digital_2016-4_20416070-D2054-Moh Azhar
Teks penuh
(2) ii. UNIVERSITAS INDONESIA. REKAYASA MATERIAL ABU SEKAM PADI DAN BATU APUNG PADA BETON RINGAN UNTUK MENINGKATKAN KEKUATAN MEKANIK SEMEN PORTLAND KOMPOSIT. DISERTASI Diajukan sebagai salah satu syarat untuk memperoleh gelar Doktor. MOH AZHAR NPM : 1006751306. FAKULTAS MATEMATIKA DAN ILMU PENGETAHUAN ALAM PROGRAM STUDI ILMU MATERIAL JAKARTA 2015. Universitas Indonesia Rekayasa material..., Moh Azhar, FMIPA UI, 2015..
(3) Rekayasa material..., Moh Azhar, FMIPA UI, 2015..
(4) Depok 17 Juni 2015. Rekayasa material..., Moh Azhar, FMIPA UI, 2015..
(5) v. KATA PENGANTAR. Puji dan syukur penulis panjatkan kehadirat Allah S.W.T., atas segala rahmat dan karunia-Nya sehingga penulis dapat menyelesaikan disertasi ini. Disertasi ini disusun sebagai salah satu syarat untuk memperoleh gelar Doktor pada program Pascasarjana, program studi Ilmu Material, Fakultas Matematika dan Ilmu Pengetahuan Alam Universitas Indonesia. Penulis menyadari bahwa, tanpa bantuan dan bimbingan dari berbagai pihak, sangatlah sulit bagi penulis untuk menyelesaikan disertasi ini. Olek karena itu, penulis mengucapkan terima kasih kepada yang terhormat : 1.. Bapak Dr. Azwar Manaf, M.Met selaku promotor dalam penulisan disertasi, arahan teknis penelitian, dorongan moral dan semangatnya untuk terus berkembang.. 2.. Bapak Dr. Bambang Soegijono, M.Si selaku kopromotor 1 atas segala arahan teknis penelitian serta dorongan semangatnya yang tidak pernah berhenti selama proses penelitian.. 3.. Ibu Dr. Vera Indrawati Judarta, M.Si selaku kopromotor 2 atas segala arahan teknis dan bantuan penggunaan fasilitas laboratorium di Indocement Tunggal Prakarsa.. 4. Ibu Dr. Vivi Fauzia, M.Si selaku Ketua Program Studi Pascasarjana Ilmu Material, Departemen Fisika, Fakultas Matematika dan Ilmu Pengetahuan Alam. 5.. Bapak Saiful Bahri, ST. M.Si, Ibu Laily, ST dan Bapak H. Agus yang telah membantu dalam memfasilitasi penggunaan laboratorium Indocement Tunggal Prakarsa.. 6.. Keluargaku : Ayahanda H Husain Mukdiem (alm), Ibunda Hj Misbah (almh), H Muhammad Hilman (alm), dan Hj Sutra Malkini (almh), Istri tercinta Malda serta anak-anakku tercinta Munadhilah Ummahat, S.Hum, Nuha Mufidah, Fauzan Muhtadi, dan Faruq Mahdi, kakanda Hidayat Alamsyah dan Johansyah atas segala pengertian, perhatian, kasih sayang dan do’anya kepada penulis selama menjalani studi di Universitas Indonesia.. Universitas Indonesia Rekayasa material..., Moh Azhar, FMIPA UI, 2015..
(6) vi. 7.. Seluruh Pimpinan PT. Indocement Tunggal Prakarsa yang telah banyak memberikan kemudahan untuk menggunakan semua fasilitas laboratorium yang diperlukan.. 8.. Seluruh civitas akademika pascasarjana Ilmu Material, Fakultas Matematika dan Ilmu Pengetahuan Alam Uneversitas Indonesia, terutama teman seperjuangan Dr. Rahmat Doni, Dr. Novizal, Dr. Iwan. Semoga disertasi ini bisa bermanfaat bagi penulis sendiri dan bagi orang lain. yang membacanya walaupun masih jauh dari kesempurnaan.. Depok, Juni 2015. Penulis. Universitas Indonesia Rekayasa material..., Moh Azhar, FMIPA UI, 2015..
(7) Rekayasa material..., Moh Azhar, FMIPA UI, 2015..
(8) viii. ABSTRAK : Moh Azhar Nama Program Studi : Ilmu Material : Rekayasa Material Abu Sekam Padi dan Batu Apung pada Beton Judul Ringan untuk Meningkatkan Kekuatan Mekanik Semen Portland Komposit Telah dilakukan penelitian pembuatan beton ringan atau lightweight concrete (LWC) menggunakan batu apug (BA) dan abu sekam padi (ASP). Sampel beton ringan yang dibuat mengandung BA dengan fraksi berbeda, adapun material semen, pasir, dan abu sekam padi volumenya dijaga tetap. Terdapat dua parameter utama yang menentukan sifat mekanik sampel LWC masing-masing adalah densitas sampel dan rasio air/semen (w/c). Sifat mekanik yang paling utama dari LWC adalah kekuatan tekan. Pada campuran dengan fraksi volume batu apung terbesar (100%) menghasilkan densitas dan kekuatan tekan paling rendah masing-masing sebesar (1389,6 kg/m3 dan 11,1 MPa). Diketahui bahwa makin rendah fraksi batu apung dalam sampel beton makin tinggi nilai densitas dan kekuatan tekannya, disebabkan oleh tingginya nilai fraksi pori baik pori terbuka maupun pori tertutup dalam sampel beton. Observasi terhadap fotomikro SEM batu apung menunjukkan bahwa terdapat sejumlah besar pori dengan bentuk memanjang ke bagian dalam dari permukaan sampel beton. Pori hadir dengan kerapatan jumlah pori relatif besar serta dengan ukuran yang bervariasi. Fakta ini menjelaskan mengapa batu apung besifat ringan karena memiliki densitas massa yang rendah. Pola difraksi sinar X sampel beton ringan memperlihatkan dominasi fasa kristalin diidentifikasi sebagai fasa quartz (SiO2). Namun dapat dipastikan sampel beton ringan terdiri dari fasa campuran antara fasa kristalin dan dengan sedikit fasa amorph. Fotomikro SEM beton ringan menunjukkan bahwa senyawa Kalsium Silikat Hidrat (CSH) mulai tumbuh pada waktu awal proses hidrasi dan terus berkembang sampai umur beton mencapai umur hidrasi 28 hari yang ditandai dengan sifat fisik yang padat dan peningkatan kekuatan beton. Dapat dipastikan bahwa senyawa CSH ini memiliki peranan penting terhadap pengaturan sifat mekanik seperti kekuatan tekan. Penelitian ini menyimpulkan bahwa batu apung dan abu sekam padi adalah material berbasis silika amorph yang memiliki densitas lebih rendah terutama dibandingkan dengan material pembentuk beton lainnya. Baik densitas dan kekuatan tekan sampel beton ringan ditentukan oleh rasio antara batu apung dan abu sekam padi. Ditemukan rasio terkecil BA/ASP yaitu 8 menghasilkan nilai densitas dan kekuatan tekan optimal, masing-masing pada usia beton 28 hari sebesar 1891 kg/m3 dan 23 MPa. Komposisi beton ringan yang terbaik diperoleh dari hasil penelitian ini adalah komposisi campuran PCC (1,00) : Pasir (1,00) : ASP (0,05) : BA (0,50) dengan nilai Slump 8 cm ditandai oleh nilai rasio antara kuat tekan dan densitas tertinggi adalah 1285. Kata kunci: Beton Ringan, Abu Sekam Padi (ASP), Batu Apung (BA), Slump, Berat Jenis, dan Kuat Tekan.. Universitas Indonesia Rekayasa material..., Moh Azhar, FMIPA UI, 2015..
(9) ix. ABSTRACT Name : Moh Azhar Study Program : Materials Science Title : Lightweight Concrete Containing Rice Husk Ash and Pumice Materials to Improve the Mechanical Strength of Portland Cement Composites Research studies on the manufacture of lightweight concrete (LWC) using pumice and rice husk ash (RHA) materials have been done. LWC samples were made of pumice materials with a different mass fraction, while the cement, sand, and rice husk ash materials were keep fixed. It was found that there are two main parameters that determine the mechanical properties of LWC which are density and the water and cement ratio (w/c ratio). The main mechanical properties of LWC sample is the power press. Samples with the largest volume fraction of pumice (100%) resulted in lightest density (1389.6 kg/m3) and the smallest strength of LWC (11.1 MPa). It was found that, the lower the mass fraction of pumice in LWC samples, the higher the density values and compressive strength were obtained. This was caused by the high mas fraction value of pores, which were both open and closed pores. Scanning electron micorscopy (SEM) images for the pumice showed that the there are a large number of regular and structured pores extending deep inside the surface of the sample. It was observed that pores present with pore size does not vary significantly but with the density of the relatively large number of pores, indicating pumice has a low mass density. The XRD pattern of the lightweight concrete samples indicated that the samples were dominated by crystalline phases in which the quartz (SiO2) is the main phase and a small fraction of amorphous phase was also obtained. SEM images of lightweight concrete samples showed that the structure of Calcium Silicate Hydrates (CSH) started growing at the beginning of hydration time and continue to evolve into a more solid structure until the age of 28 days, where the compound has an important role to the mechanical properties such as compressive strength. The study concluded that the pumice and rice husk ash is are amorphous silica-based material which has a lower density compared to other concrete forming material such as cement and sands. Both density and light weight concrete compressive strength are determined by the ratio between pumice and rice husk ash, in which the smallest ratio 8 resulted in the largest density and compressive strength, which are 1890.5 kg/m3 and 23.2 MPa respectively at the age of 28 days. The study concluded that the best composition for lightweight concrete samples was the following: PCC (1,00): Sand (1,00): ASP (0,05): BA (0,50) with a slump value of 8 cm resulted in the largest value of a ratio between compressive strength and density of 1285. Keywords: Lightweight Concrete (LWC), Rice Husk Ash (RHA), Pumice, Slump, Density, and Compressive Strength. Universitas Indonesia Rekayasa material..., Moh Azhar, FMIPA UI, 2015..
(10) x. DAFTAR ISI. JUDUL. ii. PERNYATAAN ORISINALITAS. iii. PENGESAHAN. iv. KATA PENGANTAR. v. PERNYATAAN PUBLIKASI. vii. ABSTRAK. viii. DAFTAR ISI. x. DAFTAR TABEL. xii. DAFTAR GAMBAR. xiii. BAB I. BAB II. PENDAHULUAN. 1. 1.1 Latar Belakang. 1. 1.2 Tujuan Penelitian. 3. 1.3 Manfaat Penelitian. 4. 1.4 Batasan Masalah. 4. 1.5 Model Operasional Penelitian. 4. TINJAUAN PUSTAKA. 5. 2.1 Beton Agregat Ringan (LWC). 7. 2.2 Portland Cement (PC). 16. 2.2.1 Reaksi Hidrasi. 17. 2.2.2 Hidrasi C3S dan C2S. 20. 2.2.3 Hidrasi C3A. 21. 2.2.4 Hidrasi C4AF. 21. 2.2.5 Kinetika Hidrasi Semen. 22. 2.3 Abu Sekam Padi (ASP). 24. 2.4 Batu Apung (BA). 30. Universitas Indonesia Rekayasa material..., Moh Azhar, FMIPA UI, 2015..
(11) xi. BAB III. BAB IV. BAB V. METODE PENELITIAN. 38. 3.1 Bagan Penelitian. 38. 3.2 Alat, Bahan Penelitian dan Bentuk Spesimen. 40. 3.2.1 Alat Penelitian. 40. 3.2.2 Bahan Penelitian. 41. 3.2.3 Bentuk Spesimen. 41. 3.3 Rencana Adukan Beton. 42. 3.3.1 Rencana Adukan Beton Tahap 1. 42. 3.3.2 Rencana Adukan Beton Tahap 2. 42. 3.4. Prosedur Penelitian. 43. 3.4.1 Pemeriksaan Air. 44. 3.4.2 Pemeriksaan Agregat. 44. 3.4.3 Persiapan Pembuatan Adukan Beton. 48. 3.4.4 Pengujian Workability. 48. 3.4.5 Pengujian Kuat Tekan dan Densitas Beton. 49. 3.4.6 Pengujian dengan SEM, EDAX, XRF, dan XRD. 50. HASIL DAN PEMBAHASAN. 51. 4.1 Pendahuluan. 51. 4.2 Karakteristik Fisik Agregat. 52. 4.3 Karakteristik Abu Sekam Padi. 53. 4.4 Karakteristik Batu Apung. 58. 4.5 Kuat Tekan Beton Ringan. 65. KESIMPULAN DAN SARAN. 78. 5.1 Kesimpulan. 78. 5.2 Saran. 78. DAFTAR REFERENSI. 79. LAMPIRAN. 83. Universitas Indonesia Rekayasa material..., Moh Azhar, FMIPA UI, 2015..
