PROSES ASSESSIBILITY AND DUCTING UTILITIES DENGAN PENDEKATAN LEAN CONSTRUCTION
Teks penuh
Gambar
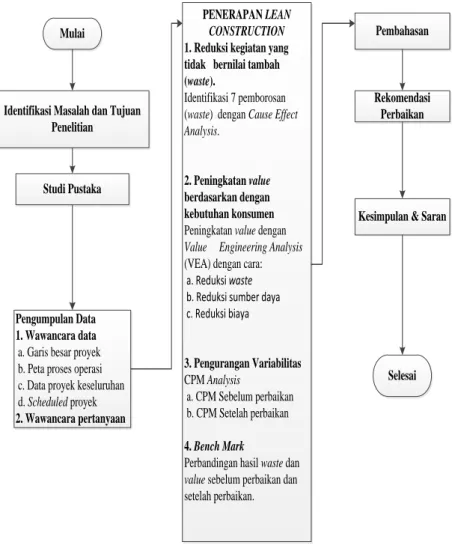
Dokumen terkait
Sementara itu, Kunandar (2013: 123) menyatakan, penilaian kompetensi pengetahuan sebagai berikut. Guru dapat melakukan penilaian kompetensi pengetahuan siswa dengan
Seseorang yang menderita hipertensi disebabkan karena ada masalah dari dalam diri atau dari luar, kemudian penderita hipertensi tersebut memiliki keyakinan
Perselisihan dalam Dewan Keamanan tentang aksi militer, dan intervensi dipandang sebagai kegagalan untuk mencegah Genosida Rwanda 1994, gagal untuk menyediakan bantuan
Untuk memperoleh kekerasan permukaan , tahan aus dan mempunyai inti yang ulet serta tangguh maka, Carburizing adalah salah satu cara perlakuan yang dapat diberikan pada baja
Jenis penelitian yang dipakai adalah penelitian hukum normatif, yaitu penelitian yang dilakukan berdasarkan perundang-undangan.Perundang-undangan yang akan dibahas dalam
Faktor lain juga sangat menentukan keberhasilan riset saya di Jepang adalah; saya memulai riset ketika laboratorium hanya memiliki empat orang peneliti (profesor,
Hasil pengujian regresi menunjukkan bahwa risiko perusahaan, kualitas audit, dan komite audit berpengaruh terhadap tax avoidance masing-masing sebesar 0,012, 0,005, dan 0,017..
Secara simultan menunjukkan bahwa kualitas pelayanan, kinerja paramedis dan sistem persediaan obat-obatan berpengaruh positif dan signifikansi terhadap tingkat