Analisis Pengendalian Kualitas Nanas Kaleng Menggunakan Metode Six Sigma FMEA-AHP Pada Bagian Line Preparasi (Studi Kasus: PT Great Giant Pineapple, Lampung)
Bebas
10
0
0
Teks penuh
(2) 3.4 Prosedur Penelitian Prosedur penelitian adalah langkah-langkah secara sistematis yang ditempuh untuk mengungkapkan data dan fakta yang berkaitan dengan penelitian. Penelitian pendahuluan terdiri dari survei pendahuluan, studi literatur, identifikasi masalah, penentuan batasan masalah, pengumpulan data dan analisis data, hasil dan pembahasan serta kesimpulan. Prosedur penelitian dapat dilihat pada Gambar 3.1.. Gambar 3.1 Diagram alir penelitian. 30.
(3) 3.4.1 Survei Pendahuluan Berdasarkan Gambar 3.1 penelitian ini dimulai dengan survei pendahuluan dan studi literatur. Survei pendahuluan dilakukan melalui wawancara dan diskusi dengan pihak terkait PT. Great Giant Pinneapple, Lampung Tengah untuk mengetahui jenis produk yang paling banyak diproduksi, kondisi umum tentang penerapan pengendalian kualitas nanas pada bagian Line Preparasi, dan jenis penyimpangan yang terjadi selama proses produksi. 3.4.2 Studi Literatur Studi literatur dilakukan setelah mengetahui permasalahan yang terjadi di bagian Line Preparasi. Studi literatur dilakukan dengan mencari jurnal-jurnal mengenai penelitian terdahulu yang mendukung dalam mencari solusi dari permasalahan selain itu, studi literatur dilakukan dengan cara mengumpulkan, membaca buku-buku, artikel dan jurnal terkait penelitian yang dilakukan. 3.4.3 Identifikasi Masalah Hasil dari survei pendahuluan digunakan sebagai identifikasi masalah bahwa terdapat beberapa kendala pada proses produksi nanas kaleng khususnya bagian Line Preparasi. Kendala tersebut dapat diketahui dari salah satu penyimpangan produk selama proses produksi. Jenis defect yang terjadi adalah broken, mashed, core, serta kontaminasi kulit dan daun. 3.4.4 Pengumpulan Data 1. Jenis dan Sumber Data a. Data primer Data primer diperoleh dari hasil pengamatan secara langsung di bagian Line Preparasi PT. Great Giant Pineapple. Jenis data primer yang dibutuhkan pada penelitian ini meliputi data verifikasi cacat untuk shift A dan shift B dengan total pengambilan 15 hari, spesifikasi produk nanas kaleng yang 31.
(4) dijadikan objek penelitian, identifikasi FMEA untuk mengetahui penyebab masalah cacat, dan keperluan data untuk menentukan usulan perbaikan berdasarkan tingkat RPN tertinggi menggunakan AHP. b. Data sekunder Data sekunder adalah data yang diperoleh dengan cara mengumpulkan dokumen yang tersedia diperusahaan. Data sekunder digunakan untuk mendukung data-data selain wawancara. Adapun data sekunder yang dibutuhkan meliputi jumlah kecacatan yang terjadi di bagaian Line Preparasi, jenis kecacatan yang terjadi di bagian Line Preparasi, spesifikasi produk nanas kaleng, proses produksi bagian Line Preparasi. Data sekunder diperlukan untuk mendukung data-data selain dari wawancara. 2. Prosedur Pengumpulan Data a. Observasi Observasi dilakukan dengan cara pengamatan secara langsung pada kegiatan produksi nanas kaleng di bagian Line Preparasi di PT. Great Giant Pineapple. b. Wawancara Wawancara dilakukan dengan pihak yang mengetahui tentang proses produksi khususnya di bagian Line Preparasi. Wawancara dilakukan langsung dengan pihak yang benar-benar mengetahui kondisi sebenarnya yang terjadi di perusahaan. c. Dokumentasi Dokumentasi dilakukan untuk memperoleh informasi serta data-data yang tersedia di PT. Great Giant Pineapple. 3.4.5. Pengolahan dan Analisis Data. 1.. Pendefinisian (define) Tahap pertama penerapan Six Sigma yaitu define yang dilakukan untuk mengetahui jenis penyimpangan mutu atau cacat yang paling banyak selama proses produksi. Pendefinisian jenis penyimpangan tersebut dilakukan melalui pengumpulan data primer, data sekunder, maupun wawancara dengan departemen Cannery atau Quality Control. Pada tahap ini dilakukan identifikasi produk yang diamati dan aktivitas produksi bagian Line Preparasi. Untuk itu, diagram pareto. 32.
