PRA RANCANGAN PABRIK
PEMBUATAN BIOGAS DARI HASIL FERMENTASI
THERMOFILIK LIMBAH CAIR PABRIK KELAPA
SAWIT SISTEM RECYCLE MENJADI ENERGI
LISTRIK UNTUK KAPASITAS 45 TON TBS/JAM
TUGAS AKHIR
Diajukan untuk Memenuhi Persyaratan
Ujian Sarjana Teknik Kimia
DISUSUN OLEH:
FEBRIANSYAH ANSARI ROSDI
NIM: 080405085
DEPARTEMEN TEKNIK KIMIA
FAKULTAS TEKNIK
UNIVERSITAS SUMATERA UTARA
MEDAN
KATA PENGANTAR
BismillahirrahmanirrahimAssalammu‘alaikum Wr. Wb
Dengan mengucapkan puji syukur kehadirat Allah SWT atas limpahan rahmat, ridho dan karunianya, sehingga penulis dapat menyelesaikan Skripsi ini dengan judul “Pra Rancangan Pabrik Pembuatan Biogas Dari Hasil Fermentasi Thermofilik Limbah Cair Pabrik Kelapa Sawit Sistem Recycle Menjadi Energi Listrik Untuk Kapasitas 45 Ton TBS/Jam.
Pra rancangan pabrik ini disusun untuk melengkapi tugas-tugas dan merupakan salah satu syarat untuk menempuh ujian sarjana pada Departemen Teknik Kimia, Fakultas Teknik, Universitas Sumatera Utara.
Akhir kata kepuasan dan kebahagian penulis dalam menyelesaikan skripsi ini tidak terlepas dari bantuan berbagai pihak. Oleh karena itu, pada kesempatan ini penulis mengucapkan terima kasih kepada semua pihak yang telah membantu dan membimbing penulis selama mengerjakan skripsi. Penulis menyadari sepenuhnya tanpa dukungan dan bantuan mereka, penulis tidak mungkin dapat menyelesaikan skripsi ini. Perkenankanlah penulis mengucapkan terima kasih kepada :
1. Bapak Dr. Eng. Irvan, MSi sebagai Dosen Pembimbing I sekaligus Ketua Departemen Teknik Kimia FT USU yang telah membimbing, memberikan masukan dan arahan selama menyelesaikan skripsi ini.
2. Bapak Ir. Bambang Trisakti, M.Si sebagai Dosen Pembimbing II sekaigus dosen penguji I yang telah membimbing, memberikan masukan dan arahan selama menyelesaikan skripsi ini.
3. Ibu Ir. Renita Manurung, MT sebagai Koordinator Tugas Akhir Departemen Teknik Kimia, Fakultas Teknik, Universitas Sumatera Utara.
4. Ibu Dr. Ir. Fatimah, MSi, Sekretaris Departemen Teknik Kimia, Fakultas Teknik, Universitas Sumatera Utara.
5. Ibu Dr. Ir. Rosdanelli Hasibuan, MT sebagai Dosen Penguji II yang telah memberikan saran dan kritik pada Tugas Akhir saya ini.
7. Dan yang paling Teristimewa Ayahanda tercinta Sariono Saputro dan Ibunda tercinta Hj. Rosida Ritonga yang selalu sabar dan mendoakan, memotivasi penulis dalam menyelesaikan skripsi.
8. Adik Spesial dihati yaitu Refina Sari Siregar, ST yang telah memberikan motivasi dan semangat kepada penulis selama mengerjakan Tugas Akhir ini. 9. Seluruh staf pengajar dan pengurus administrasi Departemen Teknik Kimia
Universitas Sumatera Utara.
10. Rekan seperjuangan Vandy Desriandi, atas kerjasamanya dalam penulisan tugas akhir ini dalam suka dan duka.
11. Teman-teman seperjuang penulis, Juki purnomo, Rizky martua Hsb, Edenta Ginting, Ahmad Syahrun Hsb, Alexander, Edwin Fauzi, Rendy ramadhan, yang tergabung dalam kelompok “PASKAS” , Cristopel Tobing, Rossi Wedana Tarigan dan teman-teman Eks-D4 2005 semua yang terus menyemangati dan selalu berbagi ilmu kepada penulis selama penyusunan skripsi.
12. Para pembimbing tambahan, Halim Cahjadi, ST, Riki Handoko, ST, Azlansyah, ST, Amalia Yolanda, ST, Senafati, ST, Dahyat, ST, yang telah memotivasi dan membantu dalam kelengkapan bahan penyusunan skripsi.
13. Pasukan LPPM yaitu bg Joel “Gondes”, Elton Jhon Situmeang, Dedy Anwar, Alfy syahrin, nanta “blak-blakan”, Basril, dan Jhon Almer. dan adik-adik junior 2006, 2007, 2008, 2009, 2010 semua yang telah memberikan bantuan dan doa kepada penulis.
14. Serta pihak-pihak yang telah ikut membantu penulis namun tidak tercantum namanya.
Dalam penyusunan tugas akhir ini, penulis menyadari masih terdapat banyak kekurangan. Oleh karena itu, penulis sangat mengharapkan saran dan kritik yang bersifat konstruktif demi kesempurnaan penulisan ini. Akhir kata, semoga laporan ini dapat bermanfaat bagi kita semua. Terima kasih.
Medan, 20 Juli 2011 Penulis,
INTISARI
Palm Oill Mill Effluent (POME) merupakan hasil buangan limbah cair kelapa
sawit yang mempunyai kandungan senyawa glukosa, protein dan karbohidrat tinggi dan apabila diolah dengan baik maka dapat menghasilkan Biogas. Biogas ini selanjutnya akan mengalami proses purifikasi sebelum disintesa menjadi senyawa kimia baru yang secara luas dibutuhkan dalam kehidupan manusia, Selama ini biogas dikenal hanya dimanfaatkan sebagai bahan bakar keperluan rumah tangga khususnya untuk memasak saja, padahal biogas bisa juga dimanfaatkan sebagai sumber energi pembangkit generator listrik.
Pra rancangan pabrik pembuatan Biogas menjadi energi listrik ini direncanakan menghasilkan listrik dengan kapasitas 76,043 MWh/hari dan beroperasi selama 365 hari dalam satu tahun.
Lokasi pabrik yang direncanakan adalah di Perbaungan, Sumatera Utara dengan luas areal 3.180 m2. Tenaga kerja yang dibutuhkan 37 orang dengan melakukan kerjasama dengan PTPN IV Adolina dalam hal pengolahan limbah.
Hasil evaluasi ekonomi Pabrik Pembuatan Biogas menjadi Energi listrik ini sebagai berikut:
• Total Modal Investasi : Rp 172.222.963.756,-
• Total Biaya Produksi : Rp 76.229.242.231,-
• Hasil Penjualan : Rp 141.554.154,-
• Laba Bersih : Rp 45.516.301.047,-
• Profit Margin (PM) : 45,92 %
• Break Even Point (BEP) : 53,42 %
• Return on Investment (ROI) : 26,43 %
• Pay Out Time (POT) : 3,78 tahun
• Return on Network (RON) : 44,05 %
• Internal Rate of Return (IRR) : 42,07 %
DAFTAR ISI
Hal
KATA PENGANTAR ...i
INTISARI ... iii
DAFTAR ISI ... iv
DAFTAR TABEL ... xiii
DAFTAR GAMBAR ... x
2.8.1 Deskripsi Proses Pra Rancangan Pabrik Pembuatan
DAFTAR TABEL
Tabel 2.1 Komposisi Biogas ... II-1 Tabel 2.2 Komposisi Kimia Limbah Cair POME ... II-8 Tabel 2.3 Karakteristik Limbah POME dan Baku Mutu Limbah ... II-9 Tabel 3.1 Neraca Massa pada Tangki Neutralisasi ...III-1 Tabel 3.2 Neraca Massa Tangki Pencampur ...III-1 Tabel 3.3 Neraca Massa Reaktor Fermentasi ...III-2 Tabel 3.4 Neraca Massa Bak Sedimentasi ...III-2 Tabel 3.5 Neraca Massa Water Trap...III-3 Tabel 3.6 Neraca Massa Desulfurisasi ...III-3 Tabel 3.7 Neraca Massa Generator ...III-3 Tabel 4.1 Neraca Energi Tangki Neutraliser (M-01) ... IV-1 Tabel 4.2 Neraca Energi Tangki Pencampur (M-02) ... IV-1 Tabel 4.3 Neraca Energi Fermentor (R-01/R-02) ... IV-1 Tabel 6.1 Daftar Penggunaan Intrumentasi pada Pra-Rancangan Pabrik
DAFTAR GAMBAR
DAFTAR LAMPIRAN
LAMPIRAN A PERHITUNGAN NERACA MASSA ... LA-1 LAMPIRAN B PERHITUNGAN NERACA PANAS ... LB-1 LAMPIRAN C PERHITUNGAN SPESIFIKASI PERALATAN ... LC-1 LAMPIRAN D PERHITUNGAN ASPEK EKONOMI ... LD-1
INTISARI
Palm Oill Mill Effluent (POME) merupakan hasil buangan limbah cair kelapa
sawit yang mempunyai kandungan senyawa glukosa, protein dan karbohidrat tinggi dan apabila diolah dengan baik maka dapat menghasilkan Biogas. Biogas ini selanjutnya akan mengalami proses purifikasi sebelum disintesa menjadi senyawa kimia baru yang secara luas dibutuhkan dalam kehidupan manusia, Selama ini biogas dikenal hanya dimanfaatkan sebagai bahan bakar keperluan rumah tangga khususnya untuk memasak saja, padahal biogas bisa juga dimanfaatkan sebagai sumber energi pembangkit generator listrik.
Pra rancangan pabrik pembuatan Biogas menjadi energi listrik ini direncanakan menghasilkan listrik dengan kapasitas 76,043 MWh/hari dan beroperasi selama 365 hari dalam satu tahun.
Lokasi pabrik yang direncanakan adalah di Perbaungan, Sumatera Utara dengan luas areal 3.180 m2. Tenaga kerja yang dibutuhkan 37 orang dengan melakukan kerjasama dengan PTPN IV Adolina dalam hal pengolahan limbah.
