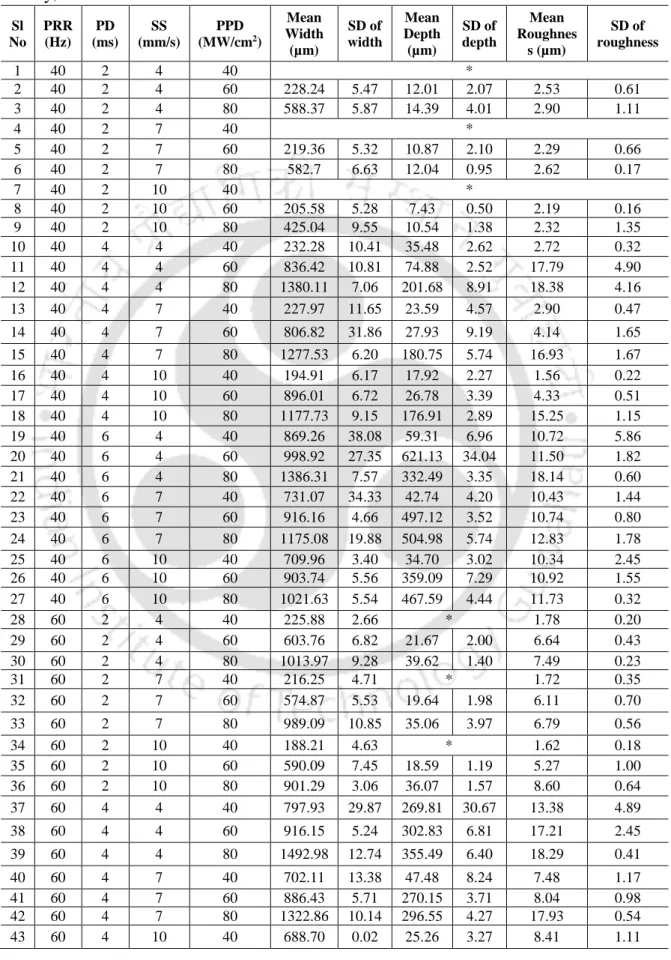
Fabrication of closed microchannels using thermal bonding technique
- Testing of fabricated closed microchannels for microfluidic application
The syringe and bound channel were placed on the stage of the optical microscope. The fluid input flow rate can be adjusted independently by the syringe pump. A constant flow rate of 800 µl/hr was maintained for the injection of the fluid into the channel.

