Lithium ion battery electrode is porous electrode composed of various components such as active material, binder and conducting agent. Among them, the connector and the conducting agent are inactive parts, so they cannot directly help the active material to implement the capacitance, but they constitute the electrode and help the active material to work. These studies proved too high a ratio of binder or carrier agent for noticeable difference in results that cannot be applied to market production.
KF9300 (Kureha) was used as binder and Super P and Ketjen Black were used as conductors. The slurry mixed with two different ratios of binder and conductive agent; 2% binder with 2% conductive agent and 2.5% binder with 1.5% conductive agent. Cathode with Ketjen Black conductor shows lower bond strength and lower resistance compared to cathode with Super P conductor.
These results show that the bonding structure of the binder and the conductive agent influences cell performance both physically and electrochemically. The SEM image of freeze-dried slurry with a) Super P conductive agent (2%), b) Ketjen Black conductive agent (2%), c) Super P conductive agent (1.5%).
Introduction
Lithium-ion batteries
Researches about lithium-ion battery
- Active material
- Electrochemistry
- Factors influence lithium-ion battery performance
The first lithium-ion battery was developed in 1980 by Goodenough, using LiCoO2 as the cathode.16 In 1982, Yazami used graphite as the anode.17 In 1985, a prototype lithium-ion battery using LiCoO2 and graphite was developed. by Yoshino.18 The first commercialization of the lithium-ion battery was in 1990 by Sony Corporation.19. The energy density of lithium ion battery is determined by three factors which are cell voltage (Vcell), gravimetric capacity (Ah/kg) and density (mg/cm3). Specific Work Energy Density = (Cell Voltage) x (Specific Capacity) / (Mass Loading) / (Thickness) = (Cell Voltage - Overvoltage) x (Specific Capacity) / (Mass Loading) / (Thickness) .
Cell overpotential is defined as the additional potential beyond the thermodynamic requirement necessary to drive a reaction at a given rate.26 Overpotential can be classified into three categories which are resistance overpotential, charge transfer overpotential or activation overpotential, and concentration overpotential. .6. Since the electronic and ionic conductivity of the electrode is affected by the dispersion of the slurry, much research has been carried out by changing the mixing time or sequence to improve the dispersion of the slurry. Also, drying at very high temperature results in low adhesion strength and high electrode resistance, as shown in Figure 11.
Schematic drawing of solvent evaporation and particle sedimentation on electrodes for lithium-ion batteries during drying. Electrode pressing is critical because porosity is related to electrode rotation, which is related to the movement of lithium ions in the electrode composition.
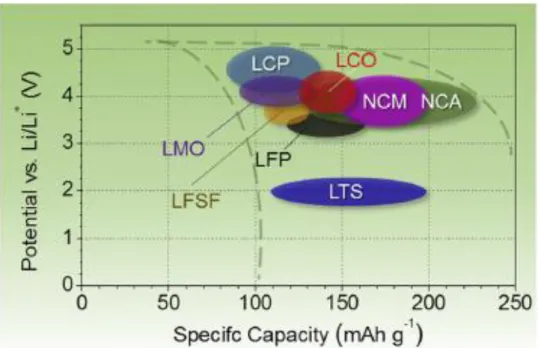
Researches about commercialized lithium-ion battery binder
Liu and researchers investigated the optimized ratio of acetylene black conductive agent and PVDF binder composition for LiNi0.8Co0.15Al0.05O2 cathode.28 They also experimented with the porosity effect. Cycling behavior of LiNi0.8Co0.15Al0.05O2 cathode containing different amounts of inactive materials at 5:3 PVDF/AB ratio versus MCMB anode.11. In the anode, the bond structure of CMC thickener and SBR binder is different, so that the whole electrode structure is different in order of slurry composition.
CMC acts as a thickener to make the slurry viscous so that the electrode can be easily produced. However, because the bonding structure of CMC encapsulates active material particles, it can act as a resistance in the anode while the battery cell is operating. In 2012, Chia-Chen Li and Yu-Sheng Lin reported the interaction of CMC and SBR with active material.3 As shown in Figure 19, they suggested that SBR has a higher preference for LiFePO4 than for CMC thickener.
