Questions regarding the use of the book should be directed to the Rights and Permissions Department of INTECHOPEN LIMITED (permissions@intechopen.com). The type and yields of the pyrolysis products depend largely on the type of material treated.
Industrial applications of pyrolysis
The effect of the use of catalysts on the pyrolytic gas yield was reported by Chen et al. In experiments conducted by Lee et al., the optimum reaction temperature range for the production of bio-oil by fast pyrolysis was found to be 410–510°C [33].
Other applications of pyrolysis
Fast pyrolysis of rice straw, sugarcane and coconut shell in an induction heating reactor. Microwave pyrolysis of polymeric materials: treatment of waste rubber and characterization of value-added products.
Fast pyrolysis of lignin for production of aromatic hydrocarbons by mesoporous catalysts
This chapter presents a review of the recent literature on the fast pyrolysis process for the production of aromatic hydrocarbons using mesoporous catalysts. Catalytic fast pyrolysis of lignin with catalysts to produce aromatic hydrocarbons has attracted much research interest in recent years.
Factors that influence the pyrolysis process
- Kind of the catalyst
- Reactor types
- Exterior heating pyrolysis reactors
- Interior heating pyrolysis reactors
- Temperature and the rate of heating
- Effect of the reaction time
- Effect of lignin source
Recently, a fixed bed reactor has been widely used in the pyrolysis process of lignin or biomass. The pyrolysis process of lignin in a fluidized bed reactor resulted in a higher yield of bio-oil.
Deactivation of the catalysts
Although two catalysts were formed to be effective catalysts for deoxygenation reaction, increasing the formation of aromatic hydrocarbons from lignin, the acidic HZSM-5 was observed to be more active than CoO/MoO3.
The role of mesoporous catalyst acidity and textural topology
The mesoporous zeolite Y and the mesoporous material, Al-MCM-41, were tested for the catalytic fast pyrolysis of lignin. Catalytic fast pyrolysis of lignin over high surface area mesoporous aluminosilicates: Effect of porosity and acidity.
Introduction
Influence of process parameters on synthesis of biochar by pyrolysis of biomass: an alternative source of energy. The yield of biochar depends on organic constituents of biomass and the pyrolytic process parameters such as temperature, time, heating rate, purge gas, particle size, catalyst, flow rate, pressure and types of pyrolysis reactors.
Source of biomass
According to the International Biochar Initiative (http://www.biochar-international.org/biochar), biochar can be defined as 'a solid material obtained from the carbonization of biomass'. The main component of biochar is carbon, followed by hydrogen, oxygen, ash content, and trace amounts of nitrogen and sulfur. Most countries such as Australia, Finland, Germany, United Kingdom and Turkey are cutting generation.
Conversion techniques
Combustion
The conversion of biomass can be accomplished by two processes, namely (i) biochemical process or (ii) thermochemical process. Combustion is considered one of the most suitable and primitive technologies for the conversion of biomass [11].
Gasification
Pyrolysis
Effects of process parameters on yield of pyrolytic products
- Effect of carrier gas flow rate
- Effect of catalysts
- Effect of heating rate
- Effect of pressure
- Effect of particle size
- Effect of residence time
- Effect of temperature
- Effect of compositions of biomass
- Effect of reactor configuration
The yield of liquid (tar) and gaseous product decreases after mixing inorganic salt with the biomass, while the yield of solid products increases [20]. In addition, the yield of biochar was found to be increased after acid and base modification of biomass. The residence time between volatiles generated during pyrolysis and the hot biochar affects the yield of biochar.
At lower temperatures, the yield of biochar was high, probably due to the partial decomposition of the biomass.
Application of biochar
Moreover, above this temperature range, the decomposition of vapors produced as a result of secondary reactions becomes more active, which reduces the yield of liquid products [33]. As the cellulose content of biomass increases, there is a corresponding increase in gaseous products, but the yield of tar and carbon decreases. The height of these bed reactors is also an important factor affecting the yield of pyrolytic products.
The yield of biochar in both reactors remains the same, but the yield of liquid and gaseous products is different [53].
