Based on this research, a simulation model is designed that uses steam methane reforming to observe the methane slip effect at the reformer. From the simulation plant model, an analysis of the causes and consequences of the methane slip process is determined based on variation in the composition of the raw material (natural gas). Aspen HYSYS 2006 provides a tool for designing a stable and dynamic simulation model of a hydrogen production plant from methane.
CHAPTERl INTRODUCTION
Background of study
Currently, almost all hydrogen is produced via steam reforming of natural gas; more than 95% of all hydrogen produced, the US National Renewable Energy Laboratory (NREL) assessment of hydrogen production via steam reforming shows that the majority of the energy consumed, approximately 87.1%, is that contained in the natural gas produced is fed to the steam reformer. The energy in the natural gas is greater than the energy content of the hydrogen produced;
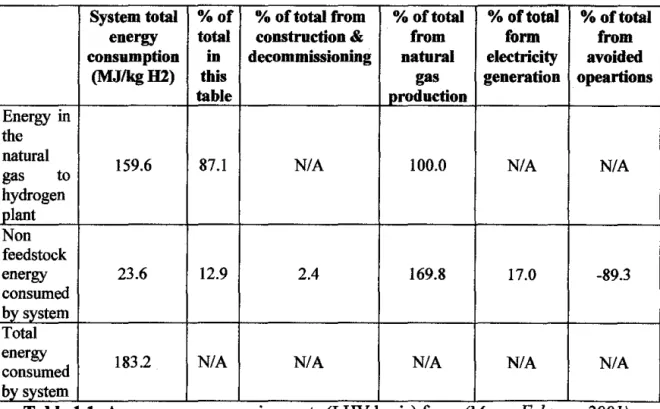
Problem Statement
By analyzing each of these steps, it was found that the large amount of energy consumed in natural gas production comes specifically from natural gas extraction and transportation. Some technologies, mainly steam methane reforming, are being well developed and can be used in the near term. Hydrogen production via steam-methane reforming with validated data taken from an anunonia plant application.
Objective of Study
Therefore, it is important to find an appropriate, economical and simple solution to reduce the amount of methane slippage. It is important to study the design parameter for the methane steam reformer before designing the process model in the simulation environment. To carry out this study, an optimized model of hydrogen production using methane as feedstock was developed using Aspen HYSYS 2006 software and equipment data specification from an industrial application.
CHAPTER2
LITERATURE REVIEW
Hydrogen production
Hydrogen production from steam methane reforming
The additional heat required to drive the process is usually provided by burning some of the methane. One of the goals of this study is to understand the process. implications in a complex SE-SMR reactor. Steam methane reforming usually uses natural gas as a feedstock, which is later converted into hydrogen in refineries.
The simple assumption that natural gas consists only of pure methane is acceptable in process modeling and would not lead to an irrelevance of the model. Fluctuations in the carbon dioxide content of natural gas will be the main problem, as the quality of natural gas is different. Natural gas feed is preheated in coils in the waste heat section of the reformer and sulfur is removed over a zinc oxide catalyst.
Process steam is added and the mixture of natural gas and steam is further preheated before entering the tubular reformer. The H2/CO ratios produced depend on the feedstock, C02 recycle and operating conditions such as temperature and pressure discharge from the reformer. Only methane, carbon monoxide, carbon dioxide, hydrogen and steam are found at the exit of the steam reformer.
1996). The model is implemented in gPROMS (1997) (general Process Modeling System), which is a combined discrete/continuous modeling environment for chemical process systems.