(12) xii. DAFTAR TABEL Variasi sampel terhadap density (Ke dkk, 2009). 8. Tabel 2.2 Porositas pada variasi sampel yang digunakan (Ke dkk, 2009). 9. Tabel 2.1. Tabel 2.3. Kekuatan Tekan (MPa) pada beberapa tipe agregat ringan terhadap beberapa variasi rasio air dan semen (Chi dkk, 2003). 10. Tabel 2.4. Sifat dari agregat yang digunakan (Chi dkk, 2003). 11. Tabel 2.5. Reaksi hidrasi senyawa semen. 17. Tabel 2.6. Proporsi campuran dan Properties dari RHA pada Beton (Mehta, P. K.,1992). 26. Tabel 2.7 Sifat kimia dan fisik material yang digunakan pada LWC (Hanifi Binici, 2007). 31. Tabel 2.8 Sifat fisik dari batu kali sebagai agregat (Hanifi Binici, 2007). 32. Tabel 2.9 Sifat fisik dari crushed ceramic (CC) dan crused basaltic pumice (CBP) (Hanifi Binici, 2007). 32. Tabel 2.10 Hasil uji XRF dari berbagai tipe campuran batu apung dan Semen (Uma Ramasamy dan Paul Tikalsky, 2012). 34. Tabel 3.1. Proporsi campuran PCC, pasir, BA, ASP, dan air. 42. Tabel 3.2. Proporsi campuran PCC, pasir, BA, ASP, Slump, dan w/c. 43. Tabel 4.1 Nilai densitas agregat dihitung berdasarkan SK.SNI. 52. Tabel 4.2. Hasil uji mineralogi Abu Sekam Padi. 55. Tabel 4.3. Komposisi senyawa kimia Abu Sekam Padi dengan XRF. 56. Tabel 4.4. Hasil EDAX abu sekam padi diambil dari 3 posisi. 58. Tabel 4.5. Hasil uji mineralogi Batu Apung. 61. Tabel 4.6 Komposisi senyawa kimia Batu Apung dengan XRF. 62. Tabel 4.7. Hasil EDAX batu apung pada 3 posisi. 65. Tabel 4.8. Densitas dan kuat tekan beton umur 3-28 hari kubus 1-7. 66. Tabel 4.9 Rasio antara Kuat Tekan terhadap Densitas sampel 1-7 umur 28 hari Tabel 4.10 Densitas, Slump dan Kuat Tekan Beton umur 3-28 hari kubus 8-11 Tabel 4.11 Rasio antara Kuat Tekan terhadap Density sampel 8-11. 71 73. Tabel 4.12 Hasil uji mineralogi Beton Ringan umur 3-28 hari. 76. 70. Universitas Indonesia Rekayasa material..., Moh Azhar, FMIPA UI, 2015..
(13) xiii. DAFTAR GAMBAR Gambar 2.1 Grafik korelasi antara kekuatan tekan dan fraksi volume LWA pada beberapa variasi sampel yang digunakan (Ke dkk, 2009). 9. Gambar 2.2 Grafik hubungan antara kekuatan tekan dan densitas sampel yang telah dikeringkan pada beberapa variasi sampel yang digunakan (Ke dkk, 2009). 9. Gambar 2.3 Pengaruh rasio air/binder terhadap kekuatan tekan pada beberapa tipe agregat (Chi dkk, 2003). 11. Gambar 2.4 Pengaruh vraksi volume terhadap kekuatan tekan dan rasio air/binder (Chi dkk, 2003). 11. Gambar 2.5 Hasil Uji Kuat Tekan Beton Silinder Ukuran 4"x8" (Uma Ramasamy dan Paul Tikalsky, 2012). 14. Gambar 2.6 Kuat tekan berbagai jenis LWC pada berbagai usia (Kawkab H. dkk, 2008) Gambar 2.7 Evolusi mikrosktuktur CSH pada komposisi 100 wt% semen Portland selama proses hidrasi sampai 56 minggu (A. Manaf, and V. Indrawati, 2011) Gambar 2.8 Pengaruh proses desorption air terhadap modulus elastisitas pada semen Portland untuk (a) W/C = 0,3 dan (b) 0,4 (Alizadeh, Beaudoin dan Rakim, 2011) Gambar 2.9 Pengaruh variasi komposisi ratio C/S & porositas terhadap modulus elastisitas (Alizadeh, Beaudoin dan Rakim, 2011) Gambar 2.10 Diagram Fasa hidrasi semen (Taylor, 1997). 15. 18. 19 19 20. Gambar 2.11 Mikrograf SEM RHA dibakar pada temperatur berbeda Hwang dan Wu (Hwang, C. L., and Wu, D. S., 1989). Gambar 2.12 Mekanisme mengisi kekosongan dan efek transisi zona Penguatan RHA (Mehta, P. K.,1992) Gambar 2.13 Fotomikro SEM dari sampel RHA (Rosario Madrid, dkk, 2012) Gambar 2.14 Pola XRD dari sampel RHA (radiasi Cu - Kα) (Rosario Madrid, dkk, 2012) Gambar 2.15 Pola XRD SiC dari Sekam Padi (Rosario Madrid, C. A. Nogueira and F. Margarido, 2012) Gambar 2.16 Kekuatan tekan pada campuran beton terhadap waktu pengerasan (Hanifi Binici, 2007) Gambar 2.17 Aliran panas untuk kombinasi campuran yang berbeda selama 75 jam pertama (Uma Ramasamy dkk, 2012). 25 26 27 27 29 33 36. Universitas Indonesia Rekayasa material..., Moh Azhar, FMIPA UI, 2015..
(14) xiv. Gambar 2.18 Aliran panas untuk kombinasi campuran yang berbeda selama 75-225 jam (Uma Ramasamy dkk, 2012). 36. Gambar 2.19 Mikrostruktur dari agregat Uygunoglu, dkk, 2013). 37. Gambar 3.1. batu. apung. (Tayfun. Alur Penelitian. 39. Gambar 3.2 Bentuk specimen uji. 41. Gambar 4.1 Fotomikro SEM Abu Sekam Padi dengan pembesaran 100x (a), 5000x (b), 20000x (c). 54. Gambar 4.2 Hasil XRD Abu Sekam Padi. 55. Gambar 4.3 Hasil EDAX Abu Sekam Padi beupa grafik, tabel komposisi unsur, dan pengambilan foto permukaan. 57. Gambar 4.4 Fotomikro SEM Batu Apung dengan pembesaran 100x (a), 200x (b), 500x (c), 1.000x (d), 2.000x (e), dan 5.000x (f). 59. Gambar 4.5 Hasil XRD Batu Apung. 61. Gambar 4.6 Hasil EDAX Batu Apung brupa grafik, tabel komposisi, dan posisi pengambilan Foto. 65. Gambar 4.7 Grafik Densitas terhadap Rasio BA/ASP (a) dan Grafik Kuat Tekan terhadap Densitas sampel kubus 1-7 pada umur beton 28 hari (b) Gambar 4.8 Diagram batang Kuat tekan beton pada umur 28 hari dari kubus 1 sampai kubus 7. 69. Gambar 4.9 Grafik perbandingan nilai Kuat Tekan terhadap densitas sampel kubus 1 sampai 7 umur 28 hari. 70. Gambar 4.10 Grafik Kuat tekan beton pada umur 3 sampai 28 hari pada proses pengerasan beton kubus 8-11. 72. Gambar 4.11 Grafik nilai slump terhadap Kuat Tekan Umur 28 hari. 72. Gambar 4.12 Perbandingan nilai Kuat Tekan terhadap Densitas pada kubus 8-11 umur beton 28 hari. 73. Gambar 4.13 Foto SEM Beton Ringan Umur 7 hari (A), 14 hari (B), 21 hari (C), dan 28 hari (D) pembesaran 20000 x. 74. Gambar 4.14 Hasil uji XRD pola difraksi Beton Ringan umur 28 hari. 75. 68. Universitas Indonesia Rekayasa material..., Moh Azhar, FMIPA UI, 2015..
(15) 1. BAB I PENDAHULUAN 1.1.. Latar belakang Beton merupakan material komposit yang diperoleh dari suatu proses. pencampuran beberapa material, dan air yang mengeras seiring perkembangan waktu menjadi benda padat. Komposisi beton terdiri dari semen, agregat halus, agregat kasar, air dan rongga udara. Rongga udara mempunyai pengaruh terhadap kuat tekan beton. Makin besar volume rongga udara yang terdapat dalam beton maka kuat tekan beton akan semakin menurun dan sebaliknya makin kecil volume rongga udara yang terdapat dalam beton maka kuat tekan beton makin bertambah. Proses pembuatan beton terbentuk dari semen dan air yang menghasilkan pasta semen yang digunakan untuk mengikat agregat kasar dan agregat halus. Campuran bahan-bahan pembentukan beton ditetapkan sedemikian rupa, sehingga menghasilkan beton segar yang mudah dikerjakan dan memenuhi kekuatan tekan rencana setelah mengeras dan cukup ekonomis. Hingga dekade terakhir ini, beton telah menjadi salah satu bahan pilihan yang paling utama untuk digunakan dalam konstruksi bangunan. Disamping penggunaan beton konvensional yang telah umum digunakan dalam konstruksi bangunan, ada alternatif lain sebagai pengganti beton konvensional, yaitu menggunakan agregat ringan atau lightweight aggregate (LWA), dari segi biaya lebih ekonomis dan dari segi pembebanan lebih ringan, Beton ringan atau lightweight concrete (LWC) juga disebut beton agregat ringan atau lightweight aggregate concrete (LWAC) adalah beton yang memiliki berat jenis (density) lebih ringan daripada beton pada umumnya (beton konvensional). LWC dapat dibuat dengan berbagai cara, antara lain dengan: menggunakan agregat ringan (fly ash, batu apung atau Pumice Stone, expanded polystyrene – EPS, dll), campuran antara semen, silica, pozollan, dll (dikenal dengan nama aerated concrete) atau semen dengan cairan kimia penghasil gelembung udara (dikenal dengan nama foamed concrete atau cellular concrete). Tidak seperti beton biasa, berat LWC dapat diatur sesuai kebutuhan. Pada umumnya berat LWAC berkisar antara 1600 – 2000 kg/m3. Karena itu keunggulan LWC. Universitas Indonesia Rekayasa material..., Moh Azhar, FMIPA UI, 2015..
(16) 2. utamanya ada pada berat, sehingga apabila digunakan pada proyek bangunan tinggi (high rise building) akan dapat secara signifikan mengurangi berat sendiri bangunan, yang selanjutnya berdampak kepada perhitungan pondasi. Keuntungan lain dari LWC antara lain: Memiliki nilai tahanan panas (thermal insulation) yang baik Memiliki tahanan suara (peredaman) yang baik Transportasi mudah Dapat mengurangi kebutuhan bekisting (formwok) dan perancah (scaffolding).. LWC memungkinkan Engineering sipil untuk merencanakan alternatif lain selain penggunaan agregat beton konvensional dan memiliki nilai yang lebih ekonomis dalam sebuah struktur. Pengurangan beban mati pada struktur dapat dilakukan dengan menggunakan bentang (longer spans) atau mengurangi bagian dari elemen struktur itu, dan mengurangi jumlah baja yang diperlukan dan bahkan dimensi pondasi. Dalam pembuatan LWC memungkinkan juga untuk mengurangi biaya penempatan dan transportasi. Selain teknis dan kepentingan ekonomi, LWC dapat diintegrasikan ke dalam proses pembangunan yang berkelanjutan dengan menggunakan agregat buatan, khususnya yang lebih ringan dari agregat alami, hal tersebut dapat melestarikan sumber daya alam. Selain itu, berkontribusi mengurangi volume sampah yang dihancurkan, dan dapat mengoptimalisasi struktur dengan mengurangi beban mati. Dengan demikian, beton baru ini dapat mengurangi permasalahan limbah dengan baik. LWC yang ada memiliki kelemahan yaitu porositas yang besar sehingga kekuatannya lebih kecil dan lebih mudah berdeformasi dibandingkan dengan agregat normal. Komponen terlemah dari LWC bukanlah terletak pada semen sebagai matriksnya atau zona transisi antar muka tetapi terletak pada agregatnya. Jadi unjuk kerja mekanik LWC tidak hanya dikendalikan oleh kualitas semen sebagai matriks tetapi juga volume agregat dalam beton dan sifat agregat (Chi dkk, 2003). Berbagai riset telah dilakukan yang berkenaan dengan studi tentang perilaku LWC, sehingga Zhang dan Gjorv menunjukkan pengaruh kepadatan (density) pada LWC terhadap kekuatan mekanik dan mekanisme kegagalan pada. Universitas Indonesia Rekayasa material..., Moh Azhar, FMIPA UI, 2015..