Hasil evaluasi ekonomi Pabrik Pembuatan Biogas menjadi Energi listrik ini sebagai berikut:
• Total Modal Investasi : Rp 172.222.963.756,-
• Total Biaya Produksi : Rp 76.229.242.231,-
• Hasil Penjualan : Rp 141.554.154,-
• Laba Bersih : Rp 45.516.301.047,-
• Profit Margin (PM) : 45,92 %
• Break Even Point (BEP) : 53,42 %
• Return on Investment (ROI) : 26,43 %
• Pay Out Time (POT) : 3,78 tahun
• Return on Network (RON) : 44,05 %
• Internal Rate of Return (IRR) : 42,07 %
BAB I
PENDAHULUAN
1.1Latar Belakang
Pembangkit listrik sangat diperlukan untuk menggerakkan roda pembangunan di semua bidang. Pada saat sumber energi suatu pembangkit melimpah, di saat itu pula biaya pembangkitan akan murah. Begitu juga sebaliknya, pada saat sumber energi mulai berkurang, maka di saat itu pula biaya pembangkitan akan menjadi mahal. Konsumsi listrik Indonesia setiap tahunnya terus meningkat sejalan dengan peningkatan pertumbuhan ekonomi nasional. Kebutuhan listrik untuk masyarakat maupun industri diperkirakan belum akan tercukupi (Antara, 2008). Untuk itu, perlu dilakukan pencarian sumber baru untuk mencukupi kebutuhan listrik.
Salah satu sumber energi yang dapat digunakan untuk mencukupi kebutuhan listrik adalah biogas. Selama ini biogas dikenal hanya dimanfaatkan sebagai bahan bakar keperluan rumah tangga khususnya untuk memasak saja, padahal biogas bisa juga dimanfaatkan sebagai sumber energi pembangkit generator listrik. Biogas sebenarnya sudah mulai dimanfaatkan sejak beberapa puluh tahun yang lalu, namun tidak banyak digunakan oleh masyarakat. Biogas yang dikenal masyarakat lebih banyak dihasilkan dari pengolahan kotoran ternak atau kotoran manusia. Sebenarnya biogas juga bisa dihasilkan dari biomassa yang lain. Gas metana (CH4) yang merupakan komponen utama biogas adalah gas yang dihasilkan dari perombakan anaerobik senyawa-senyawa organik, seperti limbah cair kelapa sawit. Indonesia saat ini merupakan negara produsen minyak kelapa sawit mentah (crude palm oil, CPO) terbesar di dunia. Luas areal perkebunan sawit di Indonesia terus bertumbuh dengan pesat, demikian pula produksi dan ekspor minyak sawitnya. Dari data terakhir yang kami peroleh bahwa Luas areal tanaman kelapa sawit meningkat dari 5,45 juta hektar pada tahun 2005 menjadi 7,5 juta hektar pada tahun 2009. Dalam kurun waktu yang sama, produksinya berupa CPO dan CPKO (minyak inti sawit mentah), meningkat dari 11,8 juta ton menjadi 18,6 juta ton (Departemen Pertanian, 2009).
rata-rata sebesar 25.000 mg/l. Saat ini, diperkirakan jumlah limbah PKS di Indonesia yang berupa TKKS sebesar 15,2 juta ton/tahun dan POME mencapai 28,7 juta ton /tahun. Secara alami gas metana dihasilkan pada kolam-kolam pengolahan limbah cair Pabrik Kelapa Sawit (PKS). Limbah cair yang ditampung di dalam kolam-kolam terbuka akan melepaskan gas metan (CH4) dan karbon dioksida (CO2). Kedua gas ini merupakan emisi gas penyebab efek rumah kaca yang berbahaya bagi lingkungan. Selama ini kedua gas tersebut dibiarkan saja menguap ke udara. Berdasarkan penelitian, limbah cair kelapa sawit termasuk sumber energi alternatif (biogas) yang besar konversinya yaitu sebesar 20 m3 biogas/m3 limbah cair (Asian Palm Oil, 2007). Konversi listrik sekitar 6 kWh/ m3 biogas (Green Indonesia, 2008)
1.2Perumusan Masalah
Konsumsi listrik Indonesia setiap tahunnya terus meningkat sejalan dengan peningkatan pertumbuhan ekonomi nasional. Untuk itu, perlu dicari solusi untuk menanggulangi kebutuhan listrik di Indonesia. Limbah cair kelapa sawit yang selama ini pemanfaatannya belum optimal dapat digunakan sebagai sumber kebutuhan listrik. Untuk itu, perlu dibuat suatu pra rancangan pabrik untuk mengolah limbah cair kelapa sawit menjadi gas metana sebagai sumber kebutuhan listrik. Produk utama dari proses ini adalah listrik.
1.3Tujuan Pra Rancangan Pabrik
Ada beberapa tujuan pembuatan pra rancangan pabrik pembuatan biogas dari limbah cair kelapa sawit dengan metode recycle sebagai sumber kebutuhan listrik, yaitu :
1. Untuk memberikan informasi awal tentang kelayakan pendirian pabrik pembuatan biogas dari limbah cair kelapa sawit dengan metode recycle sebagai sumber kebutuhan listrik.
2. Untuk memberikan informasi tentang perkiraan tata rancangan pabrik pembuatan biogas dari limbah cair kelapa sawit.
1.4Manfaat Pra Rancangan Pabrik
BAB II
TINJAUAN PUSTAKA
2.1 Pengertian Biogas
Biogas adalah gas yang dihasilkan ole dari bahan-bahan domestik (rumah tangga), sampah biodegradable atau setiap limbah organik yang
biodegradable dalam kondisi anaerobik. Kandungan utama dalam biogas adalah
bersih daripad karbon dioksida yang lebih sedikit. Biogas yang dihasilkan oleh aktivitas sangat populer digunakan untuk mengolah limbah biodegradable karena bahan bakar dapat dihasilkan sambil menghancurkan bakteri patogen dan sekaligus mengurangi volume limbah buangan (Anonim, 2007).
Biogas sebagian besar mengandung gas metana (CH4) dan karbon dioksida (CO2), dan beberapa kandungan yang jumlahnya kecil diantaranya hydrogen sulfida (H2S) dan ammonia (NH3) serta hydrogen dan (H2), nitrogen yang kandungannya sangat kecil (Wahyuningsih, 2009). Tetapi secara umum rentang komposisi biogas adalah sebagai berikut:
Tabel 2.1 Komposisi Biogas
Komponen %
Metana (CH4) 55-75
Karbon dioksida (CO2) 25-45
Nitrogen (N2) 0-0,3
Hidrogen (H2) 1-5
Hidrogen sulfida (H2S) 0-3
Oksigen (O2) 0,1-0,5 Sumber : id. Wikipedia.org, 2007
sampah-sampah organik tersebut membusuk, akan dihasilkan gas metana (CH4) dan
karbon dioksida (CO2). Tapi, hanya CH4 yang dimanfaatkan sebagai bahan bakar
(Wahyuningsih, 2009).
Adapun khusus mengenai gas CH4 perlu diperhatikan adanya kemungkinan ledakan. Karakteristik lain dari CH4 murni adalah mudah terbakar. Kandungan metana dengan udara akan menentukan pada kandungan berapa campuran yang mudah meledak dapat dibentuk. Pada lower explosion limit (LEL) 5,4 vol % metana dan upper explosion limit (UEL) 13,9 vol %. Dibawah 5,4 % tidak cukup metana sedangkan diatas 14 % terlalu sedikit oksigen untuk menyebabkan ledakan. Temperatur yang dapat menyebabkan ledakan sekitar 650–750 oC , percikan api dan korek api cukup panas untuk menyebabkan ledakan ( Iqbal, 2008).
2.2 Sejarah Biogas
Gas CH4 (metana) terbentuk karena proses fermentasi secara anaerobik oleh
bakteri metana atau disebut juga bakteri anaerobik dan bakteri biogas yang mengurangi sampah-sampah yang banyak mengandung bahan organik sehingga terbentuk gas metana (CH4) yang apabila dibakar dapat menghasilkan energi panas. Sebetulnya di tempat-tempat tertentu proses ini terjadi secara alamiah sebagaimana peristiwa ledakan gas yang terbentuk di bawah tumpukan sampah di Tempat Pembuangan Sampah Akhir (TPA) Leuwigajah, Kabupaten Bandung, Jawa Barat. Gas metana sama dengan gas LPG (Liquidified Petroleum Gas), perbedaannya adalah gas metana mempunyai satu atom C, sedangkan elpiji lebih banyak. (Rahman, 2005).
Kebudayaan Mesir, China, dan Roma kuno diketahui telah memanfaatkan gas alam ini yang dibakar untuk menghasilkan panas. Adapun orang pertama yang mengaitkan gas bakar ini dengan proses pembusukan bahan sayuran adalah Alessandro Volta pada tahun 1776. Pada tahun 1806 Willam Henry mengidentifikasikan gas yang dapat terbakar tersebut sebagai CH4, lalu Becham pada
tahun 1868, murid Louis Pasteur dan Tappeiner memperlihatkan asal mikrobiologis dari pembentukan CH4.
pembangkit biogas dengan memanfaatkan limbah pertanian. Selama Perang Dunia II banyak petani di Inggris dan benua Eropa yang membuat digester kecil untuk menghasilkan biogas yang digunakan untuk menggerakkan traktor. Karena harga BBM (Bahan Bakar Minyak) semakin murah dan mudah memperolehnya pada tahun 1950-an pemakaian biogas di Eropa ditinggalkan. Namun, di negara-negara berkembang kebutuhan akan sumber energi yang murah dan selalu tersedia selalu ada. Kegiatan produksi biogas di India telah dilakukan semenjak abad ke-19. Alat pencerna anaerobik pertama dibangun pada tahun 1900.
Negara berkembang lainnya, seperti China, Filipina, Korea, Taiwan, dan Papua Niugini, telah melakukan berbagai riset dan pengembangan alat pembangkit biogas dengan prinsip yang sama, yaitu menciptakan alat yang kedap udara dengan bagian-bagian pokok terdiri atas pencerna (digester), lubang pemasukan bahan baku dan pengeluaran lumpur sisa hasil pencernaan (slurry) dan pipa penyaluran gas bio yang terbentuk (Nandiyanto, 2007)
Dengan teknologi tertentu, gas metana dapat dipergunakan untuk menggerakkan turbin yang menghasilkan energi listrik, menjalankan kulkas, mesin tetas, traktor, dan mobil. Secara sederhana, gas metana dapat digunakan untuk keperluan memasak dan penerangan menggunakan kompor gas sebagaimana halnya LPG (Rahman, 2005).
