In the first phases of the project, the main goal was to define the project problem statement, purpose and scope. The next step was to identify which technology would best suit the project and research each option extensively.
Introduction and Purpose of Study
Company Background
Facility Background
Project Background
Problem Statement
Project Aim
- Aim
- Objectives
- Action
Project Scope
Document Structure
In order to determine the main requirements of the new system, a requirements study had to be carried out. Evaluating these six criteria will help TFM ensure that the new system is viable at all levels of the business. The implementation of the system will take place with the help of two external consulting companies, RedBrush Solutions and AccTech Systems.
The implementation of the new system will only begin when the necessary steps to define and justify the system have been completed. Once the system has been properly implemented, it is extremely important to ensure that all employees are familiar with the use of the new technology. The PO number is used to track the purchase order on the system and to confirm receipt of the parts later.
Scanning the barcodes should eliminate much of the typing and should automatically update information on the system as needed. This system will adequately address most of the system requirements identified during the PIECES analysis. This system will address only some of the system requirements identified during the PIECES analysis.
The MO must then be placed in the document box of the next manufacturing process. The analytical hierarchy process (AHP) was then used to determine the technical requirements of the barcoding system.
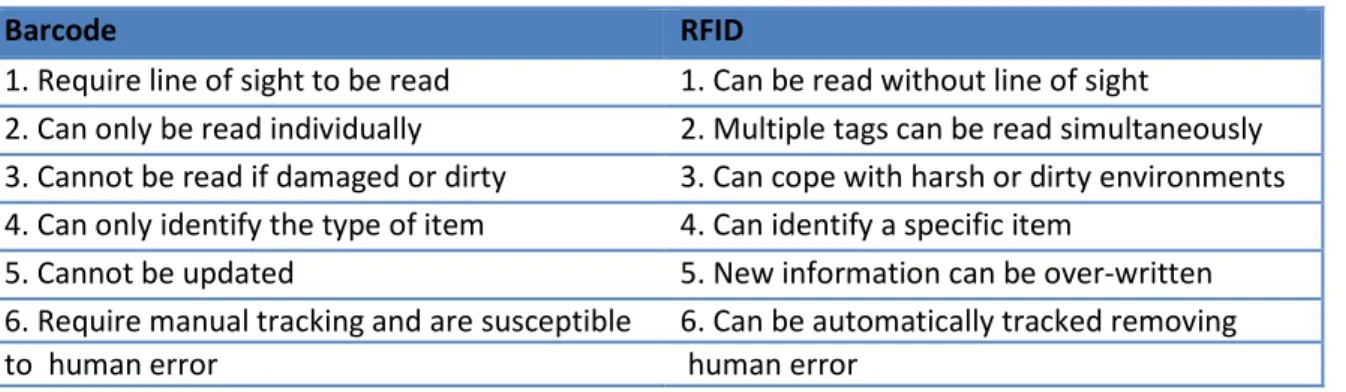
Introduction and Purpose of study
Literature Review and Selection of Appropriate Technologies
While barcodes require scanning, RFID tags can be scanned remotely. By following the right steps this system can be implemented successfully and provide a comprehensive solution to the company's problems.
Methods, Tools and Techniques
Information requirements include the quality, timeliness, accuracy levels and format of the information entered into the system. Financial requirements are used to identify areas where costs can be saved and profits can be increased by implementing the new system. Technical feasibility is a measure of how the technical aspects of the project will be implemented and maintained.
Legal feasibility is not such a critical issue in the case of TFM, as the implementation of the system does not directly affect contractual obligations towards their customers. The most critical phase of this project is the successful implementation and integration of the new system. This training session will be facilitated by key persons involved in the planning and implementation of the project.
A key aspect of implementation and training is to ensure that all employees are aware of the correct operating procedures to be followed when using the new system.

Application of Methods, Tools and Techniques
Once the receiving department has verified the contents of the delivery, the purchase order can be closed in the system, automatically updating stock levels in the ERP system. When the MO is marked as open in the system, the required raw materials (RM) are transferred to work in process (WIP), which in turn updates the RM inventory levels in the ERP system. When a GA order is opened in the system, the corresponding parts and assemblies are transferred from inventory to WIP in the ERP system.
