40 Plot hubungan variasi pengairan 7 hari terhadap kestabilan pada kondisi kadar aspal optimum dengan waktu pengairan 30 menit.

1 BABI
Rumusan Masalah
Bagaimana pengaruh penambahan ban sobek terhadap karakteristik campuran AC-WC dengan variasi celup berulang?
Tujuan dan Manfaat
Pokok Bahasa Dan Batasan Masalah Batasan masalah pada penelitian ini adalah
- Bab II Tinjauan Pustaka
- Bab III Metode Penelitian
- Bab IV Hasil dan Pembahasan
Bab ini membahas tentang teori dan rumusan yang digunakan untuk mendukung penelitian yang diperoleh dari berbagai sumber. Bab ini menjelaskan metode-metode yang digunakan dalam penelitian untuk data-data yang dibutuhkan dalam pengolahan data.
1 BAB II
Konstruksi Perkerasan Jalan Raya
Konstruksi perkerasan lentur (flexible pavetmanet), Merupakan perkerasan yang menggunakan bahan pengikat bitumen yang bersifat lentur terutama pada cuaca panas. Perkerasan lentur mendistribusikan beban lalu lintas ke lapisan tanah bawah yang dipadatkan melalui beberapa lapisan sebagai berikut.

5 Kekurangan perkerasan lentur
Lapis Aspal Beton (Laston)
Menurut Spesifikasi Campuran Aspal Departemen Pekerjaan Umum Tahun 2010, Laston (AC) terdiri dari tiga jenis campuran, yaitu Laston Wear Layer (AC-WC), Laston Binder Layer (AC-BC) dan Laston Foundation Layer (AC-Base). dengan ukuran agregat maksimum masing-masing campuran adalah 19mm, 25,4mm, 37,5mm. Peraturan mengenai sifat-sifat aspal campuran panas di Indonesia seperti campuran aspal tipe AC-WC merupakan peraturan yang dikeluarkan oleh Kementerian Permukiman dan Prasarana Wilayah bersama-sama dengan jalan raya, sehingga hal tersebut menjadi acuan dalam penelitian ini, seperti terlihat pada tabel 2.

10 Sifat-Sifat Campuran
Karakteristik Campuran Aspal Beton
Stabilitas, yaitu kekuatan campuran aspal dalam menahan deformasi akibat beban tetap dan beban berulang tanpa mengalami keruntuhan (pelelehan plastis). Untuk mencapai fleksibilitas yang tinggi diperlukan VMA yang besar, VIM yang kecil dan penggunaan aspal penetrasi yang tinggi.
Bahan Penyususun Perkerasan Jalan
- Agregat
Faktor-faktor yang mempengaruhi kemampuan kerja antara lain gradasi agregat, dimana agregat yang bergradasi baik lebih mudah untuk dikerjakan, dan kandungan bahan pengisi, dimana terlalu banyak bahan pengisi akan mempersulit pengaplikasian. Agregat kasar secara umum harus memenuhi persyaratan yang telah ditentukan sesuai ketentuan yang ada, seperti terlihat pada tabel 2.
14 Tabel 2. 3 Ketentuan Agregat Kasar
15 b. Agregat Halus
Sedangkan batuan beku ekstrusif terbentuk dari magma yang muncul ke permukaan bumi saat terjadi letusan gunung berapi dan aktivitas geologi lainnya. Batuan metamorf, disebut juga batuan metamorf, berasal dari batuan sedimen atau batuan beku yang telah diubah oleh tekanan dan panas yang kuat di dalam bumi atau oleh reaksi kimia yang intens.
18 b. Agregat yang Diproses
Pada campuran aspal, hanya menggunakan agregat bersudut atau bulat tidak akan menghasilkan campuran aspal yang baik. Agregat hidrofobik (yang tidak menyukai air) merupakan agregat yang mempunyai sifat daya lekat yang tinggi terhadap aspal, contoh agregat tersebut adalah batu kapur dan dolomit.
23 2.7.2 Bahan Pengisi (Filler)
Aspal
Gradasi agregat mempengaruhi ukuran rongga dalam campuran dan menentukan kemampuan kerja serta stabilitas campuran. Grading padat merupakan grading agregat dimana terdapat butiran-butiran dari agregat kasar sampai agregat halus, sehingga disebut gradasi kontinyu atau gradasi baik.