2.3 Faktor yang Berpengaruh Pada Proses Anaerobik
Aktivitas metabolisme mikroorganisme penghasil metana tergantung pada faktor:
2.3.1 Temperatur
perubahan berjalan perlahan. Apabila bakteri bekerja pada temperatur 40oC produksi gas akan berjalan dengan cepat hanya beberapa jam tetapi untuk sisa hari itu hanya akan diproduksi gas yang sedikit. Perubahan temperatur tidak boleh melebihi batas temperatur yang diijinkan. Untuk bakteri psychrophilic selang perubahan temperatur berkisar antara 2 oC/ jam, bakteri mesophilic 1 oC/jam dan bakteri thermophilic 0.5 o
C/jam (Fry, 1973).
2.3.2 Derajat Keasaman (pH)
Derajat keasaman memiliki efek terhadap aktivasi biologi dan mempertahankan pH agar stabil penting untuk semua kehidupan. Kebanyakan dari proses kehidupan memiliki kisaran pH antara 5 – 9. Nilai pH yang dibutuhkan untuk digester antara 7 – 8,5. Pertumbuhan bakteri penghasil gas metana akan baik bila pH bahannya pada keadaan alkali (basa). Bila proses fermentasi berlangsung dalam keadaan normal dan anaerobik, maka pH akan secara otomatis berkisar antara 7 – 8,5. Bila derajat keasaman lebih kecil atau lebih besar dari batas, maka bahan tersebut akan mempunyai sifat toksik terhadap bakteri metanogenik. Derajat keasaman dari bahan didalam digester merupakan salah satu indikator bagaimana kerja digester. Untuk bangunan digester yang kecil, pengukuran pH dapat diambil dari keluaran/effluent digester atau pengambilan sampel dapat diambil di permukaan digester apabila telah terpasang tempat khusus pengambilan sampel (Fry, 1974).
2.3.3 Ketersediaan Unsur Hara
mempertahankan pada level yang optimal untuk mencapai digester yang baik tanpa adanya efek toksik (Amaru, 2004)
2.3.4Alkalinitas
Alkalinitas limbah cair dapat dihasilkan dari hidrokarbon, karbonat(CO32-) dan
bikarbonat (HCO3-) yang berikatan dengan kalsium, magnesium, kalium dan amonia.
Alkalinitas limbah cair membantu mempertahankan pH agar tidak mudah berubah yang disebabkan oleh penambahan asam. Selain itu, alkalinitas juga mempengaruhi pengolahan zat-zat kimia dan biologi serta dibutuhkan sebagai nutrisi bagi mikroba. Kadar alkalinitas diperoleh dengan menitrasi sampel dengan larutan standar asam dan diperoleh hasil dalam satuan mg/L CaCO3(Amaru, 2004)
2.4 Tahapan Metabolisme dalam Degradasi Anaerobik
Umumnya, proses anaerob terjadi pada empat tahapan utama, yaitu :
hidrolisis, fermentasi, asetogenesis, dan metagenesis. Setiap tahapan melibatkan populasi mikroba yang berbeda.
2.4.1 Hidrolisis
Material organik polimerik dihidrolisis menjadi monomer seperti glukosa, asam lemak dan asam amino oleh bakteri hidrolitik. Proses hidrolisis adalah proses yang sangat penting pada limbah organik tinggi. Solubilisasi melibatkan proses hidrolisis dimana senyawa – senyawa organik kompleks dihidrolisis menjadi monomer – monomer. Lemak dihidrolisis menjadi asam – asam lemak atau gliserol; protein dihidrolisis menjadi asam – asam amino atau peptida sedangkan karbohidrat dihidrolisis menjadi monosakarida dan disakarida. Reaksi hidrolisis dapat dilihat sebagai berikut:
Lemak asam lemak rantai panjang, gliserol Protein asam-asam amino, peptida rantai pendek Polisakarida monosakarida, disakarida
Pada tahap ini produk yang telah dihidrolisa dikonversikan menjadi asam lemak volatil, alkohol, aldehid, keton, amonia, karbondioksida, air dan hidrogen oleh bakteri pembentuk asam. Asam – asam organik yang terbentuk adalah asam asetat, asam propionat, asam butirat dan asam valerat. Reaksi asidogenesis dapat di lihat di bawah ini:
C6H12O6 CH3CH2CH2COOH + 2 CO2 + 2 H2
glukosa asam butirat C6H12O6 + 2 H2 CH3CH2COOH + 2 H2O
glukosa asam propionat
2.4.3 Asetogenesis
Asam lemak volatil dengan empat atau lebih rantai karbon tidak dapat digunakan secara langsung oleh metanogen. Asam-asam organik ini dioksidasi terlebih dahulu menjadi asam asetat dan hidrogen oleh bakteri asetogenik penghasil hidrogen melalui proses yang disebut asetogenesis. Asetogenesis juga temasuk pada produksi asetat dari hidrogen dan karbon dioksida oleh asetogen dan homoasetogen. Kadang-kadang proses asidogenesis dan asetogenesis dikombinasikan sebagai satu tahapan saja. Reaksi asetogenesis dapat dilihat di bawah ini:
CH3CH2COOH CH3COOH + CO2 + 3 H2
asam propionat asam asetat
CH3CH2CH2COOH 2 CH3COOH + 2 H2
asam butirat asam asetat
2.4.4 Metagenesis
Pada akhirnya gas metana diproduksi dengan dua cara. Pertama adalah mengkonversikan asetat menjadi karbon dioksida dan metana oleh organisme asetropik dan cara lainnya adalah dengan mereduksi karbon dioksida dengan hidrogen oleh organisme hidrogenotropik. Metanogen yang dominan digunakan pada reaktor biogas adalah Methanobacterium, Methanothermobacter, Methanobrevibacter, Methanosarcina dan Methanosaeta. Reaksi metanogenesis
dapat dilihat dibawah ini:
CO2 + 4H2 CH4 +2H2O (Lang, 2007)
Gambar 2.1 Skema fermentasi metana pada proses anaerobik (Speece, 1996)
2.5 Palm Oil Mill Effluent (POME)
Palm oill mill effluent (POME) berasal dari air kondensat pada proses
sterilisasi, air dari proses klarifikasi, air hydrocyclone (claybath), dan air pencucian pabrik. Jumlah air buangan tergantung pada sistem pengolahan, kapasitas olah pabrik, dan keadaan peralatan klarifikasi. Limbah cair POME mengandung bahan organik yang relatif tinggi dan tidak bersifat toksik karena tidak menggunakan bahan kimia dalam proses ekstraksi minyak kelapa sawit (Siregar, 2009).
Komponen organik kompleks (Karbohidrat, protein, lipid)
Asam-asam lemak rantai panjang (Propionat, butirat dan lain-lain)
35 %
17 % 13 %
10 % Hidrolisis
Asidogenesis
20 % 5 %
Komponen organic sederhana (Gula, asam amino, peptida)
CH4, CO2
72 % 28 %
Komposisi kimia limbah cair POME dan komposisi asam amino limbah cair segar disajikan pada Tabel 2.2 berikut.
Tabel 2.2 Komposisi Kimia Limbah Cair POME
Komponen % Berat Kering
Ekstrak dengan ether 31.60
Protein (N x 6,25) 8.20
Serat 11.90
Ekstrak tanpa N 34.20
Abu 14.10
P 0.24
K 0.99
Ca 0.97
Mg 0.30
Na 0.08
Energi (kkal / 100 gr) 454.00
Sumber : Siregar, 2009
Limbah cair POME umumnya bersuhu tinggi, berwarna kecoklatan, mengandung padatan terlarut dan tersuspensi berupa koloid dan residu minyak dengan kandungan biological oxygen demand (BOD) yang tinggi. Parameter yang menggambarkan karakteristik limbah terdiri dari sifat fisik, kimia, dan biologi. Karakteristik limbah berdasarkan sifat fisik meliputi suhu, kekeruhan, bau, dan rasa, berdasarkan sifak kimia meliputi kandungan bahan organik, protein, BOD, chemical
oxygen demand (COD), sedangkan berdasakan sifat biologi meliputi kandungan
bakteri patogen dalam air limbah (Siregar, 2009).
Berdasarkan Keputusan Menteri Negara Lingkungan Hidup ada 6 (enam) parameter utama yang dijadikan acuan baku mutu limbah meliputi :
a. Tingkat keasaman (pH), ditetapkannya parameter pH bertujuan agar mikroorganisme dan biota yang terdapat pada penerima tidak terganggu, bahkan diharapkan dengan pH yang alkalis dapat menaikkan pH badan penerima.
c. COD, kelarutan oksigen kimiawi adalah oksigen yang diperlukan untuk
merombak bahan organik dan anorganik, oleh sebab itu nilai COD lebih besar dari BOD.
d. Total suspended solid (TSS), menggambarkan padatan melayang dalam cairan
limbah. Pengaruh TSS lebih nyata pada kehidupan biota dibandingkan dengan
total solid. Semakin tinggi TSS, maka bahan organik membutuhkan oksigen
untuk perombakan yang lebih tinggi.
e. Kandungan total nitrogen, semakin tinggi kandungan total nitrogen dalam cairan limbah, maka akan menyebabkan keracunan pada biota.
f. Kandungan oil and grease, dapat mempengaruhi aktifitas mikroba dan merupakan pelapis permukaan cairan limbah sehingga menghambat proses oksidasi pada saat kondisi aerobic (Siregar, 2009).
Adapun karakteristik dari limbah POME yang dihasilkan dapat dilihat pada Tabel 2.3 di bawah ini:
Tabel 2.3 Karaktersitik Limbah POME dan Baku Mutu Limbah
Parameter Komposisi
BOD5 (mg/L) 23000-26000
COD (mg/L) 42500-55700
Soluble COD (mg/L) 22000-24000 TVFAs (mg acetic acid/l) 2500-2700
SS (mg/L) 16500-19500
Oil and grease (mg/L) 4900-5700
Total N (mg/L) 500-700
pH 3,8-4,4
Sumber : Zinatizadeh, et al, 2007
Berdasarkan data di atas, ternyata semua parameter limbah cair POME berada diatas ambang batas baku mutu limbah. Jika tida dilakukan pencegahan dan pengolahan limbah, maka akan berdampak negatif terhadap lingkungan seperti pencemaran air yang mengganggu bahkan meracuni bota perairan, menimbulkan bau, dan menghasilkan gas metan dan CO2 yang merupakan emisi gas penyebab efek rumah kaca yang berbahaya bagi lingkungan (Siregar, 2009).
