The investigations carried out were on operating temperature, reactor type, reactor dimensions, residence time, reactor operating pressure, heating rate, presence of catalyst and rubber particle size. The use of the catalyst showed a positive impact on the oil yield, an increase from 49.92% to 51.7% was observed in the absence of the basic catalyst.
CHAPTER 1: Introduction
- Background
- Aims
- Objectives
- Dissertation structure
As part of the investigation, an economic feasibility study was conducted to understand whether the tire pyrolysis process is a profitable operation. Finally, a brief overview of the ASPEN plus simulation scheme of the tire pyrolysis process from the literature with the relevant reaction kinetics is given.
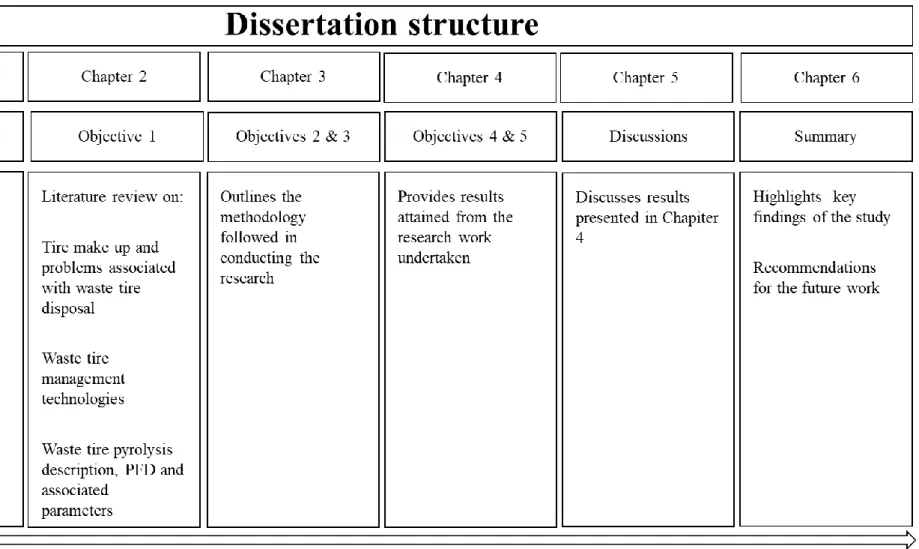
CHAPTER 2 : Literature review
Chapter overview
Tyre make-up
The numbering of the tire sections in table 2.2 of the tire sections corresponds to the numbering in figure 2.1. It can be noted that most of the parameters in Table 2.4 are percentages by weight, but the calorific value (CV) indicated with an asterisk (*) in superscript has different units, namely MJ/kJ.

Waste tyres environmental issues
Waste tyre management methods
- Landfilling and stockpiling
- Recycling and reuse
- Waste tyre retreatment
- Waste tyre thermal treatment technologies
- Gasification
- Pyrolysis of waste tyres
According to Kordoghli, et al. 2014) below is a compilation of areas where end-of-life tires can be reused (Table 2.5). The remanufactured tires are made from 15% less crude oil than new tires (Kordoghli, et al., 2014).
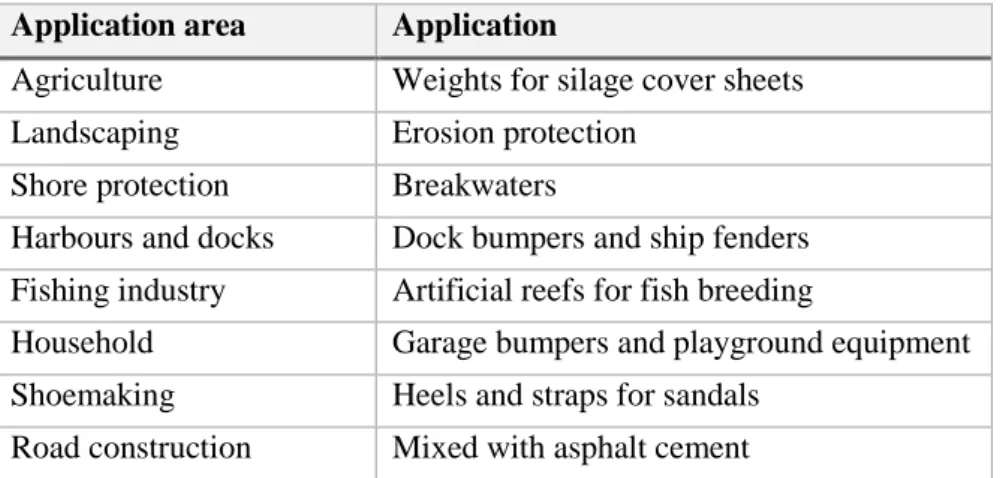
Factors affecting tyre pyrolysis
- Reactor type
- Pyrolysis reactor temperature
- Reactor pressure
- Resident time
- Catalyst
- Waste tyre particle size
- Feedstock composition
- Heating rate
- Steam incorporation
- Impact of operating parameters overview
Temperature is the main determining parameter responsible for the breakdown of tires and the volatilization of the solid material to gas. Optimization of the mentioned operating conditions mainly depends on the yield of oil derived from the tire.