(17) 3. high-performance LWC (Zhang dan Gjorv, 1991). Yang dan Huang menyoroti pentingnya fraksi volume LWC pada kekuatan tekan dan modulus elastis LWC (Yang dan Huang, 1998). Umumnya, kualitas LWC tidak hanya dilihat dari densitasnya saja tetapi juga dari sifat mekaniknya. Wasserman dan Bentur mengadakan penelitian bahwa kepadatan (densitas) agregat yang sama tidak menghasilkan kekuatan beton yang sama pula (Wasserman dan Bentur, 1997). LWC unjuk kerja secara mekanik tidak hanya dipengaruhi oleh kualitas dari semen sebagai matrik saja, tetapi juga dipengaruhi oleh volume dan sifat dari agregat (Chi dkk, 2003). Banyak penelitian menunjukan bahwa peranan volume dan sifat sangat penting pada LWC terutama densitas partikelnya, dan kekuatannya pada unjuk kerja mekanik pada LWC (Ke dkk, 2009; Zang, 1998; Lydon, 1982; Yang dan Huang, 1998). Secara umum kandungan agregat sekitar 70-80 % dari volume beton. Besarnya volume fraksi beton dan agregat memberikan pengaruh yang sangat besar terhadap modulus elastisitas beton dan berpengaruh juga pada sifat yang lain (Chi dkk, 2003). Penelitian yang telah dilakukan untuk meningkatkan unjuk kerja secara mekanik pada LWC dengan menambahkan material lain diantaranya adalah: fly ash (Chi dkk, 2003), pumice (Failla dkk, 1997; Gunduz, 2005; dan Hanifi Binici, 2007). Oleh sebab itu Peneliti melakukan studi lebih dalam untuk memodifikasi LWC dengan menambahkan abu sekam padi (ASP) atau rice husk ash (RHA), dan batu apung (BA) atau pumice, beserta pengaruh penambahan material-material tersebut tehadap sifat mekaniknya. ASP berasal dari daerah Cianjur dan BA dari daerah Sukabumi Jawa Barat. Dengan adanya penambahan ASP dan BA pada LWC diharapkan dapat meningkatkan nilai ekonomis dan sifat mekaniknya serta dapat meningkatkan nilai tambah ASP dan BA yang selama ini dianggap sebagai limbah. 1.2.. Tujuan Penelitian Mengeksplorasi lebih dalam tentang pengaruh penambahan material ASP. dan BA atau Pumice pada LWC terhadap sifat mekanik terutama sifat kuat tekan beton non struktur.. Universitas Indonesia Rekayasa material..., Moh Azhar, FMIPA UI, 2015..
(18) 4. 1.3.. Manfaat Penelitian Dengan adanya menelitian ini harapkan dapat memberikan sumbangsih. terhadap perkembangan IPTEK, khususnya dibidang Materials Science dan Teknik Sipil. Penelitian ini juga diharapkan dapat membantu untuk memberikan solusi dalam meningkatkan nilai ekonomis Abu Sekam Padi yang selama ini dianggap sebagai limbah dan Batu Apung yang kurang pemanfaatannya, khususnya untuk aplikasi dibidang Teknik Sipil.. 1.4.. Batasan Masalah Dalam penelitian ini hanya difokuskan kepada peninjauan sifat mekanik. LWC yang ditambahkan bahan pengisi berupa ASP dan BA saja. Sifat mekanik yang dimaksud disini adalah sifat kuat tekan untuk LWC non struktur.. 1.5.. Model Operasional Penelitian Penulisan dalam penelitian ini terbagi dalam lima BAB, BAB 1 sampai. BAB 5, BAB 1 merupakan pendahuluan yang terdiri dari latar belakang, tujuan penelitian, manfaat penelitian, batasan penelitian dan model operasional penelitian. BAB 2. merupakan tinjauan pustaka atau studi literatur. BAB 3. merupakan metodologi penelitian yang meliputi proses preparasi sampel, karakterisasi sample hingga pengamatan dan pengolahan data. BAB 4 berisikan mengenai data hasil penelitian dan pembahasan. Hasil dan analisa merupakan hasil interprestasi data yang diperoleh dari hasil karakterisasi sample berdasarkan hipotesis dan dasar teori pendukungnya. BAB 5 merupakan kesimpulan dan saran. Kesimpulan sementara yang diperoleh selama penelitian dan saran-saran untuk memperbaiki proses pembuatan atau memberikan alternative terhadap material maupun proses yang dilakukan.. Universitas Indonesia Rekayasa material..., Moh Azhar, FMIPA UI, 2015..
(19) 5. BAB II TINJAUAN PUSTAKA. Penggunaan beton dan bahan-bahan vulkanik seperti abu pozzolan sebagai pembentuknya telah dimulai sejak zaman Yunani dan Romawi, bahkan mungkin sebelum itu (Nawy, 1985:2-3). Penggunaan bahan beton bertulang secara intensif dimulai pada awal abad ke sembilan belas. Pada tahun 1801, F. Coignet menerbitkan tulisannya mengenai prinsip-prinsip konstruksi dengan meninjau kelembaban bahan beton. Pada tahun 1850, J.L. Lambot untuk pertama kalinya membuat kapal kecil dari bahan semen untuk dipamerkan pada Pameran Dunia 1855 di Paris. J. Monier, seorang ahli taman dari Perancis, mematenkan rangka metal sebagai tulangan beton untuk tempat tanamannya. Pada tahun 1886, Koenen menerbitkan tulisan mengenai teori dan perancangan struktur beton, dan pada tahun 1906, C.A.P. Turner mengembangkan plat slub tanpa balok. Seiring dengan kemajuan besar yang terjadi dalam bidang ini terbentuklah German Committee Reinforce Concrete (GCRC), Australian Concrete Committee (ACC), American Concrete Institute (ACI), dan British Concrete (BC). Di Indonesia, Departemen Pekerjaan Umum-Lembaga Penyelidikan Masalah Bangunan (DPU-LPMB) menerbitkan peraturan-peraturan standar beton yang biasanya mengadopsi peraturan internasional yang disesuaikan dengan kondisi bahan dan jenis bangunan di Indonesia. Struktur beton dapat didefinisikan sebagai bangunan beton yang terletak di atas tanah yang menggunakan tulangan atau tidak menggunakan tulangan (ACI 318-89, 1990:1-1). Struktur beton sangat dipengaruhi oleh komposisi dan kualitas bahan-bahan pembentuk beton. Kekuatan tekan beton dipengaruhi oleh beberapa faktor, diantaranya: perbandingan air terhadap semen (w/c), perbandingan agregat terhadap semen (a/c), dan usur agregat (gradasi, bentuk, kekerasan, kekuatan, permukaan, ukuram maximum). Untuk harga w/c yang sama, makin besar a/c makin tinggi kekuatan beton, karena makin banyak agregat makin banyak air yang diserap, sehingga w/c efektifnya berkurang. Beton mempunyai kuat tekan yang besar sementara kuat tariknya kecil. Oleh karena itu untuk struktur bangunan, beton selalu dikombinasikan dengan tulangan. Universitas Indonesia Rekayasa material..., Moh Azhar, FMIPA UI, 2015..
(20) 6. baja untuk memperoleh kinerja yang tinggi. Beton ditambah dengan tulangan baja menjadi beton bertulang. Kekuatan tekan adalah kemampuan beton untuk menerima gaya tekan persatuan luas. Beton terbuat dari agregat halus dan kasar yang diikat bersama pasta semen akan menjadi campuran beton segar yang kemudian mengeras, maka kualitas semen sangat mempengaruhi kualitas beton, yang bila semakin tebal tentu semakin kuat. Beton mengalami deformasi disertai dengan penyusutan akibat mengeringnya beton seiring dengan bertambahnya waktu pengerasan. Agar diperoleh hasil yang memuaskan, dibutuhkan pengenalan mendalam mengenai sifat-sifat yang berkaitan dengan bahan-bahan penyusun beton tersebut. Untuk mengetahui dan mempelajari perilaku bahan-bahan penyusun beton memerlukan pengetahuan mengenai karakteristik masing-masing komponen. Parameterparameter yang paling mempengaruhi kekuatan beton adalah Kualitas semen, proporsi semen terhadap campuran, kekuatan dan kebersihan agregat, interaksi atau adhesi antara pasta semen dengan agregat, penyelesaian dan pemadatan beton yang benar, perawatan beton, dan kandungan klorida tidak melebihi 0,15% dalam beton yang diekspos dan 1% bagi beton yang tidak diekspos (Nawy, 1985:24). Nilai kuat tekan beton dengan kuat tariknya tidak berbanding lurus. Setiap usaha perbaikan mutu kekuatan tekan hanya disertai oleh peningkatan kecil dari kuat tariknya. Nilai kuat tarik berkisar antara 9%-15% kuat tekannya. Kecilnya kuat tarik beton ini merupakan salah satu kelemahan dari beton biasa, untuk mengatasinya beton dikombinasikan dengan baja tulangan. Pendekatan hitungan dilakukan dengan menggunakan modulus of rapture, yaitu tegangan tarik beton yang muncul saat pengujian tekan beton normal (Mulyono T., 2005). Setelah perancangan beton selesai, dilakukan pengujian lanjutan beton segar dan pengujian beton keras. Pengujian beton segar dimaksudkan untuk mengetahui workability atau kemudahan dalam pengerjaannya. Indikator dari kemudahan pengerjaan ini dapat dilihat dari nilai slump beton. Tujuan pengujian beton segar lainnya adalah untuk melihat apakah terjadi bleeding dan segregation atau tidak. Sedangkan pengujian beton keras terutama dimaksudkan untuk mengetahui kekuatan tekan. Pengujian ini dilakukan dengan membuat benda uji berbentuk silinder atau berbentuk kubus yang pada umur tertentu diuji.. Universitas Indonesia Rekayasa material..., Moh Azhar, FMIPA UI, 2015..