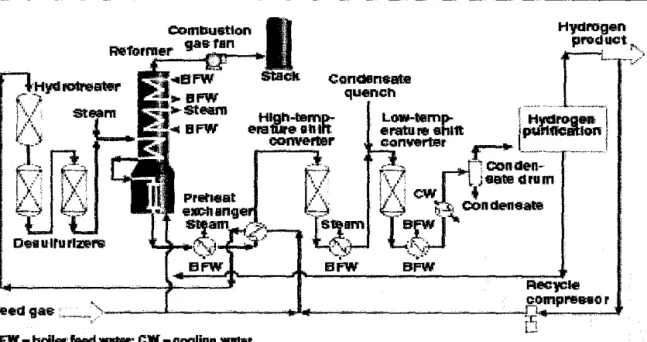
Methane slippage
The relationship between the increase in methane slip at the reformer outlet and the fluctuation of carbon dioxide content in natural gas is illustrated in Figure 2.3. The equilibrium calculation based on the reforming model was performed to determine the required steam-to-carbon ratio (S/C = 0-5) and the reforming temperature C) at which coke formation was not dynamically unfavorable at that time. The generation of coke during catalytic steam reforming could lead to deactivation of catalysts, resulting in low durability, reforming reaction activity and waste of valuable raw materials.
Based on a study conducted by Kajomsak Faugnawakij et.al (2006) on the thermodynamic analysis of carbon formation in methane reforming with dimethyl ether (DME) steam, it has been shown that there are significant differences between cases where the raw material component is manipulated to effect coke to see shape. This chapter describes the research that has been done on the production of hydrogen via the steam reforming process. In addition, there are many processes that produce hydrogen from hydrocarbons; in this case, steam reforming is described as the preferred process.
The main purpose of this literature review is to study hydrogen production; steam reforming of methane and more importantly methane slip research in the reformer. Few researchers have done their research on hydrogen production by methane steam reforming and some research is used for this thesis.
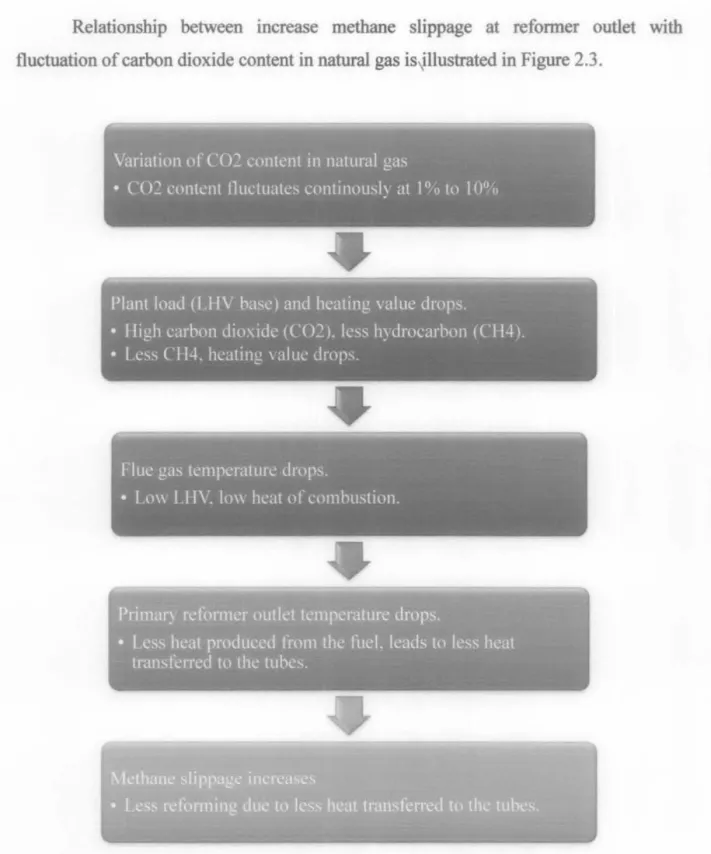
CHAPTER3
PROJECT METHODOLOGY
Research Tools
- Aspen HYSYS 2006
Aspen HYSYS
Research Activities
- Data collection
- Base Case Development
- Base Case Validation
The variation in the input/output data and the operating ranges are important factors in determining whether the data is a good representation of process behavior over a wide range of conditions. At this stage, general understanding of the process should be obtained whereby both theoretical analysis and experience of the operators help to identify the variables, variable relationships, approximate correlations and dynamic property. At a fundamental level, the comprehensive choice of operating and property method can enable us to model a wide range of processes for the future.
