We would like to express our sincere thanks to our head of department, all professors and all colleagues of the Textile Engineering Department of DIU. This sector maintains the lion's share of the GDP, it is gradually improving day by day, so that now Bangladesh is one of the best countries for exporting readymade garments. The quality of the garment is very important and the quality depends on the finishing process.
As we have collected some important data of various 7 to 10 day processes, we have identified 4 main garment quality problems. The report contains the causes and solutions of the problem we have.
1
Introduction
Finishing processes make goods attractive and improve their functional properties, visual appearance and grip. Our thesis is based on finishing processes and started as "Study on Finishing Process for RMG". From the very beginning of our studies, we were very interested in this part of the garment industry, so when we got the opportunity to work on the garment industry, we heartily chose the topic.
We got the opportunity to work in Mondol Fabrics LTD & Impress- Newtex Composite Textiles LTD both industries. In this report we try to show the frequent mistakes and the remedies that will improve the quality of the garments.
Objectives
The readymade garment industry is one of the most potential and income generating sectors of Bangladesh. The 'Made in Bangladesh' label has also brought glory to the country, making it a prestigious brand all over the world. In textile production, after getting the fully stitched garments through the sewing department, the garments are passed to the finishing section for threading, stain removal, ironing, metal detecting, folding, labeling, packaging and cartooning to get the final appearance, which is known as a finishing process for garments.
Limitations of the study
During working hours, data collection was not so easy as either they did not follow any data maintenance system or we could not get hold of the system. We collected all the information about each garment and could only check what a particular garment has.
4
Garments Finishing
These are sent in the finishing department for wire cutting, stain removal, ironing, metal detecting, folding, tagging, packing, cartooning to get the final look. So the finishing process is carried out by a series, and the final result of finishing is related to the buyer's requirement and satisfaction.
Process Flowchart
Thread Trimming
- Types of Thread Trimmers
Spot Removing
- Types of Spots
- Spot Removal Treatment
Garments are kept in a chamber and high air circulation is created to remove loose threads from the garment and remain as waste in the waste section. The surgical spirit is another that is of great importance in removing stains from.
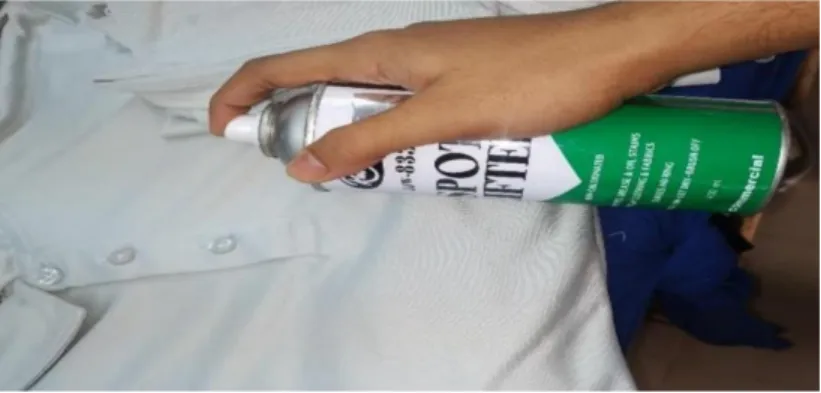
Ironing
- Ironing Equipment
- Recommended Ironing Temperature for Different Fabrics
- Ironing Tips
The significant factor in choosing the right ironing station is the airflow through the garment to cool and set it. The durability of the ironing board cover is based on several factors such as hydrolysis, pressure and heat resistance of the materials used. Dry cleaners and full service laundry providers usually use a large steam press to do most of the ironing work, a rotary iron can be used as an alternative.
If not, start with a low temperature and test by ironing on a small area, then gradually increase the temperature.
Metal Detector
- Features of Metal Detector Machine
Control panel: This panel is used to set the specifications that will detect the metal according to the manufacturer's requirements. Registration position indicator: The machine registers the location of the broken needle to find out more easily. Return device: There is a return device that sends the products to an operator after making an alarm when the machine detects foreign objects in a product.
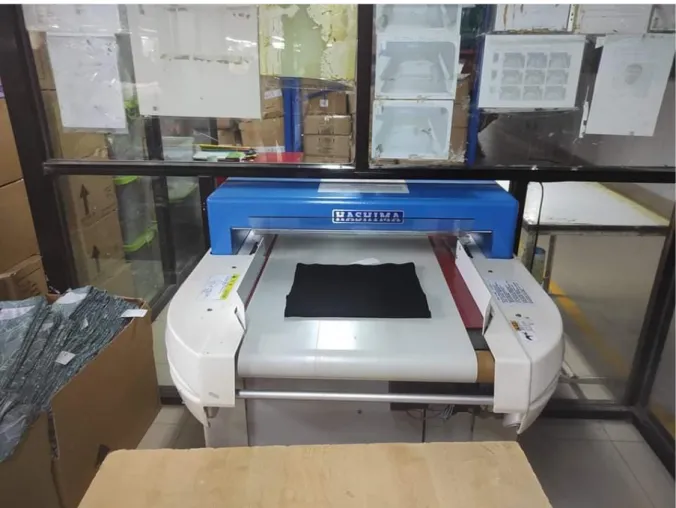
Garment Measurement
- Method of Garment Measurement
- Preparation for Measuring Garments
- Measurement Technique
- Importance of Taking Accurate Measurement
Chest: Place measuring tape 1'' below arm seam, straight across front, outer edge to outer edge. Center Back Sleeve Length: Fold the neck in half to find the center, now measure from the center of the neck to the shoulder point, twist and follow the top sleeve line to the bottom edge of the sleeve, including the cuff. Waist: Lay the garment flat and measure along the top edge of the waist from outer edge to outer edge.
