Polymer blending is a process of combining two or more types of polymer to achieve desired properties instead of developing new polymer. This study was conducted to characterize the thermal conductivity properties and tensile strength properties of the polymer blend composed of polypropylene and polycarbonate. Maleic anhydride grafted with polypropylene was chosen as compatibilizer to improve the miscibility of the mixture.
Samples will be laboratory tested to determine the thermal conductivity value of each formulation using the ASTM E1225 -04 Standard Test Method for Thermal Conductivity of Solids using the Guarded Comparative Longitudinal Heat Flow technique. Tensile strength test specimens are prepared by an injection molding machine, and testing is performed in accordance with ASTM 0638-10 Standard Test Method for Tensile Properties of Plastics. Time PPIPCIPP-g-MA Figure 17: Thermal conductivity value of selected mixtures Figure 18: Stress and strain graph (PPIPC).
Recently, a new polymer blend has been successfully produced using compatibilizers, and since then many studies have been conducted on different types of polymer blends to further characterize their properties. The mixture will also retain the special properties of PP, such as high chemical and temperature resistance, low thermal conductivity and low water absorption. Thermal conductivity is a property of a material that refers to its ability to conduct heat and is considered one of the most important properties of polymers.
The aim of this project is to define the thermal conductivity behavior of PP/PC blends compatible with polypropylene graft and maleic anhydride (PP-g-MA).
Problem statement
Objectives and Scope of study
CHAPTER2 LITERATURE REVIEW
Thermal conductivity
The thermal conductivity of the polymer can not only be changed by introducing other particles into the polymer matrix, but it can also be changed by changing the process parameters. The effect of pressure on the thermal conductivity of polymer melts has also been studied by several researchers [6]. Overall, the findings indicated that thermal conductivity will increase with increasing pressure and temperature.
Previous studies have revealed that thermal conductivity is the least measured polymer property [7] and yet it is one of the most important properties in polymer processing. Thermal conductivity can be measured using ASTM: E 1225-04 standards, and commercial techniques generally calculate thermal diffusivity and calculate thermal conductivity using the heat capacity value, which are measured separately. However, some studies have been done to find another method of measuring the thermal conductivity of the polymer.
The measurement of small polymer thermal conductivity is being performed using differential scanning calorimetry [8]. The use of DSC as a method for measuring thermal conductivity does not require any modification of the existing DSC instrument. It is suitable for thermal conductivity of the small sample, which is a cylinder with a diameter of 6 mm and a length of 2-8 mm.
The developed method can also minimize the effect of thermal contact resistance on thermal conductivity measurement. A research has been carried out on the reinforcement of PC as a dispersed phase within the PP matrix and the improvement of the properties of these composites with the addition of nanoclay, montmorillonite (MMT) [1]. The results presented in the graph are divided into two sections corresponding to low and high T m· The x-axis illustrates the number and corresponding time of piston movements (strokes).
Based on their findings, it can be concluded that the presence of PC content within a PP matrix will cause a significant increase in mechanical properties of PP/PC blend. Polypropylene is one of the most widely used polyolefins in industry due to its versatility and good properties such as excellent chemical resistance, good mechanical and thermal properties and relatively cheap [9] as summarized in Table I. Polypropylene also has good workability and can be processed by a variety of methods including extrusion, blow molding, injection molding and thermoforming [10].
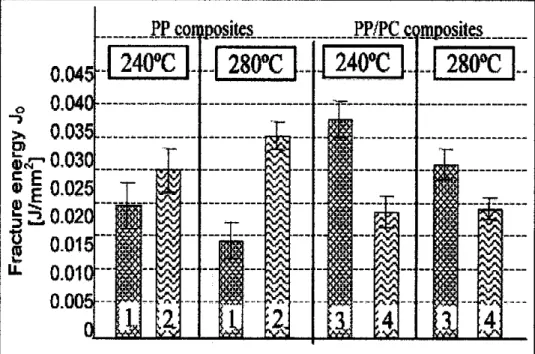
Polycarbonate
The polycarbonate market is continuously growing as many studies have been conducted to overcome the disadvantages of polycarbonate such as limited scratch and weather resistance. The main problem with immiscible mixtures is high interfacial tension and poor adhesion between two phases, resulting in poor mechanical properties. A few solutions have been incorporated to solve the problem, and one of the ways is to use compatibilizers to improve the adhesion between phases of polymer blends.
A compatibilizer is a type of coupling agent that can improve the interfacial adhesion of separate phases in a polymer mixture and reduce the interfacial tension at the phase boundaries, making the particles smaller to increase the contact area. As a result, any force or energy acting on the mixture is transferred from one phase to the other, improving the mechanical properties of the mixture. One of the compatibilizers for the PP/PC blend is polypropylene grafted maleic anhydride (PP-g-MA).
It has been reported that graft copolymer can be effectively used as compatibilizer for polymer blend [12]. A study by Renaut et at [13] concluded that PP-g-MA was more effective than the terpolymer ethylene/acrylic ester/maleic anhydride (EBuAMA) and offered better thermomechanical properties of PP/PC blends. PP/PC blend with PP-g-GMA showed overall good result of compatibilization as Young's modulus, tensile strength and Izod impact strength experienced significant increase [13].
