The effect of the presence of Ce on the support and its influence on catalyst deactivation was also investigated. Solid-state IR spectra of Rh-deposited CZOm (left) and ZOm (right) after treatment under N2 at 500◦C. At 500◦C, increasing the S/C ratio had a positive effect on methane (X CH4) conversion, as shown in Figure 5.
This may be related to a better distribution of the Rh group on the oxide support. In the case of the CZOm samples, they were counted in the initial conversion since those catalysts showed deactivation.

Materials and Methods
SAED and energy dispersive X-ray spectrometry (EDS) analyzes performed on a Rh-containing region of the spent non-reduced CZOm supported catalyst after reaction at low temperature. In the case of the ZrO2 support, the microemulsion was heated to 70◦C for 30 min at the end of the synthesis in order to destroy the micelles. The completion of the synthesis was confirmed by the bleaching of the solution and its IR analysis, which showed no peaks related to Rh4(CO)12(νCO at 2075 (vs), 2069 (vs), 2044 (m) and 1885 (s) cm −1 in n-hexane). The solvent was thus removed in vacuo at room temperature.
The CEA-NASA software was used to calculate the outlet composition of the stream at thermodynamic equilibrium. Methane conversion was taken as a reference to evaluate the catalytic activities of the tested samples and was compared with the one calculated at the thermodynamic equilibrium.
Conclusions
Influence of the preparation method in the metal-support interaction and reducibility of Ni-Mg-Al based catalysts for methane steam reforming. Int. Low-temperature steam reforming of methane using metal oxide promoted Ni-Ce0.8Zr0.2O2 catalysts in a compact reformer.Int. Effect of H2S and thiophene on the steam reforming activity of nickel and rhodium catalysts in a simulated coke oven gas stream.Appl.
Effect of steam and hydrogen treatment on the catalytic activity of pure Ni honeycomb for methane steam reforming. Chem. Steam reforming of methane over noble metal catalysts on Ce–ZrO2 at low temperature. Fuel procedure.
Methane and Ethane Steam Reforming over
O 4 -Supported Rh and Ir Catalysts: Catalytic Implications for Natural Gas Reforming Application
- Introduction
- Results and Discussion
We evaluated steam reforming of benzene, as a model tar, over MgAl2O4 supported Rh and Ir catalysts. The aim of this study is to assess the catalytic performance of Rh-, Ir- and Ni-supported catalysts for steam reforming of natural gas. Thus, in this study, the effectiveness of all three metals for performing steam reforming with natural gas was evaluated.
The performance of MgAl2O4 supported Rh, Ir and Ni catalysts was investigated for steam reforming of natural gas under industrially relevant conditions. These MgAl2O4 supported metal catalysts have been characterized in our previous publications and used as catalysts for steam reforming of methane [20], gasifier-derived hydrocarbons, including benzene [19], and complex mixtures, including tar [21], and biomass-derived ethylene. glycol [37] and aqueous products produced via fast pyrolysis [38].