(21) 7. Beton dapat juga digunakan untuk struktur yang memerlukan bahan yang ringan, misalnya beton ringan struktural (DPU-LPMB SKBI.1.4.53,1989:5) yaitu beton yang mengandung agregat ringan dan mempunyai density sesuai dengan standar ASTM (America Society For Testing And Material) C-567. 2.1. Beton Ringan atau Lightweight Concrete (LWC) Pada tahap awal dalam merancang sebuah proyek bangunan, sifat bahan konstruksi harus dievaluasi dengan baik. Oleh karena itu, muncul kebutuhan untuk menganalisis bahan-bahan untuk digunakan dalam konstruksi secara eksperimental dengan lebih rinci. Hal ini merupakan inti dari kegiatan awal merancang sebuah proyek. bangunan (Gunduz dan Ugur, 2005). Jadi, secara. umum, sebelum merekomendasikan material untuk aplikasi tertentu (baik struktural atau non-struktural) maka diperlukan studi tentang karakteristik mekanik pada material itu sendiri (Babu dkk, 2005). Sebagai Salah satu alternatif yang dewasa ini telah luas digunakan sebagai komponen dari bangunan sipil adalah LWC yang dibuat dari campuran lightweight aggregate (LWA), yaitu beton yang mempunyai massa kering udara sesuai dengan syarat pada ―Testing Method for Unit Weight of Structural Lightweight Concrete” ASTM C-567 dimana densitynya tidak lebih dari 1900 kg/m3. Penggunaan LWA dalam pembuatan LWC dikarenakan LWA memiliki konduktivitas thermal rendah dan dari segi pembiayaan produksi blok beton ringan dapat lebih ekonomis. LWA dapat diproses menggunakan bahan alami, baik yang diproses lebih lanjut maupun yang tidak. LWA memiliki jumlah rongga yang besar didalamnya, sehingga bila digunakan untuk pembuatan LWC akan memiliki efisiensi isolasi thermal yang relatif lebih tinggi jika dibandingkan beton normal. Pada LWC memiliki keunggulan berupa beratnya yang ringan, dan isolasi thermal yang baik, tetapi memiliki kelemahan berupa sifat mekanik yang relatif rendah, sehingga hanya cocok digunakan sebagai non-load bearing walls (AlJabri dkk, 2005). Keunggulan lainnya pada LWC adalah dalam hal mengurangi beban mati pada struktur dan beban lateral gempa.. Universitas Indonesia Rekayasa material..., Moh Azhar, FMIPA UI, 2015..
(22) 8. Aplikasi LWC atau LWAC dalam bidang teknik sipil secara umum digunakan untuk struktural dan non-struktural, serta sebagai pengisi atau untuk komoponen isolasi panas dan suara seperti panel, bata, partisi serta beban bantalan elemen struktural (Asgeirsson dan Lettsteypur, 1984). Ada dua parameter utama yang menentukan sifat mekanik LWC yaitu densitas dan rasio w/c. Oleh karena itu untuk rasio w/c yang konstan, dengan menggunakan LWA yang memiliki nilai berat jenis yang tinggi akan menghasilkan tingkat kekuatan yang lebih tinggi pula. Sifat mekanik yang paling utama dari LWC disini adalah sifat kekuatan tekan. Kekuatan tekan pada LWC dipengaruhi oleh banyak faktor, antara lain kualitas dan ukuran agregat (besar, menengah dan halus), komposisi beton, dan kondisi pengerasan. Ke dkk (2009) mengadakan studi tentang estimasi kualitas agregat didasarkan pada pengukuran berbagai karakteristik fisik dan pengamatan struktur porinya. Tujuan dari studi ini adalah untuk memberikan pemahaman yang lebih baik tentang pengaruh karakteristik LWA terhadap kuat tekan dan modulus elastisitas dari beton. Pada penelitiannya digunakan sampel dengan. variasi. agregat dan densitasnya yang ditampilkan pada Tabel 2.1.. Tabel 2.1. Variasi sampel terhadap density (Ke dkk, 2009) Name 0/4 650 A 0/10 550 A 0/10 430 A 0/10 520 S 0/10 675 S 0/8 750 S. Various densities 3 ρv(kg/m ) ρssd(kg/m3) ρrd(kg/m ) 600,5 1223,2 926,8 560,3 1137,6 921,2 454,7 878,2 736,9 493,4 1033,6 900,6 729,0 1578,2 1433,6 877,7 1714,1 1576,9 3. Intergranular porosity 1-ρv/ ρrd 0,35 0,39 0,38 0,45 0,49 0,44. Untuk sampel yang dibuat ada 6 variasi dimana angka pertama menunjukan rentang ukuran d/D, angka yang kedua mengindikasikan densitas sampel dan huruf terakhir mengindikasikan : A untuk clay dan untuk S adalah butiran dari agregatnya. Pada tabel 2.1 untuk ρssd adalah saturated-surface-drieddensity, ρrd adalah densitas partkel kering dan ρv adalah bulk density. Sedangkan untuk pengukuran porositas terhadap sampel agregat yang dibuat ditampilkan pada Tabel 2.2. Universitas Indonesia Rekayasa material..., Moh Azhar, FMIPA UI, 2015..
(23) 9. Tabel 2.2. Porositas pada variasi sampel yang digunakan (Ke dkk, 2009). Total porosity Water open porosity after 20 days immersion (%) Water porosity/Total porosity. Dry particle density. 0/4 650 A. 0/10 550 A. 0/10 550 A. 0/10 520 S. 0/10 675 S. 0/8 750 S. 64 41,7 65,16 0,93. 65 31,3 48,15 0,92. 72 20,6 28,61 0,74. 65 13,5 20,77 0,90. 45 16,5 36,67 1,43. 39 17,35 44,48 1,58. Hasil pengukuran kekuatan tekan terhadap variasi sampel terhadap densitas yang digunakan dalam penelitian ini (Ke dkk, 2009) seperti terlihat pada Gambar 2.1.. Gambar 2.1. Grafik korelasi antara kekuatan tekan terhadap densitas pada fraksi volume LWA beberapa variasi sampel yang digunakan (Ke dkk, 2009) Sedangkan hasil pengukuran kekuatan tekan pada variasi sampel terhadap densitas setelah dikeringkan dapat dilihat pada Gambar 2.2.. Gambar 2.2. Grafik hubungan antara kekuatan tekan dan densitas sampel yang telah dikeringkan (Ke dkk, 2009). Universitas Indonesia Rekayasa material..., Moh Azhar, FMIPA UI, 2015..
(24) 10. Pada penelitian Ke dkk (2009) didapatkan kesimpulan bahwa untuk agregat yang densitasnya dibawah 1000 kg/m3 yaitu pada sampel 0/4 650 A, 4/10 550 A, 4/10 430 A dan 4/10 520 S memiliki kekuatan tekan yang sangat dipengaruhi oleh fraksi volume agregatnya. Sedangkan untuk sampel 4/10 675 S dan 4/8 750 S yang memiliki densitas 1430 kg/m3 dan 1570 kg/m3, kenaikan fraksi volume tidak mengurangi kekuatan tekan pada LWC. Chi dkk (2003) mengadakan penelitian tentang pengaruh karakteristik agregat terhadap kekuatan dan kekakuan pada LWC. Pada penelitiannya digunakan Portland cement dengan specific gravity 3,15 pada semua campuran, dan digunakan agregat dari pasir kali dengan specivic gravity dan ukuran maksimumnya 4 mm sebanyak 1,8 %. Bentuk specimen uji mengacu kepada ASTM C192, sedangkan prosedur pengujiannya mengacu kepada ASTM C39. Penelitian ini menghasilkan data tentang kekuatan tekan pada beberapa tipe agregat terhadap beberapa variasi rasio air dan semen yang ditampilkan pada Tabel 2.3 dan Gambar 2.3. Sifat dari tipe agregat ditampilkan pada Tabel 2.4. Sedangkan hasil penelitian tentang pengaruh fraksi volume terhadap kekuatan tekan dan rasio air/binder ditampilkan pada Gambar 2.4.. Tabel 2.3. Kekuatan tekan (MPa) pada beberapa tipe agregat ringan terhadap beberapa variasi rasio air dan semen (Chi dkk, 2003) Aggregate Volume w/b= 0,3 w/b= 0,4 w/b= 0,5 type fraction (%) (A1) (A2) (A3) I (B1). 18 24 30 36. (C1) (C2) (C3) (C4). 41,7 37,5 35,0 31,8. 32,6 29,5 27,6 23,0. 29,8 25,7 23,3 21,3. III (B2). 18 24 30 36. (C1) (C2) (C3) (C4). 43,9 41,2 38,7 35,6. 27,3 33,4 30,4 28,4. 27,4 26,3 24,6 21,5. III (B3). 18 24 30 36. (C1) (C2) (C3) (C4). 48,2 47,4 45,8 42,6. 38,3 37,6 38,9 37,5. 31,2 29,5 27,7 29,7. Universitas Indonesia Rekayasa material..., Moh Azhar, FMIPA UI, 2015..
(25) 11. Tabel 2.4. Sifat dari agregat yang digunakan (Chi dkk, 2003) Aggregate type. Specific grafity (SSD) 1,65 1,69 1,76. Compressive strength (MPa). I II III. Specific grafity (OD) 1,23 1,29 1,44. Water Bulk unit absorption weight(AD) (%) (kg/m3) 34,4 857 30,5 952 20,8 972. Crushing value (%) 43,9 36,1 31,6. Particle strength (MPa) 6,01 7,53 8,57. Aggregate type. 50. Type I Type II Type III. 45 40 35. 30 25 20 0.25 0. 0.30 0.1. 0.35 0.2. 0.40 0.3. 0.45 0.4. 0.50 0.5. Water/binder ratio. Gambar 2.3. Pengaruh rasio air/binder terhadap kekuatan tekan pada beberapa tipe agregat (Chi dkk, 2003). Compressive strength (MPa). Volume fraction VF=18% VF=24% VF=30% VF=36%. 50 45 40 35 30 25 20 0.25 0. 0.30 0.1. 0.35 0.2. 0.40 0.3. 0.45 0.4. 0.50 0.5. water/binder ratio. Gambar 2.4. Pengaruh fraksi volume terhadap kekuatan tekan dan rasio air/binder (Chi dkk, 2003). Universitas Indonesia Rekayasa material..., Moh Azhar, FMIPA UI, 2015..
(26) 12. Dari penelitian yang dilakukan Chi dkk (2003) dapat disimpulkan bahwa pada LWC penggunaan rasio air/binder dan sifat LWA sangat mempengaruhi kekuatan tekan LWC itu sendiri. Beton dengan substitusi batu apung dapat digolongkan sebagai LWC. Substitusi parsial atau mengganti sebagian agregat kasar normal dengan agregat ringan batu apung pada beton dapat dijadikan penyelesaian permasalahan density agregat kasar yang besar yaitu sekitar 1200-1700 kg/m3. LWC merupakan salah satu bagian dari beton ringan selain aerated lightweight concrete dan no fine lighweight concrete. LWC dapat dibuat dari agregat ringan yang berasal dari a) agregat ringan produk industri misalnya furnace bottom ash, furnace klinker, b) agregat ringan natural misalnya batu apung dan scoria, c) agregat ringan artifisial misalnya slag, expand shale,expand clay, perlite dan vermiculite. Menurut ACI 213R-87 (ACI Committee 213R-87, 1999) terdapat tiga jenis LWC berdasarkan density, yaitu: a) LWC kepadatan rendah dengan density kering udara 400 – 800 kg/m3 dan kuat tekan antara 0,69– 6,89 MPa. Agregat ringan yang digunakan antara lain vermiculite dan perlite. b) LWC kekuatan moderat dengan density kering udara 800–1400 kg/m3 dan kuat tekan antara 6,89–17,24 MPa. Agregat ringan yang digunakan antara lain batu apung dan scoria. c) LWC struktural dengan density kering udara 1440 – 1850 kg/m3 dan kuat tekan lebih besar dari 17,24 MPa. Agregat ringan yang digunakan antara lain pumice stone, slag, clay dan slate. Bulk Density atau density LWC bervariasi tergantung pada density agregat, kadar semen dan factor air-semen. Secara umum density LWC akan naik jika density agregat dan kadar semen meningkat, tetapi akan menurun jika faktor airsemen meningkat. Density LWC juga sangat berpengaruh pada sifat-sifat mekanik yang dihasilkan yaitu kuat tekan dan kuat tarik. LWC dengan density rendah akan sukar dipadatkan sehingga segregasi yang terjadi menyebabkan rendahnya kuat tekan dan kuat tarik. Penentuan density LWC berdasarkan standar ASTM C56791 (ASTM C567-91, 1996). Menurut Satish dkk. (Chandra Satish and Berntsson Leif, 2002), density LWC terbagi menjadi density tinggi antara 1550-1850 kg/m3 dan density menengah antara 800–1550 kg/m3. Menurut ACI 213R-87 (ACI Committee 213R-87, 1999) terdapat tiga density LWC yaitu: a) density rendah. Universitas Indonesia Rekayasa material..., Moh Azhar, FMIPA UI, 2015..