29 Ukuran
- Ban bekas dan Perkerasan
Proses basah merupakan suatu cara pencampuran dimana sobekan ban bekas dimasukkan ke dalam aspal panas dan diaduk dengan kecepatan tinggi hingga homogen. Metode kering adalah metode pencampuran dimana ban bekas yang retak dimasukkan ke dalam agregat, yang dipanaskan sampai suhu pencampuran, setelah itu ditambahkan aspal panas.
Karakteristik Marshall
- Stabilitas (stability)
Pengurangan dalam jumlah asfalt dalam campuran menyebabkan lekatan antara butiran agregat berkurangan, mengakibatkan pembebasan butiran (menggosok) dan mengelupas permukaan (pelucutan) pada lapisan turapan. Semakin tinggi nilai VFA bermakna semakin banyak lompang dalam campuran yang diisi asfalt, jadi ketaktelapan air dan udara campuran juga akan menjadi lebih tinggi tanpa mengira nilainya.
42 campuran
Penelitian Terdahulu
Namun penambahan kandungan karet dapat menambah rongga terisi pada campuran, namun perlu diperhatikan bahwa penambahan kandungan karet 3% justru lebih banyak terisi rongga yang lebih rendah dibandingkan dengan kandungan karet. Hubungan MQ dengan penambahan aspal dan kadar debu pada ban karet menunjukkan bahwa dengan bertambahnya kadar karet maka nilai MQ tidak memberikan hasil yang konstan melainkan menurun pada kisaran 5,0%-5,5% dan sedangkan pada kisaran 5,5%. - 6% dari MQ sebenarnya berlanjut.
1 BABIII
3 1.2. Lokasi Material
Lokasi Penelitian
Waktu Pelaksanaan
Persiapan Peralatan dan Pengambilan Sampel
- Pemeriksaan Analisa Saringan Agregat Kasar dan Halus a. Tujuan
4 3. Talam dan Kuas
Pemeriksaan Analisa Saringan Agregat Kasar dan Halus a. Tujuan
6 6. Bak Perendam
Penyelidikan ini bertujuan untuk mengetahui berat jenis (massa), berat jenis kering permukaan jenuh (SSD), berat jenis semu (apparent) dan serapan agregat halus.
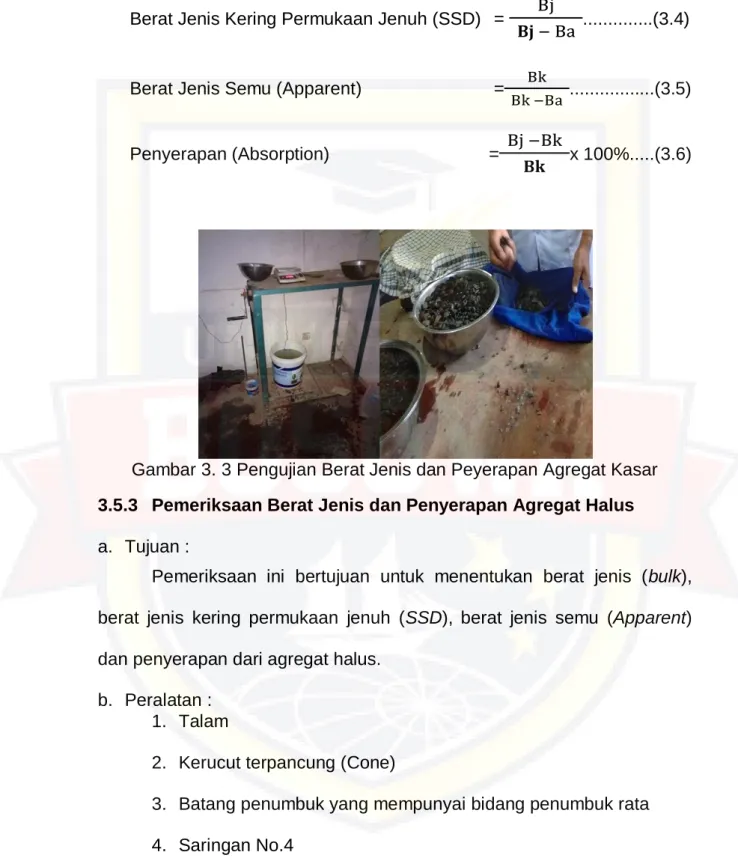
8 7. Air Suling
Keluarkan benda uji, keringkan dalam oven bersuhu 110ºC, kemudian dinginkan benda uji dan timbang (BK). Tentukan berat piknometer yang berisi air dan ukur suhu air tersebut hingga mencapai suhu baku 25ºC (B).