2.6 Pengaruh Sistem Recycle Terhadap Proses Pengolahan POME
laju dekomposisi COD dapat dilakukan dengan meningkatkan Sludge Retention Time (SRT) dengan mengembalikan lumpur dari digester ke reaktor. Oleh karena itu pengaruh dari fermentasi POME dengan sistem recycle sludge diharapkan dapat meningkatkan laju dekomposisi COD di atas 80%.
Konversi Volatile Solid menjadi gas adalah fungsi dari SRT. Pada fermentasi POME dengan digester anaerobik berpengaduk HRT sama dengan SRT tetapi pada kondisi fermentasi dengan recycle HRT tidak sama dengan SRT. SRT yang lama akan meningkatkan laju dekomposisi VS pula (Burke, 2001).
Selain parameter-parameter yang mengukur efisiensi suatu proses anaerob dari segi kualitas dan kuantitas biogas yang dihasilkan, parameter yang menjadi indikator kualitas cairan fermentasi yang dikeluarkan atau discharged slurry juga sangat penting dan harus memperhatikan baku mutu limbah buangan industri yang berlaku. Parameter yang paling sering digunakan dalam hal ini adalah COD (chemical oxygen demand), yakni ukuran tak langsung dari jumlah senyawa organik, baik yang dapat terbiodegradasi maupun yang tidak dapat terbiodegradasi. Pengujian COD biasanya dilakukan dengan mengukur kemampuan kalium dikromat untuk mengoksidasi senyawa organik.
Dari penelitian yang pernah dilakukan diperoleh data bahwa :
1. Produksi gas pada fermentasi dengan recycle sludge ataupun non recycle memberikan tren yang hampir sama namun pada fermentasi dengan recycle
sludge produksi gas lebih tidak stabil dibanding fermentasi non recycle
sludge dikarenakan adanya penumpukan amonium yang berlebihan. Dari
hasil yang diperoleh di dalam penelitian yang telah dilakukan dapat dilihat bahwa mikroba di dalam fermentor untuk fermentasi dengan recycle sludge terus berproduksi dan berkembang, namun pada akhir masa fermentasi mengalami keracunan karena nutrisi yang diberi tidak dapat diserap secara keseluruhan. Sehingga hendaknya dilakukan pengurangan pemberian amonium bikarbonat.
3. disimpulkan bahwa fementasi dengan recycle sludge memiliki performa lebih baik dibandingkan fermentasi non recycle sludge.
4. disimpukan bahwa fermentasi anaerobik dengan recycle sludge lebih meningkatkan laju dekomposisi COD yang berarti limbah buangan yang dihasilkan lebih rendah konsentrasinya dan memenuhi standar baku mutu limbah buangan. Laju dekomposisi COD yang diperoleh dari penelitian ini telah memenuhi persyaratan CDM yaitu laju dekomposisi COD > 80%. (Senafati&Amalia, 2009).
2.7 Kegunaan Biogas
Biogas memiliki kandungan energi tinggi yang tidak kalah dari kandungan energi dalam bahan bakar fosil. Nilai kalori dari 1 m3 biogas sekitar 6000 watt jam, setara dengan setengah liter minyak diesel. Oleh karena itu biogas sangat cocok menggantikan minyak tanah, LPG, butana, batu bara, dan bahan bakar fosil lainnya. Biogas mengandung 75% metana. Semakin tinggi kandungan metana dalam bahan bakar, semakin besar kalor yang dihasilkan. Oleh karena itu, biogas juga memiliki karakteristik yang sama dengan gas alam. Sehingga jika biogas diolah dengan benar, biogas bisa digunakan untuk menggantikan gas alam. Dengan demikian jumlah gas alam bisa dihemat. Limbah biogas dapat digunakan sebagai pupuk. Limbah biogas, kotoran ternak yang telah hilang gasnya (slurry) merupakan pupuk organik yang sangat kaya akan unsure-unsur yang sangat dibutuhkan tanaman. Bahkan, unsur-unsur tertentu seperti protein, selulosa, dan lignin tidak bisa digantikan oleh pupuk kimia. Dengan demikian kita juga bisa mengurangi anggaran untuk membeli pupuk (Can, 2008).
2.8 Deskripsi Proses dan Sifat-Sifat Bahan Baku dan Produk
2.8.1 Deskripsi Proses Pra Rancangan Pabrik Pembuatan Biogas Dari Hasil Fermentasi Thermofilik Limbah Cair Kelapa Sawit Sistem Recycle Sistematik proses Pembuatan biogas Dari Hasil Fermentasi Thermofilik Limbah Cair Pabrik Kelapa Sawit Sistem Recycle disajikan dalam Gambar 2.2. Palm
Oil Mill Effluent (POME) ditampung di dalam Bak Penampungan (BP-01) untuk
persediaan selama satu minggu, selanjutnya POME dipompa menuju Bak Neutralisasi (M-101) untuk dicampur dengan NaHCO3 , FeCl2, NiCl2 dan CoCl2. Penambahan senyawa NaHCO3 dilakukan untuk menetralkan pH POME karena fermentasi berlangsung dengan baik dalam pH 6-8, sedangkan penambahan senyawa FeCl2, NiCl2 dan CoCl2 bertujuan sebagai nutrisi bagi inokulum.
Setelah itu, POME dari M-01 dialirkan ke Bak Pencampur (M-02) untuk dicampur dengan aliran recyle dari Tangki Sedimentasi (RC-01/RC-02). Umpan POME dialirkan ke fermentor. Suhu di dalam fermentor dijaga 550C, dimana bakteri yang digunakan adalah bakteri thermofilik. Proses yang terjadi meliputi proses hidrolisis, asidifikasi, dan proses pembentukan metana dengan hydraulic retention
time 6 hari. Dari fermentor, limbah yang tidak terolah ditampung kedalam
RC-01/RC-02 untuk diendapkan, sebagian dari limbah pada RC-RC-01/RC-02 di recyle kembali ke M-02 dan sisanya dialirkan ke Bak Penampung Akhir untuk diolah lanjut sebagai land application
Biogas yang dihasilkan terdiri atas CH4, CO2, H2S dan H2O. Biogas yang dihasilkan dialirkan ke Water Trap (DT-01) untuk memisahkan air yang terkandung di dalam biogas. Gas H2S yang terdapat di dalam biogas perlu dihilangkan, karena gas ini dapat memepengaruhi kinerja dari Generator listrik apabila tidak dihilangkan. Proses desulfurisasi (penghilangan sulfur) dari gas dilakukan dengan penyerapan di dalam adsorber Tangki Desulfurisasi (D-01) menggunakan adsorben zinc oxide (ZnO) yang bekerja pada suhu 60 OC dan tekanan 1 atm.
2.8.2 Sifat-Sifat Bahan Baku dan Produk 2.8.2.1 Ferro Klorida (FeCl2)
Fungsi: sebagai sumber nutrisi bagi mikroba 1. Berat molekul : 126,751 gr/mol
3. Kelarutan dalam air : 64,4 gr/100 ml pada 10 0C 4. Densitas : 3,16 gr/cm3
5. Agen flokulan dalam pengolahan air limbah buangan 6. Tidak larut dalam tetrahidrofuran
7. Merupakan padatan paramagnetik (Wikipedia, 2010)
2.8.2.2 Natrium karbonat (NaHCO3) Fungsi : sebagai agen penetral pH. 1. Berat molekul : 84,0079 gr/mol 2. Titik lebur : 500 C (323 K) 3. Densitas : 2,159 gr/cm3
4. Kelarutan dalam air : 7,89 g / 100 ml pada 180 C 5. Tingkat kebasaan (pKb) : -2,43
6. Berwarna padatan putih
7. Merupakan senyawa ampoterik (Wikipedia,2010)
2.8.2.3 Nikel(II)Clorida (NiCl2)
Fungsi : sebagai nutirisi bagi mikroba 1. Berat molekul : 129,599 gr/mol 2. Titik lebur : 10010 C
3. Densitas : 3,55 gr/cm3
4. Kelarutan dalam air : 64 g / 100 ml pada 250 C 5. Berwarna padatan hijau muda
6. Memiliki struktur kristal monoclinic 7. Bersifat eksotermis
(Wikipedia,2010)
2.8.2.4 Kobalt (II)Klorida (CoCl2)
2. Titik lebur : 735 0C 3. Titik didih : 1049 oC 3. Densitas : 3,356 gr/cm3
4. Kelarutan dalam air : 52,9 g / 100 ml pada 200 C 5. Berwarna coklat kemerahan
6. Memiliki koordinat geometri oktahedral (Wikipedia,2010)
2.8.2.5 Metana (CH4)
Fungsi : merupakan komponen unsur terbesar di dalam biogas. 1. Berat Molekul : 16,043 g/mol
2. Temperatur kritis : -82,7oC 3. Tekanan kritis : 45,96 bar 4. Fasa padat
• Titik cair : -182,5oC • Panas laten : 58,68 kJ/kg 5. Fasa cair
• Densitas cair : 500 kg/m3 • Titik didih : -161,6oC • Panas laten uap : 510 kJ/kg 6. Fasa gas
2.8.2.6 Karbon Dioksida (CO2)
Fungsi : merupakan salah satu komponen di dalam biogas. 1. Berat Molekul : 44,01 g/mol
2. Temperatur kritis : 31oC 3. Tekanan kritis : 73,825 bar 4. Densitas kritis : 464 kg/m3 5. Fasa padat
• Densitas padat : 1562 kg/m3 • Panas laten : 196,104 kJ/kg 6. Fasa cair
• Densitas cair : 1032 kg/m3 • Titik didih : -78,5oC
• Panas laten uap : 571,08 kJ/kg • Tekanan uap : 58,5 bar
7. Fasa gas
• Densitas gas : 2,814 kg/m3 • Spesifik graviti : 1,521
• Spesifik volume : 0,547 m3/kg • CP : 0,037 kJ/mol.K
• CV : 0,028 kJ/mol.K
BAB III
NERACA MASSA