(27) 13. antara 400–800 kg/m3. b) density menengah antara 800–1400 kg/m3 dan c) density tinggi antara 1440–1850 kg/m3. Dionisius dkk (Dionisius Tripriyo, dkk., 2010) melaporkan bahwa kadar optimum substitusi parsial batu apung pada beton agregat ringan batu apung adalah 20% dari berat agregat kasar dengan kuat tekan dan kuat tarik belah sebesar 39,24 MPa dan 4,05 MPa. Kondisi campuran beton agregat ringan memerlukan tambahan 20% fly ash, additive sika Ln 1,5% dan sika Vz 0,4% dengan permukaaan batu apung dilapisi pasta semen. Sedangkan, density beton agregat ringan batu apung adalah 1850 kg/m3 lebih ringan 22% daripada beton agregat normal. Joedono (Joedono, 2006) melaporkan bahwa dimensi agregat maksimum 15 mm, baik agregit kasar batuan piroklastik merah maupun batu apung menghasilkan kuat tekan rnaksimum, yaitu 24, 26 Mpa dan 7,7 T Mpa. Modulus elastisitas untuk beton batuan piroklastik merah tertinggi diperoleh pada ukuran maksimum 15 mm 19366,26 Mpa Modulus elastisitas beton batu apung tertinggi diperoleh pada diameter maksimum 25 mm yaitu sebesar 6691.542 Mpa. Hasil pengujian kuat tarik belah untuk beton dengan agregat kasar batuan piroklastik mempunyai tren yang teratur bila dibandingkan beton batu apung yang cenderung naik-turun tidak beraturan. Uma Ramasamy dan Paul Tikalsky (2012) melaporkan hasil penelitiannya tentang beton yang menggunakan batu apung sebagai bahan campuran semen porland. Kuat tekan beton adalah salah satu pertimbangan utama dalam desain campuran beton. Menurut ASTM C39, kuat tekan silinder ukuran 4"x8" diuji dengan nilai yang berbeda dari batu apung sebanyak lima campuran yang biasa digunakan untuk spesifikasi 4 ksi. Lima campuran termasuk 100% semen (ASTM Tipe II / V), 20% dari DS200, DS325, batu apung ultrafine dengan 80% semen dan 30% DS325 dengan 70% semen dengan rasio w/c 0.485. Hasil uji kuat tekan ditunjukkan pada Gambar. 10.. Universitas Indonesia Rekayasa material..., Moh Azhar, FMIPA UI, 2015..
(28) 14. Gambar 2.5 Hasil Uji Kuat Tekan Beton Silinder Ukuran 4"x8" (Uma Ramasamy dan Paul Tikalsky, 2012) Campuran yang mengandung batu apung mencapai kuat tekan lebih rendah dibandingkan dengan campuran 100% semen porland. Namun, kekuatan minimum pada usia 7 hari lebih besar dari 3000 psi dan pada usia 28 hari ini lebih besar dari 4500 psi. Campuran yang mengandung batu apung ultrafine mencapai kekuatan awal tinggi dibandingkan dengan campuran yang mengandung DS200 dan DS325. Tren ini didukung oleh hasil dari perilaku hidrasi semen ketika dicampur, di mana campuran batu apung ultrafine menunjukkan karakteristik hidrasi cepat. Campuran 80C20DS200 mencapai lebih tinggi kekuatan pada 7 dan 28 hari dibandingkan dengan campuran 80CDS325 yang menunjukkan perbedaan perilaku hidrasi yang ditunjukkan oleh nilai yang berbeda dari batu apung. Kawkab H. dkk (2008) melaporkan hasil penelitian sifat mekanik beton agregat ringan menggunakan batu apung lokal (tersedia di utara Iraq) untuk produksi beton struktur agregat ringan. Dalam penelitian ini, dua jenis beton ringan diproduksi menggunakan batu apung sebagai agregat kasar dengan pasir alam dan juga dengan batu apung sebagai agregat halus, diselidiki efek menggunakan Superplasticizer: High Range Water Reducing Admixture (HRWRA) ditambah dengan 8% abu sekam padi sebagai pengganti sebagian berat semen, pada sifat mekanik beton ringan. Pengujian yang dilakukan antara lain adalah kekuatan tekan dan kekuatan tarik belah untuk semua jenis beton agregat. Universitas Indonesia Rekayasa material..., Moh Azhar, FMIPA UI, 2015..
(29) 15. ringan dan pada berbagai usia curing. Pada campuran yang menggunakan 8% abu sekam padi, dengan dosis optimum HRWRA (6% berat semen) menunjukkan peningkatan yang cukup sifat mekanik pada semua umur dibandingkan dengan referensi beton. HRWRA adalah salah satu jenis superplasticizer sulfonasi melamin formaldehid kondensat, yang dikenal secara komersial sebagai Melment L10, digunakan selama penelitian ini sebagai kisaran tinggi air mengurangi campuran. Supperplasticizer digunakan untuk menghasilkan beton mutu tinggi dengan mengurangi rasio w/c, dengan slump 50 ± 5 mm, untuk referensi campuran beton. Hasil menunjukkan bahwa secara umum, semua spesimen beton memperlihatkan peningkatan kuat tekan pada berbagai usia. Gambar 2.6 menunjukkan bahwa kuat tekan LWAC menurun dengan penambahan batu apung agregat halus sebagai pengganti total pasir alam. Penyebab utama adalah bahwa penambahan agregat halus batu apung untuk LWAC meningkatkan kebutuhan air untuk campuran agar mendapatkan kemampuan kerja yang cocok dan sebagai hasilnya, kekuatan berkurang. Persentase penurunan 28-hari kuat tekan beton Ref2 dibandingkan dengan Ref1 beton (tanpa agregat halus batu apung) adalah 4,39%. Persentase peningkatan kuat tekan pada 90 hari curing RHA-HRWRA1 dan beton RHA-HRWRA2 relatif terhadap referensi beton yang masing-masing. Compressive strength (N/mm2). 7.76% dan 12,8%.. 38 36 34 32 30 28 26 24 22 20 18 16. Ref1 concrete RHA-HRWRA1 concrete Ref2 concrete RHA-HRWRA2. 0. 10. 20. 30. 40. 50. 60. 70. 80. 90. 100. Age (days). Gambar 2.6 Kuat tekan berbagai jenis LWAC pada berbagai usia (Kawkab H. dkk, 2008) Universitas Indonesia Rekayasa material..., Moh Azhar, FMIPA UI, 2015..
(30) 16. 2.2 Portland Cement (PC) Semen adalah bahan yang bersifat adhesif maupun kohesif, yaitu bahan pengikat. Semen Portland pertama kali diproduksi dipabrik oleh David Saylor di Coplay Pennsylvania, Amerika Serikat pada tahun 1875. Menurut ASTM C150,1985, definisi semen Portland yaitu semen hidrolik yang dihasilkan dengan cara menghaluskan klinker yang terutama terdiri dari kalsium silikat hidrolik, yang umumnya mengandung satu atau lebih bentuk kalsium sulfat sebagai bahan tambahan yang digiling bersama-sama dengan bahan utamanya. Fungsi semen untuk bereaksi dengan air menjadi pasta semen. Pasta semen berfungsi untuk merekatkan butir-butir antar agregat agar terjadi suatu massa yang kompak/padat. Selain itu pasta semen juga untuk mengisi rongga-rongga antara butir-butir agregat. Walaupun volume semen kira-kira 10 persen dari volume beton, namun karena bahan perekat yang aktif dan mempunyai harga paling mahal dari bahan dasar beton yang lain maka peranan semen menjadi sangat penting. Sedangkan agregat tidak memainkan peranan yang penting dalam reaksi kimia tersebut, tetapi berfungsi sebagai bahan pengisi mineral yang dapat mencegah perubahanperubahan volume beton setelah pengadukan selesai dan memperbaiki keawetan beton yang dihasilkan. Pada umumnya beton mengandung rongga udara sekitar 1% - 2%, pasta semen (semen dan air) sekitar 25% - 40%, agregat halus dan kasar sekitar 60% 75% (PB 1989). Untuk mendapatkan kekuatan yang baik, sifat dan karakter dari masing-masing material penyusun tersebut perlu dipelajari. Semen merupakan hasil industri yang sangat kompleks, dengan campuran serta susunan yang berbeda-beda. Semen dapat dibedakan jadi dua kelompok, yaitu semen hidrolik dan non hidrolik. Bahan-bahan utama penyusun semen Portland adalah Kapur (CaO), Silika (SiO2), Oksida Besi (Fe2O3), dan Alumina (Al2O3). Ada 2 sifat utama semen Portland yaitu sifat fisika diantaranya kehalusan butir, waktu pengikatan, kekuatan tekan, pengikatan semu, panas hidrasi, dan hilang pijar. Berikutnya sifat kimia meliputi kesegaran semen, sisa yang tak larut dan yang paling utama adalah komposisi syarat yang telah ditentukan.. Universitas Indonesia Rekayasa material..., Moh Azhar, FMIPA UI, 2015..
(31) 17. 2.2.1 Reaksi Hidrasi Ketika air ditambahkan ke dalam campuran semen, proses kimiawi yang disebut hidrasi akan berlangsung. Senyawa kimia di dalam semen akan bereaksi dengan air dan membentuk komponen baru yang disebut pasta semen, yang mempunyai kekentalan tinggi dan akhirnya menjadi pasta yang mengeras yang mempunyai kekuatan mekanik yang tinggi. Ada 2 mekanisme hidrasi semen yaitu mekanisme larutan dan mekanisme padat. Pada mekanisme larutan, zat yang direaksikan larut dan menghasilkan ion dalam larutan.. Ion-ion ini kemudian akan bergabung sehingga. menghasilkan zat yang menggumpal (flocculate). Pada semen, proses hidrolisis lebih dominan dari pada larutan, karena daya larut senyawa yang ada kecil. Pada Tabel 2.5 terlihat hasil reaksi hidrasi senyawa semen. Tabel 2.5. Reaksi hidrasi senyawa semen Senyawa yang bereaksi. Komponen yang dihasilkan. Trikalsium Silikat + Air. Gel Tobermorit + Kalsium Hidroksida. Dikalsium Silikat + Air. Gel Tobermorit + Kalsium Hidroksida. Tetrakalsium Aluminoferrit + Air + Kalsium Hidroksida Tetrakalsium Aluminat + Air + Kalsium Hidroksida Tetrakalsium Aluminat + Air + Gypsum. Kalsium Aluminoferrit Hidrat Tetrakalsium Aluminat Hidrat Kalsium Monosulfoaluminat. Semen bertindak sebagai pengikat ketika bereaksi dengan air untuk membentuk struktur yang dominan terdiri dari Kalsium Silikat Hidrat (CSH), yang tumbuh membentuk struktur berbentuk pelat sebagai produk dari hidrasi. Pada tahap awal proses hidrasi, struktur masih belum begitu padat, yang ditandai oleh adanya pori-pori atau rongga. Mekanisme hidrasi dapat dianalisis melalui pertumbuhan strukturmikro pasta semen pada waktu yang berbeda selama proses hidrasi. Porositas berkurang seiring bertambahnya waktu hidrasi, hal tersebut dikarenakan adanya pertumbuhan kristalit CSH seiring bertambahnya waktu hidrasi. Evolusi mikrostruktur dari CSH pada pasta semen di hari ke 7, 28 dan 56 Universitas Indonesia Rekayasa material..., Moh Azhar, FMIPA UI, 2015..
(32) 18. untuk 100% semen Portland yang dikarakterisasi menggunakan SEM ditampilkan pada Gambar 2.7 (A. Manaf, and V. Indrawati, 2011). Gambar 2.7 Evolusi mikrosktuktur CSH pada komposisi 100 wt% semen Portland selama proses hidrasi sampai 56 minggu (A. Manaf, and V. Indrawati, 2011) Hasil SEM pada campuran 100wt% Portland semen Gambar 2.7 menunjukkan bahwa struktur CSH mulai mengembang atau tumbuh pada waktu awal dan terus berkembang sampai struktur lebih padat dari CSH hadir pada akhir waktu (56 hari). Struktur yang padat membuat beton lebih tahan lama karena tahan terhadap serangan lingkungan. Menurut Alizadeh, Beaudoin dan Raki (2011) CSH merupakan produk utama dari proses hidrasi pada semen Portland, dimana senyawa ini betanggung jawab penuh dan memiliki peranan penting terhadap pengaturan sifat mekanik dan fisik seperti kekuatan dan penyusutan setelah pasta semen mengeras. Proses desorption air pada semen Portland berpengaruh terhadap modulus elastisitasnya terutama akan signifikan ketika tingkat kelembaban relatif sekitar di bawah 11%, seperti pada Gambar 2.8 Hasil yang didapat seperti pada Gambar 2.8 terkait sekali dengan keberadaan dan kondisi dari CSH yang ada pada semen Portland. Parameter utama yang mengontrol pembentukan berbagai struktur CSH adalah rasio molar antara CaO dan SiO2 (C/S ratio), tetapi studi yang mempelajari pengaruh ratio C/S terhadap sifat mekanik pada CSH masih terbatas.. Universitas Indonesia Rekayasa material..., Moh Azhar, FMIPA UI, 2015..