10 3.5.4 Pemeriksaan Abrasi
Pemeriksaan Kadar Lumpur Agregat Kasar a. Tujuan
Keluarkan sampel dari oven dan dinginkan hingga suhu kamar, kemudian timbang sampel.

Pemeriksaan Berat Jenis Aspal a. Tujuan
15 b. Peralatan
Isi piknometer yang berisi benda uji dengan air suling dan diamkan hingga keluar gelembung udara, kemudian tekan tutupnya dengan kuat. Pemeriksaan ini bertujuan untuk mengukur jarak terjauh yang dapat ditarik antara dua cetakan yang diisi aspal minyak sebelum pecah pada suhu dan kecepatan penarikan tertentu.
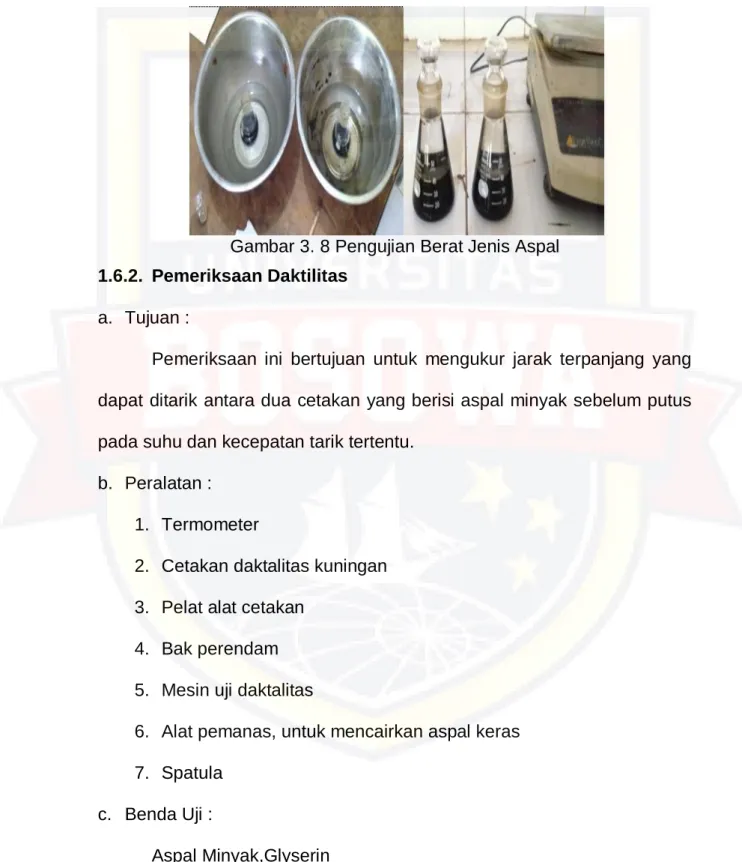
18 d. Prosedur Kerja
Pemeriksaan Titik Lembek Aspal a. Tujuan
Kemudian masukkan semua peralatan ke dalam wadah kaca. Isi wadah dengan air suling yang bersuhu 5ºC dan ketinggian air bervariasi dari mm, letakkan termometer yang sesuai untuk pekerjaan ini di antara kedua benda uji. Sesuaikan jarak antara permukaan pelat dasar dan bagian bawah benda uji menjadi 25,4 mm.
25 c. Benda Uji
Penentuan Jumlah dan Persiapan Benda Uji
- Penentuan Jumlah Benda Uji
Pengujian Stabilitas Sisa (60 0) Kadar
Pengujian variasi Parutan Ban Bekas (60ºC) KadarParutan
- Pembuatan Benda Uji I a. Peralatan
- Pengetesan Benda Uji I Dengan Alat Marshall
Sebelum dilakukan pengujian dengan alat Marshall, benda uji terlebih dahulu direndam dalam air bersuhu 60ºC selama 30 menit. Dengan pengujian sampel akan diperoleh data kestabilan dan aliran sebagai dasar penentuan sifat-sifat campuran.
31 1.10. Pembuatan Benda Uji
Tuangkan aspal tembus 60/70 dan plastik yang sudah dipanaskan ke dalam campuran agregat dalam panci sesuai volume lalu aduk hingga tercampur rata.
1 BAB IV
Hasil Pemeriksaan Karakteristik Agregat
Bj = Berat permukaan tepu objek ujian kering (SSD) Ba = Berat objek ujian dalam air.