Process modelling and simulation flowsheet
- Reactions and reaction kinetics
If necessary, simulations are useful to enable further studies without having to repeat the experiments (Foo, et al., 2005). In some cases, simulations have been instrumental in conducting studies that may be difficult or impossible to run using traditional means (Barberousse, et al., 2009). Waste tire pyrolysis process is no exception to this, among other authors, studies carried out by Olazar, et al.
Given the simulation evaluations and developments made in the field of tire pyrolysis simulation kinetics, this research study was conducted using a simulation approach. ASPEN plus has been used in a number of studies related to the tire pyrolysis process, below (Figure 2.7) is a description of an ASPEN tire pyrolysis flow sheet as developed by Ismail, et al (2016). Research studies have made great strides in the development of simulation models of tire pyrolysis processes that describe typical tire oil yields.
Based on the simplified equation 1 above, many research studies have developed kinetics that capture the products as aggregated components instead of the individual components that form coal, gas, and petroleum products. Different studies have developed different kinetics depending on the type of pyrolysis parameters used in the process, according to Ismail et al (2016) tire pyrolysis kinetics used in the ASPEN plus environment are generally based on Arrhenius equations as shown below (Equation 2 ).
Economics of waste tyre pyrolysis
Summary
Depending on the financial feasibility studies, a catalyst may be added to improve the oil production yield and quality. In terms of the optimum operating temperature, based on the reported findings in Table 2.8 and Table 2.9, it can be observed that the optimum oil yield is generally achievable at temperatures averaging around 500 oC. The advantage of using reactors with some mixing helps speed up reaction time and thus improves turnaround time.
The secondary reactions negatively affect oil quality and yield, as they favor the reversion of formed gases back to coal products. The literature studies show that great progress has been made with the simulation studies, and a number of kinetics have been developed from experiments to mimic an actual pyrolysis process. From an economic point of view, literature studies show that waste tire pyrolysis process can be considered a feasible process, generally with payback periods of less than 4 years.
CHAPTER 3: Methodology
Overview of the chapter
Methodology followed in this study
Process description
- Assumptions
- Property method and stream class
- Feedstock
- Calculator blocks
- Reaction kinetics
- Optimum numerical model
Hence, the use of PR-BM in this study further validates its use in waste tire pyrolysis applications. The right choice of method for estimating different simulation aspects plays a crucial role in the reliability of the findings. Figures 3.6, 3.7 and 3.8 show the input of the band proxanal, ultanal and sulfanal in the ASPEN simulation environment.
The block naming on Table 3.14 has been kept consistent with the naming used in the simulation environment. In the development of the simulation, calculation blocks were used to perform calculations that could not be modeled using the basic ASPEN simulation Palette blocks. The Fortran statements were used in the execution of the calculation blocks used in the simulation environment.
Reported discrepancies were attributed to the difference in heating rates between the experiment and the model. As explained above, the heating rate is an unstable parameter and can be difficult to simulate in the ASPEN plus environment.