(5) digunakan untuk menunjukan masalah yang paling dominan sehingga dapat diketahui pokok permasalahan yang harus diprioritaskan. Berdasarkan data dari hasil analisis pareto dilakukan wawancara untuk identifikasi CTQ, selanjutnya diteliti yang nantinya akan dilakukan usulan untuk tindakan perbaikan. 2. Pengukuran (Measure) a. Pengambilan sampel Pengambilan jumlah sampel mengacu pada standar ANSI pada Tabel 3.1. Jumlah produk STB14 65 Oz yang dihasilkan dari shift A dan shift B rata-rata per hari 732 kaleng A10 dalam satu hari dilakukan dua kali pengambilan sampel. Satu kali pengambilan sampel sebesar 20 untuk shift A dan 20 kaleng untuk shift B. Total pengambilan sampel untuk shift A dan shift B adalah masing-masing 15 kali, sehingga total sub grup 30. Adapun jenis sampel yang digunakan adalah jenis sampel statistik. Jenis sampel statistik yaitu sampel dipilih secara acak, dimana seluruh populasi diikutsertakan dalam proses seleksi (Syukron dan Kholil, 2013). Tabel 3.1 Contoh Inspeksi Normal ANSI/ASQCZ1.9-1993 Banyak Produk yang Dihasilkan 91 150 151 280 281 400 401 500 501 1200 1201 3200 3201 10000 10001 35000 35001 150000. Ukuran Sampel 10 15 20 25 35 50 75 100 150. Sumber: Ariani, 2004 b.. Uji Kenormalan Data Tujuan uji normalitas adalah ingin mengetahui distribusi sebuah data mengikuti atau mendekati distribusi normal. Distribusi normal adalah distribusi data yang berbentuk lonceng (bell shaped). Data dikatakan baik apabila data tersebut tidak menceng ke kiri atau ke kanan (Santoso, 2010). Pada penelitian. 33.
(6) ini, uji normalitas dilakukan menggunakan Minitab 16 dengan jumlah satu kali pengambilan sampel sebanyak 20 produk nanas kaleng. Menurut Wibowo (2015), uji Shapiro wilk reliabel bila jumlah data yang digunakan kurang dari 20. Dasar pengambilan keputusan dalam uji normalitas yaitu jika nilai signifikansi lebih besar dari 0.05 maka data tersebut berdistribusi normal. Sebaliknya, jika nilai signifikansi lebih kecil dari 0.05 maka data tersebut tidak berdistribusi normal. Apabila data yang didapatkan tidak normal maka cara menaganinya ialah melakukan pemotongan data, kemungkinan terdapat data yang jauh dari rata-rata misalnya sangat tinggi atau sangat rendah. Perbesar sampel, jika sampel sangat besar maka data akan mendekati normal (Hamdi, 2014). c. Pembuatan peta kendali Peta kendali-P digunakan untuk mengendalikan proses melalui perhitungan proporsi produk yang ditolak karena cacat setiap pengambilan sampel. Penolakan didasarkan pada kualitas yang tidak memenuhi persyaratan sehingga dianggap cacat, tidak peduli banyaknya cacat tersebut. Peta kendali p digunakan untuk data yang berhubungan dengan atribut, dimana karkteristik kualitas tidak dapat diukur atau jika diukur tidak diperlukan ketepatan pengukuran karena keputusan yang akan diambil berupa persyaratan memenuhi spesifikasi atau tidak memenuhi spesifikasi yang dianggap rusak atau ditolak (Kuswadi dan Mutiara, 2004). Adapun pembuatan Peta Kendali p dilakukan dengan tahap-tahap sebagai berikut: Menentukan ukuran sampel yang akan diamati. Menghitung persentase ketidaksesuaian, persentase kerusakan produk digunakan untuk melihat seberapa besar proporsi kerusakan produk yang terjadi pada tiap sub grup (per tanggal). Rumusnya adalah sebagai berikut: (8). -. Keterangan: p = persentase ketidaksesuaian (cacat) pn = jumlah cacat n = ukuran subgrup Menghitung batas kendali dengan menggunakan rumus sebagai berikut:. 34.