In that article they experiment with two different mixing sequences mixing CMC and SBR together and mixing CMC first and then mixing SBR last. However, since silicon experiences high volume expansion during lithium insertion, research on polymeric binder of silicon anode is more important. Various attempts to alleviate silicon anode volume expansion have been attempted by changing the polymer binder.
CMC shows better cyclic performance compared to PVDF when using a silicon graphite composite.29 There is research to use a new type of bonding material. An electrochemically active polyamide binder was used for a silicon anode.30 In 2012, a highly crosslinked polymer binder for a high performance silicon anode was reported.31. However, for the commercialization of the battery, the total ratio of binder and conductive agent should not exceed 5 to 10%.
The aim of this research is to confirm the effect of inactive parts in the electrode of the lithium ion battery. The physical properties of the electrode and the electrochemical performance of the cell may differ depending on the binder and conductive agents, even though the active material and its ratio are the same. If it is possible to confirm the role of inactive materials in electrode composite, it would be much easier to maximize cell performance without developing active material.
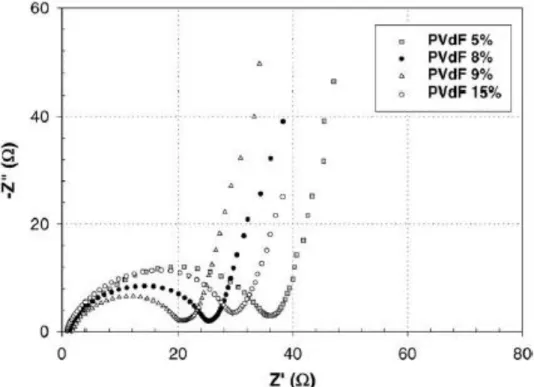
Experimental Method
Electrode and cell manufacturing
Physical characterization
Electrochemical characterization
Results and Discussions
Anode
- Anode binder and slurry freeze dry
- Anode Physical property
- Anode Electrochemical property
Electrode with the high CMC ratio shows the highest average bond strength of 5.029 gf/15mm and maximum bond strength of 5.4 gf/15mm. Since CMC has the facial bonding structure that covers active material particles, it has better bonding ability compared to SBR, so the high CMC ratio electrode has a higher bonding strength than the low CMC ratio electrode. From this result it is possible to predict that the fatigue stress of the high CMC ratio electrode will be higher than the low CMC ratio electrode.
Electrode with a high CMC ratio shows a lower initial capacity compared to the high SBR ratio electrode when their active material ratio and weight are all the same. The full cell with the high CMC ratio anode shows the initial capacity of 13.5mAh. The voltage profile during charge condition, the red line cell which is the high CMC ratio cell has higher potential compared to other two cells.
These results show that the anode electrode with high CMC ratio has higher overpotential during charging and discharging in the initial cycle. However, the cycle retention of the high CMC ratio electrode was better than the high SBR ratio electrode when charged for the 3C rate. In the first charge cycle at 3C rate, the high CMC ratio and the medium CMC ratio cell show similar charging voltage.
The continuous charging current for the high CMC ratio cell was maintained for more than 8 minutes, but for the high SBR ratio cell, it lasted for about 4 minutes. Continuous charging current for the high CMC ratio cell was maintained for more than 6 minutes, but for the high SBR ratio cell, it was maintained for less than 2 minutes. At the 20th cycle, the CC and CV charging time ratio for the high CMC ratio cell is about 1:3.
The charging voltage profile of the 1st, 20th and 50th cycles suggests that the cell with a high CMC ratio has a lower charging voltage, but the difference is much lower than charging at 3C rate. Both the 3C charging rate test and the 1C cycle life test show that the high CMC ratio electrode has better cycle retention compared to the low CMC ratio electrode. When measuring the outer angle of the electrode surface, the average contact angle of the high CMC ratio electrode was 159.8o and the standard deviation was 1.89o.
The mean contact angle of the low CMC ratio electrode was 161.2o and standard deviation was 2.2o. To confirm the effect of CMC more clearly, it is necessary to check 2.6% CMC ratio electrode without SBR content.
