The compressive strength of cement mortar and concrete with different percentages of nanocement was found. Hui li et al., [8], Maile Aiu and Huang [9] studied the effect of nano materials on the compressive strength of cement mortar.
Properties of materials
- Cement
- Fine aggregate
- Coarse aggregate
- Water
The special focus of the current investigation intends to highlight the replacement of cement with nano-cement in higher percentages. Therefore, an attempt was made to study the properties of nano-cement, properties of cement paste with nano-cement, properties of cement mortar with nano-cement and compressive strength of concrete with nano-cement.
Synthesis and characterization of nano cement 1 Production of nano cement
Microstructure analysis of nano cement
The specific surface area of cement was found to be 3700 cm2/g and for nano cement the specific surface area was found to be 485,000 cm2/g. It can be seen that the particles in nano size have much higher specific surface area compared to particles in micro size.
Tests on cement paste with nano cement: normal consistency and setting time
The initial setting time of nano cement paste was reduced to 30 minutes with 50% replacement, while the initial setting time of normal cement paste is 50 minutes. The final setting time of the cement paste with nano cement was reduced to 245 minutes at a replacement level of 50%.
Tests on cement mortar with nano materials
- Compressive strength of cement mortar by experiment
- Microstructure of cement mortar with nano cement
- Energy dispersive X-ray spectroscopy study on cement mortar with nano materials
- FTIR Spectrum for 28 days cement mortar with nano materials Fourier transform infrared spectroscopy is a technique used to obtain
EDAX images of cement mortar in which cement was replaced with NC are shown in Figure 9. FTIR transmission spectra of cement mortar in which cement was replaced with nano cement are shown in Figure 11.
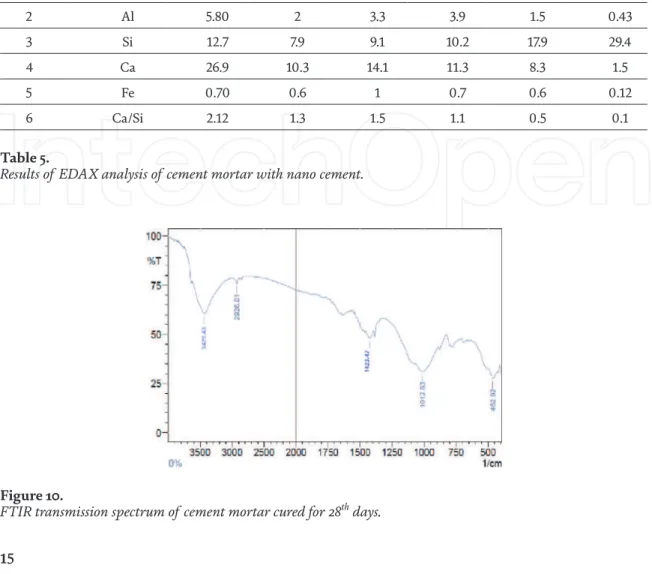
Compressive strength of concrete with nano materials
Table 8 shows that the nanocement is very effective in increasing the compressive strength of concrete.
Conclusions
Effect of grinding on materials
1 Department of Civil Engineering, Vignan's Lara Institute of Technology and Sciences, Vadlamudi, Guntur, Andra Pradesh, India. 2 School of Engineering and Technology, Karunya Institute of Technology and Sciences, Coimbatore, Tamil Nadu, India.
Effect of nano materials on properties of cement paste and cement mortar The normal consistency of cement paste with nano cement was found to range
The chemical properties of the nanoparticles were found to be the same as the particles before grinding.
Effect on compressive strength of concrete
Macro- and nanomaterials for improving mechanical and physical properties of cement kiln dust-based composite materials. Comparative study of the properties of nano-silica, silica fume and fly ash incorporated cement mortars.
Introduction
The cause of the NONRIVAL CEM I 52.5 N-sulphate resistance has been explained, despite the manufacturer's declared C3A content of up to 8% by weight. The first step of the external sulphate attack is the penetration of sulphate ions from the external environment into the concrete.
Experimental procedure 1 Materials
Casting and curing
Sulfate-resistant pozzolanic cement with C3A content in clinker ≤9 wt. %: marked with either CEM IV/A-SR or CEM IV/B-SR. The end result of each method is the knowledge of the increased chemical (e.g. sulfate) resistance of the tested cement system compared to the reference one.
Testing procedures for cement
Testing procedures for mortars conducted to sulfate attack
Results and discussion
Basic properties of cements and mortars after basic curing
The normal consistency of cements represents the water content per amount of cement in the cement paste required to achieve the standardized density [18], expressed as a percentage. The higher value of the normal consistency of N-cement means that to achieve the same density of the cement paste, a larger amount of water is required than with SR- and PC-cement.