(7) C. =p. (9) (10) (11). Dimana: C = Central UCL = Upper Control Limit LCL = Lower Control Limit Memplotkan data proporsi dan melakukan analisis terhadap data yang diplotkan. Apabila terdapat data out of statistical control atau data diluar batas spesifikasi, maka data tersebut harus dihilangkan dan direvisi dengan menghilangkan data diluar batas spesifikasi dan mengganti dengan data yang baru. Pembuatan peta kendali dilakukan hingga proses dalam keadaan terkendali (in statistical control). Hal ini digunakan sebagai syarat utama untuk menghitung kapabilitas proses. Syarat utama dalam menghitung kapabilitas proses yaitu nilai rata-rata proses berada dalam keadaan stabil atau terkendali (Gazperz, 2012). d. Perhitungan Nilai Sigma dan DPMO Nilai sigma dihitung menggunakan rumus-rumus perhitungan sigma yang sudah baku dan menggunakan tabel panduan nilai sigma yang sudah tersedia dapat dilihat pada Lampiran 1. Untuk melakukan perhitungan nilai sigma, maka nilai DPMO pada proses harus terlebih dahulu diketahui. Penentuan nilai DPMO ditujukan untuk mengetahui nilai cacat per satu juta produk yang dihasilkan mengacu pada rumus 3, 4, dan Tabel 2.2. e. Perhitungan Nilai Kapabilitas Proses Nilai kapabilitas proses digunakan untuk memprediksi secara kuantitatif berapa baik suatu prduk dapat memenuhi spesifikasi serta untuk menentukan kebutuhan peralatan serta pengendalian yang dibutuhkan. Nilai kapabilitas dihitung berdasarkan data primer yang diperoleh. Pada pengendalian proses statistik terdapat dua jenis data yaitu atribut dan variabel.. 35.
(8) Perhitungan kapabilitas proses mengacu pada rumus 1 sampai dengan 2. 3. Analyze Tahap analyze adalah tahap ketiga setelah measure. Pada tahap analyze aktivitas yang dilakukan adalah mengidentifikasi mengenai penyebab utama timbulnya permasalahan kegagalan produk atau kecacatan produk. Alat yang digunakan pada tahap analyze adalah diagram sebab-akibat dan FMEA (Failure Modes adnd Effect Analysis). Pada tahap ini menghasilkan informasi atau pernyataan mengenai sebab utama terjadinya kecacatan yang harus dilakukan perbaikan. a. Pembuatan Diagram Sebab Akibat Pembuatan diagram sebab akibat digunakan untuk menunjukan secara jelas permasalahan yang memengaruhi suatu masalah. Diagram sebab akibat ini dapat mendorong berfikir secara sistematis dalam memecahkan masalah. Proses pembuatan diagram sebab akibat yaitu akibat atau masalah dituliskan disebelah kanan diagram dan penyebab atau faktorfaktor yang memengaruhi ditulis disebelah kiri. Faktor-faktor penyebab utama dalam perusahaan untuk tingkat penolakan 20% yaitu mesin, bahan baku, metode, serta manusia. Format pembuatan diagram sebab akibat secara umum ditunjukan dalam Gambar 3.2. Manusia. Mesin. Metode. Akibat. Lingkungan. Bahan Baku. Gambar 3.2 Format pembuatan diagram sebab-akibat (Sumber: Herjanto, 2007). 36.
(9) b.. Identifikasi FMEA (Failure Modes and Effect Analysis) Setelah mengidentifikasi penyebab timbulnya cacat, langkah selanjutmya ialah identifikasi FMEA (Failure Modes and Effect Analysis) dilakukan diskusi dengan ahli atau pakar pada PT. Great Giant Pineapple. Ahli atau pakar yang digunakan ada lima meliputi ketua bagian ketua Line preparasi shift A, dan ketua Line preparasi shift B beserta staff, Staff improvement. Proses diskusi dilakukan dengan penyebaran kuisioner yang dapat dilihat pada Lampiran 6 Penentuan FMEA dilakukan dengan menghitung nilai RPN (Risk of Priority Number) dan diisikan nilai frequency of occurance (seberapa sering modus terjadi), degree of severity (seberapa besar pengaruh modus kegagalan), dan canche or probability of detection (seberapa besar kemungkinan modus kegagalan terdeteksi). Format tabel FMEA dapat dilihat pada Tabel 3.2. Tabel 3.2 digunakan untuk rekap akhir perhitungan RPN (Risk of Priority Number). Penilaian RPN (Risk of Priority Number) didasarkan pada skala dari severity, occurance dan detection, berdasarkan perkalian ketiga nilai tersebut maka didapatkan nilai yang paling besar. Nilai paling besar berdasarkan hasil perkalian S, O, dan D digunakan sebagai alternatif dalam pembuatan hierarki AHP. Tabel 3.2 Identifikasi Failure Modes and Effect Analysis Modus of Failure. Cause of Failure. Effect of Failure. Degree of Failure. ….. ….. ….. …. S. O D. … … …. RPN (S*O *D). R a n k. ….. ….. recommended actions ……. Sumber: Schotles et al.(2003). 4.. Improve Tahap Improve adalah tahap keempat setelah tahap analyze. Pada tahap analyze untuk menentukan prioritas perbaikan dilakukan pembobotan kriteria S, O, dan D menggunakan AHP. Pembobotan AHP dilakukan dengan penyebaran kuisioner kepada ahli yang lebih mengetahui proses di PT. Great Giant Pineapple yang dapat dilihat pada Lampiran 10 Langkah-langkah yang dilakukan pengumpulan data, penyusunan matriks berpasangan, normalisasi dan uji. 37.