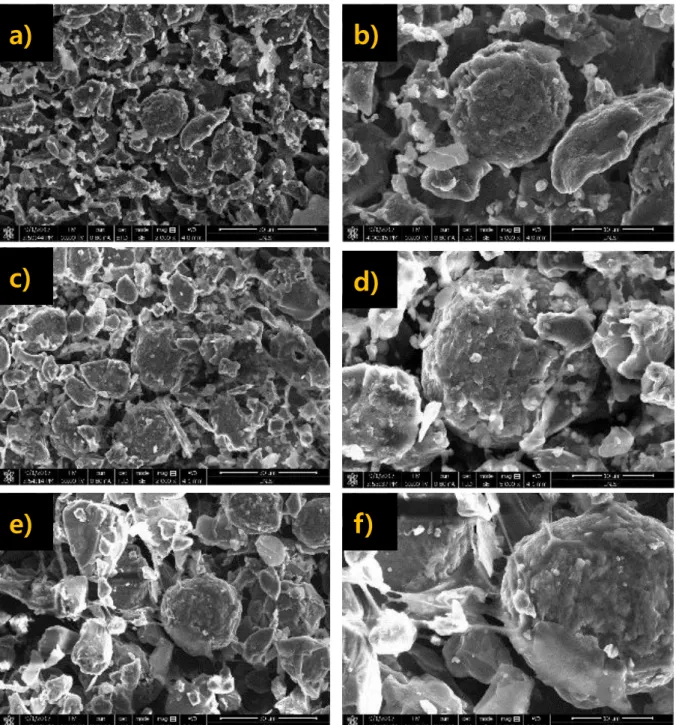
Cathode
- Cathode binder and slurry freeze dry
- Cathode Physical property
- Cathode Electrochemical property
The electrode using Ketjen black as a conductive agent showed lower mechanical strength than the electrode using super P as a conductive agent. Cell with higher PVDF ratio electrode showed poor cycling at 1C and 3C charge cycle retention. In 1C rate cycles, the electrode half-cell with a PVDF ratio of 2.5% showed a retention of 44%, which is much lower than the electrode with a PVDF ratio of 2%, which showed a retention of 60 after 50 cycles .2% showed.
This result is inconsistent with the electrode result with high CMC ratio in anode because higher PVDF ratio accompanies the lower conductive medium ratio. When the conductive agent is not sufficient, the conductive network cannot be established well, so that the cell performance may deteriorate. The voltage profile for the 1st, 20th, 50th cycle of 1C rate charging indicates a high overpotential for the poorly conducting network electrode.
In the initial cycle, the cell with 2.5% PVDF ratio shows similar performance compared to the other samples, but has a high charge voltage and a low discharge voltage. At the 20th cycle, the charge-discharge voltage gap between the 2.5% PVDF cell and the 2% PVDF cell increased, and at the 50th cycle, the difference appears clear. The voltage profiles of 3C rate charging reveal the importance of a well-established conduction network in the cathode composite.
Cell with 2.5% PVDF ratio almost does not have the constant current charging condition at the initial cycle of 3C rate charging. Electrode with Ketjen Black conductive agent showed the electrical conductivity of 0.0581 S/cm, which is 4 times higher than the electrode with super P conductive agent. Electrode with Ketjen Black conductive agent has lower cell impedance because Ketjen Black conductive agent establishes the well-developed conductive network in the electrode.
In addition, since cathode active materials have poor electronic conductivity, it needs not only a binder but also a conductive agent in the composite. The ratio of the conductive agent is extremely important because the establishment of the conductive network is strongly related to the cycle life and rate of cell performance. Therefore, as in the case of the anode, finding the optimum point of binder and conductive agent and using the appropriate ratio of conductive agent with high specific surface area would improve cell performance.

Conclusion
Yazami, R.; Zaghib, K.; Deschamps, M., Carbon fibers and natural graphite as negative electrodes for lithium-ion batteries. Yabuuchi, N.; Ohzuku, T., New lithium insertion material of LiCo1/3Ni1/3Mn1/3O2 for advanced lithium-ion batteries. Bockholt, H.; Indrikova, M.; Netz, A.; Golks, F.; Kwade, A., The interaction of successive process steps in the production of lithium-ion battery electrodes with regard to structural and electrochemical properties.
M.; Song, X., Optimization of acetylene black conductive additive and polyvinylidene difluoride compound for high power rechargeable lithium-ion cells. Winter, M., Silicon/graphite composite electrodes for high capacity anodes: Influence of binder chemistry on cycling stability. S.; Cho, J., A highly cross-linked polymeric binder for high-performance silicon negative electrodes in lithium-ion batteries.
Acknowledgement