DESIGN AND BUILD IRONERS WITH CAD/CAM TOPSOLID7 ASSISTANCE TO MAKE 20 MILLIMETER CALIBER BALL ETUS. The research steps are: (1) literature and field study (2) measurement of the cup result from the deep drawing process and available press tools (3) design of ironing dies (4) drawing of ironing dies with TopSolid7 (5) production of iron dies (6) measuring the ironing dies, is the result of the manufacturing process.
Latar Belakang
Salah satu metode yang dapat digunakan untuk membantu merencanakan desain die besi dan merencanakan proses pembuatan die adalah melalui perangkat lunak computer aided design (CAD) dan computer aided manufacturing (CAM). Dari proses perancangan dengan menggunakan software CAD/CAM akan dihasilkan G-code yang dapat digunakan untuk proses pembuatan benda kerja yang dirancang dengan bantuan computer numerik control (CNC).

Rumusan Masalah
Tujuan
Batasan Masalah
Manfaat Penelitian
KAJIAN PUSTAKA & DASAR TEORI
Kajian Pustaka
Dasar Teori
- Ironing
- Thickness Reduction Ratio
- Gaya Ironing
- Dies
- Punch
- Spesifikasi Bahan CuZn30
- CAD dan CAM
- Proses Pemesinan
Semakin tebal benda kerja yang akan dikerjakan maka semakin tebal pula die block yang digunakan. Parameter lain yang digunakan dalam proses pemboran seperti feed rate dapat dilihat dari tabel rekomendasi Ulrich Fischer sebagai berikut.
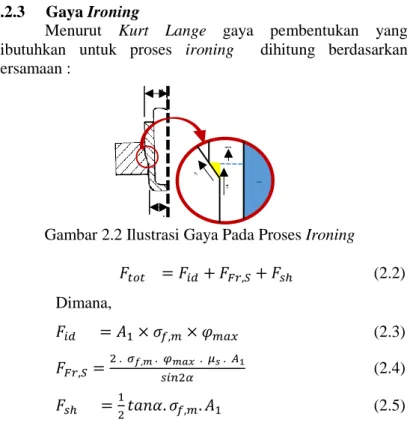
METODOLOGI PENELITIAN
Diagram Alir Penelitian
Langkah – langkah Penelitian
- Studi Literatur dan Studi Lapangan
- Pengukuran Cup Hasil Deep Drawing dan Press
- Pembuatan Dies Ironing
- Pengukuran Dies Ironing Hasil dari Proses
- Kesimpulan dan Saran
Hasil perhitungan tebal dinding cup pada proses penyetrikaan tahap 1 menunjukkan bahwa tebal dinding cup setelah proses penyetrikaan tahap 1 (𝑡1) adalah 3,33 mm, sehingga diameter luar cup setelah penyetrikaan tahap 1 (𝐷𝑙1) adalah 37,86 . Ketebalan dinding cup diperoleh dari hasil perhitungan ketebalan dinding cup pada proses penyetrikaan pada langkah ke 4. Dari hasil tersebut dapat dihitung berapa tegangan yang diterima material benda kerja pada tahap 1 proses penyetrikaan.
Dari perbandingan ini, dapat disimpulkan bahwa bahan kosong Cuzn30 tidak retak selama langkah 1 dari proses penyetrika. Dari hasil ini, jumlah tegangan yang diterima oleh bahan kosong pada langkah 2 dari proses penyetrika dapat dihitung. Dari ini Hasilnya, besarnya tegangan yang diterima material benda kerja dihitung pada langkah ke 3 proses penyetrikaan.
Dari hasil tersebut dapat dihitung besarnya tegangan yang diterima material benda kerja pada proses penyetrikaan tahap 4.