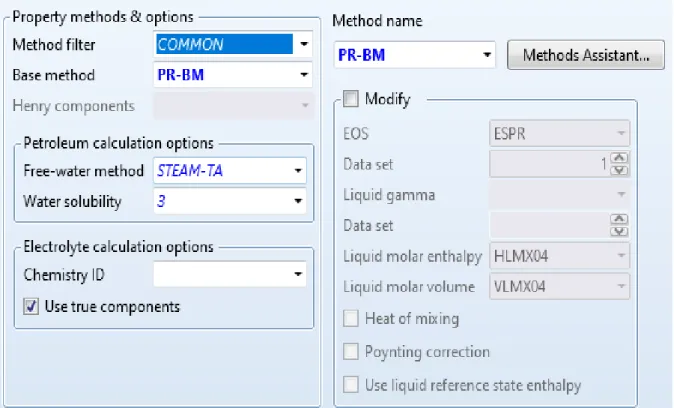
Economic evaluation of waste tyre pyrolysis
As outlined above, a lot of research work on tire pyrolysis modeling was done using lump parameter kinetics. However, the complete reactions depicted in Appendices A and B are only crucial to investigate in cases where the final properties of the final products are taken into account. As such, complete reactions are more important in the case of characterizing tire-derived pyrolysis oil versus crude oil-derived diesel.
A number of aspects can be considered, these may be but not limited to the viscosity, CV and sulfur content. As such, the layout of the study by means of knob parameter kinetics was deemed sufficient for the goals and objectives outlined for this study.
Summary
CHAPTER 4: Results
- Model validation
- Physical property selection
- Sensitivity analysis: Impact of reactor type and temperature
- Sensitivity analysis: Impact of reactor type at 550 o C
- Sensitivity analysis: Impact of residence time and reactor size
- Sensitivity analysis: Impact of reactor pressure
- Sensitivity analysis: Impact of reactor heating rate
- Sensitivity analysis: Impact of the presence of the catalyst
- Sensitivity analysis: Impact of tyre particle size
- Optimized numerical approach
- Economic evaluation
According to the results, it can be observed that the increase in oil yield results in a decrease in charcoal generated. It can be observed that char was highest on the PFR compared to the CSTR and the furnace reactor. An increase in PFR length is found to have a small positive effect on oil yield, the increase was not as significant as that observed with temperature.
Reactor operating pressure plays a key role in oil recovery in waste tire pyrolysis. As seen in the effect of temperature, it can be seen that the increase in oil yield is due to the decrease in char produced. Page | 61 Figure 4.6: Effect of reactor pressure on oil yield (wt.% is based on the weight of waste rubber).
In an investigation where the effect of a catalyst was investigated, it was observed that the presence of a catalyst has a large impact on oil yield, Figure 4.8 below shows that the presence of a catalyst results in a 1.8% point increase in oil yield. Page | 64 Figure 4.10: Optimization of particle size, feed rate and temperature for maximum oil yield (% wt are from . weight of waste rubber).
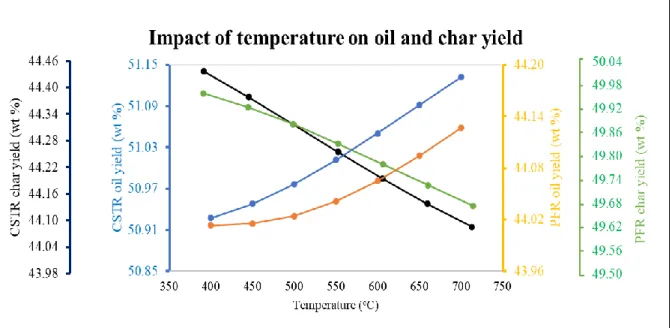
CHAPTER 5: Discussions
Impact of reactor size and residence time
The residence time is generally dependent on the flow rate, the size of the reactor and the particle size. In general, the large particle size requires larger reactor size to achieve longer residence time to achieve complete vaporization of the entire mass. PFR showed that larger diameter and longer length of the reactor had a positive influence on the oil yield.
Operating the pyrolysis reactor at a lower pressure reduces the occurrence of secondary reactions in the gas phase. The use of a catalyst generally has a positive effect on the yield and quality of the obtained oil. The investigation carried out in this study focused on the overall effect of catalyst use on oil recovery.
Based on Figure 4.8, it was observed that the presence of the catalyst resulted in an increase in oil yield from 49.92 to 51.7. Depending on the temperature and residence time, the large particle size can result in the interior of the particles not being heated.