(10) konsistensi dengan rumus 6 dan 7. Untuk menentukan tingkat kepentingan kriteria dilakukan melalui wawancara dengan pihak yang paling mengetahui kondisi Line preparasi. Setelah normalisasi matriks, langkah selanjutnya ialah menghitung bobot. Nilai bobot terbesar dari analisis AHP digunakan sebagai rekomendasi perbaikan bagi perusahaan. 3.4.6 Kesimpulan dan Saran Berdasarkan hasil penelitian dapat dilanjutkan pada tahap berikutnya yaitu menyusun kesimpulan dan saran. Kesimpulan menjawab tujuan dari penelitian yang telah diajukan. Kesimpulan yang diambil memperhatikan pertimbangan dari hasil yang diperoleh dari penelitian serta didukng dengan teori sebagai landasan berfikir. Saran yang diberikan kepada PT. Great Giant Pineapple didapatkan dari hasil penelitian yang telah dilakukan.. 38.
(11)
Gambar
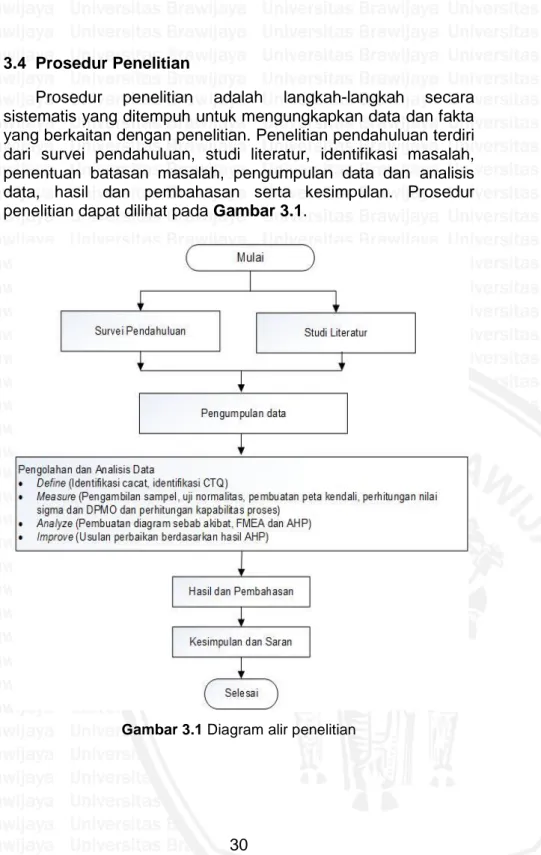
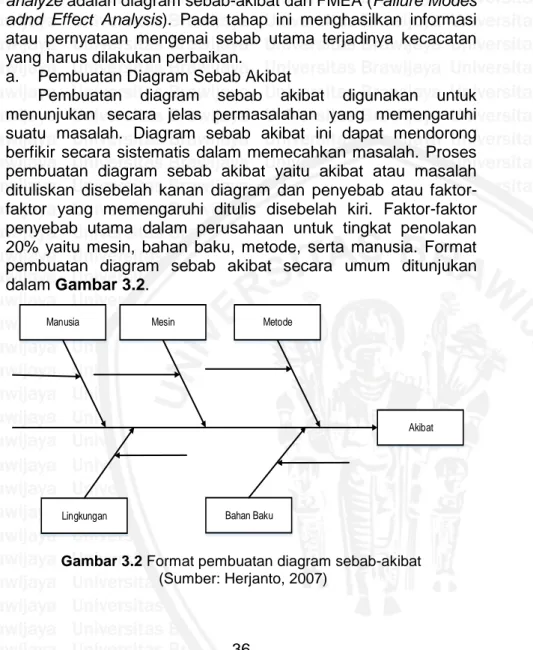
Dokumen terkait