We would also like to thank everyone who responded to our questionnaires and interviews, which helped us come up with this study. We hereby declare that the work presented in this thesis titled "A Study of Knit Fabric Defects and Their Causes" is our original work, has not been presented for a degree by any other university and all resources of materials used for this thesis are been duly acknowledged. This study assesses findings of knitwear defects due to change in stitch length.
In the textile industry, errors often occur and the length of the seam directly affects these errors. By varying the stitch length at the same count on three double jersey knitting machines with the same diameter on the same rib structure, we found the effect of stitch length on normal knitting errors. Changing the stitch length gradually increases or decreases the amount of some of the major defects in the knitwear industry, such as holes/splits, loops/falling stitches, lycra shedding, knots, etc.
For this study, we collected various samples of common knit fabric defects and some quality inspection sheets performed in the 4-point system method from a reputable textile industry. First, we analyzed the data from the quality control sheets, and then we analyzed how changing stitch length affects the increase or decrease of major defects on gray knit fabric.
Introduction
Knitting
- There are two types of knitting
- Knitting machines
Active stitches are held on a needle until another loop is passed through them. In fabric knitting, the entire fabric can be made from a single yarn by adding stitches to each yarn in turn.
Basic Weft knitted structures
- Plain knit structure
- Rib structures
- Purl knit structures:
- Interlock structures
- Features of an interlock Knitting Machine
- Single Jersey Circular Knitting Machine
- Features of Circular Knitting Machine
- Knitting Needles
- Latch Needle
- Types of Latch Needle
- Properties of Latch Needle
- Different Parts of Latch Needle
- Additional Parts of a latch needle
- Main Features of the Latch Needle
- Knitting Action of the Latch Needle
- Advantages of Latch Needle
- Application of Latch Needle
- Common faults in knit fabric
- Common faults in knit fabric, their causes & remedies
- Fabric Quality Inspection
- Four Point System
- The formula to calculate points per 100 square yards
- General Inspection Procedures
- Acceptable calculation for Grey fabric inspection
- Example
It requires two sets of needles operating between each other so that stripes of face stitches and back stitches are knitted on each side of the fabric. As with rib structures, it requires the participation of both needle beds to make the loops. Fact and fiction surround the invention of the safety pin in the same way as the bearded pin.
The latch spoon, which is an extension of the blade, bridges the gap between the hook and the shank that covers the hook when closed, as shown in dotted lines. The head of the needle hook is at the top of the edge of the trick. As the needle stock moves up the slope of the reaming cam, the old loop, held down by the sinker, slides into the hook and contacts the bolt, rotating and opening it.
When the needle reaches the top of the cam, the old loop is removed from the hook and rivet spoon on the shank. At this point the new yarn is fed through a hole in the feed guide to the down needle hook as there is no danger of the yarn being fed under the latch. The old loop makes contact with the bottom of the latch, causing it to close on the hook.
As the head of the needle descends below the top of the trick, the old loop slides off the needle and the new loop is pulled through it. The continued descent of the needle pulls the loop length, which is approximately twice the distance the head of the needle descends, below the surface of the sinker or dummy plate that supports the sinker loop. The distance is determined by the depth setting of the thrust cam, which can be adjusted.
The locking needle has the great advantage that it is self-acting or loop controlled, so individual movement and control of the needle makes it possible to achieve stitch selection. During the loop formation, the yarn had already broken in the area of the hook of the needle. Disc loop length is not properly related to cylinder loop length; the loop pops out of the hook of the needle.
The space between adjacent wales is irregular and the closed look of the fabric is broken in an ugly way. We normally inspect 10% of the rolls we receive and grade them based on a four-point system.
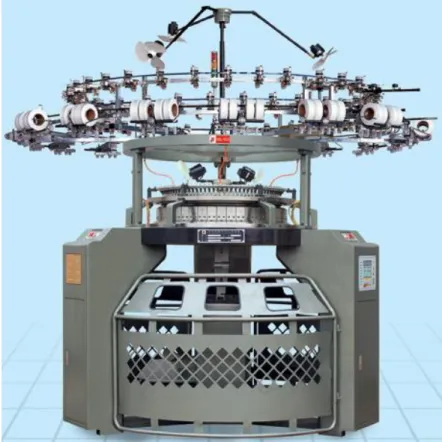
Data Collection
- Data Inspection Sheet at Stitch Length 2.80
- Data Inspection Sheet at Stitch Length 2.58
- Data Inspection Sheet at Stitch Length 2.65
- Table: Machine no 14: 1X1 Rib, 34/1 & 2.8 stitch length
- Table Machine No12: 1X1 Rib, 34/1 & 2.58 stitch length
- Table Machine no 12: 1X1 Rib, 34/1 & 2.65 stitch length
- Data table of different stitch length
- Graphs of the fabric faults found on the average data table
- Yarn Contamination
- Oil Stain
- Knot
- Hole
- Lycra Out
- Fluff
- Loop
From the above graph, we can see that the yarn contamination increased with the increase in stitch length. From the above graph, we can see that oil slick increased with the increase in stitch length. From the above graph we can see that the knots have increased with the increase in stitch length.
The reason for this is, as the stitch length increases, the tension of the feed yarn also increases. From the above graph we can see that the hole / cracks increased with the decrease in stitch length. For the increased tension on yarn, it breaks more in case of reduced stitch length during knitting.
From the above chart, we can see that the Lycra outer increases more with the increase in stitch length. From the above chart, we can see that Fluff increases more with the increase in stitch length. From the above diagram, we can see that as the stitch length decreases, the error loop increases.
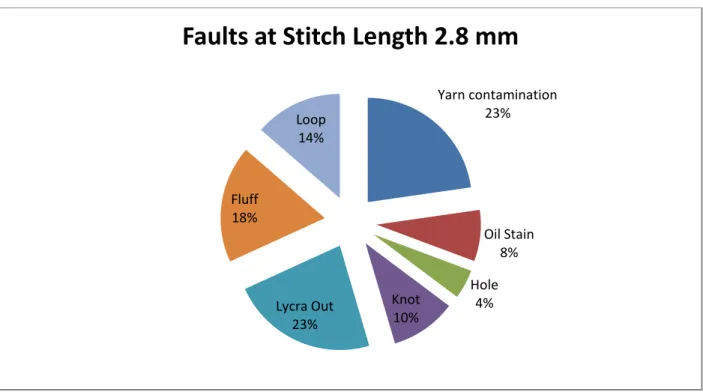
Decisions
Further Study
Conclusion