Summary and future prospects
Different kinetic models were proposed by several authors working on biomass pyrolysis kinetics. A detailed comparison of general packed bed and fluidized bed reactors is given in Table 4. An outlet for the pyrolysis products is provided just above the bottom of the pyrolyzer.
The modeling of the packed bed and the fluid bed pyrolysers is discussed in detail below. The modeling of the packed bed pyrolysis reactors is divided into drying stage and the pyrolysis stage. The type of pyrolysis-slow and fast/flash pyrolysis b.The type of reactor-fixed bed and fluidized bed reactors.
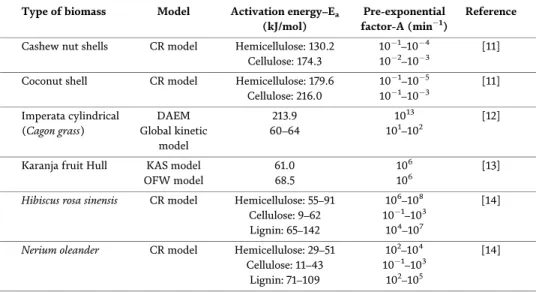
Waste plastics pyrolysis in conical spouted beds
The interest of this strategy lies in the fact that a tar-free syngas is produced due to the high activity of the reforming catalyst. In addition, the results obtained by the pyrolysis of different patches are also reported in this section, as long as the product distribution of the pyrolysis step is critical for the evaluation of the subsequent reforming step. One of the main challenges in pyrolysis of plastics is the sticky behavior of molten plastic particles, which causes agglomeration and subsequent defluidization in fluid bed reactors [46].
A remarkable solid residue yield (7% by weight) was obtained by the pyrolysis of PET, where this residue was obtained, which coats the sand particles.
Pyrolysis and in-line reforming of plastics
Parametric study of HDPE pyrolysis and in-line reforming
The increase in conversion and hydrogen production with temperature in the catalytic steam reforming of municipal solid waste [59] is explained because all the endothermic steps involved are favored: (i) initial pyrolysis of waste; (ii) char. As in the previous section, the effect of spacetime on the conversion, hydrogen production and yield of gaseous products has been investigated. This section shows the effect the S/P ratio in the range 3-5 has on conversion, hydrogen production and product yield at zero time in operation.
Numerous studies support this classification of coke deposited by reforming CH4, hydrocarbons and biomass derivatives.
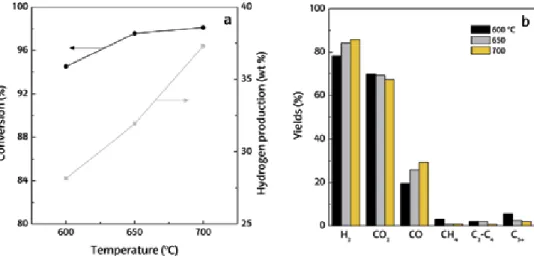
Pyrolysis and in-line reforming of different plastics
Hydrogen produced during pyrolysis and in-line catalytic reforming of different plastics is shown in Figure 8a. Wu and Williams [26] also observed a lower pyrolysis volatile conversion of PS compared to HDPE in pyrolysis and in-line reforming of various plastics. Czernik and French [31] achieved hydrogen production of 34 wt. % in pyrolysis and in-line PP reforming using two fluidized bed reactors.
Hydrogen production (a) and product yield (b) by pyrolysis and in-line reforming of different types of plastic.
Conclusions
Energy production from air gasification of two industrial plastic wastes in a pilot-scale fluidized bed reactor. Effect of polyethylene co-feeding on steam gasification of biomass in a conical bed reactor. Investigation of coke formation on Ni-Mg-Al catalyst for hydrogen production from catalytic steam pyrolysis-gasification of polypropylene.
Effects of gasification temperature and catalyst ratio on hydrogen production from catalytic steam pyrolysis gasification of polypropylene.