Leg opening: Place a measuring tape on the left leg, straight across the bottom, from edge to edge. Garments are sewn to size and are checked again in the finishing section, although that is measured before sewing. It is a must process to check the size.
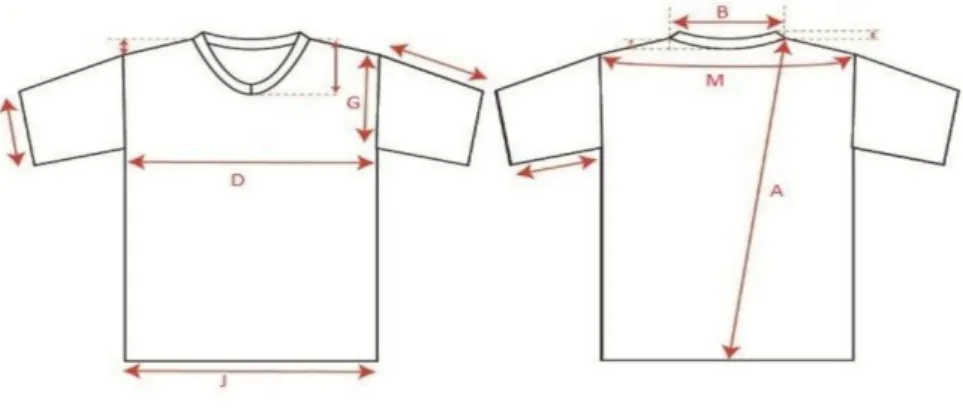
Folding
- Folding Process of Some Basic Garments
- Automatic Folding Machine
Fold the pants in half, inseam to outside seam, keeping the ends of the waistband to the inside of the pants. Fold the leg into thirds - fold the bottom edge over the knee and fold up to the waist edge.
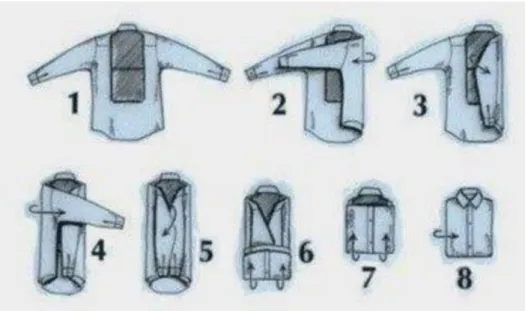
Garments Packing & Cartoning
- Types of Packaging
- Classification of packaging
- Types of Garments packaging Carton
It can be adjusted very easily for different sizes and types of clothes in order to achieve the best desired fold. This differentiates the sizes and colors and in this way the clothes are kept in the carton.
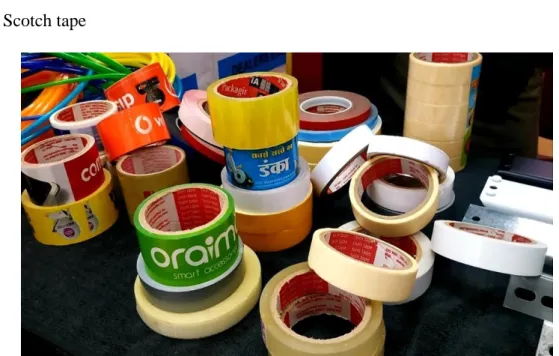
Final Inspection
- Final Inspection Activities
- Acceptable Quality Level
- AQL Chart
The term AQL, comprehensively acceptable quality level refers to the maximum range that can be accepted during the random sampling and inspection. Since most of the acceptance decisions of the garment shipments for the export market depend on AQL-based sampling plan. In any industrial sector, before accepting the finished goods from the manufacturer buyer does inspection of goods.
Foreign buyers are so concerned about the quality of the product and so they offer the manufacturer AQL for the product at the beginning when the order is placed. If passing the AQL means that the goods are at an acceptable level of quality, the inspection team issues the certificate to ship, and if it fails to pass the AQL, then it can be checked or returned.
Experimental Data
Finishing Sequence
Thread Cutting
- Faults & remedies
- Daily Sewing Thread Cutting Report
From the thread cutting section, we have collected some data and analyzed it to find out the accuracy of the sewing section and how many errors are found in 3 hours in the thread cutting section. The table below shows the daily sewing thread cutting ratio of 3 hours by a single operator.