The base case of this study is being developed by finding and combining all the reactions that occurred in the reactions of methane with steam. Four different cases were applied in which the developed model was applied to determine the effect of carbon dioxide variation on methane drift. The study on the effect of natural gas composition on methane seepage is based on four cases presented in Table 3.1.
The process of hydrogen production from methane as feedstock was simulated using commercial flowcharting software, Aspen HYSYS 2006. Validation was performed by comparing the molar flow rate of the effluent by calculation based on the total reaction and the molar flow rate of the effluent of the process as simulated in Aspen HYSYS 2006 simulation and data from the actual plant, Petronas Fertilizer Kedah, an anunonia plant in Malaysia. The methodology starts with stoichiometric mathematical analysis that produces the input and output calculation data.
To provide an overview of previous studies related to steam methane reforming, operating conditions, causes and consequences of methane slip.
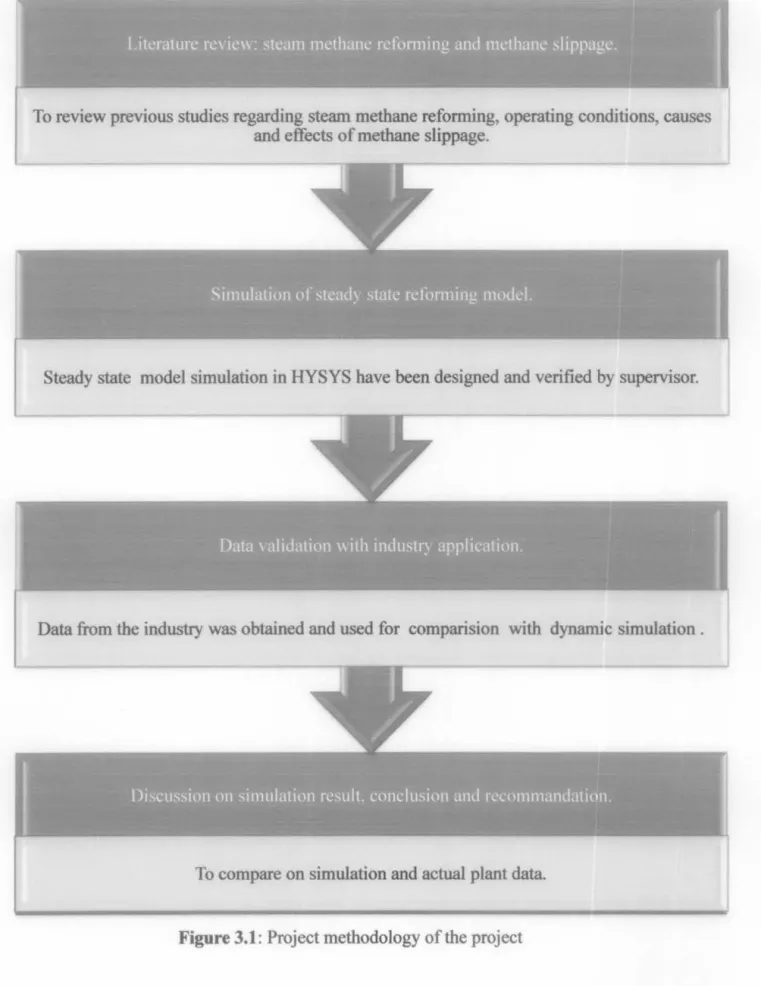
CHAPTER4
SIMULATION OF STEAM METHANE REFORMING
Modelling and Simulation of Hydrogen Production Process
- Physical Properties of the Pure Component
- Thermodynamic Property
- Integration Algorithm
- Mathematical Modeling of the Reactor Operation
- Degree of Freedom Analysis
- Modeling and Simulation Assumption
To initialize the process and to be able to run the simulation, values for the properties of the gaseous phases involved in the reforming process were chosen from specialized literature. In this method, it is assumed that the solute in equilibrium with the saturated solution is a solid containing a negligible amount of the supercritical fluid. The partial molar volume V of the solid solute in the system at all pressures considered. and temperatures are equal to its molar volume at atmospheric pressure and 298K. Peng-Robinson equation of state if given by: .
