METAL MATRIX
ASH MENGGU
Sk Sy
DE
UNIV
RIX COMPOSITE ALUMINIUM –PAL
GGUNAKAN METODE CETRIFUGAL
SKRIPSI
Skripsi Yang Diajukan Untuk Melengkapi Syarat Memperoleh Gelar Sarjana Teknik
DISUSUN OLEH :
CHANDRA ANDRIKA 100401025
DEPARTEMEN TEKNIK MESIN
FAKULTAS TEKNIK
IVERSITAS SUMATERA UTARA
MEDAN
2015
ALM OIL FLY
AL CASTING
METAL
MATRIX
COMPOSITEALAMINIUM
_PALM OIL
FLY
ASH ME NGGUNAKAN METODE,
CE TRI FUGAL CASTING
CHANDRA ANDRIKA
100401025
Telah Diperbaiki/Diperiksa dari Ilasil Seminar Skripsi
Periode Ke824, Pada Tanggal30 September 2015
Telah dise ujui oleh
Pembi bing
Ir. Tugiman. MT.
METAL
fufr4TRIX COMPOSTTEALUMINIUM
-PALM
OTLFLY
ASH ME
N GGUNAKAITMBTODE.
CE TRIFUGAL
CASTING
CHANDRA ANDRIKA
10040102s
Telah DiperbaikilDiperiksa dari Hasil Seminar Skripsi
Periode Ke824, Pada Tanggal30 September 2015
Penguji
II
ffilus*r
Suprianto. ST.MT
NIP. 197909082008 121001
METAL
MATMX
COMPOSITE
AL(|MINIL\M
-PALh{
OIL
FLl'
J
Sff M
EN
GG(iN""lfi
{I/
1\{ ETO DE
C E TRI F U GAL -CA^9Ili\rG
CHANDRA ANDRIKA NrM.1fi)40102s
Diketahui / Disahkan :
Departemen Teknik Mesin
Fakultas teknikusu
Ketua,
Disetujui Oleh: Dosen Pembimbing,
Lr
Ir. Tusiman MT.
Fl-rP. 19570412 I 98503 1004
,1,
KANDIDAT I
NamaA.IIM
'Iugas Sarjana
Judul Tugas Sarjana
Dosea Peifibitnbirrg
Dosen Pembandirrg
#Av,
iA
zuwlD*-
ffi
Wtffi:,tu-ffi
Penilaian Terhada.p seminar slaipsi.Mahasiswa tersebut adalah :
i,CATATAN HA;SIL SEMINAR.
1. Judul
2. Sistematika
3. Bahasp/'Iulisan
4. Materi yang dikoreksi
-
lolw,bn
drlrqt-:
flor'[rt]6;r'."""
"'
:Wd'^yfu
5,Gambar
_
C,rq*_II.SETELAH SE}'dINAR DIDISIKUSIKAN DAN EVALUASI ANTARA DoSEN PEMBA}IDING
DAN DOSEN IPEMBIMBINCi, MAKA HASILSEMINAR ADALA}I :
1,
Dapat langsung mengikuti Sidang Slcipsi.(Zleenu
perba:ikarr sebagian catetan semmar dan akan dibimbiagoleh Dosen pembanding sebelum
\-/
Sidang Skripsi,
3'
Periu perbajrkan yang menrlasar dan akan dibimbing oleh Dosen Pembandinl; setelah terlebihdahulu melnlui bimbingan ulan6; dari Dosen pembimbing.
illM*i
/ Perlu Per.baikan *)lvlemenuhi / .Ps*l*+sbaikan *)
lv[ememr:hii Perlu Perbaikan *)
Mean;/E?&llr
Teknik Mesin,
hfii,,{fwt?t:
/i or^h )trar.1sr y1' .
:,k
tfitr.*r.il/,(.
KANDIDAT:
NamaNIM Tugas Sarjana Judul T\rgas Sa{an*
Dosea Peiribimbing
Dqsen Pembandirrg
2.
Sistematika
: Vflemenuhi / Ferlu Per.baikan *) 3.Bahasa/'Iutrisan
; lv[emenuhi / Perlu Perbaikan *)4' Materi vang
dlkoreksi
,
.,,..[*l*
..Lil-.llu..n
,2,.[tth/-lxlri:fltr*
;
t,,,
&. or+*,/:?ri/r4.-I
. . Sp?lt
[,
H}l|Jl.,'4*.'.
llq
5,Gambar
II.SETELAH SE}yIINAR DIDISIKUSIKAN DAN EVALUASI ANTARA DOSEN PEMBANDING
DAN DOSEN IPEMBIMBING, MAKA FI,ASILSEMINAR ADALAH :
1.
Dapat langsung mengikuti Sidang Skripsi.4@
Perlu perba:lkan sebagian catatan seminar dan akan dibimbing oleh Dosen Pembanding sebelum Sidang Skripsi.Perlu perbaikan yang msnJasar dan akan dibimbing oleh Dosen Pemban{in1; setelah terlebih
dalrulu melalui bimbingan ulang dari Dosen Pe,mbimbing.
J.
D'sen*{Lr'*'
l,rrfrZ,nr.
Teknik Mesin,
0l
d.,t
a
h,lr;4"
/
n
dyo,/osy
ftT:
Penilaian Terhadap Seminar Slaipsi,Mahasiswa tersebut adalah :
DEPARTEMEN
TEKNIK
MESIN FT
USUPERIODE
HAWTANGGAL
NAIvIA NIM
:824
: Rabu / 30 September 2015
: Chandra Andrika
: 100401025
NO NAMA MAIIASISWA / NIM TANDA TANGAN
\y
fu%
MaLrr
,&Uu\
ff+rr &r{,
f
voaowgc
'fl.!!#
Lv
4.,*"
\Aox
fuionj
q,,,+
3y
B tUa
ft(hrlontca@-4-u
l-tercLV
9uuan&z^
F?+
Iv
\^
uun,nL A+vrarf
Meflan, 30 September 201 5
r"dr\u Seminar,
V,r
Ir. Tugiman. MTNAMA
NIM
MATA PELAJARAN
SPESIFIKASI
DIBERIKAN TANGGAL
SELESAI TANGGAL
KETUA
DEPARTEMEN TEKNIK MESIN,
TUGAS SARJANA
: CHANDRA ANDRIKA : 100401025
: PENGECORAN LOGAM
: Lakukan studi eksperimental untuk menganalisa pengaruh heat treatment terbadap sifat mekanis dan
mikrostruktur pada pembuatan metal matrix
c o mp o s i t e menggunakan metode c e nt r ifu ga I c a s t ing.
Untuk itu :
1.
Sebelurnnya lakukan pengujian komposisi rawMaterial, kekerasan, impak, mikrostruktur, SEM
dan EDS sebelum dilakukannya heat treatment
2.
Lakukan pengujian heat trealment dengan standarT6
3.
Lakukan
pengujian kekerasan,impak
danmikrostruktur setelah di heat treatment
15 Juli 2015
18 September 2015
MEDAN, 15 Juli 2015.
Dos$l.r PEMBTMBTNG,
n
W,/
Ir.
Tusiman MT.KARTTT BIMBINGAN
TT'GAS
SARJANA MAHASISWA
No:2260lTSl2Al5
Sub. Program Studi tsidang Tugas Judul Tugas
Diberikan tanggal Dosen Pembimbing
Proses Produksi Pengecoran Logam
ANALISA PE\GARTH HEAT TREATMENT TERTL{DAP
STFAT }IE II{]{IK DAN }IIKROSTRUKTUR }LdTERIAL METAL MATRD( COMPOSNE ALL'YD|IL'IT _PALM OIL
FLY ASH
MENGGL1\:4K4.\'}IETODE
CETRIFL'GALCASTIA'G
: 15 Juli20l5
:Ir.Tugimman,MT
Selesai
Tgl
: l8Sept 2015Nama
Mhs
; Chandra AndrikaNIM
. 100401025No Tanggal Kegiatan Asistensi Bimbingan Tanda Tangan
Dosen^Pembimbins
l5-07-201s Menerima Spesifi kasi Tugas
w-47-2015 Studi Literatur dan Pencarian Referensi
i;
)-l-07-2ats Asistensi Bab I dan Bab II
(Yl"
z
4 27-07-2015 Asistensi Perbaikan Bab I dan Bab
il
I I5 13-08-201s Asistensi Bab
Ill
) l4-08-201 s Asistensi Perbaikan Bab III
t-7 19-08-201 5 Hasil Pengujian Impak, kekerasan, SEM dan
EDS sebelum di ,rctlution treiltment
tr
8 2 I -08-2015 Hasil Pengujian lrnpak, kekerasan dan
mikrostruktur setelah di solution treatment
,:p
) 24-08-20 5 Asistensi Bab IV
l0 t-08-20 5 Asistensi Perbaikan Bab IV
I
il
07-09-20 5 Asistensi Bab V dan Daftar Pustakat7 0-09-20 5 Asistensi perbaikan Bab V dan Daftar Pustaka
l-r'/
t3 8-09-20 5 Asistensi keseluruhan dan ACC Seminar It
CATATAN:
l. Kartu ini harus diperlihatkan kepada Dosen Pembrmbing setiap Asistensi 2. Kartu ini harus dijaga bersih dan rapi
3. Kartu ini harus dikembalikan ke Departemen, bila kegiatan Asistensi
Telah selesai.
