Alur proses produksi knalpot SND Pentagon Kawasaki KLX 150 dimulai dari bahan baku dengan bahan pipa besi, plat besi, plat filter dan balok besi, yang nantinya akan dialihkan ke bagian manufaktur. Berikut ini akan diuraikan tahapan-tahapan dalam alur proses produksi dan ditunjukkan pada gambar 4.5. Deskripsi tahapan proses : 1) Gudang bahan baku. Proses produksi knalpot Kawasaki KLX 150 Pentagon SND dimulai dari tempat penyimpanan bahan baku yang bertugas menyiapkan bahan baku yang akan digunakan sebelum proses produksi dimulai.
Kegiatan yang dilakukan di gudang bahan baku adalah pemeriksaan kedatangan bahan baku dan pengiriman bahan baku. Bahan baku yang telah diukur akan segera diolah dengan cara memotong bahan baku tersebut yang nantinya akan diproses pada tahap berikutnya. Dari bahan bakunya, plat besi dibentuk dengan sistem pengelasan menggunakan las karbida dan las listrik untuk menggabungkannya.
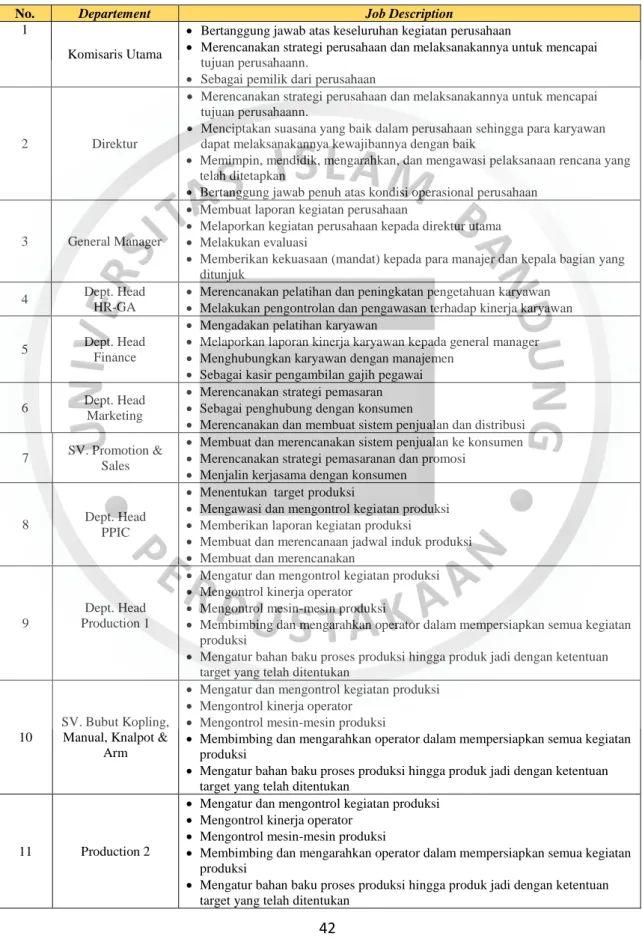
Pengolahan Data
Pemetaan Value Stream Mapping Current State
- Penentuan Produk
- Identifikasi Aliran Produk
- Pembuatan Value Stream Mapping Current State
Kegiatan identifikasi alur produksi SND Pentagon Exhaust Kawasaki KLX-150 menggunakan diagram alir untuk melihat proses pada setiap tahapan produksi, meliputi informasi proses, pengiriman, menunggu, dan aliran material. Hasil dari proses identifikasi ini akan digunakan sebagai acuan pemetaan keadaan VSM saat ini dan sebagai proses awal penerapan konsep Lean pada proses manufaktur pelepasan. Dalam proses pembuatan peta value stream keadaan saat ini, dilakukan beberapa langkah untuk memperoleh hasil pemetaan yang sesuai dengan situasi saat ini.
Fase 1 Penggambaran Entitas Customer
Fase 2 Menambah Aliran Informasi yang Melintasi Proses
Di lantai produksi, pemegang kendali berada di departemen PPIC dan membawahi departemen produksi pelepasan dan aliran informasi menggunakan jalur aliran informasi elektronik yang digambarkan sebagai garis petir dan garis padat untuk aliran informasi langsung.