[image:33.595.117.520.173.394.2]3.1 Tangki Neutralisasi
Tabel 3.1 Neraca Massa pada Tangki Neutralisasi Komponen
Masuk (kg/hari)
Keluar (kg/hari)
1 2 3 4 5 6
POME 443835,6164 - - - - 443835,6164
NaHCO3 - 1109,5890 - - - 1109,5890
FeCL2 - - 39,812 - - 39,812
NiCl2 - - - 0,533 - 0,533
CoCl2 - - - - 1,505 1,505
Total 444987,0547 444987,0547
3.2 Tangki Pencampur
Tabel 3.2 Neraca Massa pada Tangki Pencampur Komponen
Masuk (kg/hari)
Keluar (kg/hari)
6 20 7
POME 443835,6164 - 443835,6164
NaHCO3 1109,5890 369,863 1479,4521
FeCL2 39,8121 13,271 53,0827
NiCl2 0,5326 0,178 0,7101
CoCl2 1,5046 0,502 2,0061
Air - 127.925,66 127.925,66
Padatan Organik - 13717,644 13717,6442
[image:33.595.125.512.442.648.2]3.3 Reaktor Fermentasi
Tabel 3.3 Neraca Massa pada Reaktor Fermentasi Komponen
Masuk (kg/hari)
Keluar (kg/hari)
8 9 19 20 10
POME 221917,808 221917,808 - - -
NaHCO3 739,726 739,726 739,726 739,726 -
FeCL2 26,541 26,541 26,541 26,541 -
NiCl2 0,355 0,355 0,355 0,355 -
CoCl2 1,003 1,003 1,003 1,003 -
Air 63962,831 63962,831 273.647,18 273.647,18 - Padatan
Organik 6858,822 6858,822 9639,426 9639,426 -
CH4 - - - - 4993,151
H2O - - - - 47,237
H2S - - - - 1,9306
CO2 - - - - 13863,38
Total 293.507,08 293.507,08 284.054,23 284.054,23 18.905,7
587.014,173 587.014,173
3.4 Bak Sedimentasi
Tabel 3.4 Neraca Massa pada Bak Sedimentasi Komponen
Masuk (kg/hari)
Keluar (kg/hari)
19 20 21 22
NaHCO3 739,726 739,726 369,863 1109,589
FeCL2 26,541 26,541 13,271 39,812
NiCl2 0,355 0,355 0,178 0,533
CoCl2 1,003 1,003 0,502 1,505
Air 273.647,185 273.647,185 127.925,661 419.368,708 Padatan Organik 9639,426 9639,426 13717,644 5561,207
Total 284.054,236 284.054,236 142.027,118 426.081,354
3.5 Water Trap
Tabel 3.5 Neraca Massa Pada Water Trap Komponen
Masuk (kg/hari)
Keluar (kg/hari)
11 13 12
CH4 4993,151 4993,151 -
H2O 47,237 - 47,237
H2S 1,93068 1,93068 -
CO2 13863,383 13863,383 -
Total 18.905,7 18.858,464 47,237
18.905,7
3.6 Desulfurisasi
Tabel 3.6 Neraca Massa pada Desulfurisasi Komponen
Masuk (kg/hari)
Keluar (kg/hari)
13 15 14
CH4 4993,151 4993,151 -
H2S 1,93068 - 1,93068
CO2 13863,383 13863,383 -
Total 18.858,464 18856,534 1,93068 18.858,464
[image:35.595.143.497.522.671.2]3.7 Generator (G-01)
Tabel 3.7 Neraca Massa pada generator Komponen
Alur masuk (kg/hari) Alur keluar (kg/hari)
14 15 16
CH4 4.998,63 - -
CO2 10.536,88 - 24.282,92
O2 - 23.993,08 3.998,84
N2 - 90.259,68 90.259,68
H2O - - 11.246,76
15.535,51 114.252,76 129.788,27
BAB IV
NERACA ENERGI
Basis perhitungan : 1 hariSatuan operasi : kJ/hari
Temperatur basis : 25oC (298,15 K) 4.1 Tangki Neutraliser (M-01)
Tabel 4.1 Neraca Energi pada Bak Neutralizer (M-01)
Komponen Masuk (kJ) Keluar (kJ)
Umpan
8975258.234
Produk
9175543.138
∆H solution -
-200284.9047 Total 8975258.234 8975258.234
4.2 Tangki Pencampur (M-02)
Tabel 4.2 Neraca Energi pada Tangki Pencampur (M-02)
Komponen Masuk (kJ) Keluar (kJ)
6 21 7
Umpan 9175543.138 6489761.816 -
Produk - - 15665304.954
Total 15665304.954 15665304.954
[image:36.595.109.484.75.764.2]4.3 Fermentor (R-01/R-02)
Tabel 4.3 Neraca Energi pada Fermentor (R01/R02)
Komponen Masuk (kJ) Keluar (kJ)
8/9 10/11 19
Umpan 15665304.954 - -
Produk - 68731070.170 848376.593
∆H reaksi - -18638000
dQ/dT 35275794.144
BAB V
SPESIFIKASI PERALATAN
5.1 Bak Umpan POME (BP-01)
Fungsi : Menampung POME
Bentuk : Bak Silinder vertikal dengan alas datar Bahan konstruksi : Beton
Jumlah : 1 unit Kondisi operasi :
• P = 1 atm
• T = 30 0C Waktu tinggal ( τ ) : 7 hari Dengan demikian,
Panjang bak (p) = 21,17 m Tinggi bak (t) = 5,3 m
Lebar bak (l) = 10,58 m Tinggi larutan dalam bak = x 5,3 m
3728,22 3106,849
= 4,41 meter
5.2 Pompa Umpan POME (P-01)
Fungsi : Memompa POME ke Tangki Neutralisasi Jenis : Pompa screw pump
Bahan konstruksi : Commercial Steel Jumlah : 1 unit
Kondisi operasi :
• Tekanan = 1 atm
5.3 NaHCO3 Screw Conveyor (T-01)
Fungsi : Mengalirkan NaHCO3 ke Tangki Neutralisasi Bahan konstruksi : Carbon steel
Bentuk : Horizontal scew conveyor Jumlah : 1 unit
Jarak angkut = 30 ft = 9,144 m Diameter screw conveyor = 12 in,
Daya = 0,1 Hp
5.4 FeCl2 Screw Conveyor (T-02)
Fungsi : Mengalirkan FeCl2 ke Tangki Neutralisasi Bahan konstruksi : Carbon steel
Bentuk : Horizontal scew conveyor Jumlah : 1 unit
Jarak angkut = 30 ft = 9,144 m Diameter screw conveyor = 12 in,
Daya = 0,01 Hp
5.5 Tangki Neutralisasi (M-01)
Fungsi : Mencampur POME dengan NaHCO3 dan Nutrisi Bentuk : Silinder vertikal dengan alas datar dan tutup elipsoidal Bahan Konstruksi : Carbon steel SA-285 grade C
Jumlah : 1 unit Kondisi operasi :
P = 1 atm
T = 30,113 0C Waktu tinggal ( τ ) = 1 hari
Tebal shell tangki = 2 in
Jenis Pengaduk = flat 6 blade turbin impeller Jumlah Baffle = 4 buah
Daya Motor = 12 Hp
5.6 Pompa Neutraliser (P-02)
Fungsi : Memompa bahan baku ke tangki pencampur Jenis : Pompa screw pump
Bahan konstruksi : Commercial Steel Jumlah : 1 unit
Kondisi operasi :
Tekanan = 1 atm
Temperatur = 30,113 oC = 303,15 K Daya motor = 1 Hp
5.7 Pompa Sedimentasi (P-05)
Fungsi : Memompa umpan recycle ke tangki pencampur
Jenis : Pompa screw pump
Bahan konstruksi : Commercial Steel Jumlah : 1 unit
Kondisi operasi :
Tekanan = 1 atm Temperatur = 37 oC Daya = 1/4 Hp 5.8 Pompa Sedimentasi (P-06)
Fungsi : Memompa bahan baku ke tangki pencampur
Jenis : Pompa screw pump
Bahan konstruksi : Commercial Steel Jumlah : 1 unit
Kondisi operasi :
Tekanan = 1 atm Temperatur = 37 oC
5.9 Tangki pencampur (M-02)
Fungsi : Mencampur POME dengan umpan recycle
Bentuk : Silinder vertikal dengan alas datar dan tutup elipsoidal Bahan Konstruksi : Carbon steel SA-285 grade C
Jumlah : 1 unit Kondisi operasi :
P = 1 atm T = 31,708 0C
Waktu tinggal ( τ ) : 1 hari
Volume tangki = 61,6 m3 Diameter tangki = 3,74 m Tinggi tangki = 5,61 m Tinggi tutup = 0,94 m Tebal shell = 1 ½ in
Jenis Pengaduk = flat 6 blade turbin impeller Jumlah baffle = 4 buah
Daya Motor = 5,5 Hp
5.10 Pompa Umpan Bioreaktor Berpengaduk (P-04)
Fungsi : Memompa bahan baku ke tangki pencampur Jenis : Pompa screw pump
Bahan konstruksi : Commercial Steel Jumlah : 1 unit
Kondisi operasi :
Tekanan = 1 atm Temperatur = 31,708 oC
Daya =
2 1 Hp
5. 11 Fermentor (R-01)
Fungsi : Tempat berlangsungnya reaksi fermentasi Tipe : Bioreaktor berpengaduk
Bahan Konstruksi: Carbon steel SA-285 grade C Jumlah : 1 unit
Kondisi operasi : P = 1 atm T = 55 0C
Waktu tinggal ( τ ) : 6 hari
Volume tangki = 2135,5 m3 Tinggi tangki = 18,5 m Diameter tangki = 12,3 m Tinggi tutup = 2,06 m
Jenis Pengaduk = flat 6 blade turbin impeller Jumlah Baffle = 4 buah
Daya = 4,5 Hp
Menghitung jaket pemanas
Jumlah Steam = 388,124 kg/hari IDJaket = 480,114 inchi TinggiJaket = 720,172 inchi Jarak Jaket = 12 inchi ODJaket = 504,115 inchi Luas laluan air = 11,969 m2
5.12 Pompa Umpan Reaktor Floating Roof (P-03)
Fungsi : Memompa bahan baku ke tangki pencampur Jenis : Pompa screw pump
Bahan konstruksi : Commercial Steel Jumlah : 1 unit
Kondisi operasi :
5.13 Bioreaktor Floating Roof (R-02)
Fungsi : Tempat berlangsungnya reaksi fermentasi Bentuk : Floating Roof Tank
Bahan Konstruksi : Carbon steel SA-285 grade C Jumlah : 1 unit
Kondisi operasi :
• Tekanan = 1 atm
• Temperatur = 55 0C Desain Tangki
Volume Tangki = 2217,6 m3 Diameter Tangki =12,34 m Tinggi Tangki = 18,5 m
Tebal Tangki = 1,25 in Desain Tutup
Volume Tutup = 1847,107 m3 Diameter = 12,13 m Tinggi = 15,98 m
Jarak Dasar Tutup ke Tangki = 2,3 m Menghitung jaket pemanas
Jumlah Steam = 388,124 kg/hari IDJaket = 480,114 inchi TinggiJaket = 720,172 inchi Jarak Jaket = 12 inchi ODJaket = 504,115 inchi Luas laluan air = 11,969 m2 Blower
Jenis : blower sentrifugal Bahan konstruksi : carbon steel Daya = 3,5 hp
5.14 Bak Sedimentasi (RC-01/02)
Fungsi : Mengendapkan sebagian padatan-padatan yang keluar dari fermentor.
