A project dissertation submitted to the Chemical Engineering Program Universiti Teknologi PETRONAS in partial fulfillment of the requirement for the. Bubble bursting is a process where bubble rises to a liquid surface and breaks bubble film and experiences liquid jet. Invisible to the naked eye, these two events produce droplets known as film droplets and jet droplets.
Realizing the importance of bubble bursting phenomenon, this project aims to capture the bubble bursting mechanisms by using CFD and to study the effect of surface tension and initial bubble diameter on bubble bursting mechanism. However, in terms of film and jet droplet formation, this simulation shows no droplet formation from the bursting bubble, which means that no conclusion can be drawn to directly relate surface tension and initial bubble diameter to droplet formation.
INTRODUCTION
- Background of Study
- Problem Statements
- Objectives
- Scope of Study
The bursting of bubbles can also be seen as a mechanism for the release of sea salt particles to the surface of the ocean [7]. Many studies have been done to study the bubble burst phenomenon to get a clearer view of the related process industries or natural phenomenon. In this project, the bubble burst phenomenon will be modeled using the selected CFD package, FLUENT 12.0, to provide important findings on the bubble burst phenomenon mechanisms and the effects of key parameters on bubble burst.
To simulate bubble bursting mechanisms in a predefined state according to existing experimental studies using CFD. In addition, this paper is expected to also examine the effects of two key parameters on the bubble burst.
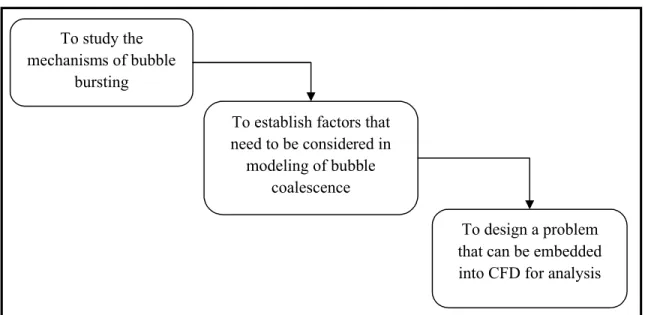
LITERATURE REVIEW
Validation Papers
Also in this study, high-speed video demonstrates that the bubble cap bursts from a single point, regardless of bubble size. Experiments by Guézennec and his colleagues also showed that the size of the jet droplet represents 10 to 18% of the size of the parent bubble. In this experiment, film droplet projections could not be observed in the images due to the limitation of the image resolution of the high-speed video.
Zhijun Han and Lauri Holappa also set up an experimental model to investigate the main factors affecting bubble bursting on their paper entitled "Bubble Bursting Phenomenon in Gas/Metal/Slag Systems" [2], where in the paper they observed the bubble bursting phenomenon at the interface of slag/iron systems using the X-ray transmission techniques and they studied the effects of bubble diameter and surface tension for two cases; bubble bursting on the free surface of molten iron and bubble bursting towards the slag/iron interface. They found that the mechanisms of bubble bursting are very similar to air/water system and two groups of droplets are found in the experiment;. The fine droplets formed by bubble film capping break at the iron melting surface and the larger droplets are formed from jet produced by collapsing the remaining bubble cavity.
Han and Haloppa also showed the relationship between bubble size and surface tension on the formation of droplets by bursting the bubble (see Figure 2.4 and Figure 2.5). In part of their experiment, Sugimoto and Higayashima briefly explained the production of jet droplets without an electric field. Sugimoto and Higayashima [9] had also researched the production of water droplets due to cracks or air bubbles eating the surface of the water under a positive DC electric field.
In part of their experiment, Sugimoto and Higayashima briefly explained the formation of jet droplets without an electric field, which is similar to other examples of bubble bursts. In part of their experiment, Sugimoto and Higajashima briefly explained the formation of the jet, which is similar to other examples of bubble bursts. There are many more articles and journals that mainly discuss the bubble burst phenomenon either experimentally or numerically.
![Figure 2.2 Jet drops formation from vertical liquid jet [8]](https://thumb-ap.123doks.com/thumbv2/azpdforg/10256761.0/15.918.345.648.224.467/figure-jet-drops-formation-from-vertical-liquid-jet.webp)
Other Experimental Studies
Generally, three papers discussed above are the mother paper or the validation paper used by this study.
Comparisons between experimental and numerical studies
METHODOLOGY
- Final Year Project Methodology
- Final Year Project Gantt Chart
- Final Year Project Research Methodology
- Tools and Equipment
- CFD Problem Solving using FLUENT
- Fluid Movement Governing Equation : Navier Stokes Equation
- Interface Tracking Method : Volume of Fluid (VOF)
- Validation Case I: Bubble bursting phenomenon in Gas/Metal/Slag systems
- Experimental and Simulation Setup
- Geometry of Computational Domain
- Model and Numerical Background
- Validation Case II: Dust formation in Electric Arc Furnace
- Experimental and Simulation Setup
- Geometry and Grid
- Model and Numerical Background
- Validation Case III: Production of Water Drops and Corona due to Rupture of
- Experimental and Simulation Setup
- Model and Numerical Background
Validation case I: The phenomenon of bubble bursting in gas/slag/metal systems by Zhijun Han and Lauri Holappa. Where ρ is the fluid density, V is the fluid velocity vector, τij is the viscous stress tensor, p is the pressure, F is the body force, e is the internal energy, Q is the heat source term, t is the time, φ is the dissipation term, and ∇. q is the heat loss by conduction. It belongs to the class of Eulerian methods characterized by a mesh that is either stationary and moves in some prescribed way to accommodate the evolving shape of the interface.