(33) 19. Gambar 2.8 Pengaruh proses desorption air terhadap modulus elastisitas pada semen Portland untuk (a) W/C = 0,3 dan (b) 0,4 (Alizadeh, Beaudoin dan Rakim, 2011) Pada penelitian ini variasi ratio C/S dan poroitas dilakukan untuk mendapatkan informasi terkait dengan sifat mekaniknya seperti ditapilkan pada Gambar 2.9. Meningkatnya presentasi porositas pada sampel akan menurunkan modulus elestisitas untuk semua ratio C/S. Dari Gambar 2.9 menunjukkan bahwa pada tingkat porositas yang lebih tinggi, nilai-nilai E pada C/S = 0,8 lebih besar jika dibandingkan dengan nilai E pada rasio C/S lainnya.. Gambar 2.9 Pengaruh variasi komposisi ratio C/S dan porositas terhadap modulus elastisitas (Alizadeh, Beaudoin dan Rakim, 2011). Universitas Indonesia Rekayasa material..., Moh Azhar, FMIPA UI, 2015..
(34) 20. 2.2.2 Hidrasi C3S dan C2S Kalsium Silikat akan terhidrasi menjadi gel kalsium silikat hidrat (gel tobelmorite) yang disingkat gel CSH dan kalsium hidroksida yang dihasilkan akan membuat sifat basa kuat (PH = 12,5). Ini menyebabkan semen sensitif terhadap asam dan akan mencegah timbulnya korosi pada besi baja. Dalam bentuk kesetimbangan reaksi hidrolisis antara senyawa C3S dan C2S ditampilkan pada diagram fasa Gambar 2.10 dibawah ni.. Sistem alir CaO – SiO2 – H2O Gambar 2.10. Diagram Fasa hidrasi semen (Taylor, 1997) Sebagai gambaran proses kimia hidrasi C3S dan C2S sebagai berikut : 2(3CaO.SiO2) + 6H2O. 3CaO.2SiO2.3H2O + 3Ca(OH)2. 2C3S. C-S-H gel. + 6H. Trikalsium Silikat. gel tobermorite. + 3CH Kalsium hidroksida. 2(2CaO.SiO2) + 4H2O. 3CaO.2SiO2.2H2O + Ca(OH)2. 2C2S. C-S-H gel. + 6H. Dikalsium Silikat. gel tobermorite. + CH Kalsium hidroksida. Universitas Indonesia Rekayasa material..., Moh Azhar, FMIPA UI, 2015..
(35) 21. 2.2.3 Hidrasi C3A Hidrasi C3A terjadi secara mendadak dengan disertai pengeluaran panas yang banyak. Akan terbentuk kristal kalsium aluminat hidrat yang menyebabkan pengerasan (hardening) dari pasta semen. Kejadian ini disebut Flash set atau quick set. Itu sebabnya perlu ditambahkan gypsum pada waktu penggilingan klinker, untuk memperkecil reaktivitas C3A. Proses kimia hidrasi C3A sebagai berikut : 3CaO.Al2O3 + 10H2O + CaSO4.2H2O Trikalsium aluminat. Gypsum. 3CaO.Al2O3.CaSO4.12H2O Ettringite. 3CaO.Al2O3 + 12H2O + Ca(OH)2. 3CaO.Al2O3.Ca(OH)2.12H2O. Trikalsium aluminat. Kalsium aluminat hidrat. C3A dan gypsum akan bereaksi lebih dahulu, menghasilkan kalsium sulfoaluminat. Kristal yang berbentuk jarum disebut Ettringite. Ettringite memblokir air dari permukaan C3A sehingga menunda hidrasi. Setelah gypsum bereaksi semua, barulah akan terbentuk kalsium aluminat hidrat. 2.2.4 Hidrasi C4AF Pada tahap awal, C4AF bereaksi dengan gypsum dan kalsium hidroksida membentuk kalsium sulfo-aluminat hidrat dan kalsium sulfo-ferrit hidrat yang kristalnya berbentuk jarum, seperti reaksi kimia berikut : 3CaO.Al2O3.Fe2O3 + 10H2O + 2Ca(OH)2 Tetrakalsium alumino-ferrit. Kalsium. 6CaO.Al2O3.Fe2O3.12H2O Aluminoferrit hidrat. Kecepatan reaksi hidrasi maksimum pada tahap awal dan kemudian menurun terhadap waktu. Ini disebabkan makin terbentuknya lapisan gel CSH pada kristal semen. Makin tebal lapisan semakin lambat hidrasi. Secara teoritis, proses hidrasi akan terhenti apabila tebal lapisan mencapai 25 mikron. Semen porland pada umumnya memiliki ukuran kristal antara 5 hingga 50 mikron. Proses hidrasi semen memerlukan air sebanyak 20% dari berat semen (faktor air- semen : w/c = 0,2) (PB 1989).. Universitas Indonesia Rekayasa material..., Moh Azhar, FMIPA UI, 2015..
(36) 22. 2.2.5 Kinetika Hidrasi Semen Studi tentang kinetika hidrasi dari semen ketika dicampur dengan air telah dilakukan oleh banyak peneliti. Mekanisme kinetika hidrasi dapat di identifikasi melalui pengukuran selama proses evolusi panas selama hidrasi. Model hidrasi dari semen Portland dan campuran semen menggunakan suplementary cementing materials (SCMs) telah banyak dilakukan peneliti (G. De Schutter, 1995, A.K. Schindler, K.J. Folliard, 2005, Klaus Meinhard, Roman Lackner, 2008, K. Fuji, W. Kondo, 1974, O. Bernard et al, 2003). Ide dasar dari mekanisme hidrasi semen adalah sebagai berikut (Judarta Vera Indrawati, 2009): 1. Hidrasi dari semen merupakan proses eksotermis dan melepaskan panas yang biasa disebut dengan hidrasi panas. 2. Derajat kebebasan dari hidrasi, dibentuk sebagai fraksi dari hidrasi panas yang telah dilepaskan. 3. Mekanisme hidrasi meliputi empat tahap yaitu: disolusi, induksi, nukleasi, dan difusi 4. Hidrasi semen Portland umumnya berhubungan dengan hidrasi dari masing-masing fase mineral semen diantaranya C3S, C2S, C3A, dan C4AF yang umumnya kalsium silika dan membentuk silika kalsium hidrat selama proses reaksi. 5. Penggunaan SCMs untuk menghasilkan campuran semen berhubungan dengan reaksi pozzolanik antara SCMs dan Ca(OH)2 dari hidrasi semen Portland. Reaksi ini memberikan kontribusi adanya panas spesifik dari masing-masing SCMs. Berdasarkan SCMs yang ditemukan di Jepang, Kishi dan Mackawa menyarankan bahwa untuk fly ash (Ca=8.8% dan CaO=48.1%) adalah 209 J/g, sedangkan untuk blast furnace slag GGBF (CaO=43.3% dan SiO2=31.3%) adalah 461 J/g.. Model hidrasi dari semen Portland dimulai dengan konsep kontinuitas periode induksi singkat diikuti dengan nukleasi dan terakhir adalah proses difusi. Proses nukleasi telah disimulasikan menggunakan model Avrami (Judarta Vera Indrawati, 2009).. Universitas Indonesia Rekayasa material..., Moh Azhar, FMIPA UI, 2015..
(37) 23. Parameter-parameter kinetik diaplikasikan dan diplot menjadi model dari hidrasi semen. Model teoritis ini sesuai dengan derajat hidrasi yang berasal dari pengukuran pelepasan panas. Model yang berasal dari hasil eksperimen ini dihitung berdasarkan. x.. Nilai dari. x. sebesar 0,3 dan 0,6 dapat digunakan sebagai. referensi untuk kinetika hidrasi semen. Nilai dari. x. hasil eksperimen sebesar 0,6. menghasilkan derajat hidrasi maksimum sebesar 0,8. Pengembangan model untuk semen campuran menghasilkan perbedaan pola morfologi untuk setiap umur pembuatan. Senyawa Alumunium di dalam tanur bereaksi membentuk produk alumunium. Pelepasan panas diukur berdasarkan perbedaan laju dari aliran panas. Pelepasan panas selama hidrasi dari campuran semen tidak hanya berasal dari mineral klinker tetapi juga senyawa alumunium di dalam slag. Sementara itu hidrasi semen dibatasi oleh difusi. Semen terhidrasi ditentukan oleh difusi pelarutan ion melalui lapisan hasil hidrasi yang terbentuk di sekitar klinker. Studi dari semen hasil slag pada tanur tinggi menyimpulkan bahwa hidrasi slag dibatasi oleh peluruhan secara eksponensial sebagai fungsi waktu. Hidrasi semen yang menyebabkan terjadinya filler dengan ukuran besar (high filler). Isi dari high filler sering digunakan di dalam proses produksi semen. Hal tersebut dimaksudkan untuk menghindari masalah kelebihan panas selama proses pengerasan semen. Terdapat dua macam jenis filler, yaitu limestone and quartz. Secara umum, filler jenis limestone sangat dipengaruhi oleh waktu induksi sehingga mekanisme hidrasi pun akan terpengaruh. Sedangkan untuk filler jenis quarsa tidak dipengaruhi oleh waktu induksi. Namun beberapa hasil studi menunjukan bahwa perubahan mekanisme hidrasi tidak begitu jelas teridentifikasi (Judarta Vera Indrawati, 2009). Beberapa hasil studi menyatakan bahwa: 1). penambahan material filler khususnya limestone kemampuan kinetis material akan meningkat, waktu dormant berkurang dan proses hidrasi dalam satu jam akan mengalami percepatan. 2). partikel-partikel filler bertindak sebagai sites dari nukleasi heterogen untuk pengendapan lebih atau kurang dari hasil hidrasi yang terkristalisasi, dalam proses ini hidrasi dapat dipercepat (Judarta Vera Indrawati, 2009).. Universitas Indonesia Rekayasa material..., Moh Azhar, FMIPA UI, 2015..
(38) 24. 2.3. Abu Sekam Padi (ASP) atau Rice Husk Ask (RHA) Abu sekam padi dibuat dengan membakar sekam padi dalam tungku suhu terkontrol untuk mendapatkan bahan pozzolan dengan kandungan tinggi silika amorf dan jumlah minimum karbon yang tidak terbakar. Umumnya kondisi pembakaran optimum adalah 500 0C selama 2 jam (AL-Khalaf, M.N., dan Yousif, H.A., 1984). Sebuah pabrik penggilingan dilakukan penggilingan RHA untuk jangka waktu 15 jam untuk masing-masing 0,5 kg RHA. RHA sebagai material tambahan campuran beton memiliki kemampuan untuk mengurangi kerusakan (cacat) dan segresi, dapat meningkatkan unjuk kerja secara signifikan (Mehta, P. K., 1983), hal ini terutama disebabkan oleh luas permukaan RHA yang besar di kisaran 50 sampai 60 m2/g (Mehta, P. K.,1992). Juga memberikan kontribusi terhadap kekuatan beton komposit pada usia awal 1 dan 3 hari, juga bertindak sebagai akselerator dalam membangun kekuatan. Sampai dengan 70 persen pengganti semen portland telah dilaporkan tanpa efek yang merugikan pada kekuatan, 10 sampai 20% pengganti semen bahkan menunjukkan efek yang menguntungkan pada kekuatan dan peningkatan yang luar biasa dalam karakteristik permeabilitas klorida dan sifat ketahanan lainnya dari beton. Juga, semen portland dicampur RHA sebanyak 10% telah terbukti cukup efektif dalam memerangi ekspansi akibat reaksi alkali agregat. Melalui efek mengisi pori-pori dan reaksi pozzolanik dari RHA karena luas permukaan yang tinggi dan struktur selular, permeabilitas beton dapat dikurangi secara signifikan (Chao Lung Hwang dan Satish Chandra, 1997). Penambahan pozzolan dapat meningkatkan sifat-sifat dari beton dengan memodifikasi mikro dan makro-struktur pasta semen. Efek menguntungkan langsung dari partikel RHA halus dan seluler pada cacat karakteristik dan pemisahan campuran beton adalah karena kemampuan adsorpsi air besar, luas permukaan internal yang tinggi, serta partikel mikroporous dan amorf. Sifat abu sekam padi dapat dilihat pada Gambar 2.11 (Hwang, C. L., and Wu, D. S., 1989). Penurunan kerusakan dalam zona transisi kuat antara materi padat dan pasta semen. Hal ini akan menyebabkan beton kedap air yang lebih dan tahan lama.. Universitas Indonesia Rekayasa material..., Moh Azhar, FMIPA UI, 2015..