KETTJA
Diketahui,
ABSTRAK
Perkembangan teknologi saat ini diharapkan menggunakan kekayaan alam dengan hemat tetapi tetap dapat menghasilkan sebuah produk dengan kualitas baik. Salah satu teknologi pembentukan logam yang dikembangkan saat ini yaitu metal matrix
composite. Metal matrix composite ini merupakan kombinasi antara logam
sebagai penyusun utama ( matrix ) dengan material lainnya sebagai penguat. Penelitian ini bertujuan untuk menganalisis pengaruh penambahan palm oil fly ash dengan variasi persentase berat 2,5%, 5%, 7,5%, 10% dan 12,5% dan serta pengaruh heat treatment T6 terhadap sifat mekanik dan mikrostrukturnya. Metode pengecoran yang digunakan adalah metode centrifugal casting yang mana pada metode ini aluminium cair dituangkan kedalam cetakan bersamaan dengan penambahan palm oil fly ash kemudian diputar sampai aluminium tersebut membeku didalam cetakan. Hasil penelitian menunjukkan penambahan palm oil
fly ash dan perlakuan heat treatment T6 dapat meningkatkan nilai kekerasan
namun menurunkan nilai impak. Nilai kekerasan meningkat sebesar 93%, nilai kekerasan tertinggi didapat pada penambahan palm oil fly ash 7,5% pada kondisi
as-cast dan heat treatment T6 yaitu 58,434 BHN kondisi as-cast dan 112,618
BHN pada kondisi setelah heat treatment T6. Untuk nilai impak tertinggi didapat pada raw material yaitu sebesar 0,241 joule/mm2 dan nilai impak terendah diperoleh pada penambahan palm oil fly ash 12,5% yaitu sebesar 0,206 joule/mm2 pada kondisi as-cast dan 0,202 joule/mm2 pada kondisi heat treatment T6. Hasil mikrostruktur menunjukkan terjadinya perubahan bentuk butiran dan distribusi persipitat yang merata pada matrix aluminium setelah dilakukannya heat
treatment T6. Hasil pengujian Scanning Electron Microscope (SEM) menunjukkan terbentuknya morfologi chinese script. Hasil pengujian Electron
Dispersive Spectroscopy EDS menunjukan bahwasannya unsur Si merupakan
unsur terbanyak di dalam palm oil fly ash dibandingkan unsur lainnya dimana Si yang terkandung didalam metal matrix composite aluminum - palm oil fly ash dengan persentase berat 41,35 % pada penembakan spektrum 1 dan 28,77 % pada penembakan 2.
ABSTRACT
The current technological developments are expected to use natural resources sparingly but still able to produce a product with good quality. One of the metal forming technology developed in this time is MMC. Metal Matrix composite is a combination of metal as the main constituent (matrix) with other materials as reinforcement. This study aimed to analyze the effect of palm oil fly ash content with a variation of 2.5%, 5%, 7.5%, 10% and 12.5%, and the effect of T6 heat treatment on mechanical properties and microstructure of Al-POFA. Casting method used is the centrifugal casting method in which this method molten aluminum is poured into the mold simultaneously with the addition of palm oil fly ash is then rotated until the aluminum solidifies in the mold. The results showed the addition of palm oil fly ash and treatment T6 heat treatment can increase the hardness but lower the impact value. The hardness value increased by 93%, the highest hardness value obtained on the addition of palm oil fly ash 7.5% in the as-cast condition and the T6 heat treatment is 58.434 BHN as-as-cast condition and 112.618 BHN condition after T6 heat treatment. The highest value obtained for the impact on the raw material that is equal to 0.241 joules / mm2 and low impact value obtainable on the addition of palm oil fly ash of 12.5% in the amount of 0.206 joules / mm2 in the as-cast condition and 0.202 joules / mm2 on condition T6 heat treatment. Results showed microstructural changes granules and equitable distribution of precipitates in the aluminum matrix, subsequent to T6 heat treatment. Hasil pengujian Scanning Electron Microscope (SEM) menunjukkan terbentuknya morfologi chinese script. The test results showed EDS Electron Dispersive Spectroscopy bahwasannya Si element is the highest element in the palm oil fly ash than other elements where Si is contained within the metal matrix composite aluminum - palm oil fly ash with heavy percentage of 41.35% in the shooting spectrum of 1 and 28, 77% in the second shooting.
KATA PENGANTAR
Puji syukur kehadirat Allah SWT, Tuhan semesta alam. Tiada daya dan kekuatan selain dari-Nya. Shalawat dan salam kepada Rasulullah Muhammad SAW. Alhamdulillah, atas izin-Nya penulis dapat menyelesaikan skripsi ini.
Skripsi ini adalah salah satu syarat untuk dapat lulus menjadi Sarjana Teknik di Departemen Teknik Mesin, Fakultas Teknik, Universitas Sumatera Utara. Adapun judul skripsi yang dipilih diambil dari mata kuliah Pengecoran Logam, yaitu “ANALISA PENGARUH HEAT TREATMENT TERHADAP SIFAT MEKANIK DAN MIKROSTRUKTUR MATERIAL METAL
MATRIX COMPOSITE ALUMINIUM – PALM OIL FLY ASH
MENGGUNAKAN METODE CETRIFUGAL CASTING”.
Dalam penulisan skripsi ini, penulis banyak mendapatkan bantuan, motivasi, pengetahuan, dan lain-lain dalam penyelesaian skripsi ini.Penulis telah berupaya dengan segala kemampuan pembahasan dan penyajian, baik dengan disiplin ilmu yang diperoleh dari perkuliahan, menggunakan literatur, serta bimbingan dan arahan dari Bapak Ir. Tugiman, MT sebagai Dosen Pembimbing.
Pada kesempatan ini, penulis tidak lupa menyampaikan terima kasih yang sebesar-besarnya kepada:
1. Kedua orang tua tercinta, Ayahanda Marwanto, dan Ibunda Tumirah atas doa, kasih sayang, pengorbanan, tanggung jawab yang selalu menyertai penulis, dan memberikan penulis semangat yang luar biasa sehingga penulis dapat menyelesaikan skripsi ini.
2. Bapak Ir. Tugiman, MT sebagai Dosen Pembimbing Skripsi yang banyak memberi arahan, bimbingan, motivasi, nasehat, dan pelajaran yang sangat berharga selama proses penyelesaian Skripsi ini.
3. Bapak Suprianto, ST. MT yang banyak memberi arahan, bimbingan, motivasi, nasehat, dan pelajaran yang sangat berharga selama proses penyelesaian Skripsi ini.
5. Seluruh Staf Pengajar DTM FT USU yang telah memberikan bekal pengetahuan kepada penulis hingga akhir studi selesai, dan seluruh pegawai administrasi DTM FT USU, juga kepada staf Fakultas Teknik.
6. Teman satu tim (Nursuci Adek, Rama Sanjaya, Abdul Rahman dan Aji Fajar Prastia) yang telah memberikan kesempatan kepada penulis untuk bergabung dalam penyelesaian tugas sarjana ini.
7. Teman-teman seperjuangan Teknik Mesin stambuk 2010 yang banyak memberi motivasi kepada penulis dalam menyusun skripsi ini.
Semoga skripsi ini bermanfaat bagi kita semua dan dapat digunakan sebagai pengembangan ilmu yang didapat selama dibangku kuliah. Apabila terdapat kesalahan dalam penyusunan serta bahasa yang tidak tepat dalam skripsi ini sebagai manusia yang tak luput dari kesalahan penulis mengharapkan masukan dan kritikan yang bersifat membangun dalam penyempurnaan skripsi ini. Akhir kata penulis mengucapkan terima kasih, semoga skripsi ini dapat bermanfaat bagi seluruh kalangan yang membacanya. Amin Ya Rabbal Alamin.
Medan, Oktober 2015 Penulis,
DAFTAR ISI
KATA PENGANTAR ... i
DAFTAR ISI... iii
DAFTAR TABEL ... vi
DAFTAR GAMBAR ... vii
DAFTAR NOTASI... x
BAB I PENDAHULUAN... 1
1.1 Latar Belakang ... 1
1.2 Perumusan Masalah ... 3
1.3 Tujuan Penelitian ... 4
1.3.1 Tujuan Umum ... 4
1.3.2 Tujuan Khusus ... 4
1.4 Batasan Masalah... 4
1.5 Manfaat ... 5
1.6 Metode Penelitian... 5
BAB II TINJAUAN PUSTAKA... 7
2.1 Aluminium ... 7
2.1.1 Sejarah Aluminium ... 7
2.1.2 Kandungan Atom/Unsur dan Ikatan ... 9
2.1.3 Mikrostruktur Aluminium... 9
2.1.4 Sifat-Sifat Aluminium... 10
2.2 Paduan Aluminium ... 12
2.2.1 Paduan Al-Si ... 13
2.2.2 Paduan Al-Cu dan Al-Cu-Mg ... 14
2.2.3 Paduan Al-Mn ... 14
2.2.4 Paduan Al-Mg ... 14
2.2.5 Paduan Al-Mg-Si ... 14
2.3 Magnesium... 15
2.4 Fly Ash ... 16
2.4.1 Fly Ash Batubara ... 16
2.4.1.1 Sifat Kimia dan Sifat Fisika Fly Ash Batubara ... 17
2.4.2 Palm Oil Fly Ash (POFA) ... 18
2.5 Komposit Matrik Logam (Metal Matrix Composite)... 19
2.6 Proses Pengecoran Logam ... 20
2.6.1 Centrifugal Casting... 21
2.6.2 Jenis–Jenis Pengecoran Sentrifugal ... 22
2.7 Heat Treatment ... 24
2.8 Pengujian Komposisi Kimia ... 29
2.9 Pengujian Kekerasan... 30
2.10 Uji Mikrostruktur ... 31
2.11 Pengujian SEM (Scanning Electron Microscope) ... 32
2.12 Pengujian EDS (Electron Dispersive Spectroscopy) ... 33
BAB III METODOLOGI PENELITIAN ... 35
3.1 Tempat dan Waktu ... 35
3.2 Bahan, Peralatan dan Metode... 36
3.2.1 Bahan ... 36
3.2.2 Peralatan ... 39
3.3 Metode ... 44
3.3.1 Karakteristik Awal Bahan ... 44
3.3.2 Proses Pembuatan MMC dan Spesimen ... 44
3.3.3 Perlakuan Panas Metal Matrix Composite ... 46
3.4 Metode pengujian ... 47
3.4.1 Uji Kekerasan... 47
3.4.2 Uji Mikrostruktur (Metallograpy) ... 48
