It consists of neutronics and thermal hydraulics coupled in the same environment (i.e. internal coupling) and model sensitivity analysis solutions based on the associated formulation of the local sensitivity of the system variable to all input/model parameters. Adjoint sensitivity solver is implemented based on the mathematical derivation of model equations of the system. Using the integrated analysis tool, several design options for the nanofluidic molten salt reactor, including a decay heat removal system for the drain vessel, are evaluated for system performance and safety.
INTRODUCTION
Research Background and Motivation
Review on Molten Salt Reactor and Multiphysics Modeling
The problem in the design of the MSR is the predictive system behavior of liquid fuel, especially the transport of the delayed neutron precursors together with the fuel salt flow. Because the locations where they are produced and decay are different as they move through the system, the distribution determined by the transport of the delayed neutron precursors affects the overall neutronics. In other words, the results of the safety analysis of the fluid-driven MSR are highly dependent on the physical processes being modeled, especially regarding the tightly coupled neutronic and thermal-hydraulic characteristics.
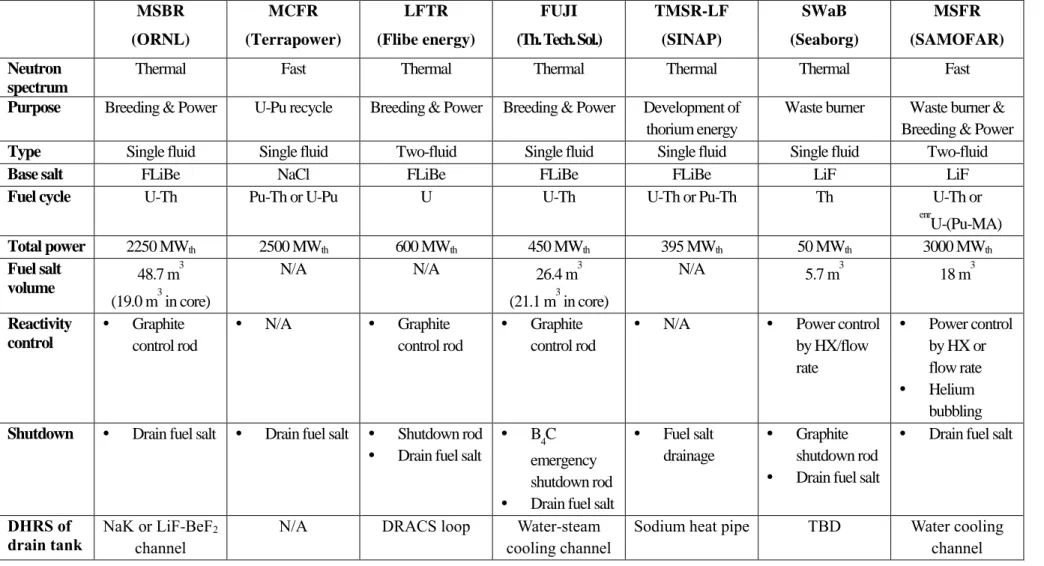
Objectives and Scope
ADJOINT-BASED SENSITIVITY ANALYSIS FOR MULTIPHYSICS
Introduction
Rodigari only performed a sensitivity analysis for neutronics model of molten salt reactor based on the adjoint method, but the effect of circulating fuel salt was included in neutronics precursor balance equation without any temperature feedback [24]. In this section, an additional-based sensitivity analysis method is applied to the Multiphysics approach for the general circulating liquid fuel system to develop a model sensitivity analysis method for molten salt reactor. To verify and validate the developed sensitivity analysis method, numerical studies are performed using MATLAB on the configurations of the one-dimensional closed loop in steady state.

Adjoint-based Sensitivity Analysis Method for Multiphysics Model
- Comparison of Sensitivity Analysis Methods
- Adjoint-based Sensitivity Analysis Method
In the derivation of the adjunct sensitivity system, source terms are determined depending on the solution of the main problem and on the basis of which parameter is chosen for sensitivity analysis. For parameter sensitivity, ASAP is considered the most efficient method for local sensitivity analysis so far [19]. On the other hand, adjoint-based sensitivity analysis can significantly reduce the computation times as well as the computation resources required to solve the problem only M times.
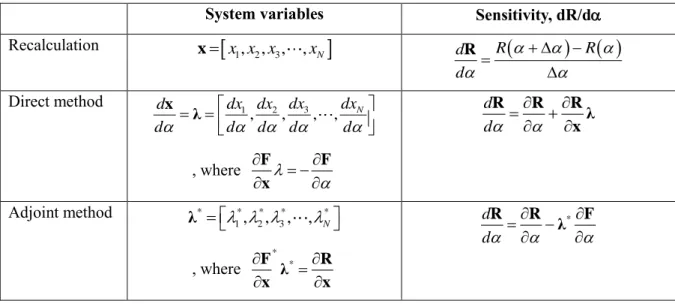
Model Sensitivity of the Circulating Liquid Fuel System
- Multiphysics Model of Circulating Liquid Fuel System
- Adjoint-based Sensitivity Analysis of Circulating Liquid Fuel System
- Validation of Adjoint-based Sensitivity Analysis Method
- Importance of Modeling Options
- Local Sensitivity Analysis of the Circulating Liquid Fuel System
- Changes of sensitivity from parameter perturbation
- Sensitivity analysis of various system responses
The equivalent form of the indirect sensitivity term of the system response can be expressed by the integrated sensitivity solution as follows. In this paper, the sensitivity of the system response is defined as the first derivative; the gradient of the system's response to parameter changes. At this point, the sensitivity of the system response depends on the approximate perturbed amount of the parameter.