(39) 25. Gambar 2.11 Mikrograf SEM RHA dibakar pada temperatur yang berbeda, Hwang dan Wu (Hwang, C. L., and Wu, D. S., 1989). Penambahan sejumlah abu sekam padi mikroporous mengadsorpsi sebagian besar air yang mengelilingi zat padat, menghasilkan air yang berkurang untuk rasio pengikat dan menyempurnakan struktur pori. Ini akibatnya mengurangi permeabilitas beton untuk penetrasi klorida seperti yang ditunjukkan pada Tabel 2.6 (Mehta, P. K.,1992). Telah ditemukan bahwa permeabilitas berkurang secara signifikan setelah 28 hari untuk pencampuran pasta semen dengan abu sekam padi 10, 20 atau 30 persen (Mehta, P. K.,1992). Permeabilitas dari pasta semen dengan abu sekam padi diyakini berada di kisaran 1x10-11 cm / detik.. Universitas Indonesia Rekayasa material..., Moh Azhar, FMIPA UI, 2015..
(40) 26. Tabel 2.6. Proporsi campuran dan Properties dari RHA pada Beton. Diadaptasi dari Mehta (Mehta, P. K.,1992). Mix Proportion, kg/m3. 1-yr. Slump mm. 28-d. Air %. 7-d. RHA (%). Permeability Coulumbs. 3-d. Mix No. Compressive strength, MPa. Fresh Proporties. 28-d. a. 0. 392. -. 1062. 786. 128. 0.33. 0.33. 1. 200. 45. 56. 65. 80. 3500. 2200. b. 9. 356. 36. 1062. 786. 128. 0.36. 0.36. 1.5. 225. 42. 56. 77. 86. 1260. 420. a. 0. 410. -. 1044. 786. 128. 0.31. 0.31. 1. 240. 47. 60. 66. 80. 3260. 2200. b. 13. 356. 54. 1044. 786. 128. 0.36. 0.36. 1.5. 175. 45. 60. 80. 92. 870. 250. a. 0. 428. -. 1026. 786. 128. 0.3. 0.3. 1.5. 225. 47. 62. 70. 81. 3000. 1800. b. 17. 356. 72. 1026. 786. 128. 0.3. 0.36. 1.5. 200. 46. 65. 80. 92. 390. 190. C. RHA. C.A. F.A. W. W/B. W/C. 1-yr. 1. 2. 3. All mixtures contained a constant amount of a superplasticizer in order to obtain high consistency. Coulumbs passed in a 6 hours standard test (AASHTO T-277), based on FHWA Report No. RD-81/119, Aug. 1981.. Penambahan bahan pozzolanik dapat mempengaruhi baik kekuatan dan permeabilitas dengan memperkuat antar muka (interface) agregat - pasta semen dan dengan memblokir pori besar di pasta semen terhidrasi melalui reaksi pozzolanik. Fenomena ini ditunjukkan pada Gambar 2.12. Hal ini diketahui bahwa reaksi pozzolanik memodifikasi pori-struktur. Hasilnya terbentuk karena reaksi pozzolanik menempati ruang kosong dalam struktur pori, yang dengan demikian menjadi padat. Porositas pasta semen berkurang, dan kemudian, pori-pori yang mengecil. Mehta (Mehta, P. K.,1992) telah menunjukkan penurunan yang signifikan dalam porositas pasta semen dengan penambahan RHA dan perbaikan dalam struktur pori.. Gambar 2.12 Mekanisme mengisi kekosongan dan efek transisi zona Penguatan RHA (Mehta, P. K.,1992). Universitas Indonesia Rekayasa material..., Moh Azhar, FMIPA UI, 2015..
(41) 27. Hasil penelitian yang dilaporkan oleh Rosario Madrid, dkk (2012) ditampilkan pada Gambar 2.13 yang memperlihatkan mikrograf SEM dari sampel abu sekam padi yang diperoleh, menunjukkan morfologi permukaan sangat berpori, dengan luas permukaan yang tinggi . Hal ini tampaknya cukup untuk aplikasi tertentu seperti bahan keramik khusus, dukungan katalis atau bahan bangunan (Rosario Madrid, dkk, 2012). Identifikasi fasa dalam RHA diperoleh dengan XRD (Gambar 2.14). Polanya berupa baris yang sangat luas dan tidak ada puncak, didefinisikan karena kristalinitas yang ditemui. Juga mewakili posisi teoritis dari reflexions utama dari fasa kristobalit (SiO2) dan grafit (C) dan tidak ada puncak ditemukan di posisi ini . Hasil yang diperoleh disimpulkan bahwa abu yang dihasilkan memiliki struktur amorph.. Gambar 2.13 Fotomikro SEM dari sampel RHA (Rosario Madrid, dkk, 2012). Gambar 2.14 Pola XRD dari sampel RHA (radiasi Cu - Kα) (Rosario Madrid, dkk, 2012). Universitas Indonesia Rekayasa material..., Moh Azhar, FMIPA UI, 2015..
(42) 28. Silikon karbida (SiC), juga dikenal sebagai carborundum , adalah senyawa silikon dan karbon dengan rumus kimia SiC. Hal ini terjadi di alam sebagai Moissanite mineral sangat langka. Butir-butir SiC dapat terikat bersama oleh sintering untuk membentuk keramik sangat keras yang banyak digunakan dalam aplikasi yang memerlukan daya tahan tinggi, seperti rem mobil, kopling mobil dan piring keramik di rompi anti peluru . SiC dengan luas permukaan yang tinggi dapat dihasilkan dari SiO2 yang terkandung di bahan sekam padi (X. Zhang, H. Wang, M. Kassem, J. Narayan, C.C. Koch, J. Mater, 2001). SiC berguna untuk struktur material pada suhu tinggi, karena kekerasan yang tinggi, ketahanan oksidasi yang tinggi, juga baik terhadap resistensi thermal kejut. Produksi keramik kepadatan tinggi oleh sintering solid state sulit karena sifat kovalen yang kuat dari Si - C obligasi. Sintering solid state SiC dapat dilakukan pada suhu tinggi hingga 2200 0C. Karena kelangkaan Moissanite alami, SiC biasanya buatan manusia yang paling sering digunakan sebagai abrasif, dan baru-baru ini sebagai semikonduktor dan berlian tiruan kualitas permata. Proses manufaktur yang paling sederhana adalah untuk menggabungkan pasir silika dan karbon di Acheson grafit tungku listrik pada suhu tinggi, antara 1600 dan 2500 0C (T.D. Shen, C.C. Koch, Acta Mater, 1996). Partikel SiO2 baik dalam bahan tanaman (misalnya sekam padi) dapat dikonversi ke SiC dengan pemanasan dalam kelebihan karbon dari bahan organik. Bahan sekelas ini yang sangat dianjurkan dalam aplikasi yang melibatkan lingkungan yang sangat agresif memerlukan ketahanan terhadap korosi dan suhu yang tinggi (yaitu lebih dari 900 °C). Selain karena kekerasan tinggi dan modulus elastisitas yang relatif tinggi. SiC terdepan di antara berbagai keramik non-oksida untuk Aplikasi komersial, SiC umumnya diproduksi dalam skala besar baik untuk digunakan sebagai abrasif atau sebagai keramik kinerja tinggi untuk aplikasi semikonduktor. Serbuk SiC dapat diproduksi dalam tiga cara utama yaitu pirolisis senyawa silan, karbonisasi langsung logam Si, dan pengurangan carbothermal SiO2. Metode pertama , yang disebut Deposisi uap kimia dari silan, mahal dan berbahaya bagi sifat prekursor digunakan, sementara karbonisasi yang menggunakan logam Si sangat tinggi biaya sumber silikon. Kedua metode. Universitas Indonesia Rekayasa material..., Moh Azhar, FMIPA UI, 2015..
(43) 29. menghasilkan kemurnian tinggi SiC bubuk untuk aplikasi teknis tertentu dan digunakan untuk bahan komposit ( yaitu Carbon Serat ) infiltrasi. Metode ketiga adalah yang termurah, mulai dari yang murah silikon dioksida dan karbon (atau sumber karbon ) yang biasanya bereaksi pada suhu berkisar antara 1400-2100 0C untuk memberikan SiC. Hadirnya oksigen dalam inti elemen bertanggung jawab untuk puncak intens SiC selama pembentukan. Sekali lagi ukuran kristal meningkat dengan peningkatan Suhu terutama karena aglomerasi. Analisis fasa SiC telah dihasilkan dari sekam padi. Angka-angka di bawah ini merupakan hasil uji SiC dengan XRD sebagaimana ditampilkan pada Gambar 2.15. Dalam pola SiC semua puncaknya tajam, yakni mewakili SiC dalam bentuk kristal dan ukuran kristal telah dihitung dengan bantuan modifikasi Rumus Scherrer dan ukuran kristal ditemukan pada kisaran 118 nm – 50 nm. Selama tahap analisis, ditemukan bahwa semua puncak tajam adalah SiC (Rosario Madrid, C. A. Nogueira and F. Margarido, 2012). Gambar 2.15 Pola XRD SiC dari Sekam Padi (Rosario Madrid, C. A. Nogueira and F. Margarido, 2012). Universitas Indonesia Rekayasa material..., Moh Azhar, FMIPA UI, 2015..
(44) 30. 2.4. Batu Apung (BA) atau Pumice Batu apung atau pumice telah digunakan selama berabad-abad oleh manusia. Agregat batu apung dapat ditemukan di banyak tempat di seluruh dunia di mana gunung berapi berada. Dewasa ini batu apung sebagai agregat telah banyak digunakan dan dikembangkan sebagai salah satu bahan dasar pembuatan beton ringan, dikarenakan sifatnya yang tangguh dan memiliki daya tahan yang baik sampai dengan 2000 tahun. Oleh sebab itulah agregat batu apung digunakan secara meluas dalam industri sipil sebagai materi konstruksi bangunan. Peningkatan pemanfaatan bahan ringan dalam aplikasi struktur bangunan sipil yang menyebabkan batu apung menjadi sangat populer untuk bahan baku batu bata ringan. Kemampuan batu apung salah satunya adalah dibuat produk yang berbeda-beda baik berdasarkan sifat fisik, kimia dan sifat mekanik. Batu apung yang digunakan sebagai agregat ringan alami ini memiliki porositas tinggi dan bobot bulk density yang rendah, sehingga diaplikasikan dalam produksi beton kekuatan rendah seperti batu-bata untuk tujuan tertentu. Karakteristik LWC secara umum tergantung kepada kadar air agregat sebelum pencampuran. Kandungan air yang berlebihan menyebabkan kurangnya daya rekat antara agregat dan mortar, Sebaliknya kandungan air kurang menyebabkan agregat menyerap sebagian dari air mortar, sehingga menyebabkan semen sub-hidrasi dan konskwensinya perubahan kapasitas dari adukan beton. Kedua kasus diatas. mengakibatkan sifat ketahanannya rendah dibandingkan. ketika agregat direndam yang cukup sesaat sebelum persiapan adukan beton. Agregat pumice yang akan digunakan harusnya direndam dalam air selama 30 menit sebelum dicampur sehingga agregat pumice tidak menyerap air lagi pada saat dicampur (Gunduz, 2005). Agregat batu apung yang dikombinasikan dengan Portland semen dan air menghasilkan LWC tahan panas, kedap suara, dan tahan api untuk dek atap, sebagai pengisi lantai ringan, isolasi dek lantai struktural, tirai sistem dinding, blok agregat batu apung dan beragam. aplikasi lain untuk isolasi permanen. (Brown dan Skinner, 1990; Failla dkk, 1997; Neville, 1996). Pada batu apung blok beton ringan atau Pumice Lightweight Concrete Block (PLWCB) yang dibuat dari campuran agregat batu apung, semen dan air telah diaplikasikan dalam. Universitas Indonesia Rekayasa material..., Moh Azhar, FMIPA UI, 2015..