Fase 3 Menambahkan Aliran Fisik Material
Pada tahap ini akan kami jelaskan setiap proses yang dilakukan dalam pembuatan knalpot Pentagon KLX 150 SND, mulai dari bahan baku hingga produk dikirim ke konsumen. Pada keterangan di kotak Proses Anda akan menemukan nama proses yang sedang dikerjakan, aliran material dan inventaris jika terjadi proses yang mengganggu. Di Kotak Data Anda akan menemukan informasi tentang setiap proses, seperti Cycle Time (C/T), Change Over (C/O), Utility, Uptime, Set Up Time dan Available Time.
Pada value stream map terdapat beberapa proses sekaligus, seperti pada proses pemotongan, hal ini menandakan proses dilakukan secara paralel dan tidak menunggu.
Fase 4 Menggabungkan setiap Aliran Fisik dengan Airan Informasi pada Value Stream Mapping
Fase 5 Melengkapi VSM dengan Informasi Production Lead Time dan Value Added Time
Perhitungan Takt Time
Identifikasi limbah pada proses pembuatan Knalpot SND Pentagon untuk Kawasaki KLX-150 pada awalnya dilakukan dengan menggunakan proses perhitungan Takt Time. Selain itu melalui perhitungan Takt Time diharapkan kita dapat mengidentifikasi beberapa informasi sebagai tolak ukur rata-rata yang diperlukan untuk menghasilkan produk dalam upaya memenuhi kebutuhan pelanggan, mengidentifikasi permasalahan yang terjadi dalam proses produksi dan untuk mengidentifikasi permasalahan yang terjadi dalam proses produksi. mengurangi limbah yang terjadi. Dalam proses perhitungan Takt Time diperlukan beberapa input antara lain waktu tenaga kerja dan permintaan produk per periode.
Dan untuk perbandingan menggunakan waktu siklus, waktu tersebut diambil berdasarkan waktu siklus terpanjang, berdasarkan pemetaan VSM Current State (Gambar 4.14). Waktu siklus terpanjang terdapat pada stasiun pengumpulan dengan nilai 40 menit. Berikut contoh perhitungan Takt Time periode 1, 10 Februari – 10 Maret 2017, dan ringkasan hasil dapat dilihat pada Tabel 4.4. Berdasarkan hasil perhitungan Takt time terlihat bahwa Takt time pada setiap periode berbeda-beda, namun cycle time pada setiap periode dianggap sebagai ukuran penyelesaian setiap produk pada setiap tempat kerja.
Identifikasi Waste
- Kuesioner 7 Waste
Setiap jenis pemborosan disingkat dengan huruf, (O: Overproduction, I: Inventory, D: Defect, M: Movement, P: Overprocess, T: Transport, W: Waiting), dan setiap hubungannya ditandai dengan garis. simbol lebih rendah. Masing-masing hubungan antar waste mempengaruhinya, yang berjumlah 31 hubungan antar waste tipe i mempengaruhi waste tipe j (i_j) seperti pada Tabel 2.3. Tahap selanjutnya adalah pembobotan sampah, hal ini dilakukan untuk mengetahui skor akhir responden yang mengisi kuesioner sampah.
Hasil pembobotan akan berbeda tiap kasus sampah, tergantung persepsi dan pendapat responden. Berdasarkan Tabel 4.5: Jika responden menjawab pertanyaan, maka skornya berdasarkan apa yang dijawabnya. Jika responden tidak menjawab pertanyaan maka skor dianggap 0. Kemudian mencari faktor konversi berdasarkan rentang derajat kekuatan jatuh, seperti terlihat pada Tabel 2.6, jika rentang 17-20 maka simbol konversinya adalah “A”, rentang 13-16 berarti simbol konversi “E”, rentang 9-12 berarti simbol konversi "I", rentang 5-8 berarti simbol konversi "O", rentang 1-4 berarti simbol konversi.