PERANCANGAN DIES IRONING
Perancangan Proses Ironing
- Ketebalan Dinding Cup Hasil Proses Ironing
- Ketinggian Dinding Cup Hasil Proses Ironing
Dari bahan baku yang berbentuk cup dilakukan proses penyetrikaan tahap 1, hasil proses penyetrikaan tahap 1 kemudian diolah menjadi penyetrikaan tahap 2 dan seterusnya hingga diperoleh hasil penyetrikaan tahap 4. Dari empat tahapan proses penyetrikaan, ukuran cetakan yang digunakan berbeda-beda pada setiap tahapannya tergantung hasil perhitungan. Pada Gambar 4.1 (a), cawan yang dibuat pada proses penyetrikaan mempunyai diameter luar 40,2 mm, diameter dalam 31,2 mm, tebal dinding cawan 4,5 mm, dan tinggi cawan 4,5 mm.
Dengan menggunakan cawan yang mempunyai diameter luar awal (𝐷𝑙0) 40,2 mm, diameter dalam (𝐷𝑑0) 31,2 mm, tebal awal (𝑡0) = 4,5 mm, dan tinggi cawan 26,61 mm, maka tebal dinding cawan adalah Hasil dari proses penyetrikaan dijelaskan sebagai berikut. Dari perhitungan tebal dinding cup pada saat proses penyetrikaan tahap 2 diperoleh tebal dinding cup setelah proses penyetrikaan tahap 2 adalah (𝑡2) 2,46 mm, jadi diameter luar cup setelah penyetrikaan tahap 2 adalah (𝐷𝑙2) 36 ,12 mm. Dari hasil perhitungan tebal dinding cup pada saat proses penyetrikaan tahap 3 diperoleh tebal dinding cup setelah proses penyetrikaan tahap 3 (𝑡3) adalah 1,82 mm, jadi diameter luar cup setelah penyetrikaan tahap 3 (𝐷𝑙3) adalah 34,84 mm.
Pada metode volume konstan, volume awal cangkir sebelum proses dianggap sama dengan volume akhir cangkir setelah proses penyetrikaan.

Dimensi Dies dan Punch Ironing
- Dimensi Dies Ironing
- Dimensi Punch Ironing
Agar proses penyetrikaan dapat menghasilkan benda kerja yang baik maka panjang pukulan juga harus diperhatikan. Untuk menentukan panjang maksimum punch yang sesuai digunakan pada proses penyetrikaan yang direncanakan, digunakan perhitungan sebagai berikut.
Gaya pada Proses Ironing
- Gaya Ironing
- Gaya Buckling pada Punch
Pada proses pengolahan setrika tahap pertama, bagian depan setrika dijaga jaraknya 2 mm dari bagian depan bahan baku. Pada penyetrikaan benda kerja tahap 1, jenis mesin yang akan digunakan adalah CNC Turning 2 Axis, dan pada software TopSolid 7 konfigurasi mesin yang digunakan adalah NC Machine Turning (XZ/C). Proses yang dilakukan untuk pembuatan stamping 1 terbagi menjadi 2 proses operasional yaitu depan dan belakang.
Pada proses pemesinan die ironing tahap pertama, parameter yang digunakan ditunjukkan pada tabel sebagai berikut. Pada penyetrikaan cetakan tahap 1, jalur pahat yang dibuat didasarkan pada rencana proses yang dirancang pada subbab sebelumnya. Sedangkan mesin bubut 2 sumbu dengan kontrol Siemens Sinumerik 840D digunakan untuk proses produksi die ironing tahap 1.
Hal ini ditunjukkan dengan kesesuaian dimensi desain dengan dimensi blanko besi cor yang diproduksi.