After a thorough quality check, the GA order is transferred to the receiving department and the GA order and job card are closed in the system. If a part is captured in the system as soon as it is manufactured, it can be transferred directly to the next step in the process if necessary. The system should also help TFM reduce the number of parts outsourced for avoidable emergencies.
The barcode system should enable TFM to reduce the time and effort required to record information on the system.
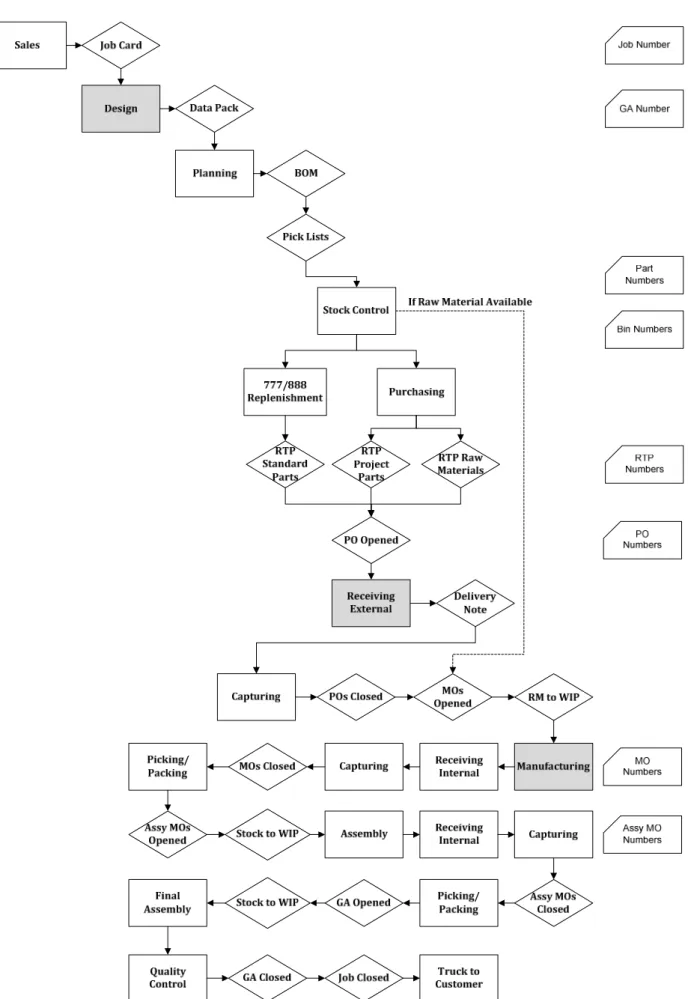
Implementation Plan and Operating Procedures
Each of these processes is assigned a station number which is specified on the relevant MO. Scan the purchase order number on the purchase order control sheet to indicate to the system which document is being processed. Scan the purchase order number to close the purchase order on the ERP system if all the parts have been received correctly.
If the purchase order is incomplete, mark the purchase order as partially completed in the ERP system. Scan the production order once all parts are completed and placed in the bin. When all parts have been received, close the production order in the ERP system.
If the production order is incomplete, mark the production order as partially completed in the ERP system.

Conclusions and Recommendations
Barcodes: A competitive tool for improved supply chain management in the fast moving consumer goods (FCMG) industry. Retrieved May 4, 2012, from Automation Mag News: http://www.automationmag.com/news/case-study-barcode-scanners-eliminate- excessive-paperwork.html. Retrieved September 4, 2012, from Zebra White Papers: http://www.zebra.com/content/dam/zebra/white-papers/en-us/barcoding-101-en-us.pdf.
Literature Review
Bar-coding
- History
- Definitions
Barcodes first appeared in 1966 and by 1970 the first Universal Grocery Products Identification Code (UGPIC) was developed by a company called Logicon Inc. The American company Monarch Marking and the British company Plessey Telecommunications were the first companies to produce barcode equipment for industrial use.