Optimized numerical model
When the studies were carried out in the simulation, it was observed that the oil yield increases with an increase in the heating rate. When the heating rate was increased to 20 K/min, the oil yield was found to decrease to 50.87. Two kinetics were used for this study, the first for the baseline scenario and the second for the presence of the catalyst.
Catalyst use requires cost consideration, particularly from the perspective of the benefits derived versus the cost associated with the use of the catalyst. Thus, this can cause some parts of the rubber to remain unreacted and thus cause it to contribute more to the unreacted carbon and actually favor more carbon production. The results shown in Figure 4.9 showed that the lower size range class (0.1 mm – 0.8 mm) exhibited higher oil yield compared to the higher size class.
Page | 71, a numerical model from the literature was used in this study to understand the optimization of various parameters. The benchmark oil recovery for the unoptimized numerical study was reported to be 26.3% (Figure 4.10).
Economic evaluation
These results were for a laboratory scale study, under the stated optimum conditions the optimum oil yield of 47.90% was achieved. A model has been developed for the pyrolysis process of waste tires using ASPEN Plus computer simulation software. Using the developed simulation, a number of studies have been carried out to gain insight into the impact of the most important process parameters on the oil yield of tires.
Studies were conducted on the operating temperature, reactor type, reactor size and residence time, reactor operating pressure, heating rate, presence of catalyst, and belt particle size. The research into the reactor type showed that the reactors with some degree of mixing generally yield a higher oil yield. An increase in reactor size showed positive results on oil yield, but there were limitations on the maximum yields achievable.
Operating pressure research done on the CSTR showed a decrease in oil yield with an increase in operating pressure. The presented results showed that the lower class of the size range (0.1 mm – 0.8 mm) results in higher oil yield in the investigated temperature range. A numerical model from the literature survey based on laboratory studies, incorporating particle size, temperature and feed rate was used to achieve optimal operating conditions for maximum oil yield.
Based on the results of this study, it can be concluded that the optimum oil yield is obtainable from the CSTR operating at a temperature range between 400 oC and 550 oC, band particle size less than 1 mm, operating pressure below 1 atm, heating rate between 10 -15 K/min and residence time of less than 1.
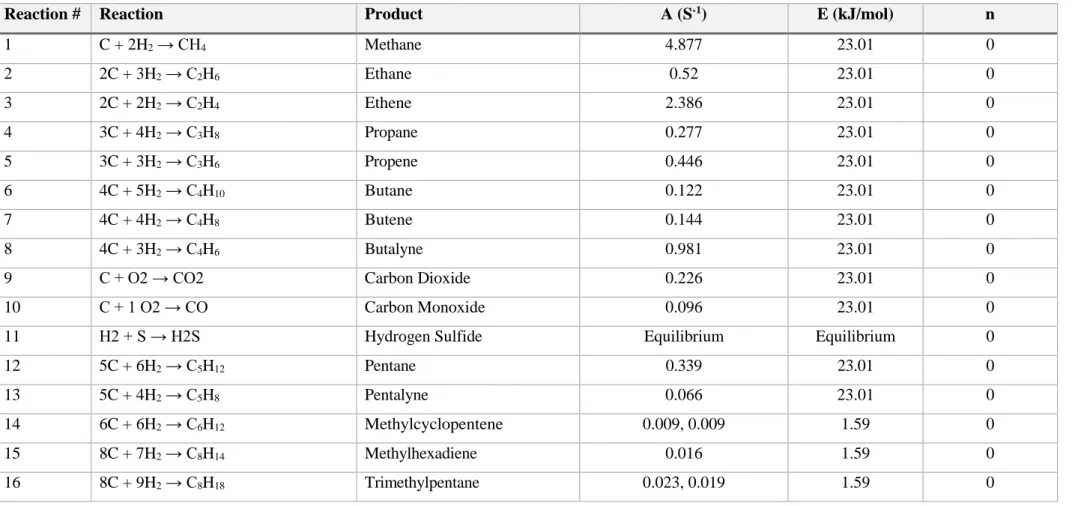
CHAPTER 6: Conclusions and recommendations
APPENDICES
APPENDIX A: Comprehensive tyre pyrolysis reactions
APPENDIX B : ASPEN plus components