Jenis : Gravity Thickner Jumlah : 2 unit
Bahan konstruksi : Carbon steel SA-212, GradeC Kondisi Operasi
• Tekanan masuk = 1 atm
• Suhu masuk = 55 oC Volume = 59,32 m3
Diameter = 3,69 m Tinggi = 6,77 m Kedalaman bahan = 5 m Waktu pengendapan= 2 jam
5.15 Water Trap (DT-01)
Fungsi : Sebagai wadah pemisah air dan biogas. Bahan konstruksi : Carbon Steel SA –285 Grade C
Bentuk : Silinder vertikal dengan alas dan tutup ellipsoidal Jenis sambungan : Double welded butt joints
Jumlah : 1 unit
Kondisi operasi :
• Tekanan = 1 atm
5.16 Desulfuriser (D-01)
Fungsi : menyerap gas H2S. Jenis : Fixed bed ellipsoidal
Bahan : Carbon steel, SA-283, grade C Kondisi operasi
• Temperatur = 65 0C
• Tekanan = 1 atm Jenis Adsorben = ZnO Jumlah Katalis = 6,188 kg Tinggi Kolom = 1,921 m Diameter Kolom = 1,281 Tinggi Tutup = 0,32 m Tebal Kolom = 1,5 in.
5.17 Generator (GE-01) 5.17.1 Kompressor
Fungsi : menaikkan tekanan produk gas dari tangki penampung Jenis : compressor
Jumlah : 1 unit dengan 5 stages Kondisi operasi:
• Tekanan masuk (P1 ) = 1atm
• Tekanan Keluar (P2) = 6 atm
• Temperatur (T) = 30 0C
Dipilih material pipa commercial steel 2 inchi Sch 40
• Diameter dalam (ID) = 2,067in
• Diameter luar (OD) = 2,375 in
• Luas penampang (A) = 0,023 ft2
• Daya yang dihasilkan = 583,33 Hp
5.17.2 Turbin
Fungsi : Menurunkan tekanan gas dari ruang pembakaran
Jenis : Centrifugal expander
Jumlah : 1 unit
Kondisi operasi:
• Tekanan masuk (P1 ) = 6 atm
• Tekanan Keluar (P2) = 1 atm
• Temperatur (T) = 28 0C
Dipilih material pipa commercial steel 0,5 inchi Sch 40
• Diameter dalam (ID) = 0,622 in
• Diameter luar (OD) = 0,84 in
• Luas penampang (A) = 0,00211 ft2
• Daya yang dihasilkan = -6.222,66 Hp
• Efisiensi motor 80% = -4.978,13 Hp
BAB VI
INSTRUMENTASI DAN KESELAMATAN KERJA
6.1 Instrumentasi
Instrumentasi adalah suatu alat yang dipakai di dalam suatu proses control untuk mengatur jalannya proses agar diperoleh hasil sesuai dengan yang diharapkan. Dalam suatu pabrik kimia, pemakaian instrumen merupakan suatu hal yang sangat penting karena dengan adanya rangkaian instrumen tersebut maka operasi semua peralatan yang ada di dalam pabrik dapat dimonitor dan dikontrol dengan cermat, mudah dan efisien, sehingga kondisi operasi selalu berada dalam kondisi yang diharapkan. Namun pada dasarnya, tujuan pengendalian tersebut adalah agar kondisi proses di pabrik mencapai tingkat kesalahan (error) yang paling minimum sehingga produk dapat dihasilkan secara optimal (Perry, 1999).
Fungsi instrumentasi adalah sebagai pengontrol, penunjuk (indicator), pencatat (recorder), dan pemberi tanda bahaya (alarm). Instrumentasi bekerja dengan tenaga mekanik atau tenaga listrik dan pengontrolannya dapat dilakukan secara manual atau otomatis. Instrumen digunakan dalam industri kimia untuk mengukur variabel – variabel proses seperti temperatur, tekanan, densitas, viskositas, panas spesifik, konduktifitas, pH, kelembaman, titik embun, tinggi cairan (liquid
level), laju alir, komposisi, dan moisture content. Instrumen – instrumen tersebut
mempunyai tingkat batasan operasi sesuai dengan kebutuhan pengolahan (Timmerhaus, 2004).
Variabel – variabel proses yang biasanya dikontrol/diukur oleh instrument adalah (Considine,1985) :
1. Variabel utama, seperti temperatur, tekanan, laju alir, dan level cairan.
2. Variabel tambahan, seperti densitas, viskositas, panas spesifik, konduktivitas, pH, humiditas, titik embun, komposisi kimia, kandungan kelembaban, dan variabel lainnya.
alat – alat itu dipasang pada peralatan proses (manual control) atau disatukan dalam suatu ruang kontrol yang dihubungkan dengan bagian peralatan (automatic control) (Perry,1999).
Menurut sifatnya konsep dasar pengendalian proses ada dua jenis, yaitu : ● Pengendalian secara manual
Tindakan pengendalian yang dilakukan oleh manusia. Sistem pengendalian ini merupakan sistem yang ekonomis karena tidak membutuhkan begitu banyak instrumentasi dan instatalasinya. Namun pengendalian ini berpotensi tidak praktis dan tidak aman karena sebagai pengendalinya adalah manusia yang tidak lepas dari kesalahan.
● Pengendalian secara otomatis
Berbeda dengan pengendalian secara manual, pengendalian secara otomatis menggunakan instrumentasi sebagi pengendali proses, namun manusia masih terlibat sebagai otak pengendali. Banyak pekerjaan manusia dalam pengendalian secara manual diambil alih oleh instrumentasi sehingga membuat sistem pengendalian ini sangat praktis dan menguntungkan.
Hal – hal yang diharapkan dari pemakaian alat – alat instrumentasi adalah:
Kualitas produk dapat diperoleh sesuai dengan yang diinginkan
Pengoperasian sistem peralatan lebih mudah
Sistem kerja lebih efisien
Penyimpangan yang mungkin terjadi dapat diketahui dengan cepat
Faktor-faktor yang perlu diperhatikan dalam instrumen – instrumen adalah (Timmerhaus, 2004) :
1. Range yang diperlukan untuk pengukuran 2. Level instrumentasi
3. Ketelitian yang dibutuhkan 4. Bahan konstruksinya
5. Pengaruh pemasangan instrumentasi pada kondisi proses
Tujuan perancangan sistem pengendalian dari pabrik biogas dari limbah cair kelapa sawit sebagai sumber energi listrik adalah sebagai keamanan operasi pabrik yang mencakup :
- Mempertahankan variabel – variabel proses seperti temperatur dan tekanan tetap berada dalam rentang operasi yang aman dengan harga toleransi yang kecil.
- Mendeteksi situasi berbahaya kemungkinan terjadinya kebocoran alat, karena komponen zat yang digunakan pada pabrik biogas dari limbah cair kelapa sawit sebagai sumber energi listrik ini sangat mudah terbakar. Pendeteksian dilakukan dengan menyediakan alarm dan sistem penghentian operasi secara otomatis (automatic shut down systems).
[image:48.595.129.563.209.571.2]- Mengontrol setiap penyimpangan operasi agar tidak terjadi kecelakaan kerja maupun kerusakan pada alat proses. Untuk pengukuran nilai variabel proses di atas dapat digunakan sebuah penganalisis (analyzer).(Timmerhaus, 2004)
Gambar 6.1 Sebuah loop Pengendalian
pengukuran. Untuk lebih jelasnya, gambar di bawah ini merupakan suatu contoh aktual dari suatu proses yang terkendali.
Gambar 6.2 Suatu Proses Terkendali
Pada dasarnya sistem pengendalian terdiri dari (Considine,1985) : a. Elemen Primer (Primary Element)
Elemen Primer berfungsi untuk menunjukkan kualitas dan kuantitas suatu variabel proses dan menerjemahkan nilai itu dalam bentuk sinyal dengan menggunakan transducer sebagai sensor. Ada banyak sensor yang digunakan tergantung variabel proses yang ada.
- Sensor untuk temperatur, yaitu bimetal, thermocouple, termal mekanik, dll.
- Sensor untuk tekanan, yaitu diafragma, cincin keseimbangan, dll.
- Sensor untuk level, yaitu pelampung, elemen radioaktif, perbedaan tekanan, dll.
- Sensor untuk aliran atau flow, yaitu orifice, nozzle dll.
b. Elemen Pengukuran (Measuring Element)
Elemen Pengukuran berfungsi mengonversikan segala perubahan nilai yang dihasilkan elemen primer yang berupa sinyal ke dalam sebuah harga pengukuran yang dikirimkan transmitter ke elemen pengendali.
- Tipe Konvensional
Tipe ini menggunakan prinsip perbedaan kapasitansi.
- Tipe Smart
c. Elemen Pengendali (Controlling Element)
Elemen pengendali berfungsi menerima sinyal dari elemen pengukur yang kemudian dibandingkan dengan set point di dalam pengendali (controller). Hasilnya berupa sinyal koreksi yang akan dikirim ke elemen pengendali menggunakan processor (computer, microprocessor) sebagai pemroses sinyal pengendalian. Jenis elemen pengendali yang digunakan tergantung pada variabel prosesnya.
Untuk variabel proses yang lain misalnya :
a. Temperatur menggunakan Temperature Controller (TC) b. Tekanan menggunakan Pressure Controller (PC)
c. Aliran/flow menggunakan Flow Controller (FC) d. Level menggunakan Level Controller (LC)
d. Elemen Pengendali Akhir
Elemen pengendali akhir berperan mengonversikan sinyal yang diterimanya menjadi sebuah tindakan korektif terhadap proses. Umumnya industri menggunakan
control valve dan pompa sebagai elemen pengendali akhir.
1. Control valve
Control valve mempunyai tiga elemen penyusun, yaitu:
- Positioner yang berfungsi untuk mengatur posisi actuator.
- Actuator Valve berfungsi mengaktualisasikan sinyal pengendali (valve).
Ada dua jenis actuator valve berdasarkan prinsip kerjanya yaitu :
a. Actuator spring/per.