3.4.3 Pengujian Impak... 48
3.4.4 Pengujian SEM (Scanning Electron Microscope) dan Pengujian EDS (Electron Dispersive Spectroscopy) ... 49
3.5 Diagram Alir Penelitian ... 50
4.1 Hasil Pengujian ... 53
4.1.1 Hasil Pengujian Kekerasan Metal Matrix Composite Al-Pofa ... 53
4.1.2 Hasil Pengujian Impak ... 56
4.1.3 Hasil Pengujian Foto Mikrostruktur Metal Matrix Composite Al-Pofa... 61
4.1.4 Hasil Pengujian SEM ... 64
4.1.5 Hasil Pengujian EDS (Electron Dispersive Spectroscopy) ... 65
4.2 Hasil Pembuatan Spesimen dari Hasil Pengecoran... 67
BAB V Kesimpulan dan Saran ... 68
5.1 Kesimpulan ... 68
5.2 Saran... 69
DARTAR PUSTAKA ... 70
DAFTAR TABEL
Tabel 2.1 Sifat-sifat fisik Aluminium... 12
Tabel 2.2 Paduan Al untuk Produk Wrought ... 12
Tabel 2.3 Komposisi Kimia Salah Satu Jenis Abu Terbang Batubara ... 17
Tabel 2.4 Penandaan Temper Pengerasan Penuaan Paduan Allumunium .... 25
Tabel 2.6 Sifat-sifat dari logam ... 30
Tabel 3.1 Tempat dan waktu penelitian ... 35
Tabel 3.2 Komposisi Aluminium A356 ... 36
Tabel 3.3 Chemical composition of Palm Oil Fly Ash ... 37
Tabel 3.4 Spesifikasi Mesin Ion Sputter JFC-1600... 50
Tabel 4.1 Hasil uji kekerasan Aluminium-Palm oil fly ash (as-cast) ... 54
Tabel 4.2 Hasil uji kekeraan Aluminium-Palm oil fly ash (heat treatment) ... 54
Tabel 4.3 Hasil pengujian impak sampel as-cast ... 57
Tabel 4.4 Hasil pengujian impak sampel heat treatment T6 ... 58
Tabel 4.5 Kandungan unsur metal matrix composit al-pofa penembakan 1 ... 67
DAFTAR GAMBAR
Gambar 2.1 Bauksit ... 9
Gambar 2.2 Struktur mikro dari aluminium murni... 9
Gambar 2.3 Struktur mikro dari paduan Aluminium-Silikon ... 10
Gambar 2.4 Diagram fasa Al-Si ... 13
Gambar 2.5 Diagram Alir Palm Oil Fly Ash ... 18
Gambar 2.6 (a) Abu Terbang (Palm Oil Fly Ash) ... 18
Gambar 2.6 (b) Bottom ash sesudah di grinding ... 18
Gambar 2.7 Penguat dalam material komposit ... 20
Gambar 2.8 Proses pengecoran sentrifugal sejati... 22
Gambar 2.9 Pengecoran semi sentritugal ... 23
Gambar 2.10 Pengecoran sentrifuge... 24
Gambar 2.11 Skema pengujian brinell ... 31
Gambar 2.12 Strukturmikro paduan Al-Si ... 31
Gambar 2.13 Mekanisme SEM (Scanning Electron Microscope) ... 33
Gambar 2.14 Teknik EDS (Proses Kontras Hasil EDS)... 34
Gambar 2.15 Contoh dari aplikasi EDS ... 34
Gambar 3.1 Aluminium seri A356 ... 36
Gambar 3.2 Magnesium ... 36
Gambar 3.3 Palm oil fly ash ... 37
Gambar 3.4 Cover fluks ... 38
Gambar 3.5 Arang kayu laut... 38
Gambar 3.6 Dapur peleburan... 39
Gambar 3.7 krusibel ... 40
Gambar 3.8 Centrifugal casting ... 40
Gambar 3.9 Furnace chamber... 41
Gambar 3.10 Microskop optic ... 41
Gambar 3.11 Hardness tester ... 42
Gambar 3.12 termokopel ... 42
Gambar 3.13 Impact tester ... 43
Gambar 3.15 Pengujian Kekerasan ... 47
Gambar 3.16 Pengujian foto mikrostruktur... 48
Gambar 3.17 Pengujian impak ... 49
Gambar 3.18 Mesin Ion Sputter JFC-1600... 50
Gambar 3.19 Mesin SEM JEOL JSM-6390A ... 51
Gambar 3.20 Diagram alir penelitian ... 52
Gambar 4.1 Grafik hubungan persentase berat palm oil fly ash terhadap nilai kekerasan ... 55
Gambar 4.2 (a) sebelum heat treatment ... 56
Gambar 4.2 (b) sesudah heat treatment... 56
Gambar 4.3 Grafik hubungan persentase berat palm oil fly ash terhadap energi yang diserap ... 59
Gambar 4.4 Grafik hubungan persentase berati palm oil fly ash terhadap nilai impak ... 60
Gambar 4.5 (a) Sampel Raw material as-cast ... 61
Gambar 4.5 (b) Sampel Raw material heat treatment T6... 61
Gambar 4.6 (a) Sampel, 2,5% Pofa as-cast ... 61
Gambar 4.6 (b) Sampel , 2,5% Pofa heat treatment T6 ... 61
Gambar 4.7 (a) Sampel 5% Pofa as-cast ... 62
Gambar 4.7 (b) Sampel 5% Pofa heat treatment T6... 62
Gambar 4.8 (a) Sampel 7,5% Pofa as-cast ... 62
Gambar 4.8 (b) Sampel 7,5% Pofa heat treatment T6 ... 62
Gambar 4.9 (a) Sampel 10% Pofa as-cast ... 62
Gambar 4.9 (b) Sampel 10% Pofa heat treatment T6... 62
Gambar 4.10 (a) Sampel 12,5% Pofa as-cast ... 63
Gambar 4.10 (b) Sampel 12,5% Pofa heat treatment T6 ... 63
Gambar 4.11 Pengujian SEM pada pembesaran 500 kali ... 64
Gambar 4.12 Hasil Pengujian SEM pembesaran 2000 kali... 65
Gambar 4.13 Hasil pengamatan SEM pada MMC Aluminium– Palm oil fly ash pembesaran 500 kali ... 66
Gambar 4.15 Hasil uji EDS metal matrix composit Aluminium–
Palm oil fly ash penembakan 2... 67
Gambar 4.16 Hasil pengecoran Metal matrix composite aluminum–
DAFTAR NOTASI
Simbol Arti Satuan
A Luas Penampang cm2
D Diameter cm
E energi joule
P Beban kgf
ρ massa jenis gr/cm
3
R jari–jari mm
t tinggi mm
ABSTRAK
Perkembangan teknologi saat ini diharapkan menggunakan kekayaan alam dengan hemat tetapi tetap dapat menghasilkan sebuah produk dengan kualitas baik. Salah satu teknologi pembentukan logam yang dikembangkan saat ini yaitu metal matrix
composite. Metal matrix composite ini merupakan kombinasi antara logam
sebagai penyusun utama ( matrix ) dengan material lainnya sebagai penguat. Penelitian ini bertujuan untuk menganalisis pengaruh penambahan palm oil fly ash dengan variasi persentase berat 2,5%, 5%, 7,5%, 10% dan 12,5% dan serta pengaruh heat treatment T6 terhadap sifat mekanik dan mikrostrukturnya. Metode pengecoran yang digunakan adalah metode centrifugal casting yang mana pada metode ini aluminium cair dituangkan kedalam cetakan bersamaan dengan penambahan palm oil fly ash kemudian diputar sampai aluminium tersebut membeku didalam cetakan. Hasil penelitian menunjukkan penambahan palm oil
fly ash dan perlakuan heat treatment T6 dapat meningkatkan nilai kekerasan
namun menurunkan nilai impak. Nilai kekerasan meningkat sebesar 93%, nilai kekerasan tertinggi didapat pada penambahan palm oil fly ash 7,5% pada kondisi
as-cast dan heat treatment T6 yaitu 58,434 BHN kondisi as-cast dan 112,618
BHN pada kondisi setelah heat treatment T6. Untuk nilai impak tertinggi didapat pada raw material yaitu sebesar 0,241 joule/mm2 dan nilai impak terendah diperoleh pada penambahan palm oil fly ash 12,5% yaitu sebesar 0,206 joule/mm2 pada kondisi as-cast dan 0,202 joule/mm2 pada kondisi heat treatment T6. Hasil mikrostruktur menunjukkan terjadinya perubahan bentuk butiran dan distribusi persipitat yang merata pada matrix aluminium setelah dilakukannya heat
treatment T6. Hasil pengujian Scanning Electron Microscope (SEM) menunjukkan terbentuknya morfologi chinese script. Hasil pengujian Electron
Dispersive Spectroscopy EDS menunjukan bahwasannya unsur Si merupakan
unsur terbanyak di dalam palm oil fly ash dibandingkan unsur lainnya dimana Si yang terkandung didalam metal matrix composite aluminum - palm oil fly ash dengan persentase berat 41,35 % pada penembakan spektrum 1 dan 28,77 % pada penembakan 2.
ABSTRACT
The current technological developments are expected to use natural resources sparingly but still able to produce a product with good quality. One of the metal forming technology developed in this time is MMC. Metal Matrix composite is a combination of metal as the main constituent (matrix) with other materials as reinforcement. This study aimed to analyze the effect of palm oil fly ash content with a variation of 2.5%, 5%, 7.5%, 10% and 12.5%, and the effect of T6 heat treatment on mechanical properties and microstructure of Al-POFA. Casting method used is the centrifugal casting method in which this method molten aluminum is poured into the mold simultaneously with the addition of palm oil fly ash is then rotated until the aluminum solidifies in the mold. The results showed the addition of palm oil fly ash and treatment T6 heat treatment can increase the hardness but lower the impact value. The hardness value increased by 93%, the highest hardness value obtained on the addition of palm oil fly ash 7.5% in the as-cast condition and the T6 heat treatment is 58.434 BHN as-as-cast condition and 112.618 BHN condition after T6 heat treatment. The highest value obtained for the impact on the raw material that is equal to 0.241 joules / mm2 and low impact value obtainable on the addition of palm oil fly ash of 12.5% in the amount of 0.206 joules / mm2 in the as-cast condition and 0.202 joules / mm2 on condition T6 heat treatment. Results showed microstructural changes granules and equitable distribution of precipitates in the aluminum matrix, subsequent to T6 heat treatment. Hasil pengujian Scanning Electron Microscope (SEM) menunjukkan terbentuknya morfologi chinese script. The test results showed EDS Electron Dispersive Spectroscopy bahwasannya Si element is the highest element in the palm oil fly ash than other elements where Si is contained within the metal matrix composite aluminum - palm oil fly ash with heavy percentage of 41.35% in the shooting spectrum of 1 and 28, 77% in the second shooting.