- Hasil Pemeriksaan Karakteristik Aspal Minyak
- Penentuan Komposisi Agregat Gabungan
- Penentuan Berat Agregat dan Aspal dalam Campuran
- Perhitungan Berat Jenis dan Penyerapan Campuran Berdasarkan hasil pemeriksaan berat jenis dan penyerapan
- Data Uji Marshall untuk Penentuan Kadar Aspal Optimum Pada pengujian benda uji dengan alat marshall, diperoleh dua data
Contoh perhitungan nilai persentase total agregat untuk aspal campuran panas (AC – WC) sebagai berikut. Selanjutnya nilai persentase total agregat campuran aspal hangat (AC-WC) berdasarkan hasil perhitungan dapat dilihat pada lampiran.

12 Kepadatan
Pembuatan Benda Uji dengan Pemabahan Parutan Ban Bekas Terhadap Agregat Halus Pada Perendaman Berulang
- Perhitungan Berat Agregat Dan Berat Aspal Menggunakan Kadar Aspal Optimum Dengan Menggunakan Parutan Ban
- Data Hasil Uji Dengan Alat Marshall Yang Diperoleh Dengan Menggunakan Kadar Aspal Optimum
- Analisis Hasil Pengujian Dengan Penambahan Parutan Ban Bekas 5% Terhadap Aregat Halus Pada Campuran Beton Aspal
6 Diagram hubungan variasi kadar ban 5% dan debit pada kondisi kadar aspal optimum dengan waktu perendaman 30 menit pada suhu 60°C. 8 Diagram hubungan variasi kadar ban 5% dan VIM pada kondisi kadar aspal optimal dengan waktu perendaman 30 menit pada suhu 60°C.

Varisi Perendaman
- Analisis Hasil Pengujian Dengan Penambahan Parutan Ban 7%
10 diagram hubungan variasi kadar kisi sabuk beras 5% dengan VMA pada kondisi kadar aspal optimum dengan waktu perendaman 30 menit pada suhu 60°C. Hasil uji stabilitas dengan variasi tyre grid pada kadar aspal optimum ditunjukkan pada Gambar 4.12.

32 d. Marshall Questient
15 Bagan hubungan variasi grid ban bekas 7% terhadap VIM pada kondisi kadar aspal optimal dari waktu ke waktu. 16 Diagram hubungan variasi kisi ban 7% terhadap VFB pada kondisi kadar aspal optimal dengan waktu perendaman 30 menit pada suhu 60°C.