Partially accelerated sulfate resistance test
The PC-mortar shows cracks on the surface of the test prisms, which spread into the interior of the mortar over time. PC-mortar contains the highest amount of sulfate attack reaction products compared to SR- and N-mortar, as previously confirmed by X-ray analysis. Phase composition of mortars after 5 years of exposure in 5% sodium sulfate solution and reference water at (20 ± 1) °C.
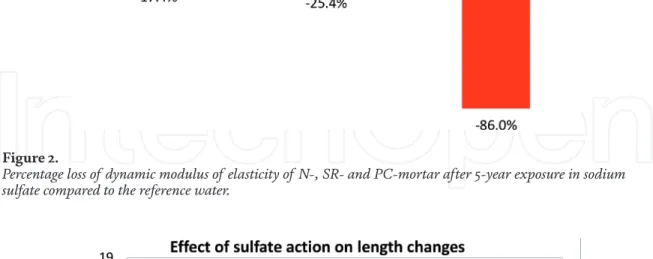
Ca(OH)2 required for the reaction with sulphate ions (see Eq. 1) is the basic condition for suppressing the aggressive effect of sulphate solution on the NONRIVAL CEM I 52.5 N-containing mortar. This is considered to be a new effective reaction mechanism that eventually leads to an increased sulphate resistance of NONRIVAL CEM I 52.5 N to the same level as that of a sulphate-resistant cement without C3A. Sulfate Resistant Cement (SR) is characterized by blocking gypsum formation and subsequent ettringite due to the absence of C3A, while NONRIVAL CEM 52.5 N blocks the formation of these reaction products by minimizing the Ca(OH)2 content through the presence of active submicron - based pozzolana.
Conclusions
The development of the uniform method, standardized at best in EN or ASTM, even a common one, for the evaluation of the resistance of concrete to sulfate attack by an accelerated test procedure is required. The M5 grade samples mixed with ninety percent concrete and left with nanosilica were found to have a finer working height in both standards and standards when collected with the conventional cement mortar. The density of concrete and cement can be improvised by adding both nano and micro NS, which tend to act as a filler material, resulting in higher quality [4–17].
Procedure
- Blending of nano silica with cement
- Hardening or setting interval (setting time)
- Strength determination (compressive strength)
- Strength determination (flexural strength)
- Durability aspect
- Temperature assessment
Expansion of nano-silica to solidify concrete and cement mortar then resulted in the improvement of sharp and long features, and overuse of nano-silica results in a decrease in quality. Nanosilica greatly improved qualities of cement and concrete in fresh and solidified phase and in durability under various environmental conditions. The mixed samples of M0 as well as M5 were tested for temperature control at 900 °C in a suppressor.
Deliberation of verdict
- Hardening or setting interval (setting time)
- Analysis of strength (compression)
- Analysis of flexural strength
- Probes on durability aspect .1 Corollary of magnesium sulphate
- Corollary of hydrochloric acid
- Assessment of temperature corollary
Also, a high in silicate hydroxide of calcium content can be seen in Figure 5 compared to Figure 4. An extra amount of silicate hydroxide of calcium was seen due to the action of hydroxides of calcium and oxides of silica. Also, hydroxide and silicate hydrate of magnesium are directed as a result of the reaction of MgSO4 with hydroxide and silicate hydroxide of calcium.
Conclusion
Ou, A study on mechanical and pressure-sensitive properties of cement mortar with nanophase materials, Cem. Repette, Effect of nanosilica on rheology and fresh properties of cement pastes and mortars, Constr. The different types of cement and their applications such as Portland, Siliceous fly ash, lime, slag and Fume silica cement differ by the amount of SiO2, Al2O3, Fe2O3, CaO, MgO, SO3 and other materials such as Na2O and K2O composition [3] .
Methodology
- Cement production simulation
- Aspen Hysys simulation
- Multivariate design of experiment
- Model fitting and statistical analysis
- Simulation and optimisation of cement flow
- Surface plots
- Energy optimization
Contour area graph showing the effects of CaO flow and SiO2 flow on cement flow. Response plane graph of the effects of CaO and SiO2 mass flow on cement production. Optimization graph showing the effects of CaO flow and SiO2 flow on cement flow.
Recommendations
Peculiarities of the synthesis of clinker from Portland cement in the presence of a significant amount of SO 3 in the raw material mixture. According to the literature, the synthesis of Portland cement clinker in the presence of a significant amount of sulfur oxides is difficult. The reasons for the decrease in the content of alite (C3S) in Portland cement clinker with an increase in the content of SO3 in it cannot be found in the literature.