BAB I
PENDAHULUAN
1.1 Latar Belakang
Kemajuan teknologi dan ilmu pengetahuan saat ini semakin pesat, hal ini sejalan dengan kemajuan industri yang semakin banyak dan kompleks. Perkembangan teknologi saat ini diharapkan menggunakan kekayaan alam dengan hemat tetapi tetap dapat menghasilkan sebuah produk dengan kualitas baik. Baik buruknya kualitas produk salah satunya ditentukan oleh material penyusunnya, usaha untuk mendapatkan material yang baik dapat dilakukan dengan cara pengembangan. Di bidang material banyak dilakukan pengembangan-pengembangan untuk mendapatkan material dengan sifat yang diinginkan. Salah satu metode yang dapat digunakan untuk meningkatkan sifat mekanik dari suatu bahan yaitu dengan membentuk material Metal Matrix composite . Material jenis ini merupakan kombinasi antara logam sebagai penyusun utama ( matrix ) dengan material lainnya sebagai penguat. Aluminium merupakan salah satu dari beberapa jenis material yang sering dijadikan bahan utama pembentukan metal matrix
composite hal ini dikarenakan aluminium banyak dipergunakan dalam bidang
keteknikan sebab aluminium memiliki sifat yang ringan dan tahan korosi tetapi aluminium memiliki kelemahan yaknik kekerasan yang rendah sehingga tidak tahan terhadap gesekan (Yasman,F.2014)
Aluminium yang dikenal sebagai logam yang memiliki tahan korosi, sifat ringan, penghantar listrik yang baik digunakan sebagai matriks sedangkan palm oil fly ash berfungsi sebagai penguat. Penggunaan palm oil fly ash sebagai penguat untuk menghasilkan aluminium komposit dengan sifat mekanik yang baik dan biaya murah yang dapat bersaing dengan komposit sejenis lainnya
Metal matrix composite adalah material yang terdiri dari gabungan dua
continuous dan penguat dengan fasa discontinuous. Terdapat 5 faktor umum dari
penguat yang mempengaruhi sifat dari material komposit yaitu konsentrasi, ukuran, bentuk, distribusi, dan orientasi. Metal Matrix Composite rmemiliki keunggulan dibandingkan dengan logam tunggalnya karena Metal Matrix
Composite dapat memiliki sifat yang diinginkan, seperti peningkatan kekuatan
dengan berat yang lebih rendah.
Perlakuan panas merupakan salah satu cara yang dapat dilakukan untuk merubah fasa bahan komposit sehingga dapat menambah kekuatan dari sifat mekanis logam tersebut. Perlakuan panas yang terjadi pada logam dapat mengubah struktur mikro dari logam sehingga akan berpengaruh terhadap sifat mekanisnya. Pada peningkatan sifat mekanik paduan Aluminium A356 dengan heat treatment T6 diperoleh hasil bahwa sifat mekanik paduan naik akibat adanya heat treatment T6, yaitu terjadi perubahan bentuk butiran dari lonjong menjadi bulat, sehingga terjadi kenaikan UTS dan kekerasan yang signifikan (Anzip dkk., 2006). Berdasarkan penelitian yang pemah dilakukan tentang paduan aluminium yaitu Penelitian perlakuan pada alumunium diantaranya Fauad Abdillah (2010). Meneliti alumuinim pada piston bekas Hijet 1000 dengan menambah beberapa fariasi persentase ADC12 yang dicor kembali dipilih perbandingan komposisi matrial piston bekas dengan ADC12 yang paling efisien yaitu 50 % PB dan 50 % kemudian diteruskan dengan perlakuan panas dengan fariasi temperature penungan 7000C, 7500C, 8000C dan temperatur artificial aging 1000C, 1500C, 2000C serta penahanan waktu holding time 2 jam, 4 jam, 5 jam pada proses age hardening setelah mendapat perlakuan panas terjadi peningkatan nilai kekerasan, nilai kekerasan yang paling bagus pada temperatur penuangan 700oC dan temperatur artificial aging 200oC dengan waktu penahanan aging 5 jam , sebesar 80,5 HRB ( Abdillah F., 2010).
jam, 5 jam, 7 jam, dan 10 jam. Hasil dari pengujian kekerasan, kekerasan benda meningkat seiring dengan bertambahnya waktu aging dengan waktu tertentuakan turun kembali jika waktu aging ditambah. Aging dengan temperatur 2000C, memberikan nilai kekerasan yang paling bagus yaitu 71,5 dengan wakrtu aging selama 7 jam.(Paryono dkk, 2011).
Proses heat treatment pada sebuah aluminium umumnya merupakan sebuah perlakuan panas untuk precipitation hardening. Tahapan proses heat
treatment awalnya material dipanaskan dan selanjutnya dilakukan pendinginan
cepat (quenching). Setelah dilakukan quenching, pada struktur aluminium terbentuk Super Saturated Solid Solution (SSSS). Setelah itu proses berlanjut dengan penuaan (aging), yaitu pemberian panas yang tidak terlalu tinggi yang berguna untuk membuat SSSS semakin mengeras dan membentuk presipitat yang tujuannya menghalangi dislokasi. Dengan terhambatnya dislokasi, maka kekerasan dari aluminium akan semakin meningkat (Callister, 2007).
Berdasarkan penelitian – penelitian diatas sudah terdapat beberapa penelitian tentang bagaimana heat treatment terhadap material MMC khususnya aluminium paduan. Maka, tujuan dari penelitian ini adalah menganalisa pengaruh laju pendinginan pada proses solution treatment terhadap kekerasan dan mikrostruktur material metal matrik composite berbahan aluminium sebagai matrik dan Palm Oil Fly Ash sebagai penguatnya.
1.2 Perumusan Masalah
Terdapat beberapa cara untuk meningkatkan sifat mekanik paduan metal
matrix composite salah satunya adalah Heat Treatment yang bertujuan melarutkan
1.3 Tujuan Penelitian
1.3.1 Tujuan Umum
Penelitian ini dilakukan untuk membuat metal matrix composite dari bahan coran aluminium tipe A356 yang diperkuat palm oil fly ash dengan metode
centrifugal casting dan meningkatkan sifat mekanik metal matrix composite aluminium–palm oil fly ash dengan menggunakan metode heat treatment.
1.3.2 Tujuan Khusus
Secara terperinci , penelitian ini memiliki tujuan khusus yang terdiri atas beberapa poin yaitu :
1. Mengetahui proses heat treatment pada material metal matriks composite aluminium - palm oil fly ash.
2. Mengetahui pengaruh heat treatment terhadap sifat mekanik material metal
matriks composite aluminium-palm oil fly ash.
3. Mengetahui pengaruh heat treatment terhadap mikrostruktur dari material
metal matrix composite aluminium–palm oil fly ash.
1.4 Batasan Masalah
Adapun penelitian ini dibatasi oleh beberapa hal yaitu sebagai berikut :
1. Bahan yang digunakan adalah aluminium A 356 dalam bentuk ingot sebagai matrik, dan palm oil fly ash sebagai penguat. Bahan di cor menggunakan metode centrifugal casting dengan menvariasikan penambahan persentase berat palm oil fly ash yaitu 2.5, 5%, 7.5%, 10%, dan 12.5%. proses pengecoran dilakukan di laboratorium Foundy Departemen Teknik Mesin Universitas Sumatera Utara.
2. Proses perlakuan panas (heat treatment) yang dilakukan adalah heat treatment T6 dengan temperatur 540oC dengan holding time 4 jam, quenching selama 20 detik dan artificial aging dengan temperatur 155oC holding time 2 jam. Media pendingin yang digunakan adalah air.
1.5 Manfaat
Manfaat penilitian ini:
1. Bagi peneliti dapat menambah pengetahuan, wawasan dan pengalaman tentang metalurgi logam.
2. Bagi akademik, penelitian ini dapat digunakan sebagai referensi tambahan untuk penelitian tentang metal matrix composite.
3. Bagi industri dapat digunakan sebagai acuan atau pedoman dalam pembuatan
bahan metal matrix composite. Dengan memanfaatkan palm oil fly ash sehingga dapat mengurangi biaya produksi sekaligus meningkatkan kualitas produk khususnya sifat mekanisnya.
1.6 Metode Penelitian
Penelitian ini dijadikan dalam bentuk laporan hasil penelitian skripsi yang dibagi atas lima bab, yang masing–masing bab terdiri dari sub bab, yaitu :
Bab 1 : Pendahuluan
Berisi tentang Pendahuluan yang terdiri dari latar belakang, perumusan masalah, tujuan penelitian, batasan masalah, manfaat penelitian dan sistematika penulisan. Bab 2 : Tinjauan Pustaka
Berisi tentang literatur dan referensi yang diperlukan berkenaan dengan bahan aluminium, metal matrix composite, palm oil fly ash, centrifugal casting dan heat
treatment
Bab 3 : Metodologi Penelitian
Berisi tentang urutan dan tata cara yang dilakukan. Dimulai dari waktu dan tempat, persediaan alat bahan, prosedur penelitian dan proses yang dilaksanakan. Bab 4 : Analisa Data dan Pembahasan
Bab 5 : Kesimpulan dan Saran
Berisi tentang penutup yang terdiri dari : kesimpulan dan saran. Dalam bab ini diuraikan tentang kesimpulan yang merupakan resume dari bab - bab sebelumnya. Terutama jawaban atas permasalahan yang diajukan, selanjutnya diberikan saran berkaitan dengan hasil penelitian.
