Optimasi Waktu Pelaksanaan Coal Handling System di PLTU Cilacap dengan Menggunakan Lean Six Sigma
Teks penuh
Gambar

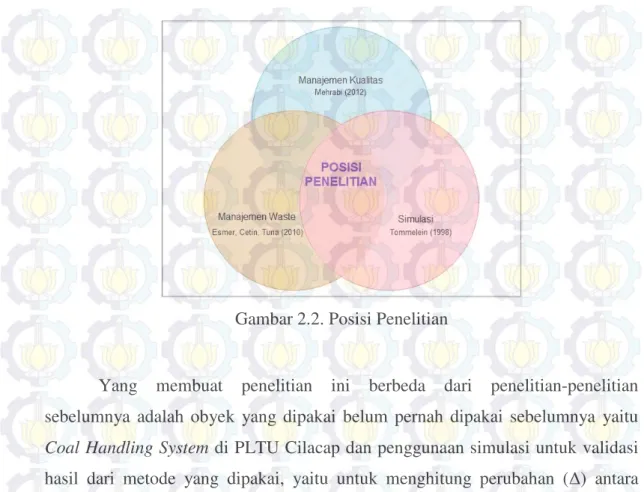


Dokumen terkait
3Retnowulan Sutantio dan IskandarOeripkartawinata,Hukum Acara Perdata dalam Teoridan Praktik,Mandar Maju,
3) Pembelajaran berbasis TIK harus banyak distimulus oleh dosen pengampu. 4) Hanya beberapa orang mahasiswa yang aktif. 5) Mahasiswa banyak sangat malu untuk
Hal ini tidak masalah jika perangkat IoT hanya 2 atau 3 perangkat namun akan menjadi masalah jika perangkat Io Tada diberbagai tempat seluruh penjuruh dunia.Solusi yang
SENARAI KES PERBICARAAN MAHKAMAH TINGGI DI HADAPAN Y.A DATO’ VAZEER ALAM BIN MYDIN MEERA.. HAKIM MAHKAMAH TINGGI MALAYA, MELAKA
“Alhamdulillah sudah ada beberapa alumni kami yang kuliah di UNAIR, beberapa anak sempat kasih kabar kepada kami bahwa sudah lulus dengan predikat yang memuaskan,”
Survey pendahuluan yang dilakukan peneliti pada tanggal 28 April sampai dengan 4 Mei 2012 di SD 1 & SD 2 Yayasan Perguruan Al-Azhar Medan, di peroleh data bahwa dari 6 guru
Perancangan Konseptual adalah suatu proses dalam membuat sebuah model informasi yang digunakan pada sebuah perusahaan, dan terlepas dari semua pertimbangan – pertimbangan
Lampiran 17 yang menunjukkan bahwa berdasarkan hasil kajian, 50% responden mengatakan ketua sudah menerapkan sistem belajar dan bekerja dengan baik, ketua menggunakan beragam