We draw some useful insights based on the implementation of lean and the challenges faced by SMEs. This section highlights the implementation of Lean at a small food processing company in southern India.
TOP 1%
Introduction
- Lean (production, manufacturing or management)
- Kaizen
This chapter presents the methodologies of Lean and Kaizen, their contribution in the business field and their future potential contribution to the field of management. It was introduced that these two methodologies provided valuable assets in the field of management.
Introduction to Kaizen and Lean 1 Lean
- Kaizen
- Lean-Kaizen
The team leader is often the manager, supervisor or engineer who is responsible for improving the process. So the Lean-Kaizen approach is required to be implemented to produce quality products by eliminating waste Muda) throughout the organization's system [31].
The contribution of the methodologies 1 Lean
- Kaizen
Therefore, continuous improvement approaches have been formally adopted in the public sector worldwide in an attempt to improve service quality and streamline processes, often in response to cuts in public spending budgets imposed by governments. A new initiative that contributes to researching lean in the public sector is the project "Lean in public sector" (http://leaninpublicsector.org/).
Conclusion
- The present and future of the methodologies
- Research background of lean
- What is lean?
- The 9 principles of lean manufacturing
- Lean tools and techniques
- Conclusion
Melton, "The Benefits of Lean Manufacturing: What Lean Thinking Brings the Process Industry". Akhil, "A qualitative study of the barriers to lean manufacturing implementation: An Indian context (NCR Delhi region)", The International Journal of Engineering & Science, vol.
Literature review
For the most part, manageable execution is concerned with a company's ability to simultaneously consider and balance financial, environmental, and social issues when transferring items or administrations to increase valuation [7-9]. Accordingly, we seek to see if our research can uncover a pathway for sustainability-focused manufacturers to adjust benefit enhancement and natural manageability, which is central to policy makers and the scientific community [10, 11].
Methodology
Of these, one of the returned responses needed answers to a few queries and was consequently eliminated from the final sample. To assess convergent validity, we initially examined the unidimensionality of the measures by means of principal component analysis. Following the suggestions of Carmines and Zeller [20], the items for each of the constructs were researched independently.
For all constructs, the Kaiser-Meyer-Olkin measure of sampling adequacy was above the suggested threshold of 0.5, and Bartlett's test of sphericity returned p values below 0.001. They recommend that to guarantee discriminant validity, the AVE for each construct should be greater than the square of the bivariate relationships of the construct with different constructs. To test reliability, Cronbach's alpha coefficient was determined for each of the summed scales.
Results and discussion
This review aimed to cover the research gap regarding the intelligent impacts of lean manufacturing on operational performance, which was recently pointed out by Buer, Strandhagen and Chan [25], as well as the tendency to work as barriers in previous comparative research. . Rinehart, Huxley and Robertson [26] unequivocally recommended that lean manufacturing will be the “standard manufacturing method of the twenty-first century”. The operational benefits of using lean manufacturing have been demonstrated in various past investigations and the implications of the current investigation confirm these findings.
In this context, lean tools and approaches contribute to the development of the supply chain decision-making process in order to achieve a better performance of textile and clothing companies in today's complicated world. Our choice of the textile and clothing sector corresponds to the problem we are studying of a production chain with multiple actors geographically spread around the world. Moreover, the nature of the textile product, which is not a homogeneous product, but very diverse, short-lived and subject to fashion effects as described in the bibliographic references [1-7].
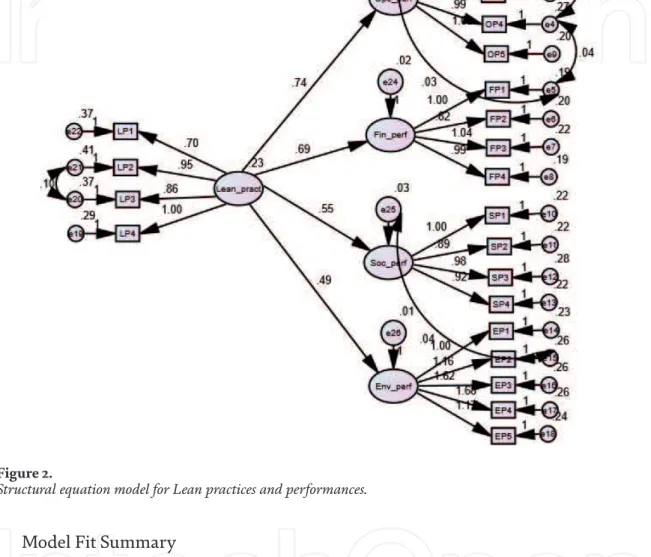
Phase “ define ”
- The problem statement
- Challenges of the proposed planning approach
- The process definition
The activities of these actors must be optimized to determine the appropriate supply for each unit in the production chain. A presentation of the different types of coordination at the supply chain level and a review of the literature on this aspect is detailed by [14, 15]. It is therefore necessary to define production and distribution planning models that take into account the specificity of the apparel supply chain.
The main objective of the current study is to reduce the total cost of the supply chain by about 10%. Defining a high-level process map gives the team a bird's-eye view of the project. One of the most commonly used high-level maps is the SIPOC, which details supplier, input, process, output and customers.
