The effect of cutting parameter on surface roughness during end milling of AISI D2 tool steel.
Teks penuh
Gambar


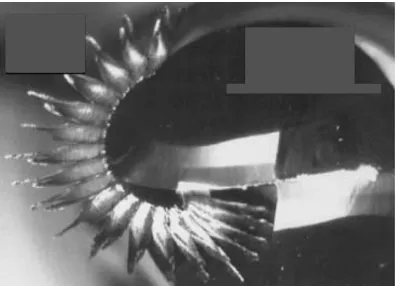

Dokumen terkait
2 Influence of cutting parameter on flank wear, Vb when milling Aluminium 6061 – T6 with PVD tools; (a) cutting speed against feed rate (b) feed rate against depth of cut.. 3 shows
This project title is a Cutting Parameter Optimization for Surface Finish in Drilling Process of AISI D2 Tool Steel using Taguchi method.. The existing method that is currently used
The scope of this project is to study the cutting parameters which spindle speed and feed rate and to study the surface roughness of AISI 1045 carbon steel by using wet
The effect of prominent milling parameters, namely cutting speed, feed rate, depth of cut (DOC), and width of cut (WOC) were studied to evaluate their effects on tool life,
• To analyze the effect of CNC milling parameters such as cutting speed, depth of cut, and feed rate to the surface roughness and microhardness of 6061 T6..
The focus of the study is on the quality of the surface roughness respective to varying depth of cut given other parameters (spindle speed, feed rate, surface speed, tool rake angle
Using Taguchi design, Fuh and Wu [6] included cutting speed, feed rate, depth of cut, tool nose radius, and flank as control factors for the creation of a statistical model to
It can be concluded that pocket working on CNC milling machines with variations in spindle speed and cutting direction results in normalization of the roughness level of N6 as a result