The compatibilizer reduces the interfacial tension, increases the interfacial adhesion, and homogenizes the domain size, thus resulting in better properties [14]. A group of researchers from Chulalongkorn University has researched using PP-g-MA as a compatibilizer in polypropylene/polyamide 6 blends [IS]. Their research results showed that the blend of PP/P A6 70/30 incorporated with 5 and 10 phr PP-g-MA exhibited high
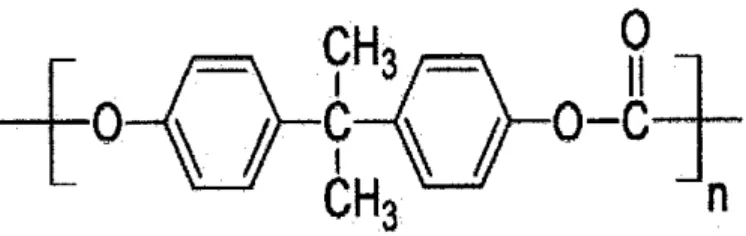
Twin Screw Extruder and Compression Molding
CHAPTER3 METHODOLOGY
Sample Fabrication
After mixing, the mixtures will be molded according to cylinder shape with 25 mm in diameter and 15 mm in length.
Testing
CHAPTER4
TGA analysis
TGA has been used to characterize PP/PC blends and the degradation temperature of PP/PC/PP-g-MA blends. Degradation temperature plays an important role in sample fabrication as it can help us determine the accurate melt processing temperature. The temperature must be high enough for the polymers to melt and flow, but not exceed the degradation temperature to avoid deterioration of their properties.
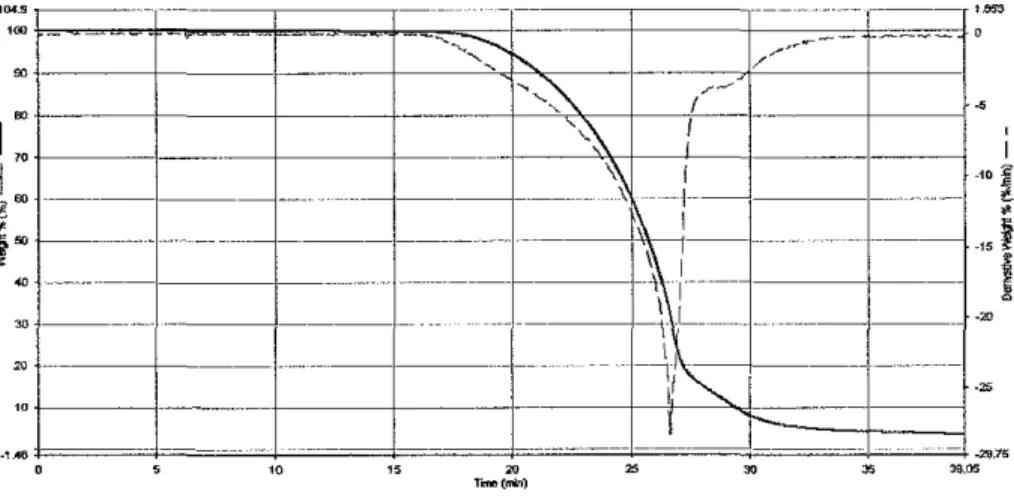
DSC Analysis
The results of the thermal conductivity test on the selected mixtures are shown in Figure 17. The test is performed on pure PP and PC to verify the exact value against literature data and the manufacturer's data. The thermal conductivity of PP is found to be 0.31, while PC is 0.21, which is in agreement with the data provided.
It can be seen from Table 3 and Figure 17 that the addition of PC to the PP matrix will decrease the thermal conductivity value of PP. The addition of 5% by mass of the compatibilizer (PP-g-MA) will reduce the value of the coefficient of thermal conductivity of the mixtures. For brittle materials, the tensile strength will be at the end of the linear-elastic portion of the stress-strain curve.
The results of the tensile test on the samples are shown in Figure 18 and Figure 19. The tensile strength values for blends with and without the compatibilizer are compared in Figure 20.
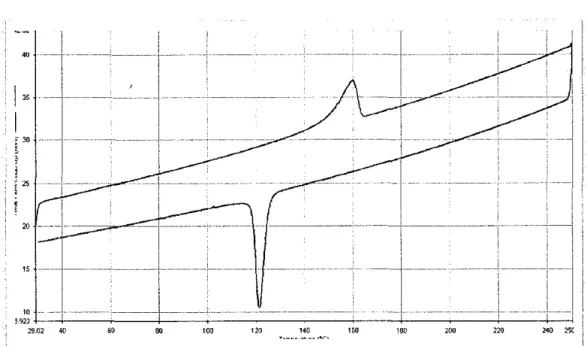
CHAPTERS CONCLUSIONS
Thomas, 1995, Effect of casting solvent and compatibilizer loading on the morphological properties of natural rubber/polystyrene blends, Polymer Plastic Technology Engineering, 34 633. Delobel, 2005, Fire safety, thermomechanical and thermal properties of PPIPC blends, Journal of Macromolecular Science, Part A: Pure and applied chemistry. 16] C.Li, G.Tian and Y.Zhang, 2002, Crystallization behavior of polypropylene/polycarbonate blends, Journal of Polymer Testing, Vol.
17] ASTM Standards: E 1225-04, Standard Test Method for Thermal Conductivity of Solids by Means of the Guarded-Comparative-Length-Flow Heat-Flow Technique.