BAB II
TINJAUAN PUSTAKA
2.1 Aluminium
2.1.1 Sejarah Aluminium
Aluminium diambil dari bahasa Latin: alumen, alum. Orang-orang Yunani dan Romawi kuno menggunakan alum sebagai cairan penutup pori-pori dan bahan penajam proses pewarnaan. Tahun 1787, Lavoisier menebak bahwa unsur ini adalah Oksida logam yang belum ditemukan. Pada tahun 1761, de Morveau mengajukan nama alumine untuk basa alum. Pada tahun 1827, Wohler disebut sebagai ilmuwan yang berhasil mengisolasi logam ini. Pada tahun 1807, Davy memberikan untuk menamakan logam ini Aluminum, walau pada akhirnya setuju untuk menggantinya dengan Aluminium. Nama yang terakhir ini sama
dengan nama banyak unsur lainnya yang berakhir dengan “ium”.
C.M. Hall seorang berkebangsaan Amerika bersama Paul Heroult berkebangsaan Prancis, pada tahun 1886 mengolah Alumina menjadi Aluminium dengan cara elektrolisa dari garam yang terfusi. Selain itu Karl Josep Bayer berkebangsaan Jerman yang merupakan seorang ahli kimia mengembangkan proses yang dikenal dengan nama proses Bayer untuk mendapat Aluminium murni.
sehingga oksigen dan Aluminium murni menjadi terpisah. Pada setiap 1 kilogram Aluminium diperlukan 2 kilogram Alumina dan 4 kilogram bauksit, 0,6 kilogram karbon, criolit dan bahan-bahan lainnya. Penggunaan Aluminium saat ini menduduki urutan kedua setelah besi dan baja dan tertinggi pada logam bukan besi untuk kehidupan industri.
Secara historis, Perkembangan proses pengecoran untuk Aluminium dan paduannya merupakan prestasi yang relatif baru. Paduan Aluminium tidak tersedia dalam jumlah yang substansial untuk pengecoran tujuan hingga lama. Setelah penemuan pada tahun 1886 dari proses elektrolitik pengurangan Aluminium oksida oleh Charles Martin Hall di Amerika Serikat dan Paul Heroult di Perancis. Meskipun penemuan Hall menghasilkan Aluminium dengan biaya sangat kecil, nilai penuh dari Aluminium sebagai bahan pengecoran tidak dilanjutkan sampai paduan cocok untuk proses pengecoran yang sedang berkembang. Aluminium dasar paduan secara umum akan ditandai sebagai sistem eutektik yang mengandung bahan intermetalik atau unsur-unsur sebagai fase berlebih. Karena kelarutan relatif rendah sebagian besar elemen paduan dalam Aluminium dan paduan kompleksitas yang dihasilkan dapat berisi beberapa fasa logam, yang terkadang cukup kompleks dalam komposisi. Fasa ini biasanya lebih larut dekat suhu eutektik dari pada suhu kamar, sehingga memungkinkan untuk panas-mengobati beberapa dari paduan oleh solusi dan penuaan panas-perawatan (Purnomo,2004).
Pengecoran Aluminium akan berakibat penurunan sifat mekanis (tarik dan impak) dari logam, yang terjadi akibat peningkatan porositas (Purnomo,2004). Porositas yang terjadi pada saat pengecoran Aluminium dapat dieleminir dengan mengontrol gas/oksigen dan variabel pengecoran lainnya seperti, temperatur, laju pembekuan, laju pendinginan (Melo,M.L.N.M.,etl., 2005) yang dapat dilakukan dengan tersedianya dapur peleburan yang memadai.
2.1.2 Kandungan Atom/Unsur dan Ikatan
Aluminium disimbolkan dengan Al, dengan nomor atom 13 dalam tabel periodik unsur. Bauksit, bahan baku aluminium memiliki kandungan aluminium dalam jumlah yang bervariasi, namun pada umumnya di atas 40% dalam berat. Senyawa aluminium yang terdapat di bauksit diantaranya Al2O3, Al(OH)3, γ
[image:32.595.239.392.229.327.2]-AlO(OH), dan α -AlO(OH). Bauksit dapat dilihat pada gambar 2.1.
Gambar 2.1 Bauksit (Dobrzanski, dkk, 2006)
Isotop aluminium yang terdapat di alam adalah isotop 27Al, dengan persentase sebesar 99,9%. Isotop 26Al juga terdapat di alam meski dalam jumlah yang sangat kecil. Isotop26Al merupakan radioaktif dengan waktu paruh sebesar 720000 tahun. Isotop aluminium yang sudah ditemui saat ini adalah aluminium dengan berat atom relatif antara 23 hingga 30, dengan isotop 27Al merupakan isotop yang paling stabil.
2.1.3 Mikrostruktur Aluminium
[image:32.595.246.384.599.722.2]Gambar 2.2 memperlihatkan struktur mikro aluminium murni. Aluminium murni 100% tidak memiliki kandungan unsur apapun selain aluminium itu sendiri.
Gambar 2.3 Struktur mikro dari paduan aluminium-silikon (Akroma,B.H., 2011)
Gambar 2.3 (a) merupakan paduan Al-Si tanpa perlakuan khusus. Gambar 2.3 (b) merupakan paduan Al-Si dengan perlakuan termal. Gambar 2.3 (c) adalah paduan Al-Si dengan perlakuan termal dan penempaan. Jika diperhatikan bahwa semakin ke kanan, struktur mikro semakin baik (Voort,1984).
2.1.4 Sifat-Sifat Aluminium
Aluminium telah merupakan salah satu logam industri yang paling luas penggunaannya di dunia. Aluminium banyak digunakan di dalam semua sektor utama industri seperti konstruksi, listrik, angkutan, peti kemas dan kemasan, peralatan mekanis serta alat rumah tangga.
Adapun sifat-sifat mekanik Aluminium antara lain sebagai berikut: a. Ringan
Memiliki bobot sekitar 1/3 dari bobot besi dan baja, atau tembaga dan banyak digunakan dalam industri transportasi seperti angkutan udara.
b. Tahan terhadap korosi
c. Kuat
Aluminium memiliki sifat yang kuat terutama bila dipadu dengan logam lain. Digunakan untuk pembuatan komponen yang memerlukan kekuatan tinggi seperti: pesawat terbang, kapal laut, bejana tekan, kendaraan dan lain-lain.
d. Mudah dibentuk
Proses pengerjaan Aluminium mudah dibentuk karena dapat disambung dengan logam/material lainnya dengan pengelasan, brazing, solder, adhesive
bonding, sambungan mekanis, atau dengan teknik penyambungan lainnya.
e. Konduktor listrik
Aluminium dapat menghantarkan arus listrik dua kali lebih besar jika dibandingkan dengan tembaga. Karena Aluminium tidak mahal dan ringan, maka Aluminium sangat baik untuk kabel-kabel listrik overhead maupun bawah tanah
f. Konduktor panas
Sifat ini sangat baik untuk penggunaan pada mesin-mesin/alat-alat pemindah panas sehingga dapat memberikan penghematan energi.
g. Memantulkan sinar dan panas
Aluminium dapat dibuat sedemikian rupa sehingga memiliki kemampuan pantul yang tinggi yaitu sekitar 95% dibandingkan dengan kekuatan pantul sebuah cermin. Sifat pantul ini menjadikan Aluminium sangat baik untuk peralatan penahan radiasi panas.
h. Non magnetik
baik secara satu persatu atau bersama-sam. Penggunaan dari aluminium dan paduannya antara lain untuk peralatan rumah tangga, kemasan makanan dan minuman, pesawat terbang, mobil, kappa laut, konstruksi bangunan rumah, dan lain-lain. Adapun sifat-sifat aluminium murni ditunjukkan pada Tabel 2.1 (Surdia,1992).
Tabel 2.1 Sifat-sifat fisik Aluminium (Surdia dan Shinroku, 1992)
Sifat-sifat Kemurnian Al (%)
99,996 >99,0
Massa jenis (20oC) 2,6989 2,71
Titik Cair 660,2 653-657
Panas Jenis (cal/g.oC)(100oC) 0,2226 0,2297
Hantaran Listrik (%) 64,94 59 (dianil)
Tahanan Listrik Koefisien temperature (/oC)
0,00429 0,0115
Koefisien Pemuaian (20-100oC) 23,86 x 10-6 23,5 x 10-6
Jenis Kristal, konstanta kisi FCC,a = 4,013 A FCC,a = $,04 A
2.2 Paduan Aluminium
Aluminium dipakai sebagai paduan berbagai logam murni, sebab tidak kehilangan sifat ringan dan sifat – sifat mekanisnya dan mampu cornya diperbaiki dengan menambah unsur–unsur lain. Paduan Al diklasifikasikan dalam berbagai standar oleh berbagai Negara di dunia. Saat ini klasifikasi yang sangat tekenal dan sempurna adalah standar Alumunium Association di Amerika yang didasarkan atas dasar standar terdahulu dari Alcoa (Alumunium Company of
America),(Surdia dan Saito, 2005). Sesuai dengan Aluminium Assosiation
paduan Al terdiri-dari produk wrought dan cor, klasifikasi produk Wrought ditunjukan pada Tabel 2.3
Tabel 2.2 Paduan Al Untuk Produk Wrought (ASM Vol. 2, 1992)
Unsur Paduan Utama Seri
Aluminium minimal 99.00% 1xxx
Mangan (Mn) 3xxx
Silikon (Si) 4xxx
Magnesium (Mg) 5xxx
Magnesium dan Silikon 6xxx Seng (Zn)
Unsur Lainnya
7xxx 8xxx 9xxx
Aluminium tempa, seri 1xxx digunakan untuk Aluminium murni. Digit kedua dari seri tersebut menunjukkan komposisi Aluminium dengan limit pengotor alamiahnya, sedangkan dua digit terakhir menunjukkan persentasi minimum dari Aluminium tsb. Digit pertama pada seri 2xxx sampai 7xxx menunjukkan kelompok paduannya berdasarkan unsur yang memiliki persentase komposisi terbesar dalam paduan.Sedangkan paduan Al yang digunakan untuk pengecoran sesuai dengan Aluminium association.