Actuator ini menggunakan spring/per sebagai penggerak piston actuator.
b. Actuator aksi ganda (double acting)
Untuk menggerakkan piston, actuator ini menggunakan tekanan udara yang dimasukkan ke rumah actuator.
- Valve, merupakan elemen pengendali proses. Ada banyak tipe valve
berdasarkan bentuknya seperti butterfly valve, valve bola, dan valve segmen. 2. Pompa Listrik
Elemen pompa terdiri dari dua bagian, yaitu :
Sebagai actuator pompa adalah motor listrik. Motor listrik mengubah tenaga listrik menjadi tenaga mekanik. Prinsip kerjanya berdasarkan induksi elektromagnetik yang menggerakkan motor.
- Pompa listrik berfungsi memindahkan/menggerakkan fluida baik itu zat cair, gas dan padat.
Secara garis besar, fungsi instrumentasi adalah sebagai berikut : 1. Penunjuk (indicator)
2. Pencatat (recorder) 3. Pengontrol (regulator)
4. Pemberi tanda bahaya (alarm)
Adapun instrumentasi yang digunakan di pabrik ini mencakup : 1. Pressure Controller (PC)
Adalah alat/instrumen yang dapat digunakan sebagai alat pengatur tekanan atau pengukur tekanan atau pengubah sinyal dalam bentuk gas menjadi sinyal mekanis. Pengatur tekanan dapat dilakukan dengan mengatur jumlah uap/gas yang keluar dari suatu alat dimana tekanannya ingin dideteksi.
Prinsip kerja :
Pressure control (PC) akibat tekanan uap keluar akan membuka/menutup
diafragma valve. Kemudian valve memberikan sinyal kepada PC untuk mengukur dan mendeteksi tekanan pada set point.
2. Flow Controller (FC)
Adalah alat/instrumen yang bisa digunakan untuk mengatur kecepatan aliran fluida dalam pipa line atau unit proses lainnya. Pengukuran kecepatan aliran fluida dalam pipa biasanya diatur dengan mengatur output dari alat, yang mengakibatkan fluida mengalir dalam pipa line.
Prinsip kerja :
Kecepatan aliran diatur oleh regulating valve dengan mengubah tekanan
discharge dari pompa. Tekanan discharge pompa melakukan bukaan/tutupan
valve dan FC menerima sinyal untuk mendeteksi dan mengukur kecepatan
Adalah alat/instrumen yang dipakai untuk mengatur ketinggian (level) cairan dalam suatu alat dimana cairan tersebut bekerja. Pengukuran tinggi permukaan cairan dilakukan dengan operasi dari sebuah control valve, yaitu dengan mengatur rate cairan masuk atau keluar proses.
Prinsip kerja :
Jumlah aliran fluida diatur oleh control valve. Kemudian rate fluida melalui
valve ini akan memberikan sinyal kepada LC untuk mendeteksi tinggi
permukaan pada set point.
Alat sensing yang digunakan umumnya pelampung atau transducer diafragma untuk mendeteksi dan menunjukkan tinggi permukaan cairan dalam alat dimana cairan bekerja.
Proses pengendalian pada pabrik ini menggunakan feedback control
configuration karena selain biayanya relatif lebih murah, pengaturan system
pengendaliannya menjadi lebih sederhana. Konfigurasi ini mengukur secara langsung variabel yang ingin dikendalikan untuk mengatur harga variabel yang dimanipulasi. Tujuan pengendalian ini adalah untuk mempertahankan variabel yang dikendalikan pada level yang diinginkan (set point).
Sinyal output yang dihasilkan oleh pengendali oleh pengendali
feedback ini berupa pneumatic signal yaitu dengan menggunakan udara
tekan. Tipe pengendali feedback yang digunakan pada perancangan ini, yaitu: 1. Jenis – P (Proportional), digunakan untuk mengendalikan tekanan gas. 2. Jenis – PI (Proportional Integral), digunakan untuk mengendalikan laju
alir (flow), ketinggian (level) cairan, dan tekanan zat cair.
3. Jenis – PID (Proportional Integral Derivative), digunakan untuk mengendalikan temperatur.
6.1.2 Syarat Perancangan Pengendalian
Beberapa syarat penting yang harus diperhatikan dalam perancangan pabrik antara lain :
2. Penggunaan supervisory computer control untuk mengkoordinasikan tiap unit pengendali.
3. Control valve yang digunakan sebagai elemen pengendali akhir
memiliki opening position 70 %.
4. Dilakukan pemasangan check valve pada mixer dan pompa dengan tujuan untuk menghindari fluida kembali ke aliran sebelumnya. Check
valve yang dipasangkan pada pipa tidak boleh lebih dari satu dalam
one dependent line. Pemasangan check valve diletakkan setelah
pompa.
5. Seluruh pompa yang digunakan dalam proses diletakkan di permukaan tanah dengan pertimbangan syarat safety dari kebocoran. 6. Pada perpipaan yang dekat dengan alat utama dipasang flange dengan
[image:53.595.112.539.412.691.2]tujuan untuk mempermudah pada saat maintenance.
Tabel 6.1 Daftar penggunaan instrumentasi pada pra rancangan pabrik pembuatan biogas sebagai sumber kebutuhan listrik
No Nama alat Jenis
instrumen Kegunaan
1 Pompa FC Mengontrol laju alir cairan dalam pipa
2 Tangki Neutralizer
LC Menunjukkan tinggi cairan dalam tangki TC Mengontrol suhu dalam tangki
3 Tangki pencampuran LC Menunjukkan tinggi cairan dalam tangki TC Mengontrol suhu dalam tangki 4 Raktor fermentasi TC Mengontrol suhu dalam tangki
LC Menunjukkan tinggi cairan dalam tangki 5 Tangki Pengendapan LC Menunjukkan tinggi cairan dalam tangki 7 Desulfurisasi PC Mengontrol tekanan gas dalam pipa
1. Pompa
[image:54.595.244.442.217.330.2]Variabel yang dikontrol pada pompa adalah laju aliran (flow rate). Untuk mengetahui laju aliran pada pompa dipasang flow control (FC). Jika laju aliran pompa lebih besar dari yang diinginkan maka secara otomatis katup pengendali (control valve) akan menutup atau memperkecil pembukaan katup.
Gambar 6.3 Instrumentasi pada pompa
2. Tangki neutralizer
Pada tangki ini dilengkapi dengan Level Controller (LC) yang berfungsi untuk mengontrol ketinggian cairan di dalam tangki dan TC yang berfungsi untuk mengontrol suhu dalam tangki. Jumlah aliran fluida diatur oleh control valve. Kemudian rate fluida melalui valve ini akan memberikan sinyal kepada LC untuk mendeteksi tinggi permukaan pada set point.
TC LC
[image:54.595.228.407.523.666.2]3. Tangki pencampuran (cairan)
Pada tangki ini dilengkapi dengan Level Controller (LC) yang berfungsi untuk mengontrol ketinggian cairan di dalam tangki dan Temperatur Controller (TC) yang berfungsi untuk mengontrol suhu dalam tangki. Jumlah aliran fluida diatur oleh
control valve. Kemudian rate fluida melalui valve ini akan memberikan sinyal
kepada LC untuk mendeteksi tinggi permukaan pada set point.
TC LC
Gambar 6.5 Instrumentasi pada tangki cairan
4. Reaktor Fermentasi
Reaktor fermentasi adalah alat tempat berlangsungnya reaksi kimia antara bahan-bahan yang digunakan. Dalam pabrik ini, reaktor merupakan tempat bereaksinya limbah cair kelapa sawit menghasilkan biogas dan produk sampingnya. Untuk mengendalikan ketinggian cairan dalam reaktor digunakan level controller (LC) dengan tujuan agar tidak terjadi kelebihan muatan dan Temperatur Controller TC yang berfungsi untuk mengontrol suhu dalam tangki
FC
TC LC
[image:55.595.227.412.208.356.2]5. Tangki Floating Roof
Tangki floating roof ialah alat untuk menampung biogas yang dihasilkan dari reaksi limbah cair kelapa sawit. Untuk mengendalikan ketinggian cairan dalam reaktor digunakan level controller (LC) dengan tujuan agar tidak terjadi kelebihan muatan dan Temperatur Controller (TC) yang berfungsi untuk mengontrol suhu dalam tangki
FC
[image:56.595.215.395.249.396.2]TC LC
Gambar 6.7 Instrumentasi pada tangki penampung gas
6. Tangki Pengendapan
Tangki pengendapan ini dilengkapi dengan Level Controller (LC) yang berfungsi untuk mengontrol ketinggian cairan di dalam tangki. Jumlah aliran fluida diatur oleh control valve. Kemudian rate fluida melalui valve ini akan memberikan sinyal kepada LC untuk mendeteksi tinggi permukaan pada set point.
LC
[image:56.595.242.363.573.678.2]7. Water Trap
Water Trap ialah alat untuk untuk menangkap air yang ada didalam biogas sehingga biogas yg keluar dari Water Trap lebih murni.
[image:57.595.277.359.387.508.2]E-95
Gambar 6.9 Instrumentasi pada Water Trap
8. Tangki Desulfurisasi
Tangki desulfurisasi ialah alat tempat terjadinya pengurangan kandungan sulfur yang ada pada biogas sehingga jumlah sulfur yang ada pada biogas tersaring di tangki sulfurisasi.
FC
Gambar 6.10 Instrumentasi pada Tangki Desulfurisasi
9. Generator
Gambar 6.11 Generator
6.2 Keselamatan Kerja Pabrik
Aktivitas masyarakat umumnya berhubungan dengan resiko yang dapat mengakibatkan kerugian pada badan atau usaha. Karena itu usaha – usaha keselamatan merupakan tugas sehari – hari yang harus dilakukan oleh seluruh karyawan. Keselamatan kerja dan keamanan pabrik merupakan faktor yang perlu diperhatikan secara serius. Dalam hubungan ini bahaya yang dapat timbul dari mesin, bahan baku dan produk, sifat zat, serta keadaan tempat kerja harus mendapat perhatian yang serius sehingga dapat dikendalikan dengan baik untuk menjamin kesehatan karyawan.