Phase “ measure ”
- The measurement system analysis
- Data collection plan
- Current situation and the gap with the desired one
Given the rolling horizon principle, the decisions made during the first week are fixed and the associated costs are recorded. The length of this horizon is determined according to the position of the first week of the month. We denote the weeks in the operational planning model with a pair (t, s), where s is the position of the week in month t.
For the operational planning model, detailed in Appendix C, the length of the planning horizon is justified by the fact that POs resulting from tactical planning must be reliably detailed at the operational level. In order to properly place decisions at the tactical level, the operational planning horizon must therefore reach the end of the month. Storage costs are defined based on the average storage level between the start and end of the period.
Phase “ analyze ”
Our approach evaluates the current situation of the clothing manufacturer incurring a logistics cost equal to 2864 k€ acquired for the 6 months. This is mainly due to the due date position of the POs throughout the month. Indeed, since the productions planned over a month in the internal units are detailed per week at the operating level, in some cases it seems mandatory to produce massively during the first weeks of the month to meet the predetermined delivery dates.
Meanwhile, for the remaining weeks of the month, the domestic production capacity is underutilized. In this case, the ROs, which reach an operational level, are assigned to subcontractors as the internal production capacity is fully utilized by the production of pre-season items deployed at the tactical level. In order to analyze the current situation of the textile and clothing supply chain and try to identify the root causes of the performance decline in this area, we establish the following Ishikawa diagram shown in Figure 5.
Phase “ improve ”
- The reserve production capacity estimation
- Production and distribution planning using a fixed reserve production capacity
- Production and distribution planning with a variable monthly reserve production capacity
Now let's see the operational level, the RPC considered at the tactical level is released. The impact of considering the RPC at the tactical planning level on supply chain costs is examined. The percentage of available internal production capacity for PM planning is therefore a fixed value (α).
First, considering the monthly RPC variable at the tactical level makes better use of internal production capacity. When α equals 100%, ROs are subcontracted because the internal production capacity is overloaded with POs. In conclusion, the use of variable RPC at the tactical level enables efficient use of internal production capacity and optimizes the distribution of production to subcontractors.
Phase “ control ”
- Sensitivity analysis of demand
- Sensitivity analysis of transportation and subcontracting costs
However, the quantities produced in subcontracted production units are particularly high when considering a fixed α equal to 80% at the tactical level. The same trends are observed for transportation and subcontractor cost savings are also obtained when RPC is considered at the tactical planning level (Figure 10). As a result, at the tactical planning level, some internal production capacity is unused; therefore enforcing RPC is pointless.
This promotes the use of an RPC to avoid using full production capacity at the tactical level. In these situations, spare capacity appears to be an essential consideration to ensure the use of foreign subcontracting (which is cheaper than domestic subcontracting) at the tactical level. Indeed, when demand or shipping or subcontracting costs increase, our approach allows us to adequately place urgent and unpredictable orders that reach the operational level at the lowest cost.
Conclusions
Variable and fixed distribution costs from premises to warehouses (CTkjplt, CFkjplt) and from warehouses to retailers (CSjiplt, CFSjiplt) are also addressed. Z1kjplt: quantity of product p to deliver, via transport mode l, from manufacturing unit k to warehouse j over period t,. Z2jiplt: quantity of product p to deliver, via transport mode l, from warehouse j to retailer i over period t,.
N1kjlt: quantity transported from production unit k to warehouse j in period t using transport method l. N2jiplt∈,SVkt∈ k∈K,j∈J,p∈P,t∈T,l∈Landi∈I (12) The purpose of the objective function is to reduce total costs consisting of installation costs, variable production costs, subcontractor costs , underutilization costs, inventory holding costs, transportation costs from production units to warehouses, and transportation costs from warehouses to retailers. Constraints (1) determine the stock level of product p in warehouse j at the end of period t.
The set of periods in the operational planning model
Constraints (2) guarantee that the total quantity stored over each period is limited by the storage capacity.
The operational planning model
- Background of lean production and lean construction: Interaction in terms of tools, techniques, and methods
- Lean methods: how tools and techniques are evolved
- The last planner system (LPS)
- Mistakeproofing (Poka yoke)
- Visual management
- Target value design (TVD)
- Value stream mapping (VSM)
- Gemba walks
- Daily huddle meetings
- Conclusions
- Problem statement
- Conceptualisation
- Evolution trajectories
- Management levels
- Formalisation modes
- The evolution management system
- The strategic orientation level
- The migration plan level
- The projects portfolio level
- Argumentation
- Competitive aspects
- Self-evaluation and learning capabilities
- Evolution management and continuous improvement
- Conclusions
Then, several management levels are proposed to manage the evolution trajectory of the system. The first corresponds to the state of the system at the moment it is examined (t = 0). The first corresponds to the control of the path between the current state and the target.
Thus, the state of the system is characterized by the value of its performance vector. Finally, looking at the projects means observing the evolution of the system in an operational way. This model must also take into account the shortcomings observed in the current state of the system (as-is model) and the possible evolution needs indicated by the company.
This sequence makes it possible to link all this level to the strategic analysis of the company. It is built on the basis of the action plan provided by the higher level.