(45) 31. konstruksi non-beban dinding pengisi bantalan dan lempengan. Penggunaan PLWCB pada sebuah struktur bangunan telah terbukti mungarangi beban mati pada setruktur bangunan tersebut, dan dalam proses produksinya kepadatan atau densitasnya dapat dibuat antara 400 kg/m3 sampai 1300 kg/m3. Pada penelitian yang dilakukan oleh Hanifi Binici (2007) untuk mempelajari tentang penggunaan limbah industri keramik dan agregat batu apung untuk LWC dilihat dari sifat kekuatan tekannya. Pada penelitian ini digunakan Portland cemen ASTM Type I (PC 42,5 MPa), agregat dari batu kali yang kering dan bersih dengan ukuran maksimum 16 mm, crushed ceramic (CC) dari limbah industri, dan crused basaltic pumice (CBP). Sifat kimia dan fisik material yang digunakan dalam penelitian ini ditampilkan pada Tabel 2.7.. Tabel 2.7. Sifat kimia dan fisik material yang digunakan pada LWC (Hanifi Binici, 2007). Materials. Pc 42,5 CC CBP Specific Gravity (kg/m3). 3180. Oxides (%) SiO2. Al2O3. Fe2O3. CaO. MgO. SO3. LOI. 19,4 88,4 63,9. 5,5 7,3 15,6. 3,9 0,5 6,3. 63,4 0,1 2,3. 1,8 0,1 2,1. 2,0 3,2. 0,4 1,6. Specific surface (m3/kg). 345. Fineness (retained on 90-μm sieve). 8,2. Vicat time of setting (min). Compressive strength (MPa). Initial Final 3day 7day 28day 115. 200 34,2 37,3 48,6. Terlihat dari Tabel 2.7 diatas bahwa pada material PC 42.5 senyawa yang dominan adalah CaO, sedangkan senyawa SiO2 lebih kecil. Pada material CC dan CBP senyawa yang dominan adalah SiO2 dan Al2O3 dengan jumlah yang tidak besar. Sedangkan Kuat Tekan bertambah besar dengan bertambahnya periode waktu reaksi. Untuk sifat fisik pada batu kali sebagai agregat yang digunakan pada penelitian Hanifi Binici ditampilkan pada Tabel 2.8, sedangkan untuk CC dan CBP ditampilkan pada Tabel 2.9.. Universitas Indonesia Rekayasa material..., Moh Azhar, FMIPA UI, 2015..
(46) 32. Tabel 2.8. sifat fisik dari batu kali sebagai agregat (Hanifi Binici, 2007) Property. Fine aggregate. Coarse aggregate. Specific gravity (kg/m3) Fineness modulus Water absorption 24 h (%) Void (%) Maximum size Bulk density (kg/m3) Abrasion value (%) Soundness test: weight loss after 30 cycles (%). 2,65 2,68 0,75 46,20 4 1695 -. 2,7 1,24 44,25 16 1627 26 7,1. Tabel 2.9. Sifat fisik dari crushed ceramic (CC) dan crused basaltic pumice (CBP) (Hanifi Binici, 2007) Property Specific gravity (kg/m3) Fineness modulus Water absorption 24 h (%) Void (%) Maximum size Bulk density (kg/m3) Abrasion value (%) Soundness test: weight loss after 30 cycles (%). CC. CBP. 2,44 2,68 0,71 44,2 4 1395 28 4,2. 2,71 3,46 0,88 64,2 4 1401 35 7,1. Dari kedua Tabel 2.8 dan Tabel 2.9 diatas memperlihatkan bahwa nilai Specific gravity terkecil didapat dari material CC yaitu sebesar 2,44. kg/m3. kemudian berturut-turut naik nilainya untuk batu kali (Fine aggregate sebesar 2,65 kg/m3 dan Coarse aggregate 2,7 kg/m3) serta yang paling besar adalah material CBP sebesar 2,71 kg/m3. Sedangkan Fineness modulus pada. Fine. aggregate dan material CC memiliki nilai yang sama yaitu sebesar 2,68, nilai terbesar terdapat pada material CBP sebesar 3,46. Dari hasil penelitian Hanifi Binici (2007) didapatkan grafik kekuatan tekan pada beberapa variasi sampel yang digunakan terhadap waktu pengerasan yang ditampilkan pada Gambar 2.16.. Universitas Indonesia Rekayasa material..., Moh Azhar, FMIPA UI, 2015..
(47) 33. Gambar 2.16. Kekuatan tekan pada campuran beton terhadap waktu pengerasan (Hanifi Binici, 2007) Dari Gambar 2.16. pada penelitian ini terlihat bahwa pada sampel M3. dimana kandungan CC (60%) memiliki kekuatan tekan yang paling tinggi (± 55 MPa) dibandingkan dengan sampel M6 (60% CBP) yang hanya memiliki kekuatan tekan ± 37 MPa. Untuk material CBP yang terbesar adalah pada sampel M5 (50% CBP) dengan kekuatan tekan sebesar ± 42 MPa. Sedangkan sampel M0 (0% replacement) memiliki kuat tekan paling kecil yaitu sebesar ± 33 MPa. Penggunaan CBP dalam campuran untuk pembuatan LWC ini perlu dikombinasikan lagi, baik peningkatan persentase CBP maupun dengan kombinasi jenis agregat yang lain, sehingga nilai kekuatan tekannya dapat lebih meningkat (Hanifi Binici, 2007). Uma Ramasamy dan Paul Tikalsky (2012) dalam laporan penelitian menjelaskan bahwa bahan semen lengkap adalah bahan yang menyediakan bahan mikro-substrat atau memiliki efek katalitik untuk bahan semen lainnya. Batu apung dapat dikarakterisasi dengan menganalisis sifat kimia dan fisika, kinetika hidrasi dan sifat beton campuran yang mengandung batu apung. Lima kombinasi campuran beton dengan batu apung dicampur dengan Tipe II / V diperiksa. Campuran kontrol dengan 100% semen, tiga campuran dengan 20% semen digantikan oleh DS200, DS325 dan Ultrafine dan ketika campuran 30% maka simbolnya adalah DS325. Universitas Indonesia Rekayasa material..., Moh Azhar, FMIPA UI, 2015..
(48) 34. Uma Ramasamy dan Paul Tikalsky juga melaporkan bahwa batu apung memiliki kandungan mineral yang berbeda di dalam setiap campuran yang dibuat. Hasil difraksi sinar X menginformasikan bahwa batu apung merupakan jenis amorf yang memiliki kualitas berbeda dengan semen murni. Sementara dari uji fluoresensi sinar X (XRF), komposisi kimiawi dari batu apung dan semen bervariasi bergantung pada kualitasnya. Tabel 2.10 adalah tabel komposisi kimiawi dari berbagai tipe campuran batu apung dan semen. Analisis kimia menunjukkan bahwa komponen dominan dari batu apung adalah silika (70%) sedangkan semen memiliki kalsium oksida (62%). ASTM C 618 mengklasifikasikan batu apung sebagai pozzolan Kelas N (untuk pozzolan alam mentah atau dikalsinasi) jika memenuhi persyaratan fisik dan kimia tertentu. Kelas N pozzolan harus memiliki minimal SiO2 + Al2O3 + Fe2O3 isi 70%, batu apung memiliki sekitar 80% dari bahan-bahan tersebut. Kehadiran senyawa mengandung silika dan alumina jelas dari bahan kimia. Berdasarkan hasil analisis kimia tersebut jelas bahwa semua nilai dari batu apung yang terdiri dari kurang lebih sama persentase elemen hanya berbeda dalam ukuran partikel, yang dapat disimpulkan dari analisis distribusi ukuran partikel dan pemindaian mikroskop elektron. Dari Tabel 2.10, dapat disimpulkan bahwa batu apung memiliki silika yang sangat tinggi, kalsium sangat rendah, alumina dan alkali lebih tinggi dibandingkan dengan jenis semen II. Tabel 2.10. Hasil uji XRF dari berbagai tipe campuran batu apung dan semen (Uma Ramasamy dan Paul Tikalsky, 2012) Type II. DS200. DS325. Ultrafine. SiO2. 20.67. 69.09. 69.16. 69.75. Al2O3. 3.97. 10.63. 10.79. 11.18. Fe2O3. 3.65. 1.01. 1. 1.04. CaO MgO. 63.57 1.55. 0.93 0.09. 0.93 0.16. 0.97 0.25. SO3. 2.81. -0.04. -0.04. -0.04. Na2O. 0.06. 2.49. 2.13. 2.34. K2O. 0.72. 4.77. 5.08. 4.79. Cl Total. 0.018 98.43. Nil 89.12. Nil 89.33. Nil 90.42 Universitas Indonesia. Rekayasa material..., Moh Azhar, FMIPA UI, 2015..
Gambar

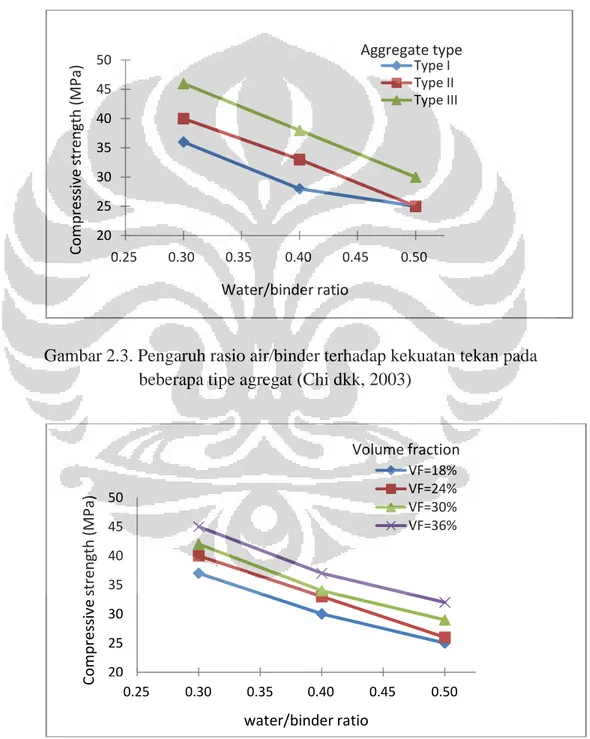


Dokumen terkait
Rincian ini digunakan untuk mendapatkan keterangan mengenai pengeluaran makanan dan minuman yang dikeluarkan khusus untuk unit institusi pemerintah dalam pelaksanaan
Menurut Peraturan Pemerintah Republik Indonesia Nomor 55 tahun 2005 menyatakan bahwa dana alokasi khusus adalah adalah dana yang bersumber dari pendapatan APBN
Tujuan skripsi ini adalah menerapakan teori himpunan fuzzy dan teori grup pada subgrup multi anti fuzzy.. Kata Kunci : grup, subgrup, Subgrup multi
Selain itu keempat algoritma yaitu: algoritma penentuan bobot awal, algoritma pelatihan dengan umpan maju (feedforward), algoritma perambatan mundur dari
Penelitian yang digunakan jenis penelitian kuantitatif yaitu memberikan suatu gambaran mengenai pengaruh penggantian agregat kasar (kerikil) menggunakan terak dengan
11 Sirozi menyebut bahwa berbagai persoalan pendidikan yang ada di berbagai negara berkembang, termasuk di Indonesia, tidak mungkin dapat dipahami jika hanya
Russell Ackoff memaparkan mengenai keterkaitan data, informasi, dan pengetahuan dengan menjelaskan bahwa kandungan dalam pikiran manusia dapat diklasifikasikan dalam lima
Yang erat dengan fungsi pengawasan adalah fungsi interpretasi. Media massa tidak hanya menyajikan fakta dan data, tetapi juga informasi serta interpretasi mengenai suatu