Materials and experiment methods
When the SO3 content of the clinker is less than 2.0%, it has a positive effect on the synthesis of Portland cement clinker, since the alkali metal sulfates formed in its presence are effective melts that reduce the temperature for the appearance of the liquid phase and its viscosity, which provides accelerated synthesis of clinker minerals [5, 6]. If the SO3 content of the clinkers exceeds 2.0%, there are negative phenomena associated with both the quality of Portland cement clinker and its production technology. The reason for the decrease in C3A content in high sulfate clinkers is the isomorphic substitution of silicon for aluminum in silicate phases.
Experimental results and discussion
Analysis of the melt heated to a temperature of 1600°C indicates that alite is formed during this superheating, but there is 6.2% free lime in the clinkers. In the presence of calcium monoaluminate, the formation of C3A and C4AF is thermodynamically impossible (reaction no. 4-6). Free lime begins to accumulate in the clinkers from the decomposition start temperature of calcium carbonate to the appearance of the liquid phase due to the difference in the lime content of the tricalcium aluminate C3A that is accepted in.
Example of calculation of high-sulphate raw material mixture No. 1 At the first stage on the basis of raw components the chemical composition of
The change in the intensity of the diffraction maxima of the main phases of the clinker produced in accordance with correction calculation no. The calculated composition of the raw mixture for obtaining alite Portland cement clinker and its chemical composition. To determine the actual phase composition of clinker produced in accordance with correction calculation no.
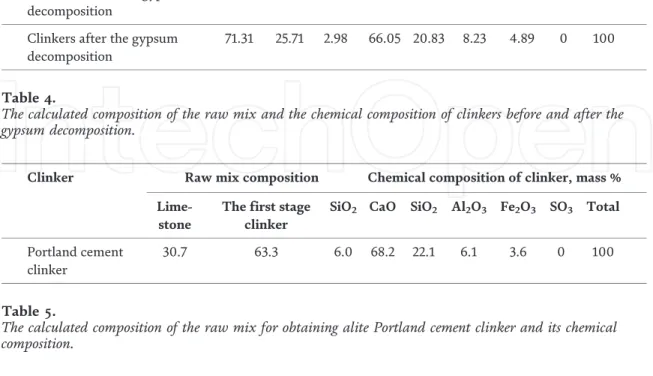
Example of calculation of high-sulphate raw material mixture No. 2 At the first stage on the basis of raw components the chemical composition of
The amount of corrective additives is equal to the difference between the amount of raw components calculated by formulas (19) and (20) and the amount of raw components calculated at the first stage and shown in Table 9. The intensity of the diffraction maximum with d = 3.72 Å, which is characteristic for C3A3C S, increases up to a temperature of 1300°C, above which temperature it is not fixed, indicating the decomposition of CaSO4 according to the reaction (No. 6) and the consequent decomposition. The amount of clay removed from the raw mix is correlated with the amount of mixed additives introduced into the raw mix, i.e.
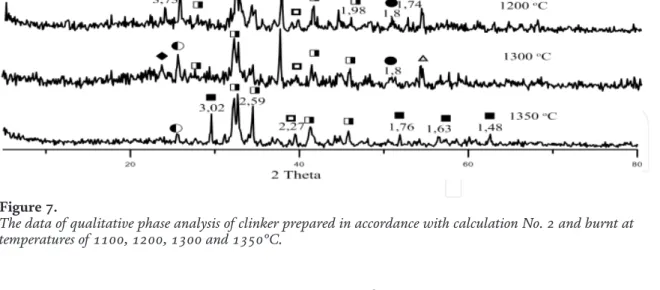
С onclusion
Data collections
The calculated costs in Table 2 are subject to some conversions as the consumption of coal, fuel and energy is shown in tons. Natural gas costs are given in $/ft3 and heating oil costs are given in $ per litre. For the two cases where volume is used, the amount consumed is converted from tons to ft3 and liters for natural gas and fuel oil respectively.
Results
Flue gas composition
The following costs of materials for fuel oil, natural gas and coal were respectively as obtained [23–25];.
Discussion of results
Natural gas is the most readily available and highly economical source of energy used for the manufacture of cement, compared to coal and fuel oil. Carbon dioxide emissions are also high in coal and fuel oil compared to natural gas. Similarly, the oxygen content is high in natural gas compared to coal and fuel oil.
Conclusion
Recommendations
2 Department of Chemical Sciences, School of Pure and Applied Sciences, Lagos State Polytechnic, Ikorodu, Nigeria. Bafuwa, "Energy and Cost Analysis of Cement Production Using Wet and Dry Processes in Nigeria," Energy Power Eng., vol. Gold, Auditing and energy recovery for dry-type cement rotary kiln systems. Energy Conversion and.