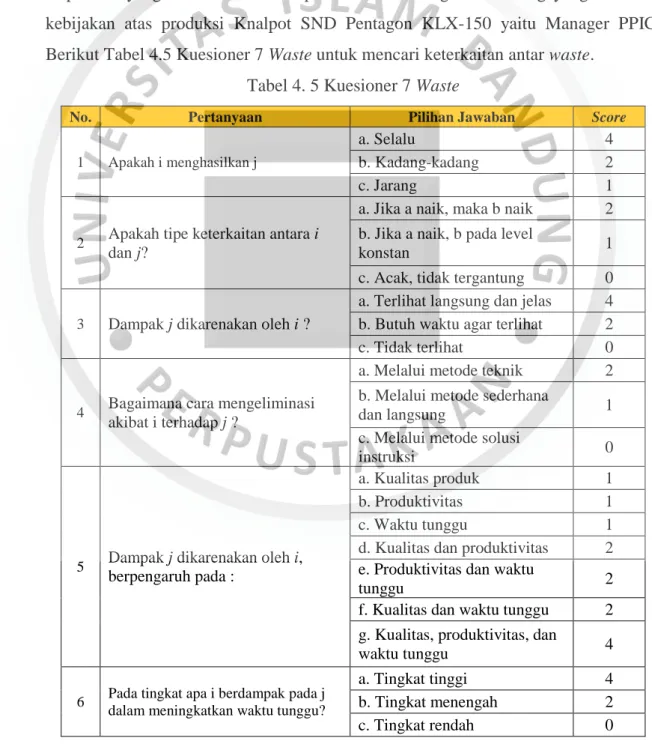
Waste Relationship Matrix (WRM)
Untuk lebih jelasnya, hasil perhitungan matriks WRM ditunjukkan pada Tabel 4.8 Nilai matriks waste sebagai berikut. Dari hasil perhitungan di atas dibuat perkiraan rata-rata berat (berat) sampah dengan membagi jumlah indikator yaitu 7 (O, I, D, M, T, P, W). Selain dalam bentuk tabel, hasil akhir penimbangan sampah juga ditampilkan secara grafis, sehingga memudahkan untuk melihat sampah mana yang mempunyai nilai paling besar.
Dari identifikasi waste yang terjadi pada proses produksi knalpot SND Pentagon KLX-150, dapat ditarik kesimpulan bahwa rata-rata berat waste yang paling besar adalah pengangkutan (transportasi/transfer) dengan bobot 6, kemudian waste diatas produksi dengan bobot sebesar 5,7 kemudian waste yang tidak diperlukan dan overprocess waste dengan bobot 5,1, selanjutnya reject dengan bobot 4,9, waiting waste dengan bobot 4,3 dan waste yang paling rendah adalah waste inventory dengan bobot 4,0 . Berdasarkan hasil penimbangan tersebut, kami melanjutkan ke perhitungan menggunakan metode VALSAT untuk membantu menemukan metode identifikasi selanjutnya.
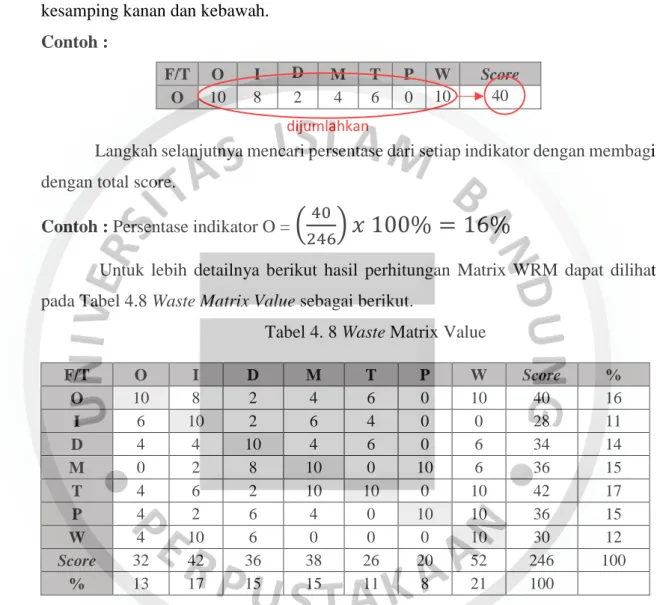
Value Stream Mapping Analysis Tools (VALSAT)
Dalam penelitian ini, peneliti membatasi penggunaan instrumen VALSAT hanya pada instrumen yang memiliki skor tertinggi.