Where Tc and Pc are the critical temperature and critical pressure, respectively, and w is the acentric factor. These equations allow the calculation of the solubility at a given temperature and molar volume of the solvent, given the vapor pressure and molar volume of the state, the critical parameters and eccentricity factors of both components and the binary interaction parameter. The integration time step can be adjusted in Aspen HYSYS to increase the speed or stability of the system.
The mathematical model of the system in the reformer is developed based on two fundamental quantities, which are total mass balance and total energy balance. Generally, this is the number of adjustable valves plus other adjustable electrical and mechanical devices. The second is the steady state degrees of freedom, Nss, which is the number of variables that must be specified for a simulation to converge.
When running the simulation it is very important to ensure that the correct initial values are used for each flow, as failure to do so can lead to convergence to different values, which is not desirable due to non-linearity and unsteady characteristics. of the process.
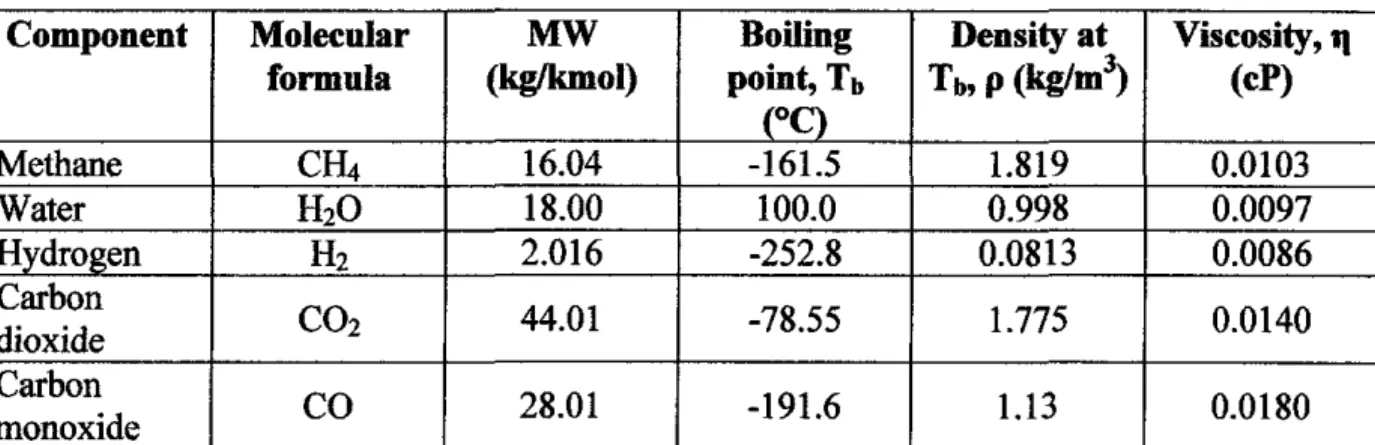
Summary
Potential energy can always be neglected; entry and exit heights are approximately the same.
CHAPTERS
RESULT AND DISCUSSION
Base case study
Base case validation
From figure 5.2, the data showed that variation of C02 in natural gas would increase the plant load. Increases in the plant load shown in the figure will also increase the heating value (LHV) for sufficient heat reaction inside the reformer. From Figure 5.3, the data showed that variation of C02 in natural gas would increase methane leakage.
Flue gas temperature increases shown in Figure 5.3 due to operator intervention to ensure that the outlet reformer temperature will not deviate from the desired temperature. The simulation results reveal satisfactory fits between the data and the model, although there are some differences. As proven in the data, changing the C02 would increase the methane slip at the reformer exit due to the poor heat transferred in the reformer tube.
All the figures show the same condition as discussed, even data plotted is not suitable for comparison, but the concept is still the same. The actual condition of the plant will be different from the simulation data due to instrument malfunction when the data was taken. Therefore, the model developed with Aspen HYSYS 2006 was valid and can be used as a real process for further analysis.