2.2.1 Paduan Al-Si
[image:36.595.222.406.586.733.2]Paduan Al-Si ditemukan oleh A. Pacz tahun 1921. paduan Al-Si yang telah diperlakukan panas dinamakan Silumin. Sifat – sifat silumin sangat diperbaiki oleh perlakuan panas dan sedikit diperbaiki oleh unsur paduan. Paduan Al-Si umumnya dipakai dengan 0,15% – 0,4%Mn dan 0,5 % Mg. Paduan Al-Si yang memerlukan perlakuan panas ditambah dengan Mg juga Cu serta Ni untuk memberikan kekerasan pada saat panas. Bahan paduan ini biasa dipakai untuk torak motor (Surdia dan Saito., 2005).
2.2.2 Paduan Al-Cu dan Al-Cu-Mg
Paduan Al-Cu-Mg adalah paduan yang mengandung 4% Cu dan 0,5% Mg serta dapat mengeras dalam beberapa hari oleh penuaan, dalam temperatur biasa atau natural aging setalah solution heat treatment dan quenching. Studi tentang logam paduan ini telah banyak dilakukan salah satunya adalah Nishimura yang telah berhasil dalam menemukan senyawa terner yang berada dalam keseimbangan dengan Al, yang kemudian dinamakan senyawa S dan T. Ternyata senyawa S (AL2CuMg) mempunyai kemampuan penuaan pada temperatur biasa. Paduan Al-Cu dan Al-Cu-Mg dipakai sebagai bahan dalam industri pesawat terbang (Surdia dan Saito., 2005)
2.2.3 Paduan Al-Mn
Mangan (Mn) adalah unsur yang memperkuat Alumunium tanpa mengurangi ketahanan korosi dan dipakai untuk membuat paduan yang tahan terhadap korosi. Paduan Al-Mn dalam penamaan standar AA adalah paduan Al 3003 dan Al 3004. Komposisi standar dari paduan Al 3003 adalah Al, 1,2 % Mn, sedangkan komposisi standar Al 3004 adalah Al, 1,2 % Mn, 1,0 % Mg. Paduan Al 3003 dan Al 3004 digunakan sebagai paduan tahan korosi tanpa perlakuan panas (Surdia dan Saito,1992).
2.2.4 Paduan Al-Mg
Paduan dengan 2 – 3 % Mg dapat mudah ditempa, dirol dan diekstrusi, paduan Al 5052 adalah paduan yang biasa dipakai sebagai bahan tempaan. Paduan Al 5052 adalah paduan yang paling kuat dalam sistem ini, dipakai setelah dikeraskan oleh pengerasan regangan apabila diperlukan kekerasan tinggi. Paduan Al 5083 yang dianil adalah paduan antara ( 4,5 % Mg ) kuat dan mudah dilas oleh karena itu sekarang dipakai sebagai bahan untuk tangki LNG (Surdia dan Saito.1992).
2.2.5 Paduan Al-Mg-Si
sangat baik mampu bentuknya untuk penempaan, ekstrusi dan sebagainya. Paduan 6063 dipergunakan untuk rangka – rangka konstruksi , karena paduan dalam sistem ini mempunyai kekuatan yang cukup baik tanpa mengurangi hantaran listrik, maka selain dipergunakan untuk rangka konstruksi juga digunakan untuk kabel tenaga (Surdia dan Saito, 1992)
2.2.6 Paduan Al-Mn–Zn
Jepang pada awal tahun 1940 Iragashi dan kawan-kawan mengadakan studi dan berhasil dalam pengembangan suatu paduan dengan penambahan kira–
kira 0,3 % Mn atau Cr dimana butir kristal padat diperhalus dan mengubah bentuk presipitasi serta retakan korosi tegangan tidak terjadi. Pada saat itu paduan tersebut dinamakan ESD atau duralumin super ekstra. Selama perang dunia ke dua di Amerika serikat dengan maksud yang hampir sama telah dikembangkan pula suatu paduan yaitu suatu paduan yang terdiri dari: Al, 5,5 % Zn, 2,5 % Mn, 1,5% Cu, 0,3 % Cr, 0,2 % Mn sekarang dinamakan paduan Al- 7075. Paduan ini mempunyai kekuatan tertinggi diantara paduan-paduan lainnya. Pengggunaan paduan ini paling besar adalah untuk bahan konstruksi pesawat udara, disamping itu juga digunakan dalam bidang konstruksi (Surdia dan Saito,1992).
2.3 Magnesium
Penggunaan Mg dalam pembuatan komposit adalah sebagai wetting agent, yaitu untuk meningkatkan pembasahan antara matriks dan penguat dengan cara menurunkan tegangan permukaan antara keduanya (Samuel,Y., 2012).
2.4 Fly Ash
Fly ash atau abu terbang merupakan salah satu produk sisa dari proses
pembakaran diruang bakar suatu pembangkit, fly ash ini biasanya berbentuk partikel-partikel halus yang keberadaannya dapat membahayakan kesehatan manusia jika tidak ditangani dengan benar. Seiring dengan kemajuan teknologi maka saat ini keberadaan fly ash tidak hanya sebagai limbah tidak bermanfaat tetapi telah dipergunakan untuk campuran beragam jenis produk seperti semen, bata tahan api dan metal matrix composite (Yasman,F.,2014)
2.4.1 Fly Ash Batubara
Fly ash batubara adalah material yang memiliki ukuran butiran yang
halus berwarna keabu-abuan dan diperoleh dari hasil pembakaran batubara (Wardani,2008). Pada pembakaran batubara dalam PLTU, terdapat limbah padat yaitu abu layang (fly ash) dan abu dasar (bottom ash). Partikel abu yang terbawa gas buang disebut fly ash, sedangkan abu yang tertinggal dan dikeluarkan dari bawah tungku disebut bottom ash. Di Indonesia, produksi limbah abu dasar dan abu layang dari tahun ke tahun meningkat sebanding dengan konsumsi penggunaan batubara sebagai bahan baku pada industri PLTU (Harijono,D., 2006).
1. Penyusun beton untuk jalan dan bendungan 2. Penimbun lahan bekas pertambangan
3. Recovery magnetic, cenosphere, dan karbon
4. Bahan baku keramik, gelas, batu bata, dan refraktori 5. Bahan penggosok (polisher)
6. Filler aspal, plastik, dan kertas 7. Pengganti dan bahan baku semen
8. Aditif dalam pengolahan limbah (waste stabilization) 9. Konversi menjadi zeolit dan adsorben
Konversi abu terbang batubara menjadi zeolit dan adsorben merupakan contoh pemanfaatan efektif dari abu terbang batubara. Keuntungan adsorben berbahan baku fly ash batubara adalah biayanya murah. Selain itu, adsorben ini dapat digunakan baik untuk pengolahan limbah gas maupun limbah cair (Marinda,P.,2008)
2.4.1.1 Sifat Kimia dan Sifat Fisika Fly Ash Batubara
Komponen utama dari abu terbang batubara yang berasal dari pembangkit listrik adalah silika ( SiO2 ), alumina, ( Al2O3 ), besi oksida ( Fe2O3 ), kalsium ( CaO ) dan sisanya adalah magnesium, potasium, sodium, titanium dan belerang dalam jumlah yang sedikit.
Tabel 2.3. Komposisi Kimia Salah Satu Jenis Abu Terbang Batubara (Wardani,2008)
Komponen Bituminus Sub Bituminous( % ) Lignit
SiO2 20-60 40-60 15-45
Al2O3 5-35 20-30 20-25
Fe2O3 10-40 04-10 3-15
CaO 1-12 5-30 15-40
MgO 0-5 1-6 3-10
SO3 0-4 0-2 0-10
Na2O 0-4 0-2 0-6
2.4.2 Palm Oil Fly Ash (POFA)
Hasil proses pembuatan Crude Palm Oil (CPO) maka akan dihasilkan limbah padat diantaranya serabut buah dan cangkang kelapa sawit itu sendiri, namun ini tidak menjadi masalah bagi Pabrik Kelapa sawit (PKS) karena limbah ini akan menjadi bahan bakar daripada boiler. Limbah padat berupa cangkang dan serat digunakan sebagai bahan bakar ketel (boiler) untuk menghasilkan energi mekanik dan panas. Uap dari boiler dimanfaatkan untuk menghasilkan energi listrik dan untuk merebus TBS sebelum diolah di dalam pabrik. Diagram alir pembentukan pofa dapat dilihat pada gambar 2.5.
Gambar 2.5 Diagram Alir Palm Oil Fly Ash
Cangkang dan serat buah sawit yang sudah terbakar, akan menghasilkan sisa- sisa pembakaran yang nantinya akan menjadi limbah daripada boiler atau furnance (tungku pembakaran) berupa abu terbang. Abu Terbang (Fly ash) , yakni abu yang berada dibawah tungku tepatnya ditempat pengumpulan abu. Abu terbang terlihat pada gambar 2.6
(a) (b)
Gambar 2.6 (a)Abu Terbang (Palm Oil Fly Ash), (b)Bottom ash sesudah di grinding (Yasman,F.,2014)
Buah Sawit Produksi
Cangkang sawit
(bahan bakar) Boiler
bak penampungan Palm Oil Fly Ash
Udara
Partikel Ash Ringan
CPO
Masalah yang kemudian timbul adalah sisa dari pembakaran pada boiler yang berupa abu dengan jumlah yang terus meningkat sepanjang tahun yang sampai sekarang masih belum termanfaatkan. Ternyata limbah abu sawit banyak mengandung unsur silika (SiO2) yang merupakan bahan pozzolanic. Berdasarkan penelitian yang dilakukan Graille dkk (1985) ternyata limbah abu sawit banyak mengandung unsur silika (SiO2) yang merupakan bahan pozzolanic (Yasman,F.,2014).