Radio-frequency Identification (RFID)
- History
- Definitions
Bar-coding versus RFID
Technical Specifications of Chosen Technology
- Barcode Types
- Barcode Scanner Types
- Barcode Reader Connection Types
- Barcode Printer Types
Wired barcode readers connect to the company's computers through a direct universal serial bus (USB) connection. The main advantage of wired barcode readers is the cost, as they are considerably cheaper than the wireless options.

Analytic Decision Making
Bar-coding in the industry
- Case Study 1: Barrett Firearm Manufacturing Inc
- Case Study 2: Flexpipe Systems Inc
- Case Study 3: Aesica Pharmaceuticals
- Case Study 4: Industrial Electronic Appliance Manufacturer
- How does this relate to TFM?
The products produced by the company are used in the collection of oil and gas, so they must be manufactured in a way that ensures environmental safety. For this reason, the company has decided that it is extremely important to be able to track specific batches and their locations in the event of a recall. The company also realized that they were doing a lot of non-value-added work by entering all the information into the system manually.
To address all the identified issues, the company decided to implement a bar-coding system with the help of an external consulting firm. After implementing the system, the company has minimized the time it takes to track down a problem group and recall it over the next few days to a quick ten-minute database search. By placing various scanners at strategic locations along the production line, the company was able to automate the data capture process.
The company wants to be able to use a system to keep inventory levels up-to-date and accurately manage important process documents.
Material and Information Flow Diagram
Requirements Study
Feasibility Analysis
Implementation and Integration
Training
Material and Information Flow Diagram
- General Order Process
- Stock Take
- Process Shortcomings
- Remedying process shortcomings
If a PO is not complete, the PO will be marked as partially complete indicating to the employees that not all parts have been received. The parts are then manufactured according to the relevant drawings and processes specified by the MO. Once all the parts are manufactured, they are transferred to the receiving department and placed in the correct container locations.
The parts and assemblies are then picked and packed and transferred to the final assembly department. Once all parts and assemblies have been attached to the truck chassis, the GA order is transferred to the quality control department. When the data controllers are satisfied that the count is accurate, the control sheets are transferred to the data capturers.
Because certain parts have already been transferred to the assembly departments, inventory controllers must conduct an inspection of the factory floor to capture any parts that are not in the correct bin locations.
Requirements Analysis
- Performance
- Information
- Economy
- Control
- Efficiency
- Service
- Physical
TFM should be able to control all access to the system, and each specific group of employees should be granted different levels of access. Some employees should be able to provide inputs to the system while others should only receive outputs from the system. The system must be able to accommodate different types of users, who are interested in different types of functions.
Extensive user manuals should be included with each barcode reader to ensure that employees can at any time resolve any errors encountered when using the readers. An operational manual should also be provided to ensure that employees know exactly what procedures must be followed during each step of the process. Adequate training sessions should be provided to ensure that employees are comfortable with the new technology and system.
These readers should be able to communicate wirelessly with the ERP system and should be reasonably robust as the working conditions are quite harsh.
Feasibility Analysis
Barcode Scanning Locations
They are also quite susceptible to damage if not handled and managed properly. Each barcode reader must be marked with a unique code and connected to its own docking station. Whenever the readers are not in use, they should be returned to these docking areas to ensure that each reader can be tracked whenever they are needed.
A checklist can be implemented to ensure the company knows who last used the reader, when it was checked out and when it was returned. Alternatively, the company may decide to assign each reader to a separate employee from each department, who will be responsible for keeping the reader secure, as well as scanning documents and related parts.
Manufacturing Department Data Capturing Area
Bar-coding Operating Procedures
Repeat this process every time 30% of the total parts have been processed to ensure that other stations can continue with their part of the process. Scan the process or station number each time parts are collected from a bin to indicate the next process is finishing. Enter the quantity of parts taken from each bin into the PDA barcode reader to indicate that parts have been transferred to work in process.
Deliver the bin with all required parts and the assembly production order to the assembly department. When all assemblies are completed, transfer the assembly and production assembly order to the shops. Scan the general assembly order number to indicate the start of the final assembly process.
Place printed barcode labels containing the bin number on each of the bin locations.
Training