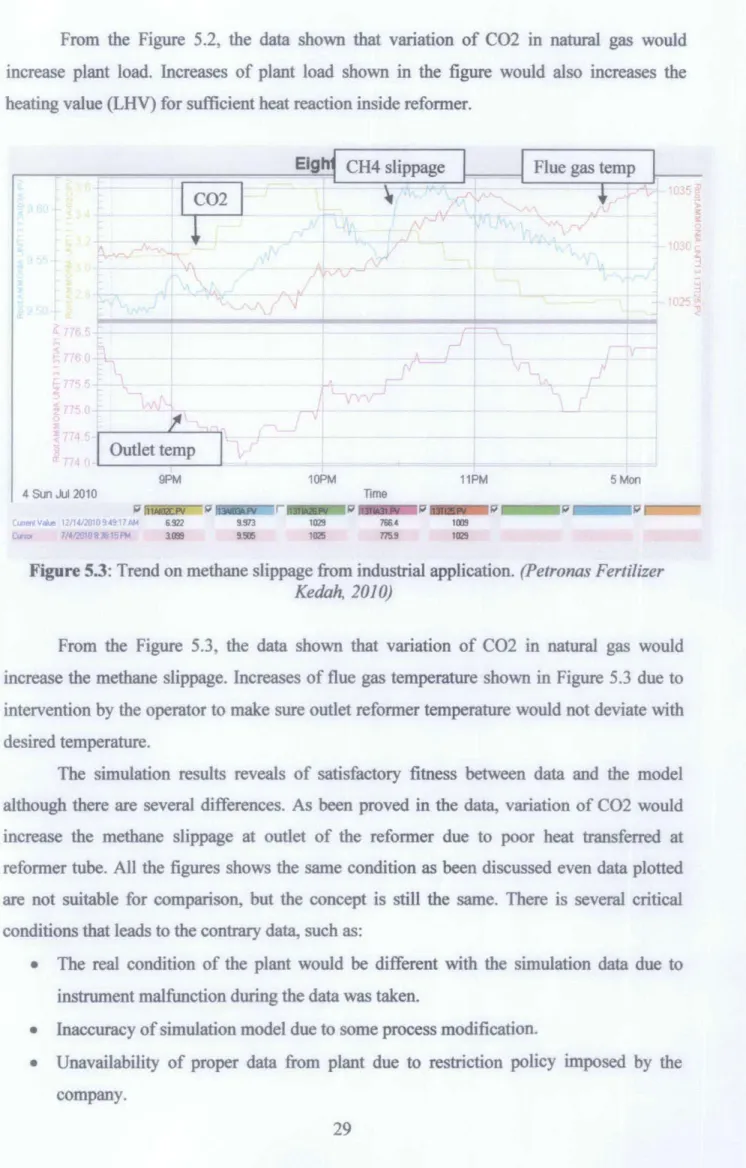
Carbon dioxide variation on methane slippage
- Evaluation on C02 variation on natural gas
- Evaluation on reformer outlet temperature
CH4 outlet vs Reformer operating temp
Evaluation on heat flow
Heat flow vs Reformer operating temp
Reforming Efficiency
It is important to evaluate the efficiency of the reforming process before a steam methane reformer is developed to actual scale. Effectiveness will determine whether the reform process can be profitable for development or vice versa. In this research, the efficiency of the reforming process is calculated using the formula below.
The lower heating value (LHV) of H2, C~ and natural gas is given (Lenz et al., 2005), while the other value is obtained from the data results. In this study, with the hydrogen/methane ratio of 3.5 and steam/carbon ratio of 1.5, the calculated reforming process efficiency is about 45. This chapter presents all the results obtained from the simulation of hydrogen production in steam methane reforming done in this research.
Several discussions were held to explain the selection of certain parameter values during the simulation process. The important part of this chapter is to present the final production of hydrogen and methane slip and also the efficiency of the reforming process. Under this condition, the yield of H2 is 44 mol% to 47 mol% and the efficiency of the reforming process is about 45.
CHAPTER6
CONCLUSION AND REOMMENDATION
Summary
Conclusion
Recommendations