Process Activity Mapping (PAM)
Identifikasi Penyebab Waste
Hal ini disebabkan oleh kurangnya perencanaan tata letak fasilitas kerja sehingga mengakibatkan jarak antar stasiun. Dari segi faktor manusia, penyebab permasalahannya adalah kurangnya tenaga kerja untuk pemeriksaan mutu, hal ini disebabkan oleh perusahaan tidak menambah tenaga kerja. Faktor manusia yang menyebabkan terjadinya pemborosan adalah operator yang tidak disiplin, hal ini disebabkan karena operator tidak menerapkan SOP pada saat bekerja.
Faktor lingkungan yang menjadi penyebab terjadinya pemborosan adalah kondisi tempat kerja yang kurang baik, hal ini diakibatkan karena kurangnya kesadaran pekerja dalam menata peralatan kerjanya. Timbulnya limbah juga disebabkan oleh faktor metode yaitu kurangnya standarisasi bahan baku yang diakibatkan oleh terbatasnya pengetahuan perusahaan dalam hal tersebut. Faktor manusia yang menjadi penyebab terjadinya pemborosan adalah kurangnya pengetahuan tenaga kerja atau pekerja, hal ini disebabkan karena kurangnya pelatihan sehingga tidak terjadi peningkatan pengetahuan pada pekerja.
Faktor metode juga menjadi penyebab terjadinya waste yaitu teknik pengelasan yang tidak tepat, hal ini disebabkan oleh kurangnya keterampilan dari pihak tukang las. Faktor material juga menjadi salah satu penyebab terjadinya pemborosan seperti material yang sulit diolah, hal ini disebabkan karena tekstur material yang tebal sehingga material tersebut mengalami tahapan proses pengelasan yang lama. Faktor lingkungan yang menyebabkan terjadinya pemborosan adalah lingkungan fisik kerja yang tidak nyaman hal ini disebabkan karena lantai produksi yang kecil dan pengap.
Faktor metode juga menjadi penyebab terjadinya pemborosan karena adanya teknik kerja yang salah, hal ini disebabkan oleh kurangnya keterampilan pada karyawan. Faktor material juga menjadi salah satu penyebab terjadinya pemborosan, seperti bahan keras yang sulit diolah yang disebabkan oleh tekstur bahan tersebut. Faktor metode juga menjadi penyebab terjadinya waste yaitu teknik pengelasan yang salah, hal ini disebabkan oleh kurangnya keterampilan dari pihak tukang las.
Faktor lingkungan yang menyebabkan terjadinya pemborosan adalah kondisi gudang yang kurang optimal, yaitu tidak adanya pengelolaan persediaan gudang. Faktor manusia yang menjadi penyebab terjadinya pemborosan adalah kurangnya tenaga kerja pada stasiun perakitan, hal ini disebabkan karena perusahaan tidak melakukan penambahan tenaga kerja, hal ini juga akibat dari adanya pembatasan pembayaran tenaga kerja oleh perusahaan sehingga perusahaan masih belum bisa menambah tenaga kerja. Faktor manusia penyebab terjadinya pemborosan adalah kurangnya tenaga kerja di bengkel pengecatan, hal ini diakibatkan oleh perusahaan yang tidak menambah tenaga kerja, hal ini juga akibat dari adanya pembatasan oleh perusahaan dalam membayar tenaga kerja sehingga perusahaan tetap tidak dapat menambah tenaga kerja.

Upaya Perbaikan
Jarak pergerakan material (A) Rencana produksi desain Menunggu pemeriksaan kualitas. B) Standardisasi dengan PDCA Bahan baku tidak memenuhi standar. Permasalahan perpindahan bahan/komponen/produk dalam jarak jauh terjadi sebanyak 5 kali, perpindahan bahan baku - pabrik 1 60 menit, dari pabrik 1 st. Sedangkan aliran bahan dari kedatangan bahan baku yang dikirim supplier ke gudang bahan baku dan dikirim ke produksi membutuhkan waktu 7200 menit atau 5 hari, dan jika bahan baku dikirim dari supplier ke gudang bahan baku lebih cepat (disarankan perbaikan point C) dan bisa langsung ditransfer ke bagian produksi, memakan waktu ± 1440 menit atau 1 hari dengan waktu transfer yang sama yaitu 60 menit.