PEMBUATAN DIES IRONING
Rancangan Dies Ironing
- Penggambaran Dies Ironing Dengan Software
- Penambahan Stock Pada TopSolid 7
Dimana setiap tahapan proses hanya menggunakan 1 jenis cetakan saja, sehingga setiap pergantian tahapan proses dilakukan dengan mengganti penyetrikaan cetakan yang digunakan. Penyetrikaan die yang dilakukan selama proses produksi adalah penyetrikaan die tahap 1, sedangkan gambar desain penyetrikaan die ironing tahap 2, 3 dan 4 terlampir pada Lampiran A. Penyetrikaan die ironing tahap 1 mempunyai diameter lubang die sebesar 37,91 mm. , tinggi cetakan 30,88 mm dan lebar dinding cetakan 25,20 mm.
Desain besi die tahap 1 memiliki lubang umpan benda kerja dengan diameter 40,20 mm dan menggunakan sudut kemiringan die 10°. Sebelum merencanakan proses pemesinan dengan computer-aided machining (CAM) TopSolid 7, bahan baku atau stock terlebih dahulu ditambahkan pada gambar 3D yang dibuat. Produksi besi tahap 1 menggunakan bahan baku berbentuk silinder dengan diameter 102 mm dan panjang 55 mm.
Setelah memasukkan ukuran bahan baku yang digunakan, posisi benda kerja pada bahan baku disesuaikan.
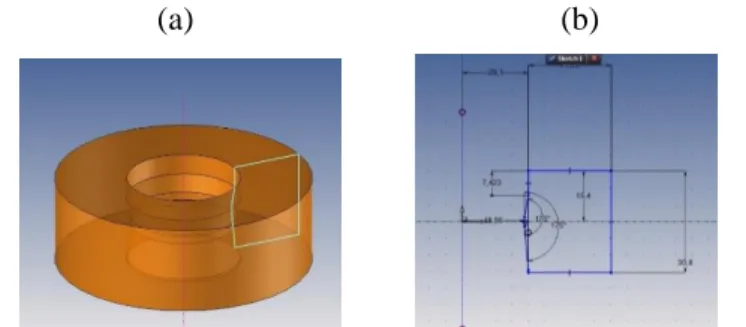
Rencana Proses Pemesinan Dies Ironing
- Rencana Proses Pemesinan
- Parameter Pemotongan
Untuk proses roughing kedalaman umpan yang digunakan adalah 0,5 mm dan untuk proses finishing adalah 0,3 mm. Pada proses pengeboran tengah, diameter bor adalah 5 mm, sehingga umpan yang disarankan adalah 0,08 mm/rev. Dengan menggunakan CNC Milling, pendekatan proses yang digunakan adalah proses pengeboran, sehingga parameter proses yang digunakan adalah parameter proses pengeboran.
Sedangkan pada proses pocket Ø14 dengan pahat end mill Ø8 dilakukan penyesuaian parameter yang digunakan yaitu kecepatan potong 100 m/menit, pemakanan 0,5 mm, kedalaman potong 0,02 mm dan putaran pahat 1500 rpm. Pada penelitian ini mesin CNC Turning yang digunakan mempunyai kecepatan putaran spindel maksimal 3500 rpm. Sedangkan pada saat melakukan proses pengeboran, putaran poros yang digunakan adalah konstan sehingga tabel rekomendasi seperti pada Gambar 5.7 diatas digunakan untuk menghitung putaran poros sebagai berikut.
TIDAK. Proses Mesin yang digunakan Alat potong Bahan Vc (m/mnt) N (rpm) F (mm/rev) Kedalaman potong (mm) Nomor pahat.

Pembuatan Toolpath
Jalur pahat dibuat sesuai rencana proses yang dirancang yaitu pada sisi depan, diawali dengan proses planing sedalam 2 mm, kemudian diselesaikan bidang planingnya. Proses dilanjutkan dengan roughing untuk memperkecil diameter bahan baku. Pengerasan seadanya dilakukan dengan batas 31 mm dari acuan awal yaitu muka cetakan yang dirancang. Saat membuat jalur pahat, waktu pemesinan yang dihasilkan juga ditampilkan; setiap proses menghasilkan waktu pemrosesan yang berbeda-beda.
Setelah lintasan pahat depan selesai dilakukan, hasil proses diverifikasi menggunakan menu verifikasi pada software TopSolid 7. Pada Gambar 5.9 (b), warna hijau menunjukkan bahwa benda kerja yang dihasilkan mempunyai dimensi ±0,1 mm dari desain yang diinginkan. Pada proses pemesinan die ironing tahap 1 belakang, alur pahat belakang diawali dengan menghadap, kemudian dilakukan finishing menghadap, kemudian dilanjutkan dengan pembubutan internal dan finishing.
Pada proses pembuatan hole holder, setting mesin yang digunakan diubah menjadi NC Machine Milling (XYZ).
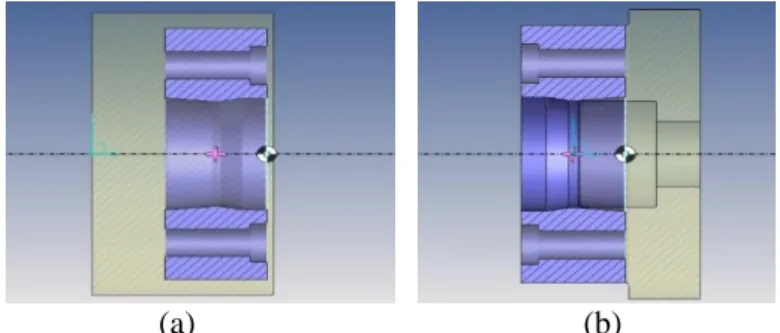
Pembuatan G – Code
Pada proses bubut, untuk mencapai kecepatan potong yang konstan sesuai dengan diameter yang dikerjakan, maka putaran spindel diubah sesuai dengan perubahan diameter selama proses pemotongan. Pada kode G yang dihasilkan oleh post processor milling 3 sumbu Fanuc, putaran spindel yang dihasilkan adalah konstan. Pada G – code hasil post processor milling 3 sumbu Fanuc terdapat perintah untuk kompensasi ketinggian pahat yaitu kode.
Dalam kode G yang dihasilkan oleh pasca-prosesor penggilingan 3-sumbu Fanuc, perintah siklus pengeboran "G81" digunakan. G - Kode yang dihasilkan oleh post-processor milling 3-sumbu Fanuc memiliki koordinat dimana nilai sumbu X menunjukkan radius benda kerja. G - Kode yang dihasilkan terlampir pada Lampiran B. Proses pembuatan lubang dudukan dilakukan dengan mesin milling CNC 3 sumbu dengan kontrol fanuc.
CAE Teknik Mesin ITS, sehingga tidak perlu melakukan penyesuaian terhadap hasil G-code yang didapat dari software.