Spot Removing Section
- Causes & Remedies of Spots
Ironing
- Problems & Faults
- Remedies
- Daily Ironing Section Report
Ironing must be performed accurately on the entire garment otherwise the temperature may cause shade variation. If the garment is thin and may have the chance to change shape, the temperature should be kept lower. From the ironing department we collected some data and analyzed it to find out the accuracy of the product and how many errors are found per hour in the ironing department.
Here 1871 pieces of clothing were processed and only 1 did not go to further process in 10 days inspection. So, 1870 pieces of clothes were submitted here where the percentage of clothes submission was impressive as it stands at 99.95%.
Quality Checking Process
- Faults found
- Daily checking Report
- Summary of Quality Checking in Finishing Section
Sometimes at the time of printing the product can be spot printed by the process also some spots can be distinguished by the chemicals used for printing, these are called spot printing. Sometimes this folding is done on the wrong side of the clothes, it is known as wrong side folding. This can be found in any part, ie the absence of a seam in the upper part of the neck is considered a missing seam.
If the raw parts of the fabric are unexpectedly visible on the sewn portion of the garments, the problem is referred to as a raw edge problem. The puckering of a seam due to a sewing error, which causes the garments to become unacceptably seamed, is known as seam puckering. After the sewing process, if garments are delivered with a broken stitch in the quality section, it is called defective stitch defect.
If the seam line is open or the fabric seam is open or loose, the fault is called an open seam. There are still some faults that can be found, such as care label missing, stitch drop, scissor hole, tuck missing, etc. Date Checked Qty Ok Qty Skip/Drop Broken Stitch Raw Edge Open Seam/ Open Trim Spot/Size Label Accessories Stripe Up- Down Stitch Closure/Thread Total.
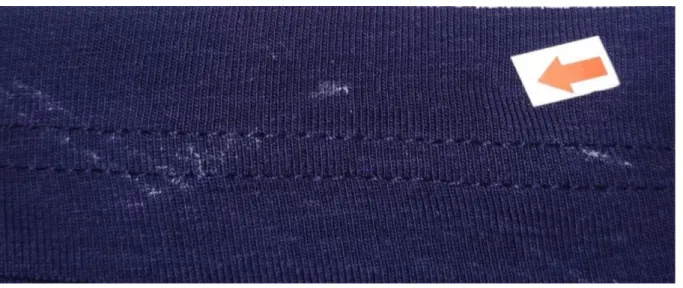
Hang Tag
Folding & Packing
- Folding process
- Daily Folding & Packing Report
Generally, wrapping is done in two terms: one is poly and the other is cartooning. The first garments are placed in a poly bag and then the whole packaged products are kept in the box. Garments should be placed so that the back is on top.
The following table indicates the daily folding and polypacking report of 3 hours by a single operator. Here 2586 pieces of clothing are ready to be folded & packed, where 2581 pieces have passed & 5 of them are defective.
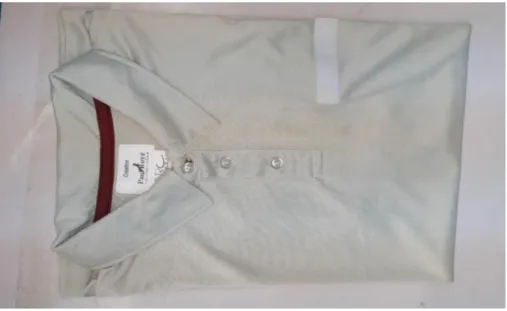
Discussion of Results
Sewing Thread Cutting Data Analysis
- Graph of Sewing Thread Cutting Report
Data Analysis of Ironing
- Ironing Production for 10 Days
Folding & Packaging
- Graph of Folding & Packaging Production
This is the last process before shipping and so here is the graph showing the final amount of packaging in 3 hours per day.
Data Analysis of Quality Inspection
- Graph of Total Finishing Faults
- Pie Chart of Quality Inspection Report
- Four (4) Major Defects
4359 pieces of garments were checked, 298 were faulty which is shown in the chart and the rest passed the quality control process. The following graph shows the percentage of defects found during the inspection of the quality of garments. Sometimes this tuck is done on the wrong side or the tuck missing from garments is known as open tuck.
Skipped or dropped stitches occur during the sewing process and are usually caused by either a faulty sewing machine or a worker error. Spots: Sometimes at the time of printing, the product may be printed with spots by the process. Also some stains can be detected by the chemicals used for printing, these are called print stains.
So here we can see the four main defects found during the quality control in the finishing section. Many different types of errors were found during the session, but these 4 problems were found regularly and in large numbers. All necessary attention was paid to the fact that we can get to know all the processes and discuss them.
Errors and there causes including remedies are also discussed for all the processes in the finishing section.
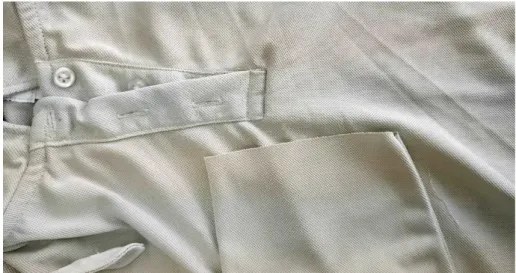
Conclusion