Variasi Perendaman
- Analisis Hasil Pengujian Dengan Penambahan Parutan Ban Bekas 10% Pada Campuran Beton Aspal Panas AC-WC
- 37 b. Stabilitas Minimum 800 (Kg)
- 39 d. Marshall Questient
- Analisis Hasil Pengujian Dengan Penambahan Parutan Ban 14% Pada Campuran Beton Aspal Panas AC-WC
- 45 c. Pelelehan (Flow) Minimum 2 - 4 (mm)
- 46 d. Marshall Questient
- 49 g. Rongga Dalam Agregat (VMA) Min 15%
- Perhitungan Berat Agregat Dan Berat Aspal Menggunakan Kadar Aspal Optimum Dengan menggunakan bahan Tambah
- Analisis Hasil Pengujian Dengan Penambahan Parutan Ban Bekas Terhadap Agregat Halus Pada Campuran Beton Aspal
23 Diagram hubungan variasi grid ban 10% terhadap VFB pada kondisi kadar aspal optimum dengan lama perendaman 30 menit pada suhu 60°C. 30 Diagram hubungan variasi kadar grid ban 14% terhadap VFB pada kondisi kadar aspal optimum dengan waktu perendaman 30 menit pada suhu 60°C.
Variasi kadar parutan ban bekas (%) Grafik Kepadatan Variasi Perendaman 0
Gambar 4.32 menunjukkan bahwa variasi kandungan parutan ban pada campuran yang direndam selama 0 hari tidak berpengaruh nyata terhadap nilai densitas. Pada kadar parutan tape 10% nilai yang didapat adalah 1,98 dan pada kadar 14% nilai densitas yang didapat adalah 1,98.
Hari
Gambar 4.33 diatas menunjukkan bahwa kestabilan campuran cenderung menurun apabila digunakan variasi parutan pita pada campuran yang direndam selama 0 hari. Nilai kestabilan mengalami penurunan pada isi ban parut 5% nilai kestabilan yang diperoleh sebesar 929,61 kg, pada isi ban parut 7% nilainya sebesar 896,98 kg, pada isi ban parut 10% nilainya sebesar 764,87 kg dan pada isi ban parut 14% nilai kestabilannya adalah 764,87 kg. nilai 764,87 kg. Nilai rendemennya adalah 759,90 kg, karena semakin banyak parutan ban yang ditambahkan ke dalam campuran maka daya rekat aspal semakin berkurang.
Variasi kadar parutan ban bekas (%) Grafik Stabiltas Variasi Perendaman 0
Gambar 4.34 terlihat penambahan karet abon pada campuran yang direndam selama 0 hari terlihat pada karet abon 5%, nilai alir yang diperoleh sebesar 6,10 mm pada karet abon 7%, nilai 6,17 mm pada karet abon 10%, nilainya adalah 7,80 dan pada 14% dari kisi ban, nilai yang diperoleh adalah 9,0 mm. Nilai flow pada perendaman 0 hari semakin besar karena semakin banyak karet suwir yang ditambahkan pada campuran maka aspal yang digunakan semakin sedikit sehingga mengakibatkan penurunan daya rekat aspal.
Variasi kadar parutan ban bekas (%) Grafik Flow Variasi Perendaman 0 Hari
56 d. Marshall Questient
Variasi kadar parutan ban bekas (%)
Terlihat pada gambar di atas bahwa perbedaan level grid ban menyebabkan nilai koefisien Marshall juga berbeda. Gambar 4.36 menunjukkan bahwa penambahan parutan tebu pada campuran perendaman 0 hari menghasilkan nilai VIM sebesar 5%, 7,21% pada nilai 7%, nilai sebesar 6,05% pada kadar 10%, nilai sebesar 17,23% dan pada nilai 14% diperoleh sebesar 15,91%.
Variasi kadar parutan ban bekas (%) Grafik VIM Variasi Perendaman 0 Hari
Nilai VIM tidak terlalu banyak berubah, hal ini dikarenakan penambahan sobekan ban pada campuran akan membuat adanya rongga pada campuran. Gambar 4.37 menunjukkan penambahan abon ban pada campuran direndam selama 0 hari dengan penambahan 5%.
Variasi kadar parutan ban bekas (%) Grafik VFB Variasi Perendaman 0 Hari
38 Diagram hubungan variasi perendaman 0 hari dengan VMA pada kondisi kadar aspal optimum dengan lama perendaman 30 menit pada suhu 60°C. Gambar 4.38 menunjukkan bahwa penambahan suwir ban pada campuran aspal press yang direndam selama 0 hari menyebabkan nilai VMA berubah, hal ini disebabkan penambahan suwir ban pada campuran aspal press mengakibatkan perubahan susunan agregat sehingga menambah rongga pada campuran aspal press. mineral agregat.
Variasi kadar parutan ban bekas (%) Grafik VMA Variasi Perendaman 0 Hari
Analisis Hasil Pengujian Dengan Penambahan Parutan Ban Bekas Terhadap Agregat Halus Pada Campuran Beton Aspal
Nilai kepadatan campuran beton aspal lapis AC-WC dengan perendaman 0 hari dapat dilihat pada gambar 4.32 untuk campuran beton aspal lapis AC-WC pada kondisi kadar aspal optimal. Dari gambar 4.39 terlihat bahwa variasi kandungan retak ban pada campuran yang direndam selama 7 hari adalah nilai densitasnya.
Variasi kadar parutan ban bekas (%) Grafik Kepadatan Variasi Perendaman 7
Hasil pengujian stabilitas dengan berbagai versi kisi ban pada kadar aspal optimal ditunjukkan pada Gambar 4.40. Gambar 4.40 di atas menunjukkan bahwa stabilitas kompon menurun dengan penggunaan ban versi sobek dalam kompon yang direndam selama 7 hari.
Variasi kadar parutan ban bekas (%) Grafik Stabiltas Variasi Perendaman 7 Hari
Pada kadar 5% nilai densitas yang diperoleh adalah 2,13, pada kadar 7% nilai densitas yang diperoleh adalah 2,13, pada kadar 10% nilai densitas yang diperoleh adalah 1,98 dan pada kadar 14% nilai densitas yang diperoleh adalah 1,93. Nilai aliran mewakili besarnya deformasi yang terjadi pada suatu lapisan perkerasan akibat beban lalu lintas.
Variasi kadar parutan ban bekas (%) Grafik Flow Variasi Perendaman 7 Hari
Gambar 4.34 menunjukkan bahwa penambahan ban suwir pada campuran yang direndam selama 7 hari menyebabkan nilai Flow semakin besar, hal ini dikarenakan semakin banyak ban suwir yang ditambahkan pada campuran maka daya rekat aspal semakin menurun. Gambar 4.36 menunjukkan bahwa penambahan abon ban pada campuran yang direndam selama 0 hari menjadikan nilai VIM pada penambahan 5% pada campuran menjadi 11,21% pada kadar 7%, nilai VIM sebesar 11,25% pada kadar 10%. adalah 19,57% dan pada 14% nilai yang diperoleh adalah 19,57% yang semuanya tidak berada dalam batas spesifikasi.