Hayward (1995) dalam Utama dan Saputra (2005) menyatakan dalam bahan pozzolan ada dua senyawa utama yang mempunyai peranan penting dalam pembentukan semen yaitu senyawa SiO2 dan Al2O3 yang dimana abu Sawit merupakan bahan pozzolanic, yaitu material yang tidak mengikat seperti semen, namun mengandung senyawa silika oksida (SiO2) aktif yang apabila bereaksi dengan kapur bebas atau Kalsium Hidroksida (Ca(OH2)) dan air akan membentuk material seperti semen yaitu Kalsium Silikat Hidrat. Unsur penyusun
fly ash sangatlah beragam tergantung dari sumber bahan bakarnya, tetapi pada
umumnya fly ash mengandung SiO2,CaO,
2.5 Komposit Matrik Logam (Metal Matrix Composite)
Material komposit adalah material yang terdiri dari gabungan dua atau lebih fasa yang berbeda baik secara fisika ataupun kimia dan memiliki karakteristik lebih unggul dari masing - masing komponen penyusunnya. Material komposit terdiri dari dua fasa, satu disebut sebagai matriks dengan masa
continuous dan penguat dengan fasa discontinuous. Dalam komposit logam,
Gambar 2.7 Penguat dalam material komposit a). konsentrasi, b). Ukuran, c) bentuk, d). Distribusi, dan e) orientasi (Calister, 2003).
Kombinasi yang terjadi pada logam komposit berupa material fasa logam (yang harus bersifat ulet) dengan material penguat berupa keramik (senyawa oksida, karbida dan nitrida) yang biasanya terbentuk partikulat dengan kadar antara 10-60% fraksi volum.
Metal matrix composite memiliki keunggulan dibandingkan dengan
logam tunggalnya karena metal matrix composite dapat memiliki sifat yang diinginkan, seperti peningkatan kekuatan dengan berat yang lebih rendah. Beberapa keunggulan metal matrix composite dibandingkan dengan logam tunggalnya, yaitu:
1. Kombinasi kekuatan dan modulus yang baik. 2. Berat jenis jenderung lebih rendah.
3. Rasio kekerasan dengan berat dan modulus dengan berat lebih baik dari logam.
4. Nilai koefisien muai panasnya lebih rendah dibandingkan logam 5. Kekuatan fatik cukup baik.
2.6 Proses Pengecoran Logam
mentah. Komposisi unsur serta kadarnya dianalisis agar diperoleh suatu sifat bahan sesuai dengan kebutuhan sifat produk yang direncanakan namun dengan komposisi yang homogen serta larut dalam keadaan padat. (Sudjana,H.,2008)
Produk pengecoran logam mempunyai bentuk dan dimensi yang khas, karena pembuatannya dilakukan dengan mengubah logam dari fasa cair menjadi padat. Pembentukan benda dilakukan sekaligus dan tidak dilakukan dengan perakitan bagian-bagian benda.
Keuntungan proses pengecoran logam adalah: 1. Dapat membuat bentuk yang rumit
2. Dapat menghemat waktu dan pengerjaan produk missal
3. Dapat menggunakan bahan yang tidak dapat dikerjakan dengan proses pemesinan
4. Ukuran Produk tidak terbatas 5. Bahan dapat dilebur ulang
Kekurangan proses pengecoran logam adalah:
1. Kurang ekonomis untuk produksi dalam jumlah sedikit
2. Permukaan secara umum lebih kasar dibanding proses pemesinan 3. Toleransi kepresisian ukuran harus lebih besar dibanding produk
pemesinan
2.6.1 Centrifugal Casting
2.6.2 Jenis–Jenis Pengecoran Sentrifugal
Ada beberapa jenis pengecoran sentrifugal, yaitu : 1. Pengecoran sentritugal sejati
Dalam pengecoran sentrifugal sejati, logam cair dituangkan ke dalam cetakan yang berputar untuk menghasilkan benda cor bentuk tabular, seperti pipa, tabung, bushing, cincin, dan lain-lainnya. Proses pengecoran logam sejati dapat dilihat pada gambar 2.8.
Gambar 2.8 Proses pengecoran sentrifugal sejati (Budi,T.K.,2010)
Berdasarkan gambar 2.8 diatas ditunjukkan logam cair dituangkan ke dalam cetakan horisontal yang sedang berputar melalui cawan tuang (pouring basin) yang terletak pada salah satu ujung cetakan. Pada beberapa mesin, cetakan baru diputar setelah logam cair dituangkan. Kecepatan putar yang sangat tinggi menghasilkan gaya sentrifugal sehingga logam akan terbentuk sesuai dengan bentuk dinding cetakan. Jadi, bentuk luar dari benda cor bisa bulat, oktagonal, heksagonal, atau bentuk-bentuk yang lain, tetapi sebelah dalamnya akan berbentuk bulatan, karena adanya gaya radial yang simetri.
Karakteristik benda cor hasil pengecoran sentrifugal sejati:
a. Memiliki densitas (kepadatan) yang tinggi terutama pada bagian luar coran,
b. Tidak terjadi penyusutan pembekuan pada bagian luar benda cork karena adanya gaya sentrifugal yang bekerja secara kontinu selama pembekuan c. Cenderung ada impuritas pada dinding sebelah dalam coran dan hal ini
2. Pengecoran semi sentritugal
Proses pengecoran ini cetakan diisi penuh oleh logam cair dan biasanya diputar pada sumbu vertikal. Bila diperlukan dapat digunakan inti untuk menghasilkan produk cor yang berongga. Bagian tengah dari cetakan biasanya padat, akan tetapi strukturnya kurang padat dan memungkinkan adanya cacat inklusi. Coran yang sulit dihasilkan melalui cara statis dapat dilakukan dengan metode ini, karena gaya centrifugal memasukan logam cair di bawah tekanan yang lebih tinggi jika dibandingkan pada pengecoran statis. Hal ini meningkatkan hasil coran secara menonjol (85-95%), benar-benar memenuhi lubang cetakan, dan menghasilkan coran berkualitas tinggi, bebas rongga dan porositas. Bagian coran yang lebih tipis dapat dibuat dengan metode ini dibanding dengan pengecoran statis. Aplikasi dari pengecoran semicentrifugal adalah untuk membuat gear blanks, pulley, roda, impelers dan rotor motor listrik (Akuan,A.,2009). Pengecoran semi sentrifugal terlihat pada gambar 2.9.
Gambar 2.9 Pengecoran semi sentritugal (Budi,T.K.,2010)
3. Pengecoran sentrifuge
Centrifuging (pressure) memiliki aplikasi yang paling luas. Pada metode ini,
lubang coran disusun disekitar pusat sumbu putaran seperti jari-jari roda, sehingga memungkinkan produksi coran lebih dari satu. Gaya centrifugal memberikan tekanan yang diperlukan logam cair seperti yang terdapat pada pengecoran semicentrifugal. Metode pengecoran ini khususnya digunakan untuk memproduksi valve bodies, bonnet,plugs, yokes, brackets dan banyak lagi pada industri pengecoran lainnya (Akuan,A.,2009)
Dalam pengecoran sentrifuge cetakan dirancang dengan beberapa rongga cetak yang diletakkan disebelah luar dari pusat rotasi sedemikian rupa sehingga logam cair yang dituangkan ke dalam cetakan akan didistribusikan kesetiap rongga cetak dengan gaya sentrifugal, seperti yang ditunjukkan dalam gambar 2.10 .
Gambar 2.10 Pengecoran sentrifuge (Budi,T.K.,2010)
2.7 Heat Treatment
disamping posisi kimianya, contoh suatu logam atau paduan akan mempunyai sifat mekanis yang berbeda-beda struktur mikronya diubah. Dengan adanya pemanasan atau pendinginan dengan kecepatan tertentu maka bahan-bahan logam dan paduan memperlihatkan perubahan strukturnya (Abdillah,F., 2010). Tidak semua paduan aluminium dapat di heat treatment. Paduan yang dapat dilakukan proses heat treatment hanya dari kelompok 2XX.X, 3XX.X dan 7XX.X (di mana elemen paduan utama adalah tembaga, magnesium dan seng). Paduan Al dari kelompok lain dapat ditingkatkan hanya dengan pekerjaan dingin karena proses pengerasan presipitasi tidak terjadi di dalamnya (Paryono dan AP. Bayuseno, 2011).
Beberapa jenis proses perlakuan panas yang biasa dilakukan pada paduan aluminium yang mampu diberi perlakuan panas, yang biasanya diawali dengan penandaan huruf W dan T. penandaan W biasanya menyatakan kondisi tidak stabil dan tidak umum digunakan. Penandaan T yan diikuti angka 1 sampai 10 menyatakan proses yang diberikan pada logam coran paduan (Eifelson,2008). Lebih jelasnya dapat dilihat pada Tabel 2.5 dibawah ini:
Tabel 2.4 Penandaan Temper Pengerasan Penuaan Paduan Allumunium (Eifelson,2008)
Temper Keterangan
T1 Didinginkan dari suhu yang ditinggikan dan diaging secara alami
T2 Didinginkan dari suhu yang ditinggikan, pengerjaan dingin dan diaging secara alami
T3 Perlakuan larutan, pengerjaan dingin, dan diaging secara alami
T4 Perlakuan larutan, dan diaging secara alami
T5 Didinginkan dari suhu yang ditinggikan dan diaging secara artifisial
T6 Perlakuan larutan, dan diaging secara artificial
T7 Perlakuan larutan dan distabilkan dengan overaging
T8 Perlakuan larutan, pengerjaan dingin, dan diaging secara artifisial
T9 Perlakuan larutan, diaging secara artifisial, dan pengerjaan dingin
Salah satu cara perlakuan panas pada logam paduan aluminium adalah dengan Penuaan Keras (Age Hardening). Melalui penuaan keras (Age
hardening), logam paduan aluminium akan memperoleh kekuatan dan kekerasan
yang lebih baik. Dahulu orang menyebut penuaan keras (age hardening) dengan sebutan pemuliaan atau penemperan keras. Penamaan tersebut kemudian dibakukan menjadi penuaan keras (age hardening) karena penemperan keras pada logam paduan aluminium berbeda dengan penemperan keras yang berlangsung pada penemperan keras baja. Penuaan keras (age hardening) berlangsung dalam tiga tahap yaitu:
a. Tahap perlakuan panas pelarutan ( Solution heat treatment )
Solution heat treatment adalah pemanasan logam aluminium dalam dapur
pemanas dengan temperatur kurang dari 5480C dan dilakukan penahanan atau holding time sesuai dengan jenis dan ukuran benda kerja, pada tahap ini terjadi pelarutan fasa-fasa yang ada, menjadi larutan padat. Tujuan dari proses ini yaitu untuk mendapatkan larutan padat yang mendekati homogen (Paryono dan Bayuseno, 2011).
b. Tahap Pengejutan / pendinginan ( Quenching )
Quenching merupakan tahap yang paling kritis dalm proses perlakuan
panas. Quenching dilakukan dengan cara mendinginkan logam yang telah dipanaskan dalam dapur pemanas kedalam media pendingin. Dalam proses age
hardening logam yang di quenching adalah logam paduan aluminium yang telah
dipanaskan dalam dapur pemanas kedalam media pendingin air. Dipilihnya air sebagai media pendingin pada proses quenching karena air merupakan media pendingin yang cocok untuk logam-logam yang memiliki tingkat kekerasan atau
hardenability yang relatif rendah seperti logam paduan aluminium.
