This book is a text on aerospace materials derived from presentations given at the first Oxford-Kobe Materials Seminar, held at the Kobe Institute on 22-25 September 1998. The Chairman of the Kobe Institute Committee in the UK is Sir Peter Williams, Master of St Catherine's College; the director of the Kobe Institute's board is Dr. Yasutomi Nishizuka; the academic director is Dr. Helen Mardon, Oxford University; and the bursar is Dr. Kaizaburo Saito. The Kobe Institute was established with the purpose of promoting the pursuit of education and research that promotes mutual understanding between Japan and other nations, and to contribute to collaboration and exchange between academics and industrial partners.
A key feature of the seminars is to provide a world-class forum focused on strengthening links between academia and industry in both Japan and the UK/Europe and promoting joint research on timely problems of common interest. The seminar was co-chaired by Professor Akihisa Inoue from Tohoku University, Professor Brian Cantor, Dr. Hazel Assender and Dr. Patrick Grant from Oxford University and Dr. Kaizaburo Saito of the Kobe Institute. The seminar was sponsored by Kobe Institute, St Catherine's College, Oxford Center for Advanced Materials and Composites, ONERA, Dowty Aerospace Propellers, Ishikawajima-Harima Heavy Industries and Kobe Steel.
The editors would like to thank the following: The Kobe Institute Committee at St Catherine's College, University of Oxford who agreed to support the Oxford–. The opinions expressed are the author's and are offered in the interest of discussion.
INDUSTRIAL APPLICATIONS
Dependence of the threshold stress for stress corrosion cracking on grain aspect ratio. Another important point is the effect of thermal aging on the damage resistance properties of carbon fiber reinforced polymers. If the aging temperature is 180 °C, oxidation is observed at the exposed edges of the samples under isothermal conditions, as shown in Figure 3.6(a).
All the tubes in the EOB are made of carbon fiber composite, using high modulus fibers. Thermogravimetric data in N2 flow of the novel poly {(phenylsilylene) ethynylene-1,3-phenyleneethynylene} (MSP-1), PI(BPDA/PDA) and their 1/1 blend films. Both factors are limited by the temperature capacity of the materials available and the cooling technology used.
In addition, the layer acts as a bonding layer to prevent tearing of the outer layer of the coating - the thermal barrier coating. This eliminates the need for heavy disc drilling, giving weight savings of 40%. The turbine inlet temperature achieved in the M88 engine of the Rafale fighter jet is already of the order of 15808C.
It is universally recognized that bond layers for thermal barrier coatings have a strong effect on the thermal fatigue life of ceramics.
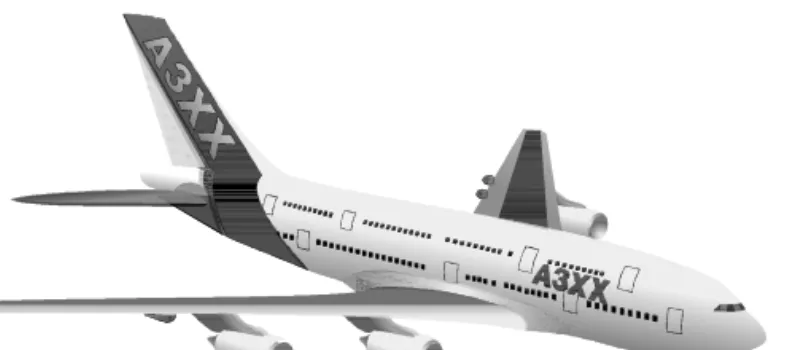
LIGHTWEIGHT MATERIALS
The final four chapters of the section describe developments in polymer matrix composite materials for aerospace applications. The performance of transport aircraft can be measured in terms of transport cost per passenger mile or cargo mile. Analogous comments can be made on the potential difficulties in repairing Al-Li alloys and especially on the impact of lithium occurrence in the aluminum scrap cycle.
Improvements in the performance of Al-Li alloys have been achieved over the past decade by eradicating some of the persistent problems hindering their application. The significant increase in performance of the titanium alloys and titanium-based intermetallic alloys in the UK should not be underestimated. The derivation of new nickel superalloys for high temperature turbine application and the associated manufacturing technologies can be traced back to the inception of the gas turbine using Nimonic 80 in the 1940s.
Regions with locally high or low crack growth resistance give rise to pinning and drag of the crack front. These aluminum-based alloys are known to have been developed using the following strengthening mechanisms: (1) solid solution strengthening, (2) precipitation strengthening, (3) grain size refinement strengthening, (4) dispersion strengthening, (5) work hardening and (6) fiber reinforcement. In this chapter we review our recent results on the synthesis and mechanical properties of the non-equilibrium aluminum-based alloys shown in figure 11.1.
The nanostructured state is also expected to exhibit an increase in the stability of the supercooled liquid, versus the transition to a crystalline phase. This suggests that crack propagation with accompanying microcracks has a significant impact on the overall fracture of MMC. Various characteristics of the reinforcement, such as shape, size, distribution, volume fraction and orientation angle in the case of fibers, are entered in advance.
When a microcrack exists before the main crack, the crack will be deflected as shown in figure 12.2. In such a case, dissolved atoms (i.e., magnesium) segregate into the matrix in the vicinity of the interface. The values of the solvus temperatures therefore vary with distance from the reinforcement due to segregation of solute in the MMC.
Effects of the existence of a precipitation-free zone on the distribution of effective plastic strain in the matrix. In the case of a multi-walled nanotube, the inner tube and the structure telescope from the outer sheath which is well bonded to the matrix resin. In the mid-1980s, the concept of a thermoplastic resin film interlayer was proposed by the American Cyanamid Company (now Cytec-Fiberite) [5].
The chemical structures of the oligomers and the formulated molecular weights (FMW) are shown in figure 14.1.
![Figure 9.2. The impact of materials performance on potential range and mass of a second- second-generation supersonic transport aircraft (after Quist [2]).](https://thumb-ap.123doks.com/thumbv2/123dok/10240880.0/103.663.77.558.106.412/figure-materials-performance-potential-generation-supersonic-transport-aircraft.webp)