Perusahaan yang lebih besar memiliki divisi keselamatan tersendiri. Divisi tersebut mempunyai tugas memberikan penyuluhan, pendidikan, petunjuk – petunjuk, dan pengaturan agar kegiatan kerja sehari – hari berlangsung aman dan bahaya – bahaya yang akan terjadi dapat diketahui sedini mungkin, sehingga dapat dihindarkan (Bernasconi, 1995)
Gambar 6.12 Tingkat kerusakan di suatu pabrik
Kerusakan (badan atau benda) dapat terjadi secara tiba – tiba tanpa dikehendaki dan diduga sebelumnya. Keadaan atau tindakan yang bertentangan dengan aturan keselamtan kerja dapat memancing bahaya yang akut dan mengakibatkan terjadinya kerusakan.
Untuk menjamin keselamatan kerja, maka dalam perencanaan suatu pabrik perlu diperhatikan beberapa hal, yaitu :
Lokasi pabrik
- Sistem pencegahan kebocoran
- Sistem perawatan
- Sistem penerangan
- Sistem penyimpanan material dan perlengkapan
- Sistem pemadam kebakaran
Disamping itu terdapat beberapa peraturan dasar keselamatan kerja yang harus diperhatikan pada saat bekerja di setiap pabrik – pabrik kimia, yaitu:
- Tidak boleh merokok atau makan
- Tidak boleh minum minuman keras (beralkohol) selama bertugas
pengetahuan mengenai bahaya sedini mungkin, sehingga pencegahan dapat diupayakan sebelum bahaya tersebut terjadi.
Berikut ini upaya – upaya pencegahan terhadap bahaya – bahaya yang mungkin terjadi pada pra – rancangan pabrik biogas dari limbah cair kelapa sawit sebagai sumber energi listrik dapat dilakukan dengan cara :
1. Pencegahan terhadap kebakaran
- Memasang sistem alarm pada tempat yang strategis dan penting, seperti
power station, laboratorium dan ruang proses.
- Mobil pemadam kebakaran harus selalu dalam keadaan siap siaga di fire
station.
- Fire hydrant ditempatkan di daerah storage, proses, dan perkantoran.
- Fire extinguisher disediakan pada bangunan pabrik untuk memadamkan api yang relatif kecil.
- Smoke detector ditempatkan pada setiap sub – stasiun listrik untuk
mendeteksi kebakaran melalui asapnya.
2. Memakai peralatan perlindungan diri Di dalam pabrik disediakan peralatan perlindungan diri, seperti :
- Pakaian pelindung
Pakaian luar dibuat dari bahan – bahan seperti katun, wol, serat, sintetis, dan asbes. Pada musim panas sekalipun tidak diperkenankan bekerja dengan keadaan badan atas terbuka.
- Sepatu pengaman
Sepatu harus kuat dan harus dapat melindungi kaki dari bahan kimia dan panas. Sepatu pengaman bertutup baja dapat melindungi kaki dari bahaya terjepit. Sepatu setengah tertutup atau bot dapat dipakai tergantung pada jenis pekerjaan yang dilakukan.
- Topi pengaman
Topi yang lembut baik dari plastik maupun dari kulit memberikan
perlindungan terhadap percikan – percikan bahan kimia, terutama apabila bekerja dengan pipa – pipa yang letaknya lebih tinggi dari kepala, maupun tangki-tangki serta peralatan lain yang dapat bocor.
Dalam menangani beberapa bahan kimia yang bersifat korosif, maka para operator diwajibkan menggunakan sarung tangan untuk menghindari hal – hal yang tidak diinginkan.
- Masker
Berguna untuk memberikan perlindungan terhadap debu – debu yang berbahaya ataupun uap bahan kimia agar tidak terhirup (Bernasconi, 1995). 3. Pencegahan terhadap bahaya mekanis
- Sistem ruang gerak karyawan dibuat cukup luas dan tidak menghambat kegiatan kerja karyawan.
- Alat-alat dipasang dengan penahan yang cukup kuat
- Peralatan yang berbahaya seperti ketel uap bertekanan tinggi, reactor bertekanan tinggi dan tangki gas bertekanan tinggi, harus diberi pagar pengaman
4. Pencegahan terhadap bahaya listrik
- Setiap instalasi dan alat – alat listrik harus diamankan dengan pemakaian sekering atau pemutus hubungan arus listrik secara otomatis lainnya.
- Sistem perkabelan listrik harus dipasang secara terpadu dengan tata letak pabrik, sehingga jika ada perbaikan dapat dilakukan dengan mudah
- Memasang papan tanda bahaya yang jelas pada daerah sumber tegangan tinggi
- Kabel-kabel listrik yang letaknya berdekatan dengan alat – alat yang beroperasi pada suhu tinggi harus diisolasi secara khusus
- Setiap peralatan atau bangunan yang menjulang tinggi harus dilengkapi dengan penangkal petir yang dibumikan (Bernasconi, 1995).
5. Menerapkan nilai – nilai disiplin bagi karyawan
- Setiap karyawan bertugas sesuai dengan pedoman-pedoman yang diberikan dan mematuhi setiap peraturan dan ketentuan yang diberikan.
- Setiap kecelakaan kerja atau kejadian yang merugikan segera dilaporkan ke atasan.
- Setiap karyawan harus saling mengingatkan akan perbuatan yang dapat menimbulkan bahaya.
6. Penyediaan poliklinik di lokasi pabrik
Poliklinik disediakan untuk tempat pengobatan akibat terjadinya kecelakaan secara tiba – tiba, misalnya menghirup gas beracun, patah tulang, luka terbakar pingsan/syok dan lain sebagainya.
Apabila terjadi kecelakaan kerja, seperti terjadinya kebakaran pada pabrik, maka hal-hal yang harus dilakukan adalah :
a. Mematikan seluruh kegiatan pabrik, baik mesin maupun listrik.
b. Mengaktifkan alat pemadam kebakaran, dalam hal ini alat pemadam kebakaran yang digunakan disesuaikan dengan jenis kebakaran yang terjadi, yaitu (Bernasconi, 1995) :
- Instalasi pemadam dengan air
Untuk kebakaran yang terjadi pada bahan berpijar seperti kayu, arang, kertas, dan bahan berserat. Air ini dapat disemprotkan dalam bentuk kabut. Sebagai sumber air, biasanya digunakan air tanah yang dialirkan melalui pipa – pipa yang dipasang pada instalasi – instalasi tertentu di sekitar areal pabrik. Air dipompakan dengan menggunakan pompa yang bekerja dengan instalasi listrik tersendiri, sehingga tidak terganggu apabila listrik pada pabrik dimatikan ketika kebakaran terjadi.
- Instalasi pemadam dengan CO2
Gambar
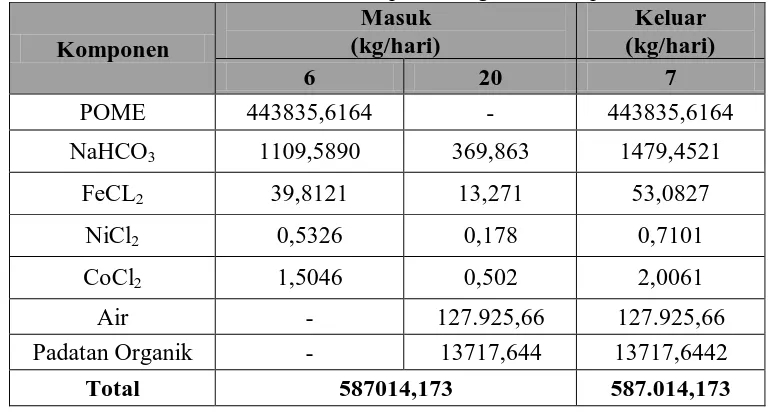

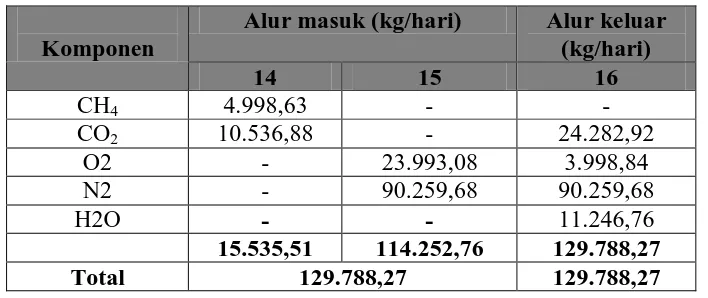
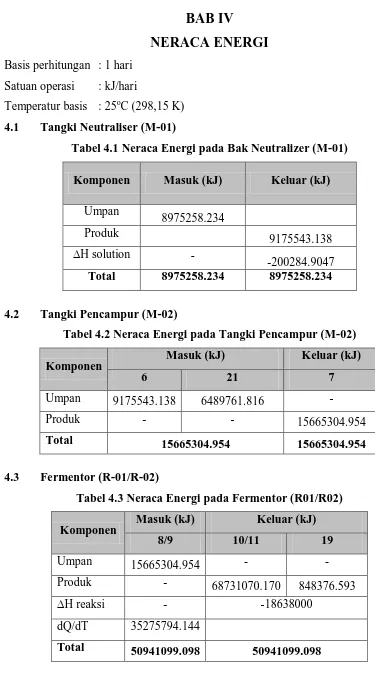
Dokumen terkait
Mengingat daerah Batam adalah salah satu daerah endemis malaria dan dikategorikan sebagai daerah resisten insektisida penting untuk diperhatikan jenis insektisida lain yang
Pembuatan dan Pengujian Converter Tekanan ke Massa merupakan suatu rangkaian elektronik berbasis mikrokontroler dengan tampilan display LCD dan menggunakan sensor tekanan
Penyusunan surat dakwaan tindak pidana korupsi yang dilakukan oleh aparatur kejaksaan dalam hal ini Jaksa Penuntut Umum selaku penuntutan dalam perkara pidana baik umum maupun
Bank adalah badan usaha yang menghimpun dana dari masyarakat dalam bentuk simpanan dan menyalurkannya kepada masyarakat dalam bentuk kredit dan/atau bentuk-bentuk lainnya
Informasi yang diakses oleh pemustaka tidak dapat dideteksi oleh pustakawan, pemustaka juga dengan leluasa dapat menggunakan informasi yang diaksesnya untuk kepentingannya tanpa
Yang harus diingat ialah bahwa present perfect tense ini tidak boleh dipakai bersama kata atau keterangan waktu yang menunjukkan saat masa lampau yang pasti?. Kalau ada kata
Data yang diperlukan pada saat di lapangan antara lain waktu edar (cycle time) alat angkut, waktu kerja tersedia, waktu kerja efektif, efisiensi operator, efektifitas
Penelitian ini bertujuan untuk menganalisis pengaruh kualitas produk terhadap kepuasan konsumen, kepuasan konsumen terhadap loalitas merek, dan kualitas produk