When a particle is a given phase, it does not change the phase; like a particle of air, it is a part of air bubble in water, remains air particle, regardless of the bubble movement. Since dimensions of the crucible are given in the experimental data, the only thing that needs to be calculated is the height of iron melt in the crucible. The solver was set to be in Pressure Based, as momentum and pressure would be the primary variables.
This simulation is set to cover the bubble burst phenomenon for approx. 0.01 real seconds, since the bubble bursting phenomenon is a very fast process, as the splitting of the bubble cap is expected to be about 0.05 real seconds [16]. Their obvious difference is in terms of the dimensions of the crucible and the size of the parent bubble. The difference between this case and the previous case is mainly on the dimensions of the equipment and the initial size of the bubble.
This crucible has an inner diameter of 45 mm and a height of 70 mm, and the geometry of the crucible is redrawn as shown in Figure 3.8. In Case III [9], the study refers to the phenomenon of bubble bursting on a water surface under a positive DC electric field. This part was chosen as a validation example to compare with the simulation results.
Relative to the bubble diameter of 2.8 mm, the size of the water vessel is considered large, and reconstructing the large domain in the simulator will require high computational costs and longer time to solve. The model and numerical background for Validation Case III will be similar to Case I and Case III.
![Figure 3.4 Averaging volume compared with bubble/drop volume[15].](https://thumb-ap.123doks.com/thumbv2/azpdforg/10256761.0/26.918.220.703.117.370/figure-averaging-volume-compared-with-bubble-drop-volume.webp)
RESULTS AND DISCUSSIONS
Bubble Bursting Phenomenon
- Bubble Film Breakage
- Liquid Jet Production
- Comparison with Literature Review
In the equilibrium position, the bubble can remain stationary for some time while the liquid film is discharged until the film reaches its critical thickness. The equilibrium position of the bubble in the atmosphere was studied by Georgescu. During the equilibrium position, there is a liquid. It can be seen above that there is one breakout point on the bubble cap, just in the center of the cap at 0.10025.
The equilibrium position of the bubble in the atmosphere was studied by Georgescu During its equilibrium position, the liquid film drains and the film eventually becomes thin. It can be observed above that a breakpoint exists in the bubble cap, the center of the cap is 0.10025s. That is, the bubble rests on the surface, draining its liquid layer to its critical thickness, and begins to burst 0.25.
Since the bubble is in its equilibrium position, it can rest for a period of time while the liquid film is drained until the film reaches its critical thickness before bursting. It can be seen above that one fracture point exists on the bubble cap, the bubble rests on the surface, with a thickness of 1, and begins to burst 0.25 ms after the bubble reaches the surface. From this point, the hole widens or is known as the breakup of bubble c into fine droplets or film droplets, until the film disappeared.
From this point, the hole expands or can be known as the disintegration of the bubble cap into fine points or film points, until the film disappeared. This result may be due to the coarse mesh or the bubble diameter is larger than the critical bubble diameter in the iron/argon system which is yet to be determined. Once the bubble reaches the surface, the bubble cap disappears, leaving a bubble cavity that tends to close and produce liquid flow.
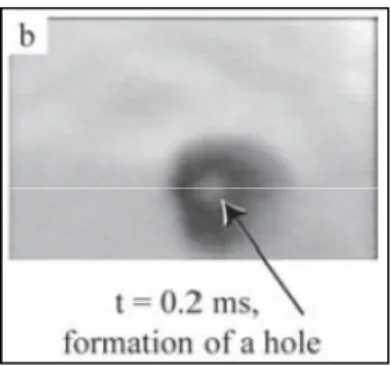
Effect of Initial Bubble Diameter to Bubble Bursting
Since jet droplet ejection depends on the size of the parent bubble, results without jet drops may be due to a coarse mesh or large bubble size. We can see that the path taken by the bubble to rise and reach the surface is the same. Figures 4.9, 4.10, and 4.11 show the position and time at which each bubble reaches the surface, the bubble cap disappears completely, and the liquid jet production is at its maximum.
Location and time of each bubble reaching the surface, bubble cap disappearing completely and highest liquid jet. From Figure 4.9, a bubble with a diameter of 11.5 mm reaches the surface before the smallest one, and this indicates that a larger bubble rises faster than a small bubble. Scale factor, derived by Collins[18], depends on the range of the ratio of bubble diameter to column diameter.
In Figure 4.10, a bubble with a diameter of 9.3 mm takes 9 ms for its film to completely disappear. The height of the liquid jet depends on the surface area of the bubble cavity rather than the larger surface area of the bubble cavity. Since no droplet can be found in both cases, a direct relationship between bubble size and droplet formation cannot be concluded. The bubble phenomenon captured by FLUENT 12.0 in this study is similar compared to the results collected from existing experimental data.
Simulation on bubble bursting was done to see the relationship between bubble bursting phenomenon with bubble diameter and surface tension. Generally, it can be seen that bubble bursting phenomenon consists of series of main events which are the formation of one single hole on bubble film, bubble film rupture and liquid jet production. All these events can be captured using FLUENT 12.0 and agree with literature review.
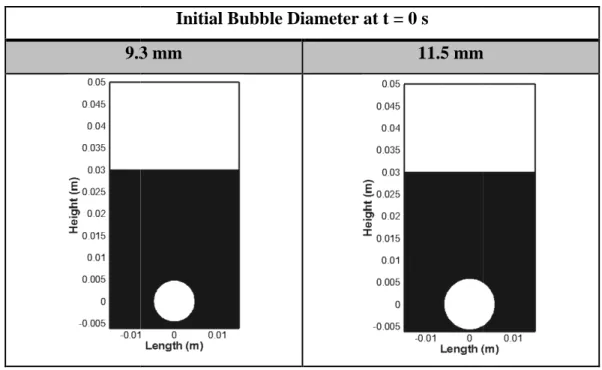