Variasi kadar parutan ban bekas (%) Grafik VIM Variasi Perendaman 7 Hari
Ini karena banyaknya aspal yang mencari rongga kosong di bawah beban dan panas. 44 Diagram hubungan variasi pencelupan 7 hari terhadap VFB pada kondisi kadar aspal optimum dengan waktu pencelupan 30 menit pada suhu 60°C.
Variasi kadar parutan ban bekas (%) Grafik VFB Variasi Perendaman 7 Hari
Gambar 4.44 menunjukkan bahwa penambahan abon ban pada campuran yang direndam selama 7 hari menurunkan nilai VFB, hal ini disebabkan karena volume pori beton aspal yang terisi aspal berkurang akibat penambahan abon ban. 45 Diagram hubungan variasi perendaman 7 hari dengan VMA pada kondisi kadar aspal optimal dengan lama perendaman 30 menit dan suhu 60°C.
Variasi kadar parutan ban bekas (%) Grafik VMA Variasi Perendaman 7 Hari
Analisis Hasil Pengujian Dengan Penambahan Parutan Ban Bekas Terhadap Agregat Halus Pada Campuran Beton Aspal
Nilai densitas campuran aspal beton AC-WC dengan lapisan keausan pada perendaman 0 hari dapat dilihat pada gambar. Hasil pengujian kestabilan dengan berbagai versi grid ban pada kadar aspal optimal ditunjukkan pada Gambar 4.47.
Variasi kadar parutan ban bekas (%) Grafik Kepadatan Variasi Perendaman
14 Hari
Gambar 4.40 diatas menunjukkan bahwa kestabilan campuran dengan variasi parutan pita pada campuran yang direndam selama 14 hari cenderung menurun. Nilai stabilitas pada kandungan plastik 5%, nilai stabilitas yang diperoleh sebesar 863,75 kg pada kandungan 7%, nilai stabilitas yang diperoleh sebesar 681,08 kg, pada kandungan 10% nilai stabilitasnya sebesar 660,57 kg, dan pada kandungan 14% nilai stabilitasnya yang diperoleh adalah 630,77 Kg, hal ini dikarenakan semakin banyak parutan ban yang ditambahkan pada campuran aspal yang digunakan maka daya rekat aspal yang digunakan semakin berkurang.
Variasi kadar parutan ban bekas (%) Grafik Stabiltas Variasi Perendaman
Dari Gambar 4.34 terlihat bahwa penambahan bank pecah pada campuran yang direndam selama 14 hari menyebabkan nilai aliran meningkat dengan penambahan kadar 5%, nilai aliran 7,43 mm pada kadar 7%, nilai aliran 7,50 mm pada Kadar 10% maka nilai aliran yang didapat adalah 9,93 mm dan pada kadar 14% maka nilai yang didapat adalah 10,50%, hal ini dikarenakan semakin banyak ban yang digerinda ke dalam campuran aspal maka aspal yang digunakan semakin sedikit maka akan semakin rendah. adhesi aspal.
Variasi kadar parutan ban bekas (%) Grafik Flow Variasi Perendaman 14 Hari
72 d. Marshall Questient
Gambar 4.36 menunjukkan bahwa penambahan variasi ban sobek pada campuran perendaman 14 hari menyebabkan peningkatan nilai VIM. Hal ini dikarenakan kadar aspal pada campuran meningkat akibat penambahan ban sobek dari kadar aspal tersebut.
Variasi kadar parutan ban bekas (%) Grafik VIM Variasi Perendaman 14 Hari