Rak bahan baku juga dipindahkan ke sebelah rak bahan jadi, rak bahan baku akan diganti dengan stasiun pengecatan di sebelah Stasiun Perakitan. Selanjutnya, stasiun penandaan laser, pengemasan, dan gudang barang jadi akan digabungkan dengan gudang bahan baku, hal ini bertujuan untuk memaksimalkan ruang yang tersedia di gudang bahan baku dan mengoptimalkan jarak antar produk/komponen yang perlu dipindahkan. Dengan menerapkan poin-poin di atas sebagai saran perbaikan, perusahaan dapat menghilangkan permasalahan bahan baku yang tidak memenuhi standar, perubahan pada stasiun pengelasan yang lama, hasil pengelasan yang tidak tepat, dan stasiun pengepakan yang menunggu selesainya pemeriksaan mutu.
Upaya perbaikan selanjutnya adalah menambah lapangan kerja. Hal ini dilakukan ketika terjadi keterlambatan pasokan bahan baku sehingga menyebabkan karyawan menganggur. Karyawan dapat melakukan pekerjaan lain tanpa harus menunggu kedatangan bahan baku dan sistem ini berlaku di seluruh tempat kerja. Untuk menjamin penambahan pekerja di stasiun pengukuran dengan mengeluarkan pekerja dari stasiun pemotongan, hal ini dilakukan dengan asumsi hulunya dipercepat (usulan perbaikan di titik F).
Selain itu, bagian PPIC akan menambah pekerjaan pembelian untuk mencari sumber pasokan bahan baku dengan asumsi ketersediaan bahan baku sudah banyak tersedia di pasar dan media online, namun harus memperhitungkan biaya-biaya yang tidak terduga. Hal ini harus dilakukan untuk meminimalisir keterlambatan bahan baku, pengurangan waktu yang signifikan terjadi ketika produksi harus menunggu 7200 menit atau 5 hari dan jika pengiriman bahan baku lebih cepat maka produksi akan menunggu ± 1440 menit atau kurang lebih 1 hari (usulan perbaikan titik A dan keadaan masa depan Gambar 4.40). Tabel 4.32 memberikan alur waktu setiap stasiun kerja melakukan kolaborasi usulan perbaikan tata letak produksi dan selanjutnya akan dilakukan perencanaan pada stasiun tertentu.
Berdasarkan Tabel 4.32, pada stasiun pengelasan sebelum perbaikan, waktu akhir proses adalah 41,11 menit untuk komponen Front Dope dan 53,35 menit untuk komponen Rear Dope.
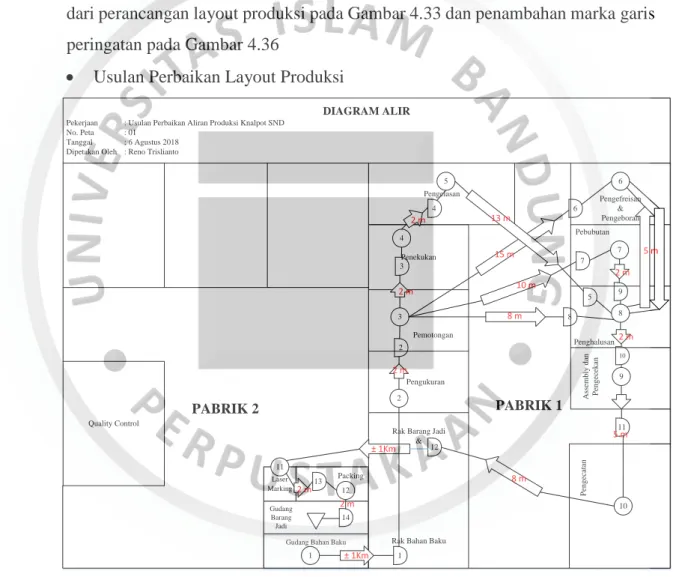
Pemetaan Value Stream Mapping Future State