Generation of various microchannel profiles using present setup and optimal parameters
Therefore, the uniform fluid flow in the channel and the ideal properties of PC for a microfluidic device mark its potential to be used as a microfluidic device. These channel profiles play a crucial role in maintaining the stability of fluid flow passing through channel-based microfluidics or heat sinks. It controls the flow resistance which can be greatly optimized by channels of different configurations such as serpentine, round and oval shaped microchannels.
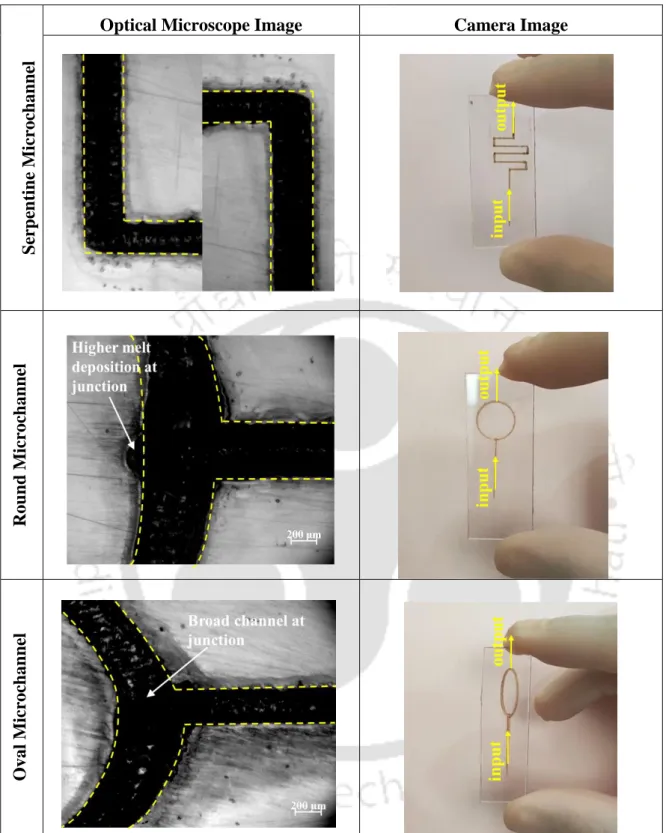
Summary
The increase in pulse power density, pulse duration and repetition rate leads to the increase in the responses viz. The scanning speed not only affects the channel geometry and roughness, but also plays an important role in channel formation. Increase in the channel geometry without increase in the roughness can be achieved by subjecting the channel to multiple numbers of scans of the laser beam.
2D thermo-physical modelling and simulation on LIPAA of moving heat source for microchannel fabrication on polycarbonate
- Scope
- The need
- Overview of two-dimensional LIPAA process model development
- Thermo-physical modelling of LIPAA using Finite Element Method (FEM)
- Assumptions
- Geometric model
- Thermal analysis
- Laser heat source
- Solution methodology
- Finite element formulation
- Results and discussion
- Effect of pulse power density on channel dimension
- Effect of pulse repetition rate on channel dimension
- Effect of pulse duration on channel dimension
- Summary
Therefore, in the current study, the temperature profile is represented on the upper side of the PC. The effect of the process parameters on the channel width and channel depth is also investigated using the developed model. At a pulse duration value of 4 ms and higher, the peak temperature exceeds the melting point temperature of the PC.
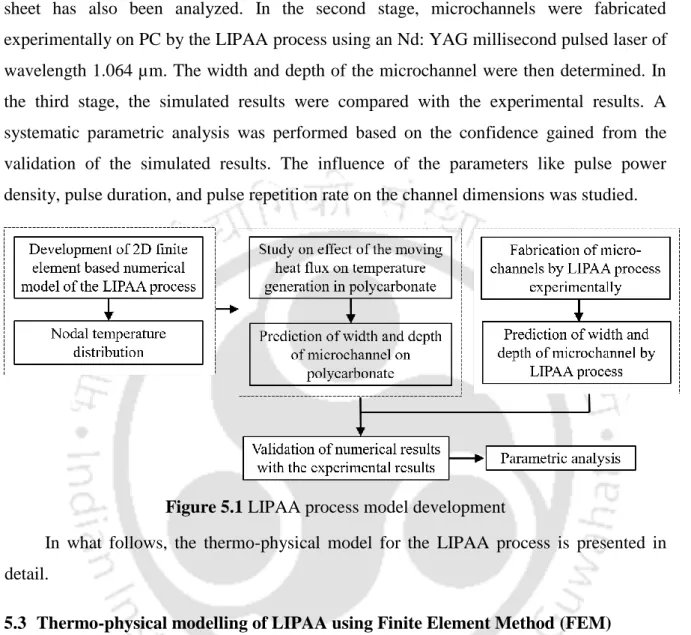
3D thermo-physical modelling and simulation on LIPAA for microchannel fabrication on polycarbonate with aluminium as metal
Scope
The need
3D thermophysical modeling and simulation in LIPAA for the fabrication of microchannels in polycarbonate with aluminum as the metal. Therefore, it was thought worthy to develop a 3D numerical model of the LIPAA process, embracing the plasma impact together with the input laser beam on both the transparent material and the metal target. In the following sections, the details of the numerical model development, its validation with experimental results, and the spatial and temporal thermophysical analysis of the process are illustrated.
Present approach for the spatial and temporal analysis of LIPAA
Three-dimensional thermo-physical modelling of LIPAA using Finite Element Method (FEM)
- Geometric modelling of process continuum
- Thermal modelling of LIPAA
- Solution methodology
- Material properties
Therefore, the incoming laser heat flux was directly applied to the interface of the two materials. The effect of a moving Gaussian heat flux was used in the numerical model of the LIPAA process. The thermal properties of PC and aluminum were considered to be temperature dependent.

Results and discussion
- Validation with experimental data
- Spatial and temporal investigation of LIPAA process
The spatial temperature contour along the x direction at different distances from the interface of the two materials is shown in figure 6.11. But again, the temperature at the interface is beyond the melting temperature of PC and thus material removal is achieved. Similarly, the effect of increasing pulse duration on the width and depth of the microchannel is shown in Figure 6.16(c) and 6.16(d).

Estimation of channel index (CI) for microchannel fabrication during LIPAA using millisecond pulsed laser
In this study, the maximum value of machining speed within the allowable limit was found to be 40.6 mm3/min, resulting in a CI value of 0.86 for process set condition of 3.06 MW/cm2 pulse power density, 60 Hz pulse repetition rate , 4 ms pulse duration and 4 mm/s scan speed. It is observed that when the machining speed is less than its maximum permissible machining speed value (47.05 mm3/min), i.e. consequently, it can be said that CI can be used as an index to determine the allowable set of process conditions for microchannel fabrication under LIPAA using a millisecond pulsed laser.

Summary
In contrast, the depth of the microchannel varies depending on the width to maintain constant blood flow through the channel and achieve the same electrical resistance. The spatial distribution along the x direction on the interface yielded half the value of the fabricated microchannel width while the depth was obtained from the distribution along the y direction on the asymmetric axis. The temperature at the interface was lower than the maximum temperature obtained, but exceeds the melting temperature of the PC and, as a result, material removal on the PC plate is achieved.
Conclusions and future scope
Overview
Conclusions and research contributions
- Microchannel fabrication using LIPAA and study on the influence of metal target properties
- Parametric and statistical investigation into microchannel fabrication on PC and fabrication of thermally bonded micro-channels
Then the channel geometry (channel width and channel depth) and channel roughness of the fabricated microchannels were measured and analyzed. However, this effect of the thermal conductivity is more clearly visible on the channel width rather than on the channel depth. Based on the model, spatial and temporal analysis of the process was carried out.
Scope for future work
Laser Source
Beam Delivery & Focusing Optics System
CNC Table
Laser Safety
The system allows the user to mix and use gases for a specific application or use individual gas directly as needed. The system also consists of nozzles that deliver pressurized regulated gas to the point of laser processing.
Chiller System