51 Plot hubungan variasi pembasahan 14 hari dengan VFB pada kondisi kadar aspal optimum dengan lama perendaman 30 menit pada suhu 60°C. Gambar 4.44 menunjukkan bahwa penambahan abon karet pada campuran yang direndam selama 14 hari menurunkan nilai VFB.
Variasi kadar parutan ban bekas (%) Grafik VFB Variasi Perendaman 14
VMA adalah persentase rongga antar butiran agregat, termasuk rongga berisi udara dan rongga berisi aspal efektif. Nilai VMA yang terlalu kecil dapat menyebabkan lapisan aspal yang dapat menutupi agregat menjadi tipis dan mudah teroksidasi, namun jika kadar aspal terlalu besar akan menyebabkan terjadinya pendarahan.
Variasi kadar parutan ban bekas (%) Grafik VMA Variasi Perendaman 14 Hari
Analisis Hasil Pengujian Dengan Penambahan Parutan Ban Bekas Terhadap Agregat Halus Pada Campuran Beton Aspal
Nilai densitas campuran beton aspal lapis aus AC-WC dengan perendaman 0 hari dapat dilihat pada Gambar 4.46 untuk campuran beton aspal lapis aus AC-WC pada kondisi kadar aspal optimal. Dari Gambar 4.46 terlihat variasi kandungan abon ban pada campuran yang direndam selama 21 hari mengalami penurunan pada kadar 5% yaitu 2,19 pada kadar 7% yaitu 2,06 pada kadar 10%.
Variasi kadar parutan ban bekas (%) Grafik Kepadatan Variasi
Hari
- 79 b. Stabilitas Minimum 800 (Kg)
Gambar 4.40 diatas menunjukkan bahwa kestabilan campuran menggunakan variasi ban sangrai pada campuran yang direndam selama 21 hari cenderung mengalami penurunan.
21 Hari
Gambar 4.48 menunjukkan bahwa penambahan karet parut pada campuran yang direndam selama 21 hari menghasilkan peningkatan nilai aliran pada penambahan kadar 5%, nilai aliran 8,33 mm pada kadar 7%, nilai aliran 8,60 mm pada kadar 10% konten. kadar, nilai aliran yang diperoleh adalah 8,73 mm dan pada kadar 14% maka nilai berikutnya yang diperoleh adalah 10,60%, hal ini disebabkan karena semakin tingginya kandungan bahan abon pada ban.
Variasi kadar parutan ban bekas (%) Grafik Flow Variasi Perendaman 21 Hari
Dari gambar diatas terlihat bahwa variasi penambahan level band grating mengakibatkan variasi nilai Marshall quotient. Gambar 4.50 menunjukkan bahwa penambahan variasi suwir ban pada campuran rendaman selama 14 hari menyebabkan peningkatan nilai VIM.

Variasi kadar parutan ban bekas (%) Grafik VIM Variasi Perendaman 21 Hari
Gambar 4.51 menunjukkan bahwa penambahan parutan tape pada campuran yang direndam selama 21 hari akan menurunkan nilai VFB. Gambar 4-52 dengan jelas menunjukkan bahwa nilai VMA cenderung bervariasi dengan meningkatnya kandungan pita parut pada campuran.

Variasi kadar parutan ban bekas (%) Grafik VMA Variasi Perendaman 21 Hari
Hubungan KAO Dengan Persentase Nilai IKS
Jumlah tumbukan pada kondisi standar adalah 75 tumbukan per sisi. Kemudian dilakukan uji perendaman benda pada kondisi KAO selama 30 menit. Nilai sisa Marshall diperoleh dari kestabilan perendaman 24 jam dibagi kestabilan perendaman 30 menit kemudian dikalikan 100%.
1 BAB V
- Kesimpulan
25.2 Saran