E(WKDQH
STEM characterization shows that high dispersion that can be achieved with Rh and Ir catalysts is supported on MgAl2O4 compared to Ni. We found that while full surface coverage with a stoichiometry 1:1 H-Rhsurf can be achieved at reforming temperatures in the 600–800◦C range for the Rh catalyst, this coverage is significantly lower for Ir (0.7:1 H- Irsurf) and even lower for Ni (0.2:1 H-Nisurf). Steam reforming using a simulating gas mixture representative of natural gas (94.5% methane, 4% ethane, 1% propane, 0.5% butane) was performed over MgAl2O4-supported 5% Ir and 5% Rh catalysts.
Methane and ethane conversion are plotted separately and shown in Figure 3 (propane conversion in Figure S3). Despite similar methane conversion, the conversion of ethane (Figure 3b) and propane (Figure S3) is significantly lower for the Ir catalyst in the lower temperature range (<750◦C). These differences in activity are important for two main reasons: (1) gas feeds with higher concentration of C2+ hydrocarbons lower the overall performance of Ir-based catalysts (more hydrocarbons remain unreacted) and (2) inhibited hydrocarbon hydrogenolysis/reforming activity is an indication that the underlying mechanism is different for Ir compared to Rh despite similar methane reforming activity.
We note that the methane conversions presented in Figure 3a are below the equilibrium conversions (with the equilibrium conversions indicated by the dashed line). We also note that the equilibrium ethane conversion shown in Figure 3b is close to complete for the entire range of conditions investigated.
D0HWKDQH
We note that the H2/CO ratio is an important metric for reforming catalysts when the steam reforming reaction is integrated into downstream processes. Based on the results described above, the Ir catalyst shows lower activity than Rh towards the steam reforming of higher hydrocarbons. Figure 4 shows the normalized metal surface area catalytic rate (molesCH4/molmetal*s) for methane and ethane steam reforming for Rh, Ir, and Ni supported catalysts as a function of temperature.
These results show that for the Ir catalyst, the ethane steam reforming rates (Figure 4b) are significantly lower compared to the methane steam reforming rates (Figure 4a). Results shown in Figure 4 indicate that over Ir catalyst at 600◦C the surface normalized ethane reforming rates (0.6 s−1) are much slower compared to methane reforming rates (3 s−1) . Shown in Table 2 are the results of ethane steam reforming using the Rh- and Ir-supported catalysts.
In Section 3.1, we reported marked differences in H2 adsorption and coverage for the Rh catalyst vs. Although the H2 adsorption experiment does not allow comparison for H/C adsorption, they show improved H retention for the Rh catalyst. The marked difference in conversion for the Ir and Rh catalysts shown in Table 2 makes it difficult to fairly compare product selectivity.
Conversion for the Ir catalyst was increased by increasing contact time (from 28 to 166 ms) to compare product selectivity at similar conversion levels. As a consequence, a lower ethane partial pressure (from 14 to 8 mol%) causes a lower coverage that increases the number of active sites (ethane conversion increases from 10 to 47%). 4) Ethane reformed over Ir supported on Al2O3 shows similar trends. Ir supported by Al2O3 is active for methane reforming; however, ethane steam reforming is severely inhibited.
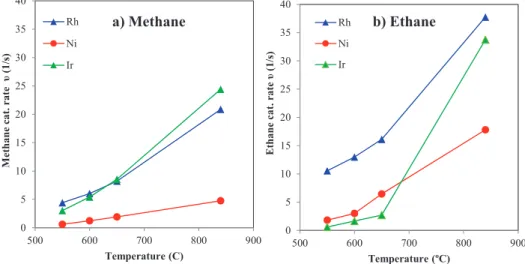
D(WKDQH
DWHU
- Experimental Methods
Thus, the partial pressure of hydrocarbons is less dependent on the reaction rate in the steam reforming of ethane than in the steam reforming of methane. Studies of steam reforming of ethane at 600 °C on Rh by Graf et al [59] showed that in the presence of H2 ethane reacts to methane at a much higher rate than in the direction of formation of reforming products; moreover, their analysis of the reaction products shows that ethane reforming and hydrogenolysis occur in parallel. In previous sections, we have shown that C2+ steam reforming activity is limited for Ir-based catalysts, probably due to a reduced capacity to break the ethane C–C bond, which becomes rate-limiting at low reaction temperatures.
Catalyst durability experiments for methane steam reforming over the Rh catalyst are shown in Figure 7a. Comparative study of benzene vapor reforming over spinel supported Rh and Ir catalysts.ACS Catal. Steam reforming of hydrocarbons from biomass-derived syngas over MgAl2O4-supported transition metal and bimetallic IrNi catalysts.Appl.
Investigation of steam reforming of CH4 and C2 hydrocarbons and carbon deposition on Ni-YSZ cermets.J. Reaction Mechanism of Naphtha Steam Reforming on Nickel-Based Catalysts and FTIR Spectroscopy with CO Adsorption to Elucidate Real Active Sites.Int. Comparative study of steam reforming of methane, ethane and ethylene on Pt, Rh and Pd supported on yttrium-stabilized zirconia.Appl.
Steam reforming of methane, ethane, propane, butane and natural gas over a rhodium-based catalyst.Catal. Steam reforming of fast pyrolysis-derived aqueous phase oxygenates over Co, Ni and Rh metals supported on MgAl2O4. Effect of support on catalytic properties of Rh catalysts for steam reforming of 2-propanol. Int.

Catalytic Dry Reforming and Cracking of Ethylene for Carbon Nanofilaments and Hydrogen Production
Experimental 1. Materials
The catalyst was placed at the end of the tube between two pieces of quartz wool and placed in the oven. The information derived from the results of these techniques allows the understanding and interpretation of the phenomena occurring during activation, DR and CC reactions. Fifteen milligrams of the studied catalyst was placed on quartz wool and deposited in the tube reactor.
FC2H4, i and FC2H4 respectively denote the molar flow rates of C2H4 at the inlet and outlet of the reactor, FH2 the molar flow rates of H2 at the outlet of the reactor. The elemental analyzes of UGSO have shown that the variations were typically less than 5%, and the subsequent tests showed that the observed conversion and yield deviations were lower than the total experimental error and therefore not statistically significant. The literature has already provided the first insight into the factors that influence the formation of CNF and the mechanism of their formation, but the current work reveals the complexity of the latter.
Although it is widely thought that the diameter of the CNF depends on the catalyst particle size, a more careful review of the literature together with the results of this work proves that other factors are also important. The results show that Fe is the main precursor to CNF growth while Ni is contributing more to C–C bond cleavage. In terms of conversion efficiency and yield, the performance of the tested catalytic formulations proved to be at least equal to other Ni-based catalyst performances described in the literature.
He defined the content of the manuscript, read, proofread and corrected all intermediate steps until final acceptance. Special thanks are due to Jasmin Blanchard for his scientific and technical contribution to this manuscript, and to all the instrumental specialists at the CCM of the Universitéde Sherbrooke for the TPR, SEM and XRD analyses. Methane Decomposition over Iron Catalysts in the Moderate Temperature Range: Influence of Catalytic Systems Structure and Reaction Conditions on Carbon Yield and Carbon Filament Morphology.J.
![Figure 31. Reaction set-up [30].](https://thumb-ap.123doks.com/thumbv2/1libvncom/9201875.0/65.723.210.516.115.382/figure-reaction-set-up.webp)