Pembuatan Komponen
Anda menentukan titik acuan ini dengan menyentuhkan alat pemotong yang ingin Anda gunakan dalam proses pemesinan ke benda kerja. Pada mesin bubut CNC, ketika pahat pemotong sedikit menyentuh bagian depan benda kerja, koordinat yang terlihat pada mesin dimasukkan ke dalam pengontrol mesin sebagai acuan benda kerja. Komponen dibuat dengan menjalankan program G-Code yang dihasilkan. Sebelumnya program G-Code dipisahkan untuk setiap proses menjadi file NC yang berbeda. Pada saat pembuatan komponen, setiap proses mempunyai waktu pengerjaan yang berbeda-beda.

Pengukuran Hasil
Data pengukuran menunjukkan kepatuhan terhadap toleransi yang dibuat selama proses verifikasi proses CAM dengan perangkat lunak TopSolid7. Iron die untuk produksi selongsong kaliber 20 mm dirancang dalam 4 tahap, dengan dimensi sebagai berikut. Perlu dilakukan pengujian langsung pada proses penyetrikaan untuk mengetahui apakah desain die yang dirancang mampu mengolah bahan baku cup dan menghasilkan cup dengan dimensi sesuai desain.
Untuk pemanfaatannya dalam dunia industri perlu dikaji penggunaan progressive dies untuk proses penyetrikaan pada pembuatan selongsong peluru. Kemudian penulis melanjutkan pendidikan tinggi di D3 Teknik Mesin Institut Teknologi Sepuluh Nopember. Penulis mengambil jurusan manufaktur. Kemudian penulis melanjutkan pendidikan tingginya di Teknik Mesin Institut Teknologi Sepuluh Nopember tahap Strata I.
Selama menempuh studi S1 di Teknik Mesin Institut Teknologi Sepuluh Nopember, penulis menjadi anggota aktif di Laboratorium Perancangan dan Pengembangan Produk.

PENUTUP
Kesimpulan
Proses yang dilakukan terdiri dari menggambar gambar 3D, menambahkan bahan baku (stok), menentukan referensi, membuat toolpath, memverifikasi dan membuat G-Code. Proses pemesinan yang dirancang dengan software TopSolid7 sesuai dengan proses pemesinan yang dilakukan pada mesin CNC.
Saran
Dibandingkan dengan kuat tarik ultimit material benda kerja yaitu CuZn30 yaitu sebesar 339 MPa, maka beban yang diterima material pada proses penyetrikaan tahap 1 lebih kecil dibandingkan dengan kuat tarik ultimit material benda kerja. Dibandingkan dengan kuat tarik ultimit material benda kerja yaitu CuZn30 yaitu sebesar 339 MPa, maka tegangan yang diterima material pada proses penyetrikaan tahap ke 2 lebih kecil dibandingkan dengan kuat tarik ultimit material benda kerja. Dari perbandingan tersebut dapat disimpulkan bahwa material benda kerja CuZn30 tidak sobek pada proses penyetrikaan tahap ke-2.
Dibandingkan dengan kuat tarik ultimit bahan blanko yaitu CuZn30 yaitu sebesar 339 MPa, maka tegangan yang diterima material pada proses penyetrikaan tahap 3 lebih kecil dibandingkan dengan kuat tarik ultimit bahan blanko. Dibandingkan dengan kuat tarik ultimit bahan blanko yaitu CuZn30 yaitu sebesar 339 MPa, maka tegangan yang diterima material pada proses penyetrikaan tahap 4 lebih kecil dibandingkan dengan kuat tarik ultimit bahan blanko. Dari perbandingan tersebut dapat disimpulkan bahwa bahan blanko CuZn30 tidak robek pada proses penyetrikaan tahap ke-4.