Tahap quenching akan menghasilkan larutan padat lewat jenuh (Super
Saturated Solid Solution) yang merupakan fasa tidak stabil pada temperatur biasa
atau temperatur ruang. Proses quenching tidak hanya menyebabkan atom terlarut tetap ada dalam larutan, namun juga menyebabkan jumlah kekosongan atom tetap besar. Adanya kekosongan atom dalam jumlah besar dapat membantu proses difusi atom pada temperatur ruang untuk membentuk zona Guinier –
Preston (Zona GP). Zona Guinier - Preston ( Zona GP) adalah kondisi didalam paduan dimana terdapat agregasi atom padat atau pengelompokan atom padat. (Surdia dan Saito, 1992).
c. Tahap Penuaan ( Aging )
Setelah solution heat treatment dan quenching tahap selanjutnya dalam proses age hardening adalah aging atau penuaan. Perubahan sifat-sifat dengan berjalanya waktu pada umumnya dinamakan aging atau penuaan. Aging atau penuaan pada paduan aluminium dibedakan menjadi dua, yaitu penuaan alami (
natural aging ) dan penuaan buatan (artificial aging ).
Penuaan alami ( natural Aging ) adalah penuaan untuk paduan aluminium yang di age hardening dalam keadaan dingin. Natural aging berlangsung pada temperatur ruang antara 15oC - 25oC dan dengan waktu penahanan 5 sampai 8 hari. Penuaan buatan ( artifical aging ) adalah penuaan untuk paduan aluminium yang di age hardening dalam keadaan panas. Artifical aging berlangsung pada temperatur antara 100oC -200oC dan dengan lamanya waktu penahanan antara 1 sampai 24 jam. ( Schonmetz, 1990).
Pengambilan temperatur artificial aging pada temperatur antara 1000C -2000C akan berpengaruh pada tingkat kekerasan sebab pada proses artificial
aging akan terjadi perubahan-perubahan fasa atau struktur. Perubahan fasa
a. Larutan Padat Lewat Jenuh
Setelah paduan alumunium melawati tahap solution heat treatment dan
quenching maka akan didapatkan larutan padat lewat jenuh pada temperatur
kamar. Pada kondisi ini secara simultan kekosongan atom dalam keseimbangan termal pada temperatur tinggi tetap pada tempatnya. Setelah pendinginan atau
quenching, maka logam paduan alumunium menjadi lunak jika dibandingkan
dengan kondisi awalnya. b. Zona [GP 1]
Zona [GP 1] adalah zona presipitasi yang terbentuk oleh temperatur penuaan atau aging yang rendah dan dibentuk oleh segregasi atom Cu dalam larutan padat lewat jenuh atau super saturated solid solution ( Smith, 1995)
Zona [GP 1] akan muncul pada tahap mula atau awal dari proses artificial
aging. Zona ini terbentuk ketika temperatur artificial aging dibawah 1000C atau mulai temperatur ruang hingga temperatur 1000C dan Zona [GP 1] tidak akan terbentuk pada temperatur artificial aging yang terlalu tinggi. Terbentuknya Zona [GP 1] akan mulai dapat meningkatkan kekerasan logam paduan alumunium. ( Smith, 995). Jika artificial aging ditetapkan pada temperatur 1000C, maka tahap perubahan fasa hanya sampai terbentuknya zona [GP 1] saja. Proses pengerasan dari larutan padat lewat jenuh sampai terbentuknya zona [GP 1] biasa disebut dengan pengerasan tahap pertama.
c. Zona [GP 2] atau Fasaθ ”
Setelah temperatur artificial aging melewati 1000C ke atas, maka akan mulai muncul fasa θ ” atau zona [GP 2]. Pada temperatur 1300C akan terbentuk zona [GP2] dan apabila waktu penahanan artificial agingnya terpenuhi maka akan didapatkan tingkat kekerasan yang optimal (Smith, 1995). Biasanya proses
artificial aging berhenti ketika sampai terbentuknya zona [GP 2] dan
terbentuknya fasa antara yang halus (presipitasiθ ”), karena setelah melewati zona
[GP 2] maka paduan akan kembali menjadi lunak kembali. Jika proses artificial
aging berlangsung sampai terbentuknya fasa θ ” atau zona [GP 2], maka disebut
d. Fasaθ ’
Kalau paduan alumunium dinaikan temperatur aging atau waktu aging diperpanjang tetapi temperaturnya tetap, maka akan terbentuk presipitasi dengan struktur kristal yang teratur yang berbeda dengan fasaθ ’. Fasa ini dinamakan fasa antara atau fasaθ ’. Terbentuknya fasa θ ’ ini masih dapat memberikan sumbangan
terhadap peningkatan kekerasan pada paduan alumunium. Peningkatan kekerasan yang terjadi pada fasaθ ’ ini berjalan sangat lambat.
e. Fasaθ
Apabila temperatur dinaikan atau waktu penuaan diperpanjang, maka fasa
θ ’ berubah menjadi fasa θ . Jika fasaθ terbentuk maka akan menyebabkan paduan aluminium kembali menjadi lunak. Sementara waktu penahanan dalam artificial aging merupakan salah satu komponen yang dapat mempengaruhi hasil dari proses age hardening secara keseluruhan. Seperti halnya temperatur, waktu penahanan pada tahap artificial aging akan mempengaruhi perubahan struktur atau perubahan fasa paduan
2.8 Pengujian Komposisi Kimia
2.9 Pengujian Kekerasan
Kekerasan aluminium dapat didefinisikan sebagai ketahanan logam terhadap indentasi. Nilai kekerasan berkaitan dengan kekuatan luluh logam karena selama identasi logam mengalami deformasi plastis. Luluh merupakan proses slip, luncur tau kembaran. Pada proses slip, struktur kisi antara daerah slip dan daerah tanpa slip terdislokasi. Batas antara daerah slip dan daerah tanpa slip disebut garis lokasi (solechan, 2010)
Kekerasan Ketahanan bahan terhadapindentasi secara kualitatif menunjukan kekuatannya (Shackelford,2009). Skala yang lazim dalam pengujian kekerasan antara lain skala Brinell, Vickers, Rockwell dan Knop. Skala kekerasan brinell (BHN) cenderung menunjukkan korelasi yang cukup linier terhadap bahan tertentu, termasuk paduan aluminium terlihat pada Tabel 2.6 merupakan sifat dari logam yang sering dipergunakan dalam pengecoran, dimanadalam Tabel tersebut terdapat sifat paduan aluminium seperti kekerasan (Amstead, 1997).
Tabel 2.6 Sifat-sifat dari logam (Amstead,1997)
Jenis Logam Kekuatan Tarik (Mpa) Keuletan (%) Kekerasan
(BHN)
Besi dan Baja
Besi cor kelabu Besi cor putih Baja 110-207 310 276-2070 0-1 0-1 12-15 100-150 450 110-500 Bukan Besi Aluminium Tembaga Magnesium Seng Titan Nikel 83-310 345-689 83-345 48-90 552-1034 414-1103 10-35 5-10 9-15 2-10 -15-40 20-100 50-100 30-60 80-100 158-266 90-250
Gambar
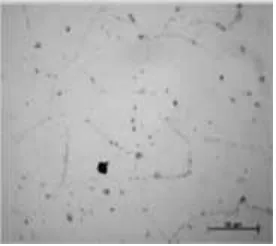
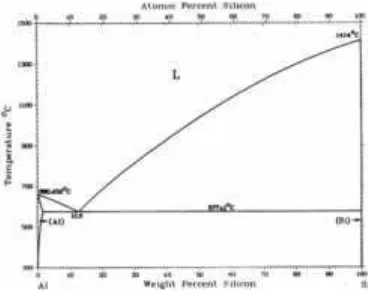
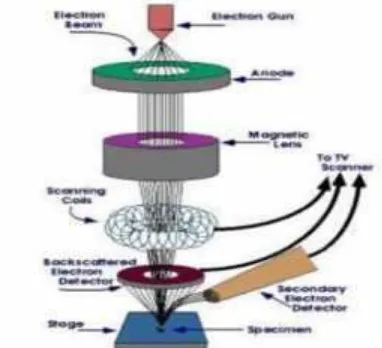
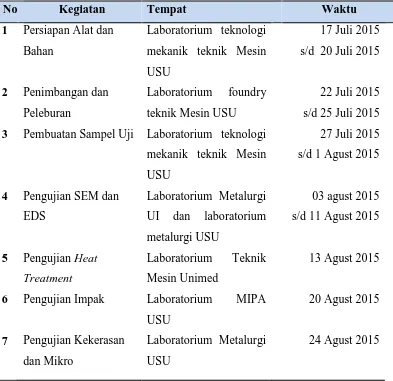
Dokumen terkait
pada Tanaman Tomat di Sumatera Utara” merupakan salah satu syarat untuk dapat memperoleh gelar sarjana pertanian di Program Studi Agroekoteknologi Fakultas Pertanian
[r]
The effects of intracerebral glucose respectively, the latter value being reflective of the faster turnover time, blood / brain lactate exchange, and gluta- transport rates expected
[r]
High concentrations of aluminum concentration of aluminum associated to cultured cells may induce apoptotic cell death by inducing transition from S be rather unlikely to occur in
[r]
[r]
magnocellular part; BLpc, basolateral amygdaloid nucleus, parvicellular part; BST, bed nucleus of stria terminalis; CeM, central medial thalamic nucleus; CDvm, caudate