It shows that terms directly related to the neutron flux strongly influence the behavior of the circulating liquid fuel system. From this point of view, the associated sensitivity field * indicates the local significance of the sensitivity of the system variable to the response.
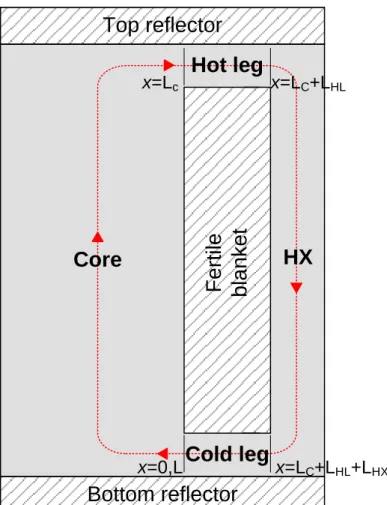
DEVELOPMENT OF INTEGRATED MULTIPHYSICS SOLVER FOR
Introduction
Based on the perturbation theory, the perturbation quantity of the multiplication factor, keff, which is easily affected by the reactor geometry or fuel composition, can be estimated with the joint transport equation in the neutron flux [34]. This means that eigenvalue changes can be approximated by adjoint functions without accounting for the perturbed state. At this stage, the unit of coupled solution varies according to the coupled neutron flux; that is
Therefore, the physical significance of the adjoint solution delayed neutron precursor c* also implies its importance. The governing equations of the circulating liquid fuel system, including all the coupled physics of neutronics and thermal hydraulics, can be expressed with additional formulations by transposing the operator's matrix. Additional formulations of the general system variables of the circulating liquid fuel system allow the estimation of the steady-state perturbed eigenvalue, which is also the most efficient way to calculate the sensitivity system.
C in (3-27) is defined with the unperturbed state of the solution and includes the multiplication factor perturbation. By multiplying the adjunct function * on both sides of the equation (3-28), integrating both sides for the entire domain, and considering the nature of the adjunct operator, the number of keff changes can be expressed with an approximation of as ( 3-30). Then the derivatives of the eigenvalue with respect to the given input parameter can be expressed with a small first-order perturbation of the .
In the following section, the overview of the integrated Multiphysics solver for the circulating liquid fuel system on how to implement both the Multiphysics solver and the adjoint sensitivity solver will be described.
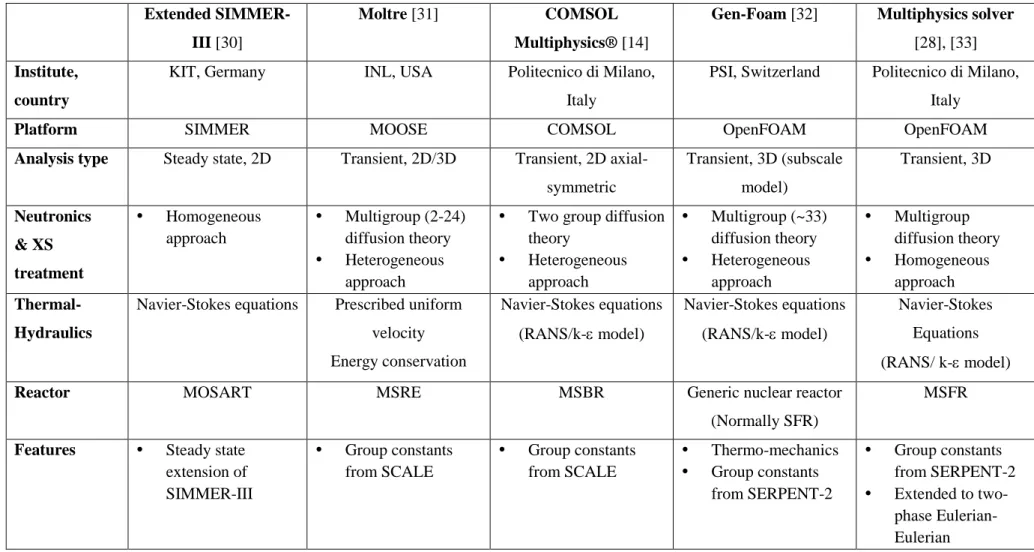
Integrated Multiphysics Solver for Molten Salt Reactor
- Solver Description
- Sensitivity Analysis of the Molten Salt Reactor
- CNRS benchmark: 2D square cavity
Unlike the adjunct solution * that indicates the importance of the neutron, like the weighting function, the physical meaning of the adjunct sensitivity field x* underlies their units. For example, the unit of the adjunct neutron sensitivity X* and the adjunct delayed neutron precursor Y* are determined by the source term C in (3-54). On the other hand, the unit of the adjunct decay heat precursor sensitivity W* and the adjunct temperature sensitivity Z* is the neutron flux per unit energy of the fuel salt.