West Sumatra and its geographical condition
West Sumatra is one of the regions in the Indonesian archipelago with a fairly complex geological arrangement. The West Sumatra region is crossed by the equator (zero degrees latitude), located exactly in the Bonjol sub-district of Pasaman district. Due to the influence of this location, West Sumatra has a trophic climate with high temperatures and humidity. However, physically, West Sumatra is a region largely photographed by the mountains and the Bukit Barisan Plateau extending from the northwest to the southeast, 63% and the area is a dense forest with elevations of up to 3000 m above sea level.
The geographical situation of West Sumatra is quite unique and lies partly in the lowlands and partly in the highlands, characterized by many mountains, lakes, valleys/gorges and rivers.
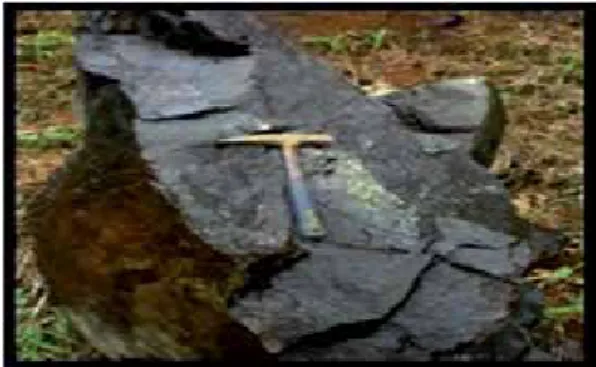
Dunite rock and its characteristics
The olivine mineral
Forsterite and its characteristics
Dunite is the main component of the Earth's mantle and is rarely found in continental rocks. MgO is one of the most important elements for plants for photosynthesis, while the pH level of rocks can neutralize acidic soils such as peatlands. The properties of the forsterite phase are melted at 1890°C and fayalite melts at a temperature of 1205°C [22].
This accumulation of olivine can give rise to a dunite-like rock at the bottom of the magma kitchen.
Nanoparticles technology
In simple terms, increasing the rotational speed of the mill will increase the energy input to the powder. The higher the ratio of the weight of the ball to the weight of the powder used, the shorter the impact frequency. The ratio of the weight of the ground ball to the weight of the powder in the grinding container used is 10:1.
For example, the weight of the ground ball is 150 g while the amount of powder is 15 g.

Synthesis of nanoparticles from forsterite
The grinding process is forsterite powder inserted into a metal chamber with several steel balls in it that move continuously. The ground ball size used in this process is a small ground ball with a diameter of 5 mm and a weight of 0.5 g. Due to this collision of the balls, the homogeneous powder that is inserted into this tool will be crushed between the balls.
Calcination and the effect of calcination temperature on the raw material structure
Samples were tested by X-ray fluorescence (XRF) to see the composition of the compounds in the dunite. The results of the XRD test of dunite raw material for each calcination temperature variation are shown in Table 2. While at the time of grinding for 10 hours, there was a clumping of the grain size, so that the size of the crystallite became large, i.e.
The meal is very influential on the surface morphology of the sample, where the longer the grinding process is done, the smaller the particle size.
High-energy milling methods, and the effect of the different parameters
The longer the grinding time, the higher the temperature at the collision of the ground balls. The collision between the grinding balls and the powder, which increases several times over time, the grinding time causes the powder particle size to be smaller. This is due to the ratio of the pellet to the powder used and also the speed of the grind and the time the grind is used.
The increase in grain size in one of the grinding results is due to the agglomeration process.
Conclusions
The size of the powder crushed with a grinding device becomes smaller than the size of the original powder. The decrease in intensity is due to changes in the size of the crystal, this change also causes the crystal structure of the forming element to change. When the grinding balls collide with each other, the powder that is ground is between the collisions of the balls so that the powder will deform and the powder will disintegrate which will cause the grain size to be small and it can also cause it to become large if the grain has solidified.
The grain size increases during the grinding time of 10 h because the particles are aggregated again after the particles are broken or broken with pellets so that they are small and then grouped until the grinding time of 10 h this is due to the powder that has been dissolved and has a small effect.