At this point, the physical meaning of the coupled sensitivity solution follows; how important the variable itself is to the sensitivity of the system's response to the given parameter. For the coupled temperature solution T*, it is obtained from the temperature equation which can be expressed from the internal energy equation. Therefore, it can be interpreted as the importance of the fuel salt in the neutron flux distribution contribution.
Therefore, the adjoint sensitivity solution provides insight into the importance of the delayed neutron precursor, including the flow effect on the neutron flux distribution. Considering the definition of the system response P, the boundary conditions of the adjacent susceptibility field for this case can be derived. From Figure 3-7, the distribution of the adjoint sensitivity field for each state variable is obtained for a given state and type of system response.
Each associated sensitivity field shows the local importance of the system variable on the system response regardless of the parameter. Since the response of the system is defined as the neutron flux field, the neighboring neutron flux susceptibility field follows the neutron flux distribution of the primary solution. In terms of generating fission energy, the lower and middle parts of the core depend on the neutron flux.

Application to New Concept of MSR: Nanofluidic Molten Salt Reactor
- Decay Heat Removal System of MSR
- The Concept of Nanofluidic MSR and Its Design Philosophy
- Implementation of Nanofluid to Solver: nanoMsrAdjointFoam
- Assessment of Decay Heat Removal Capability of Nanofluidic MSR
In this case, molten salt nanofluid could be the concept of the advanced coolant for the liquid fueled molten salt reactor; fuel salt itself with nanoparticle dispersed, only coolant for decay heat removal system of the drain tank or the mixture of nanoparticles when fuel salt drained into dump tank. To avoid the thermal shock of the drain tank and possible accident due to leakage of coolant, the same type of molten salt with fuel salt is the current coolant candidate for both systems. In this section, heat transfer system for the drain tank filled with fuel salt drained from the core with dispersed nanoparticles is considered as a pre-conceptual design of the passive decay heat removal system and its performance is investigated using extended solver of integrated multiphysics - solver.
The natural circulation loop consists of the drain tank, the hot leg, the cold leg and the heat exchanger part. The target leach tank system is MSBR leach tank with fuel salt volume of 48,705 m3 and steady state decay heat generation of 18 MWth. Since most of the fission reaction occurs in the drain tank, the temperature sensitivity to f,ref is the highest value in the drain tank according to the neutron flux distribution.
Especially for the density coefficient, , the highest sensitivity is at the inlet and outlet of the circulation loop of the drain tank. From Figure 3-29, two important variables on the temperature field under the design parameters of the pure fuel salt passive decay heat removal system can be identified; one is the kinetic constants of the precursors and the other is the thermal properties of the fuel salt. Because the kinetic constants of the precursors depend on the composition of the fuel salt, the decay heat removal performance cannot be changed by design.
Especially for nanoparticle distribution, nanoparticles are deposited at the bottom of the drainage tank and at the bottom of the channel.

CONCLUSIONS AND RECOMMENDATIONS
Conclusions
- Adjoint-based Sensitivity Analysis Method on the Multiphysics Approach
- Development of Integrated Multiphysics Tool for Liquid fueled MSR
This means that proper modeling is required to evaluate the sensitivity of the complex multiphysics system. By extending the design and sensitivity analysis method based on the associated formulation on the Multiphysics approach, the application of the molten salt nanofluid is considered to improve the performance of the passive decay heat removal system for the waste tank under natural circulation flow. In this case, separation of variables to configure each influence on system performance is expected to help the design optimization with the objectives of the adjoint sensitivity method.
Recommendations
Brovchenko et al., “Preliminary Safety Calculations for Improving the Design of the Molten Salt Fast Reactor,” in Proceedings of PHYSOR 2012 (Advances in Reactor Physics Linking Research, Industry, and Education), 2012. Rodigari, “Application of the Adjoint Sensitivity Analysis to the delayed neutron parameters in a molten salt reactor,” Technische Universiteit Delft, 2008. Aufiero et al., “Development of an OpenFOAM model for transient analysis of molten salt reactor,” Chem.
Aufiero et al., "Calculation of Effective Delayed Neutron Fraction in Molten Salt Fast Reactor: Analytical, Deterministic, and Monte Carlo Approaches," Ann. Maschek, “Molten salt-related extensions of the SIMMER-III code and its application to a combustor reactor,” Nucl. Luzzi, “Development of a multiphysics model for the study of fuel compressibility effects in the molten salt fast reactor,” Chem.
Brovchenko et al., “Design Related Studies for Preliminary Safety Assessment of Molten Salt Fast Reactor,” Nucl. Su, “Study on sodium heat pipe characteristics in passive molten salt reactor residual heat removal system” Nucl. Wang, “Conceptual Design and Analysis of Passive Residual Heat Dissipation System for 10 MW Molten Salt Reactor Experiment,” Prog.
Mochizuki, “Design of a passive waste heat removal system for the FUJI-233Um molten salt reactor system,” Ann.